В 2015 г. АО «ННК–Хабаровский НПЗ» отпраздновал свое 80-летие. Заводу, который обеспечивает своей продукцией и Восточную Сибирь, и весь Дальний Восток, пришлось пройти нелегкий путь и так же, как и другим, пережить и Великую Отечественную войну, и развал Советского Союза, и несколько экономических кризисов, в том числе и нынешний. Несмотря ни на что, 1 385 сотрудников завода во главе с генеральным директором Сергеем Николаевичем Скуридиным не сдаются и намерены двигаться только вперед. В планах завода увеличивать объем и улучшать качество выпускаемых нефтепродуктов. Об истории завода, его буднях и перспективах нам рассказал его главный механик Александр Викторович Сарыгин.
– Александр Викторович, с чего все началось?
В 1930 г. Совет Труда и Обороны принял постановление о строительстве в Хабаровске нефтеперерабатывающего завода для обеспечения нефтепродуктами развивающего народного хозяйства Дальневосточного края и примыкающих районов Восточной Сибири. Сооружение первенца нефтеперерабатывающей промышленности было признано «ударной новостройкой, имеющей народно-хозяйственное значение».
В соответствии с постановлением Совета Труда и Обороны 27 сентября 1930 г. «Союзнефть» принимает постановление о строительстве нефтеперерабатывающего завода в Хабаровске для переработки сахалинской нефти. Это предприятие было жизненно необходимо для полноценного индустриального развития Восточной Сибири и Дальнего Востока. Растущее число машин и тракторов, кораблей и самолетов, а также новые котельные остро нуждались в топливе. Строительство завода было объявлено ударной стройкой, и на Восток потянулись люди со всех уголков страны. Возводили его на окраине города, но шло время, Хабаровск рос, и предприятие оказалось прямо в его центре. Это обстоятельство создавало определенные сложности, но об этом чуть позже. 5 августа 1935 г. была сдана в эксплуатацию комбинированная крекинг-установка и получены первые литры автомобильного бензина и тракторного керосина, моторного топлива и мазут. Этот день считается Днем рождения завода. Решением Правительственной комиссии заводу было присвоено имя наркома тяжелой промышленности СССР Серго Орджоникидзе.
В 1939 г. предприятии провело реконструкцию установки №1, и это сразу дало результаты: ее производительность увеличилась в 2,5 раза. Объем отбора светлых нефтепродуктов тоже вырос. Тогда же в строй была введена и битумная установка.
Поначалу сырье для завода доставляли на самоходных баржах из Сахалина по Татарскому проливу, потом – по реке Амур, так что сроки работы напрямую зависели от периода навигации. И только в 1950 г. ХНПЗ перешел на работу с сернистой нефтью из Волго-Уральской нефтегазоносной области, известной как второе Баку. Сырье стало поступать в вагоно-цистернах по железной дороге, и это позволило сменить сезонный характер работы на круглогодичный. Для этого были построены сливная эстакада, установка термохимического обессоливания нефти и этилосмесительная установка.
– В годы войны ваше предприятие находилось вдалеке от линии фронта, и наверняка нагрузка на завод увеличилась?
Люди понимали, что каждый день гибнут тысячи советских солдат и мирных жителей, и работали, не жалея ни времени, ни сил. В первый год войны удалось внедрить более 150 рационализаторских предложений, и это принесло более 1 млн. руб. «Все для фронта, все для Победы!» – прибыль государства за счет предприятия росла, и в 1945 г. выпуск нефтепродуктов увеличился в 3,5 раза. Был создан цех по выпуску спецпродукции, в котором работали одни женщины. Они изготавливали пробки для ручных гранат и артиллерийских снарядов.
В годы войны завод стал выпускать смазочные масла для сельского хозяйства Дальнего Востока.
В 1956 г. вступили в строй действующих блок стабилизации крекинг-бензинов и установка по очистке сжиженного бытового газа, что стало началом газификации Хабаровского края.
