Автор: А.П. Завьялов (ОАО «Оргэнергогаз»).
Опубликовано в журнале Химическая техника №2/2015
Тема диагностического обслуживания технологических трубопроводов объектов ТЭК имеет высокую актуальность, поскольку надежность этих конструкций в значительной степени определяет надежность промышленного объекта в целом. Ряд крупных аварий на объектах ТЭК произошел из-за аварийных отказов технологических трубопроводов, к числу которых относятся аварии на Ачинском НПЗ (2014 г.), НПЗ компании BP в Техасе, США (2005 г.).
Тема диагностического обслуживания технологических трубопроводов объектов ТЭК имеет высокую актуальность, поскольку надежность этих конструкций в значительной степени определяет надежность промышленного объекта в целом. Ряд крупных аварий на объектах ТЭК произошел из-за аварийных отказов технологических трубопроводов, к числу которых относятся аварии на Ачинском НПЗ (2014 г.), НПЗ компании BP в Техасе, США (2005 г.).
Система обеспечения надежности и безопасности эксплуатации технологических трубопроводов объектов ТЭК основывается на регулярном проведении диагностических обследований (ревизии), а также иных видов диагностики.
Эта система в целом обеспечивает решение следующих практических задач:
- обеспечение безаварийной эксплуатации технологических трубопроводов, предотвращение аварийных отказов;
- ранжирование трубопроводов в зависимости от технического состояния по приоритетности диагностического и ремонтно-технического обслуживания;
- выполнение экспертизы промышленной безопасности в установленных законом случаях и обоснованное продление срока безопасной эксплуатации технологических трубопроводов.
Наиболее технологически сложным и трудоемким этапом диагностического обслуживания технологических трубопроводов является полная оценка технического состояния трубопровода, например, при проведении экспертизы промышленной безопасности с целью продления срока безопасной эксплуатации.
При этом необходимо оценить техническое состояние всех без исключения элементов технологического трубопровода (труб, соединительных деталей и т.д.), убедиться, что эти элементы, а также связывающие их сварные соединения не содержат недопустимых дефектов.
На первый взгляд, это не слишком сложная задача. Существуют надежные способы диагностики (ультразвуковой, рентгеновский, вихретоковый), которые позволяют с высокой точностью проводить дефектоскопию технологических трубопроводов (как тела трубы, так и сварных швов).
Но эти способы контроля, как правило, являются дорогими и трудоемкими, а также требуют значительного объема подготовительных работ (очистка трубопроводов от изоляции и лакокрасочных покрытий, зачистка сварных швов для проведения контроля, большой объем земляных работ при откапывании/закапывании подземных трубопроводов).
При этом, как показывает практика, в ряде случаев стоимость такого процесса подготовки–дефектации– ремонта технологических трубопроводов приближается к стоимости сплошной замены труб новыми, а в случае высокой дефектности может и превышать ее.
В этой связи возникает необходимость оптимизации системы технической диагностики технологических трубопроводов, обеспечения возможности продления срока безопасной эксплуатации этих конструкций с приемлемыми затратами.
Существует несколько подходов к решению этой проблемы.
Первый подход состоит во внедрении двухступенчатой системы диагностического обследования.
Задачи дефектоскопии технологических трубопроводов можно условно разделить на две основные разновидности.
Первую условно может назвать «отбраковка». При этом необходимо найти на элементе трубопровода хотя бы один недопустимый дефект, который делает невозможным его дальнейшую эксплуатацию.
Вторая задача – оценка технического состояния – состоит в получении полной картины технического состояния элемента, оценки параметров всех локализованных в нем дефектов, и на основе этой информации принятия решения о возможности дальнейшей эксплуатации элемента трубопровода.
Отличие этих задач заключается в том, что в первом случае допускается возможность пропуска (необнаружения) некоторых дефектов, а во втором случае необходимо гарантировать, что все локальные дефекты выявлены.
В этом смысле оптимизация процедуры диагностического обследования трубопровода может быть достигнута путем проведения предварительного (предремонтного) обследования.
