Автор: В.В. Буренин (МАДИ).
Опубликовано в журнале Химическая техника №1/2018
Загрязнение атмосферного воздуха – один из основных факторов негативного воздействия антропогенной деятельности людей на состояние окружающей среды.
Многие технологические процессы, в том числе и процессы химических, нефтехимических и нефтеперерабатывающих предприятий, сопровождаются поступлением в атмосферу производственных пылегазовоздушных выбросов, содержащих вредные вещества. Твердые и пластичные частицы пыли, газовые и аэрозольные загрязнения значительно ухудшают качество атмосферного воздуха, что наносит значительный ущерб здоровью людей, животных, насекомых и растительному миру.
Воздействие вредных веществ, содержащихся в пылегазовоздушных выбросах, на окружающую среду зависит от их физических и химических свойств, свойств продуктов их деструкций, а также их концентрации в выбросах и окружающей среде. Важным параметром, определяющим масштабы распространения загрязняющих вредных веществ, является их время жизни в атмосфере.
К наиболее распространенным вредным примесям, содержащимся в пылегазовоздушных выбросах промышленных предприятий и поступающим в атмосферу, относятся следующие: зола, оксид цинка, силикаты, хлорид свинца, диоксид и триоксид серы, сероводород, альдегиды, углеводороды, смолы, оксид и диоксид азота, аммиак, озон, оксид и диоксид углерода, фтороводород, хлороводород, радиоактивные газы, аэрозоли и пыли.
При сжигании топлива, прежде всего каменного угля, образуется большое количество техногенной пыли. Так, в процессе сжигания 1 т каменного угля образуется в среднем около 90…100 кг летучей золы, т.е. при степени очистки пылевоздушных выбросов 70–80% в атмосферу попадает 20…30 кг твердых частиц, при эффективности очистки 97–99% в атмосферу поступает 1…3 кг. Кроме того, вместе с золой в атмосферу поступает несгоревшее топливо (так называемый недожог), являющееся еще одним серьезным загрязнением окружающей воздушной среды.
Причины образования промышленной пыли зависят от типа производственного процесса:
- механическая обработка различных веществ (дробление, разлом, полирование и т.д.);
- тепловые процессы и процессы горения (сжигание, плавление, сушка, дистилляция и т.д.);
- отделение веществ (отпиловка, отрыв и т.д.);
- транспортировка зернистых материалов (погрузка, перегрузка, смешивание, просеивание и т.д.);
- соединение гранулированных веществ (брикетирование);
- износ и коррозия веществ.
Жидкие загрязнения (туманы, капли) образуются в следующих случаях:
- при конденсации паров;
- при распылении или разливе жидкостей;
- в результате химических или фотохимических реакций.
Образование паровых (газообразных) загрязнений характерно для различных процессов. Прежде всего, это химические реакции – окисление, восстановление, замещение и разложение, а также электрохимические (электролиз) и физико-химические (выпаривание и дисцилляция) процессы.
Наибольшую часть газообразных вредных выбросов составляют продукты окисления, образовавшиеся в процессах горения, когда при окислении углерода образуются оксид и диоксид углерода, при окислении серы – диоксид серы, а при высокотемпературном окислении азота в печах – оксид и диоксид азота. При неполном сгорании не происходит полного окисления органических веществ и могут образоваться альдегиды, кетоны или органические кислоты.
Степень опасности загрязнения приземного слоя атмосферного воздуха вредными веществами, содержавшимися в пылегазовоздушных выбросах промышленных предприятий, определяется по наибольшему рассчитанному значению приземной концентрации каждого вещества, которая может устанавливаться на некотором расстоянии от источника выброса при наиболее неблагоприятных метеорологических условиях. Значения наибольшей концентрации каждого вредного вещества в приземном слое атмосферы не должно превышать максимальной разовой предельно допустимой концентрации данного вещества в атмосферном воздухе.
Наиболее эффективным методом защиты воздушного бассейна от загрязнения пылегазовыми вредными веществами является внедрение в производство безотходных технологий. Однако по техническим и экономическим соображениям безотходная технология, создание беструбных и бессточных промышленных предприятий, полная утилизация отходов производства станут основой нашей производственной деятельности только в будущем.