До начала перестройки завод построил несколько новых установок и расширил ассортимент выпускаемой продукции. В 1965 г. была построена установка по сернокислотной очистке дистиллатов дизельного топлива и начался выпуск трансформаторного масла. В 1965 г. была сдана в эксплуатацию электрообессоливающая установка (ЭЛОУ), которая пришла на смену термохимобессоливанию.
В 1973 г. была сдана в эксплуатацию установка каталитического риформинга (ЛГ-35-11/300-95) – это дало возможность обеспечить Дальний Восток высокооктановым бензином. В 1988 г. была введена в эксплуатацию установка ЭЛОУ-АВТ, которая заменила морально и физически устаревшую установку АВТ-2.
– В 1991 г. перестала существовать самая большая в мире держава – СССР. Канули в лету плановая экономика, налаженное сотрудничество между предприятиями разных республик. Смута ХХ века – как вы ее пережили?
– Развал Советского Союза довольно болезненно отразился на нашей деятельности – рост курса доллара, неплатежеспособность покупателей, а значит, и снижение спроса на продукцию. Несмотря на нестабильное положение дел в стране, мы продолжали работать и расширяться. И даже получили право на самостоятельный экспорт своего товара за рубеж.
Ввод в эксплуатацию в 1997 г. на установке АТ новой нагревательной печи вертикально-факельного типа ПВ-1 позволило заменить три старых печи шатрового типа.
В 1998 г. мы на риформинге заменили катализаторы и стали выпускать высокооктановые бензины АИ-93 и АИ-95, а также ввели в эксплуатацию новую абсорбционно-газофракционирующую установку (АГФУ) взамен существовавшей.
В стране произошел дефолт, курс рубля резко упал, и импорт топлива стал очень разорительным, а экспорт, напротив, выгодным. Число желающих купить нашу продукцию выросло в разы. Это и помогло нам вернуть и сохранить устойчивое положение на рынке Дальнего Востока.
– Как завод проводил старое и встретил новое тысячелетие?
– В 2000 г. собственником завода стала «Группа Альянс», и это дало ему ряд преимуществ – мы перестали беспокоиться о том, где взять сырье и кому сбыть готовую продукцию. Нам предстояло решить несколько серьезнейших проблем – оборудование изрядно износилось, а глубина переработки нефти была низкой (всего 54,5%).
Более того, следовало увеличить объем выпускаемой продукции, чтобы миллионы потребителей не испытывали недостатка в ней. Дело в том, что на Дальнем Востоке ее производят только два предприятия – АО «ННК–Хабаровский НПЗ» и ООО «РН–Комсомольский НПЗ». Стоит кому-нибудь из нас заняться плановым ремонтом, и нехватка дизельного топлива или бензина может осложнить всем жизнь. Учитывая это, мы занимаемся ремонтом в марте–апреле, когда сельскохозяйственная техника в ожидании пахотного сезона находится на каникулах, а в резервуарах завода накапливаются нефтепродукты.