Цель заключается в следующем.
На начальном этапе обследования с относительно небольшими затратами следует выявить элементы трубопровода, которые содержат крупные, заведомо недопустимые и неремонтопригодные дефекты, отбраковать эти элементы для того, чтобы в дальнейшем отказаться от их детального инструментального обследования, что приведет к снижению общего объема работ по неразрушающему контролю, а также объема подготовительных работ. После этого оставшиеся элементы, которые по данным первого этапа обследования не содержат недопустимых дефектов, подвергаются детальному инструментальному обследованию с целью оценки возможности их дальнейшей эксплуатации.
При этом (при выполнении предварительного обследования) могут быть использованы совершенно различные методы неразрушающего контроля и диагностики, основанные на самых различных физических принципах.
В данном случае допустимо применение в принципе любых средств и методов диагностики, поскольку задача обязательного выявления дефектов не ставится. Невыявленные дефекты будут обнаружены на втором этапе обследования.
Такая постановка задачи дает разумную перспективу для разработчиков низкобюджетных средств диагностики.
Решение задачи обеспечения предварительной (предремонтной диагностики) постепенно привело к появлению сравнительно нового класса технических средств для диагностики технологических трубопроводов – внешнетрубных сканеровдефектоскопов (рис. 1).
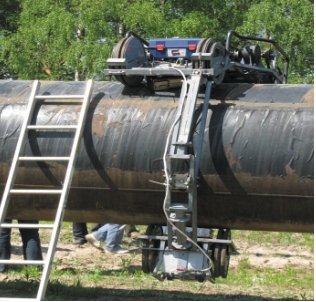
В качестве примера можно привести сканеры-дефектоскопы «Автокон-МГТУ» (ФГУ НУЦ «Сварка и контроль» при МГТУ им. Н.Э. Баумана), ДНС (ООО «Газприборавтоматикасервис»), SoNet (ООО «Акустические контрольные системы»), АМДЭ-СТ (ЗАО ДНТЦ «Дефектоскопия»), УСД (ООО НПК «РемГазДиагностика») и др. Эти технические средства, основанные на различных физических принципах неразрушающего контроля, позволяют проводить предварительную оценку технического состояния технологических трубопроводов с внешней стороны трубы.
При этом, как правило, такие технические средства обладают высокой производительностью (сотни погонных метров трубопроводов в рабочую смену) и значительно более мягкими требованиями к подготовке поверхности трубы к диагностике, чем при использовании традиционных методов контроля.
Проведение контроля возможно, как правило, после механизированной очистки трубы, без пескоструйной обработки и без специальной зачистки поверхности. Ряду средств диагностики требуется только доступ к металлу – узкая полоска снятой изоляции по верхней образующей трубы. Это позволяет на ранней стадии с приемлемой вероятностью и приемлемой стоимостью выявить элементы трубопровода, содержащие неремонтнопригодные дефекты, и, таким образом, снизить стоимость обследования, отказавшись от детального инструментального обследования этих элементов.
В целом, по нашим оценкам, в большинстве случаев применение методики предварительного (предремонтного) обследования трубопровода является обоснованным, поскольку позволяет:
- снизить общий объем работ по дефектоскопии, и как, следствие ее стоимость;
- уменьшить сроки проведения диагностических работ, и, как следствие, общую продолжительность ремонта;
- очень важно, что в этом случае можно получить на ранней стадии информацию о реальном техническом состоянии технологического трубопровода, предполагаемых объемах выбраковки элементов; это позволяет более качественно выполнить проектные работы при ремонтах и реконструкциях, более качественно спланировать комплектацию, а также привлечение оборудования и специалистов для проведения ремонтных работ.
Второй подход к совершенствованию системы диагностического обслуживания технологических трубопроводов объектов ТЭК состоит в широком внедрении средств и методов внутритрубной диагностики технологических трубопроводов.