В связи с этим в настоящее время очень актуальна очистка и обезвреживание производственных пылегазовоздушных выбросов от твердых, пластичных, газообразных, аэрозольных и жидких вредных примесей с помощью фильтров-пылегазоуловителей. .[1]
Для улавливания твердых и пластичных частиц загрязнений из производственных пылегазовоздушных выбросов применятся фильтры-пылеуловители, которые по принципу действия делятся на механические и силовые.
Для улавливания вредных газообразных примесей используются абсорбционные, адсорбционные, химические, каталитические, термические и другие методы очистки.
В последние годы заметно повысился интерес российских и зарубежных фирм к созданию новых фильтров-пылегазоуловителей с высокими технико-экономическими показателями.
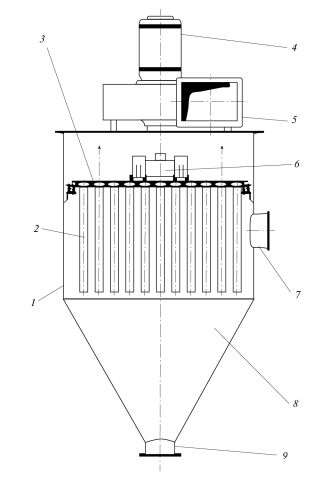
с фильтрующими патронами из пористой металлокерамики
Удобен в эксплуатации и обеспечивает повышенную степень очистки пылегазовоздушных выбросов от пыли механический фильтр-пылеуловитель [2], содержащий корпус 1 (рис. 1), фильтрующий блок 2 и устройство для регенерации 6 фильтрующего блока 2 вибрационного типа, закрепленное на перегородке 3 в корпусе, и бункер 8 для сбора уловленных частиц пыли. Блок 2 состоит из фильтрующих патронов, изготовленных из листовой пористой металлокерамики, полученной прокаткой из металлокерамического порошка с последующим спеканием при температуре 800…1300°С. Пылегазовоздушные выбросы подаются на очистку в фильтр-пылеуловитель через боковой патрубок 7 корпуса, проходят через блок 2 и очищенными выводятся из корпуса через выходной патрубок 5 вентиляторным агрегатом 4. Степень засорения фильтрующих патронов блока 2 контролируется датчиками давления (на рис. 1 не показаны), а очистка их осуществляется устройством для регенерации 6. Частицы пыли из бункера 8 выводятся через патрубок 9.
ЗАО «НТЦ Бакор» (Россия) разработаны пористые проницаемые керамические материалы с различной структурой и технология получения фильтрующих элементов для механических фильтров из этих материалов [3]. Фильтрующие элементы из этой керамики отличаются низким гидравлическим (аэродинамическим) сопротивлением с оптимальным размером пор и максимальной эффективностью при очистке, устойчивостью к кислотам и щелочам, способностью выдерживать резкие колебания температур (термоудары) очищаемых пылегазовоздушных выбросов, стабильностью физико-механических свойств в течение длительного времени при воздействии горячих запыленных газов, хорошей регенерируемостью, т.е. восстановлением фильтрующих характеристик после периодической продувки сжатием воздухом высокого давления.
Использование в механических фильтрах-пылеуловителях фильтрующих элементов из пористой проницаемой керамики дает большой экономический и экологический эффект. Кроме того, экологическая составляющая этого эффекта может быть увеличена за счет нанесения катализатора и химических веществ на высокопористую поверхность фильтрующих элементов, т.е. появляется дополнительная возможность очистки горячих газов от паров вредных веществ.
Новые фильтровальные установки модели Torit для очистки пылегазовоздушных выбросов фирмы Donaldson GmbH (Германия) [4] включают 12 механических рукавных фильтров типа Power Core, которые при необходимости легко заменяются. Эти установки по сравнению с ранее применявшимися фильтровальными установками требуют для размещения уменьшенную на 70% производственную площадь.
Повышенной степенью очистки производственных пылегазовоздушных выбросов с различным дисперсным составом твердых частиц при одновременном снижении энергозатрат отличается многоступенчатый силовой инерционный фильтр [5], одна из ступеней которого показана на рис. 2.
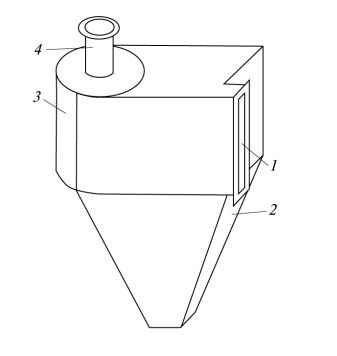
Пылегазовоздушные выбросы на очистку подаются по тангенциальному входному патрубку 1 в криволинейные секции спирального канала 3. Твердые частицы загрязнений плотностью более высокой, чем плотность газовоздушного потока, протекающего по каналам криволинейных секций, под действием центробежной силы (силы инерции) смещаются в каждой секции к ее внешней стенке, т.е. в каждом канале криволинейной секции полный пылегазовоздушный поток делится на две части: пристеночный (у внешней стенки) с большей концентрацией частиц загрязнений и отсепарированный с небольшой концентрацией частиц загрязнений. Из криволинейных секций спирального канала 3 частицы загрязнений с частью расхода газовоздушного потока (пристеночный поток) поступают через разгрузочную щель (на рис. 2 щель не показана) в бункер 1 для частиц загрязнений.
Этот расход, составляющий 1/4…1/5 часть полного пылегазовоздушного потока, после выделения и осаждения твердых частиц загрязнений в бункере 1 направляется во входной патрубок 2 следующей ступени фильтра, т.е. отсепарированный газовоздушный поток с небольшой концентрацией частиц загрязнений через выпускной патрубок 4 поступает в следующую ступень фильтра.
Особенностью конструкции многоступенчатого силового инерционного фильтра является наличие устройства для регулирования площади поперечного сечения спирального канала 3, установленного на входе в разгрузочную щель, соединяющую полость бункера 2 со спиральным каналом 3.
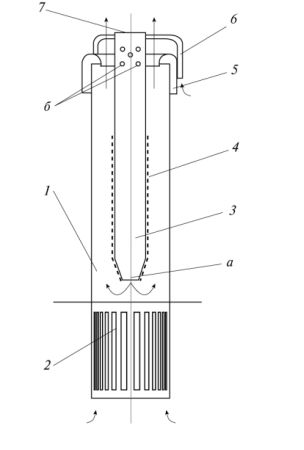
Силовой центробежный фильтр-сепаратор [6] с высокой эффективностью очищающий загрязненный технологический воздух от капельной воды и других жидкостей с помощью центробежных сил, возникающих при закручивании очищаемого технологического воздушного потока, состоит из обечайки 1 (рис. 3), завихрителя 2 на нижнем торце обечайки 1, и полого тела 3, расположенного соосно с обечайкой 1. Полое тело выполнено с элементом 4, обеспечивающим разрушение регулярных токов пленки жидкости. Элемент выполнен в виде сетки с размером ячеек 1…2 мм, закрепленной на внешней поверхности полого тела 3 со стороны его нижнего торца, расположенного вблизи завихрителя 2. Элемент 4 размещен от нижнего торца полого тела 3, имеющего отверстие, на расстоянии 0,25…0,75 длины полого тела.
Противоположный торец полого тела герметично закрыт крышкой 7 и снабжен газоподводящими патрубками 6, соединяющими внутреннюю полость полого тела 3 с окружающим внешним пространством. Поверхность полого тела, расположенная вблизи крышки 7, имеет перфорационные отверстия б, площадь проходного сечения этих отверстий (суммарная) равна или больше площади проходного сечения отверстия а.
Поток загрязненного технологического воздуха, содержащий капельную влагу, поступает на очистку внутрь авихрителя 2 фильтра-сепаратора, где под действием центробежных сил, возникающих за счет наклонного расположения лопаток завихрителя, закручивается и делится на центральный воздушный поток с зоной пониженного давления и периферийный воздухожидкостной поток с зоной повышенного давления. За счет размещения соосно обечайки и полого тела центральный воздушный поток объединяется с периферийным воздухожидкостным потоком, что устраняет вторичный унос, вызванный обратными токами. Капельки жидкости под действием центробежных сил осаждаются на внутреннюю поверхность обечайки 1 и через каплесборником 5 с частью технологического воздуха отводятся из потока. Основной поток воздуха, отделившись от жидкости, выходит через пространство между полым телом и каплесборником. Часть воздуха, вышедшего через каплесборник вместе с жидкостью, засасывается через патрубки 6 во внутреннюю полость полого тела 3 и через отверстие а подается в зону пониженного давления воздушного потока.