Средства внутритрубной диагностики нашли широкое применение для диагностики линейной части магистральных нефтеи газопроводов и показывают высокую эффективность. Однако для технологических трубопроводов их возможности ограничены в силу сложной пространственной геометрии этих конструкций, наличия в их составе разнородных конструктивных элементов (отводы, тройники, конические переходы).
Это обстоятельство обусловливает необходимость создания специализированных внутритрубных средств диагностики технологических трубопроводов. Причем, как показала практика, основную сложность здесь составляет проектирование и изготовление ходовой части, способной передвигаться по технологическим трубопроводам с учетом их сложной геометрии, особенно преодолевать вертикальные участки и тройники.
Методы неразрушающего контроля вполне традиционны: визуально-измерительный, ультразвуковой, электромагнито-акустический, вихретоковый.
К настоящему времени существует (воплощены в металле) как минимум три таких технических устройства:
- робот-трактор изготовления ЗАО «КТПИ «Газпроект» (Санкт-Петербург);
- роботизированное средство диагностики технологических трубопроводов ОАО «Оргэнергогаз» (рис. 2);
- роботизированный сканер-дефектоскоп на магнитных колесах Intro-Scan ЗАО «ИнтроСкан Технолоджи».
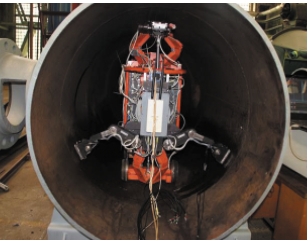
В целом можно говорить о том, что появление и совершенствование технологии внутритрубной диагностики технологических трубопроводов позволяет инженерам-диагностам и работникам эксплуатации решать большой круг новых задач:
- инструментальное обследование технологических трубопроводов без снятия изоляции в тех случаях, когда снятие изоляции трудоемко или нецелесообразно (например, в случае нанесенной в заводских условиях изоляции или после проведения ремонта с применением современных полимерных покрытий);
- проведение предварительного (предремонтного) обследования методом внутритрубной диагностики с целью уточнения технического состояния трубопровода;
- ранжирование технологических трубопроводов по приоритетности ремонта на основе данных внутритрубной диагностики;
- после проведения необходимых научно-исследовательских работ и разработки нормативно-методической документации на основе результатов внутритрубной диагностики возможно обоснованное продление срока безопасной эксплуатации (на относительно небольшой срок) технологического трубопровода в тех случаях, когда выведение его в ремонт с проведением детального инструментального обследования по техническому состоянию нецелесообразно.
Это позволяет разработать заключение экспертизы промышленной безопасности на трубопровод и осуществлять его эксплуатацию в соответствии со всеми требованиями нормативных документов; по сути, это будет важнейшим шагом для перехода на эксплуатацию технологических трубопроводов по техническому состоянию.
На сегодня технология внутритрубной диагностики технологических трубопроводов – это практически единственная технология, позволяющая с приемлемым качеством оценивать техническое состояние технологических трубопроводов без снятия изоляции и масштабных подготовительных работ. Оценка технического состояния технологического трубопровода методов внутритрубной диагностики занимает значительно меньше времени, чем обследование традиционными методами, что особенно важно в ситуации с ограниченным временем останова технологических установок.
Третий подход к совершенствованию системы диагностического обслуживания технологических трубопроводов объектов ТЭК состоит во внедрении методов контроля реальной эксплуатационной нагруженности этих конструкций.
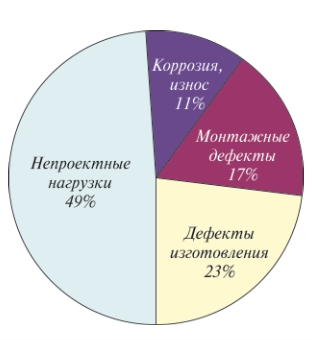
На рис. 3 представлена статистика аварийных отказов технологических трубопроводов объектов ТЭК, полученная на основе более чем 20-летнего анализа данных диагностических обследований. Согласно данной статистике, основной причиной аварий технологических трубопроводов (51%) является зарождение и развитие локальных дефектов тела трубы и сварных швов, причем доли дефектов изготовления элементов трубопроводов, монтажа и эксплуатационных, в принципе, соразмерны друг с другом.