Так как основная часть жидкости отбрасывается на внутреннюю поверхность обечайки 1 и выводится через каплесборник, мелкодисперсная часть жидкости осаждается на внешнюю поверхность полого тела 3 и силами трения вращающегося воздушного потока направляется вверх в виде пленки, в которой содержатся также капли жидкости вторичного уноса (разбрызгивание, турбулентные пульсации и т.д.). Жидкость в виде капель попадает в ячейки, образованные структурой элемента 4, выполненного в виде сетки, и наружной поверхностью полого тела 3, где накапливается до размеров, при которых под действием сил динамического давления поступательно направленного вращающегося воздушного потока преодолевает силы сцепления, и, оторвавшись от коалесцирующей поверхности, осаждается на внутренней поверхности обечайки. Оставшаяся в виде пленки жидкость, осевшая на наружную поверхность полого центрального тела 3, через перфорированные отверстия б поступает во внутреннюю полость полого тела 3, откуда через отверстие а поступает во внутреннюю полость обечайки 1.
Механические и силовые фильтры-пылегазоуловители мокрой очистки (скрубберы) предназначены для промывки жидкостями производственных пылегазовоздушных выбросов с целью их очистки (обезвреживания) от вредных примесей, а также для извлечения одного или нескольких загрязняющих компонентов. Достоинством скрубберов является сравнительно низкая стоимость очистки пылегазовоздшных выбросов, недостатками – образование большого количества шлама, необходимость обработки (очистки) образующихся сточных вод, повышенный брызгоунос и требование защиты фильтров от коррозии при обработке агрессивных сред.
Удобен в эксплуатации и обладает повышенной надежностью силовой фильтр-пылеуловитель [7] для мокрой очистки производственных пылегазовоздушных выбросов.
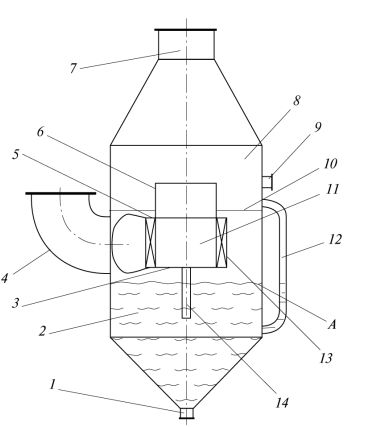
Фильтр-пылеуловитель содержит цилиндрический корпус, состоящий из верхней 8 и нижней 2 частей (рис. 4) с патрубками подвода 4 и отвода 7 пылегазовоздушных выбросов. Очищаемый поток пылегазовоздушных выбросов поступает по тангенциальному патрубку 4 поступает на очистку в нижнюю часть 2 корпуса, где происходит первоначальное взаимодействие потока с поверхностью жидкости А. Жидкость А под действием сил трения потоком пылегазовоздушных выбросов приводится во вращение, при этом происходит смачивание и сепарация крупных частиц загрязнений, содержащихся в потоке. Далее поток пылегазовоздушных выбросов, проходя между пластинами 13 вихревого контактного устройства 11, закручивается, образуя разрежение в приосевой области.
За счет разрежения по патрубку 14 транспортируется жидкость из нижней части 8 корпуса в вихревое контактное устройство 11, в котором происходит основное взаимодействие компонентов, при этом твердые частицы загрязнений переходят из потока пылегазовоздушных выбросов в жидкость. Далее жидкость с уловленными частицами загрязнений, проходя через сепаратор 6 вихревого контактного устройства 11, из распыленного состояния переходит в пленочное, отделяется от потока пылегазовоздушных выбросов, стекает на тарелку 10 и перетекает по переточному трубопроводу 12 в нижнюю часть 2 корпуса. После осветления жидкость вновь поступает в вихревое контактное устройство 11, образуя замкнутый цикл. Твердые частицы загрязнений осаждаются в нижней части 2 корпуса и в виде шлама удаляются через патрубок 1 на утилизацию. Очищенные пылегазовоздушные выбросы выводятся из верхней части 8 корпуса через патрубок 7. Жидкость подается в корпус фильтра через патрубок 9. Достоинством фильтра-пылеуловителя мокрой очистки является также то, что он может работать как в непрерывном, так и периодическом режиме.
Фирма Mitsubishi Heavy Industries Ltd. (Япония) разработала новую высокоэффективную конструкцию силового фильтра-пылегазоуловителя мокрой очистки марки DCFS [8] для очистки промышленных пылегазовоздушных выбросов от твердых частиц и вредных газовых примесей. Фильтр позволяет улавливать более 99% SO2 и 90% паров ртути, обеспечивая их выходные удельные концентрации в очищенных пылегазовоздушных выбросах ниже соответственно 50 и 1 мг/м3.
Высокой пропускной способностью, малыми габаритными размерами, низким гидравлическим сопротивлением и высокой эффективностью очистки пылегазовоздушных выбросов отличается силовой пылегазоочистительной вихревой аппарат мокрой очистки с жидкостноразбрызгивающими форсунками [9].
Поток пылегазовоздушных выбросов поступает на очистку в вихревой аппарат через патрубок 1 (рис. 5).
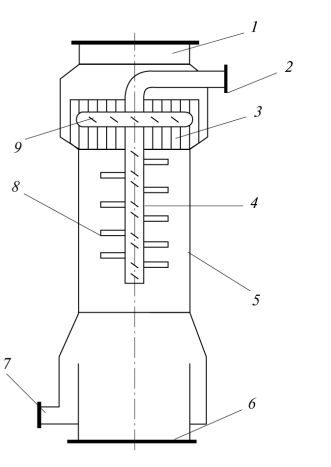
с жидкостно- разбрызгивающими форсунками
для очистки пылегазовоздушных выбросов
Затем, проходя через завихритель 3, пылегазовоздушный поток начинает вращаться вокруг центральной оси.
Поток жидкости поступает в корпус 5 аппарата через входной патрубок 2, ороситель 9, центральную трубу 4, разбрызгивающие форсунки 8, расположенные на определенном расстоянии друг от друга по высоте трубы 4.
Образовавшиеся капли жидкости двигаются практически перпендикулярно потоку очищаемых пылегазовоздушных выбросов. Под действием центробежной силы капли отработанной жидкости осаждаются на стенке (внутренней поверхности) корпуса 5 аппарата в виде пленки, стекают вниз и удаляются через выходной патрубок 7. Поток пылегазовоздушных выбросов, пройдя через слой капель жидкости, очищается от твердых частиц и газовых примесей и выходит через выпускной патрубок 6.
Достоинством разбрызгивающих форсунок 8 являются минимальные затраты энергии на создание развитой поверхности контакта газовой и жидкостной фаз по всему объему рабочей камеры в корпусе аппарата.
Для качественного сухого обезвреживания производственных пылегазовоздушных выбросов от вредных токсичных газовых примесей предназначен химический поглотитель (адсорбер) [10], имеющий оригинальный способ подготовки его к использованию. Химический поглотитель содержит стробилы хвойных пород деревьев, мерсеризованные гидроксилом щелочного металла и дополнительно подвергнутые обработке растворами, выбранными из следующей группы: гидроксид кальция, карбонат натрия, серусодержащая соль одного или более щелочных металлов, в которой степень окисления серы не превышает +4. При подготовке химического поглотителя к использованию мерсеризованные стробилы загружают в адсорбер при влажности 15–30% и сушат при температуре 40…200°С до влажности 1–10%.
Компания Dantherm Filtration GmbH (Германия) разработала технологию очистки пылегазовоздушных выбросов [11] промышленных предприятий, обеспечивающую экономию рабочего пространства и энергозатрат.