Второй причиной отказов технологических трубопроводов является воздействие на эти конструкции непроектных нагрузок.
Данная статистика позволяет сделать два важных вывода:
- поскольку дефекты зарождаются на всех стадиях жизненного цикла трубопровода, то и система диагностического обслуживания технологических трубопроводов должна распространяться на весь жизненный цикл этих конструкций (проектирование, строительство, эксплуатация, капитальный ремонт и реконструкция, ликвидация);
- обеспечение надежной и безопасной эксплуатации требует не только проведения дефектоскопии трубопроводов, но и контроля за величиной реальной эксплуатационной нагруженности.
Технологические трубопроводы объектов ТЭК являются конструкциями, которые подвержены наиболее широкому спектру непроектных нагрузок и воздействий самой различной природы и величины. Это и кинематические нагрузки, связанные с пространственными подвижками и просадками элементов трубопроводов и опорных систем, и сезонные знакопеременные нагрузки, связанные с замерзанием–оттаиванием грунта и опорного основания, и температурные нагрузки, и динамические нагрузки – вибрация, источником которой является как технологическое оборудование, в первую очередь роторные машины, так и пульсирующий поток рабочей среды – жидкости или газа.
Непроектные нагрузки и воздействия в ряде случаев существенно влияют на реальную нагруженность элементов трубопроводов, на его ресурсные характеристики. Опыт свидетельствует, что подавляющее большинство крупных аварий на технологических трубопроводах сопровождается воздействием на эти конструкции непроектных нагрузок.
В связи с этим еще одной важнейшей задачей системы диагностического обслуживания технологических трубопроводов является контроль за величиной и воздействием на конструкции непроектных нагрузок. На практике контроль может быть периодическим или постоянным (мониторинг технического состояния). Для периодического контроля используются портативные приборы, например, приборы для измерения параметров напряженнодеформированного состояния трубопроводов. Инструментальные измерения, как правило, дополняются расчетами методом конечных элементов, что позволяет распространить оценку параметров технического состояния на всю конструкцию, а не только на те зоны, где проводятся измерения (рис. 4).
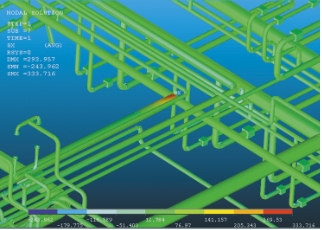
Второй разновидностью контроля за непроектными нагрузками является постоянный контроль (мониторинг технического состояния).
В зависимости от назначения, конструктивного исполнения, условий работы трубопровода система мониторинга технического состояния может включать:
- систему контроля пространственного положения элементов технологического трубопровода;
- систему измерения статических и динамических нагрузок;
- акустико-эмиссионную систему мониторинга развития опасных дефектов.
К настоящему моменту в ОАО «Оргэнергогаз» накоплен значительный опыт эксплуатации систем мониторинга НДС технологических трубопроводов, основой которых служат либо струнные датчики деформации, либо оптоволоконные датчики деформации и температуры.
В случае их применения, как правило, в состав элементов трубопроводов включаются специальные элементы – интеллектуальные вставки (рис. 5) – катушки со снятыми остаточными напряжениями и наклеенными оптоволоконными датчиками, что позволяет обеспечить достаточно высокую точность измерения параметров напряженно-деформированного состояния.
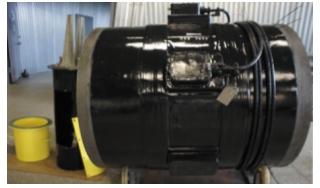
для контроля параметров напряженно- деформированного состояния трубопроводов в процессе эксплуатации
Опыт показывает, что развитие системы технической диагностики с применением описанных технических решений позволяет значительно повысить надежность и безопасность эксплуатации технологических трубопроводов объектов ТЭК.