В основе технологии лежит сухая очистка от частиц загрязнений и сорбционное обезвреживание от таких газообразных веществ, как пары ртути, диоксиды серы, азота, углерода и др., посредством их сорбции гидратной известью, активированным углем и другими сорбентами. Очистка выбросов от взвешенных частиц загрязнений осуществляется с применением механических фильтров с горизонтальным расположением фильтрующих элементов плоской формы и их последующей регенерацией воздухом низкого давления.
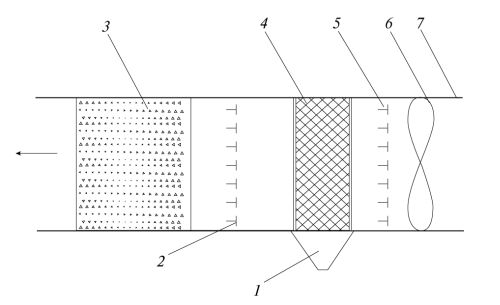
Повышенной эффективностью очистки пылегазовоздушных выбросов от взвешенных твердых и пластичных частиц загрязнений, а также вредных газовых примесей отмечается комплексный фильтр-пылегазоуловитель [12], содержащий корпус 7 (рис. 6), внутри которого последовательно установлены вентилятор 6, первый электрический фильтр 5 с высоковольтным блоком питания, механический фильтр грубой очистки 4, второй электрический фильтр 2 с высоковольтным блоком питания, фильтр-адсорбер 3 с гранулами активного угля. Комплексный фильтр-пылегазоуловитель снабжен также бункером 1 для сбора оседающих в него взвешенных частиц загрязнений от механического фильтра грубой очистки.
Развитие существующих способов и оборудования для очистки и обезвреживания пылегазовоздушных выбросов промышленных предприятий, в том числе химических, нефтехимических и нефтеперерабатывающих предприятий, не стоит на месте, оно продолжается и совершенствуется год от года.
Во всем мире все большее внимание уделяется комплексному решению проблемы качественной очистки и обезвреживанию производственных пылегазовоздушных выбросов как основной мере обеспечения экологической безопасности воздушного бассейна и окружающей природной среды в целом.
Решение проблемы высококачественной очистки и обезвреживания производственных пылегазовоздушных выбросов – ключ к сохранению окружающей среды для настоящего и будущего поколений.
Список литературы
- Буренин В.В. Очистка и обезвреживание пылегазовоздушных выбросов химических и нефтехимических предприятий//Химическая техника. 2012. №2. С. 41–44.
- Пат. 2290253 Россия. МПК В01Д 46/10. Фильтр из металлокерамики.
- Красный Б.Л., Тарасовский В.П., Красный А.Б. Принципиально новые возможности очистки высокотемпературных газов от пыли без их предварительного охлаждения//Химическая техника. 2009. №11. С. 27–30.
- Wartungsfreundlich und 70 Prozentkleiner//DDS: Deutsch.Schrein. 2010. №9. S. 42.
- Пат. 2401156 Россия. МПК В01Д 35/20. Инерционный фильтр.
- Пат. 2401156 Россия. МПК В01Д 45/12. Центробежный сепарационный элемент.
- Пат. 2400289 Россия. МПК В01Д 47/02. Устройство для мокрой очистки газов от пыли.
- Nagayasu T., Nakashoji H., Imai N.//GB Power Tech. Ind. 2011. №4. Р. 68–73.
- Дмитриев А.В., Дмитриева О.С., Николаев А.Н. Повышение эффективности очистки газовых выбросов путем установки пневмогидравлических распылителей в аппараты с интенсивным взаимодействием фаз//Экология и промышленность России. 2012. №5. С. 16–18.
- Пат. 2409418 Россия. МПК В01У 53/02. Химический поглотитель для обезвреживания газовых выбросов и способ подготовки его к использованию.
- Шилли М., Нечаевский А. Технология очистки газовых выбросов на предприятиях различных отраслей промышленности, обеспечивающая экономию рабочего пространства и энергозатрат//Сб. материалов 6-й международной научно-практической конференции. М.: ГИНЦВЕТМЕТ, 2010. С. 80–81.
- Пат. 2339879 Россия. МПК F24F 3/16. Пылегазоочиститель.