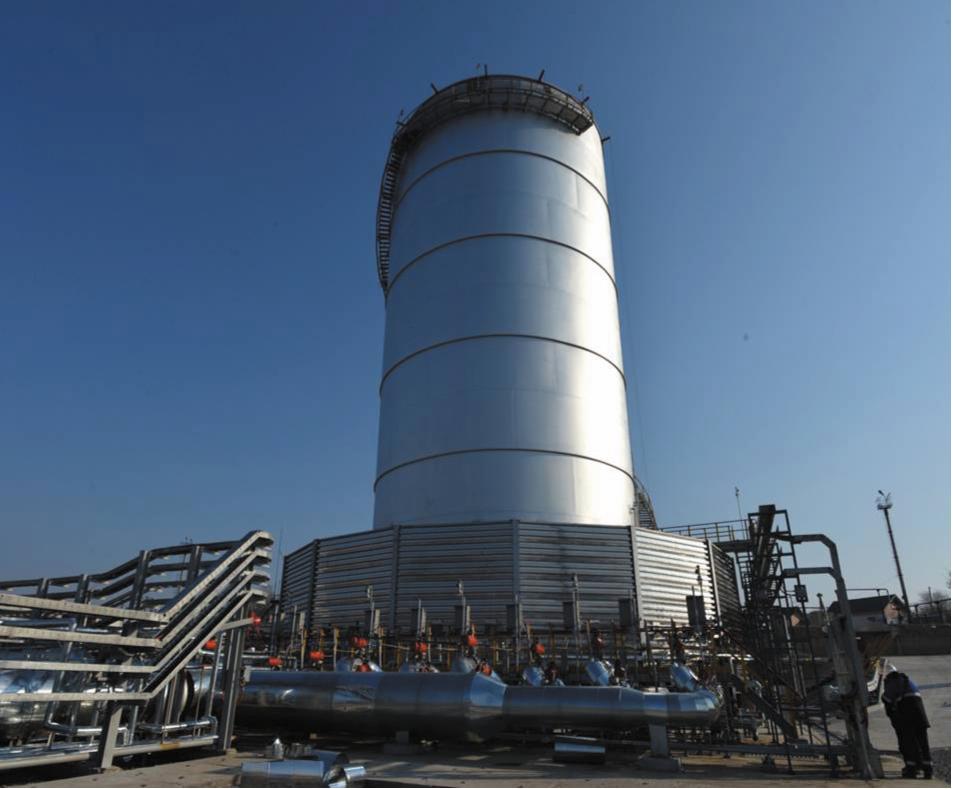
С мая по сентябрь у НПЗ весьма напряженный график, поскольку мы должны обеспечить северные районы нефтепродуктами на зиму.
С учетом всех требования и целей руководством «Группы Альянс» было принято решение о проведении генеральной реконструкции НПЗ. Комплексная программа технического перевооружения разделила этот процесс на два этапа. Первый продолжался с 2000 по 2007 гг. и обошелся в 3,3 млрд. рублей. Ситуацию усложняло то, что предприятие, как я уже говорил, находится прямо в центре города, и ему катастрофически не хватает места.
Кроме того, месторасположение завода обусловливает жесткие экологические требования к нему. Производство должно быть максимально безопасным и безвредным для окружающей среды.
Что нам удалось реализовать за 7 лет? Мы реконструировали в 2000 г. основную установку первичной переработки нефти (установка №1) с целью увеличить отбор светлых нефтепродуктов. С этой целью была установлена новая колонна для атмосферной перегонки нефти. В 2001 г. на установке АГФУ на базе существующего оборудования был смонтирован блок моноэтаноламиновой очистки сжиженного газа. В том же 2001 г. началась реконструкция очистных сооружений.
На первом этапе были заменены реагенты и автоматизирован процесс их приготовления и подачи во флотационные установки.
В 2004 г. ввели в эксплуатацию установку изомеризации легких бензинов производительностью 108 000 т в год. И в результате первыми на Дальнем Востоке стали выпускать высокооктановые бензины, соответствующие стандарту Евро-4. Ввод в эксплуатацию в 2005 г. установки «Флоттвег» по переработке нефтешламов позволил решить проблему утилизации накопившихся на территории завода отходов, образующихся при переработке нефти. В 2005 г. ввели в эксплуатацию современную технологическую парокотельную производительностью 100 т пара в час. Были демонтированы выведенные из эксплуатации установки, в том числе и насосное хозяйство для смешения сырья с присадками. Устаревшие сооружения на территории завода не задерживаются, ведь каждый метр территории – на вес золота.
В 2006 г. на НПЗ был построен комплекс эстакады налива светлых нефтепродуктов, рассчитанный на 44 вагоно-цистерны, чуть позже – в 2008 г. – эстакада налива темных нефтепродуктов.
Очистные сооружения, вода после которых попадает в Амур, подверглись дальнейшей реконструкции и модернизации. В 2006 г. и 2007 г. были построены два современных флотатора австрийской компании Koreko KWI. Это позволило достичь гарантированной очистки сточных вод по содержанию нефтепродуктов до концентрации 4 мг/л. В 2011 г. на очистных сооружениях ХНПЗ был запущен флотофильтр (Koreko KWI) с новыми реагентами, что позволяет достичь содержания нефтепродуктов в сточных водах на выходе до 0,7 мг на литр.
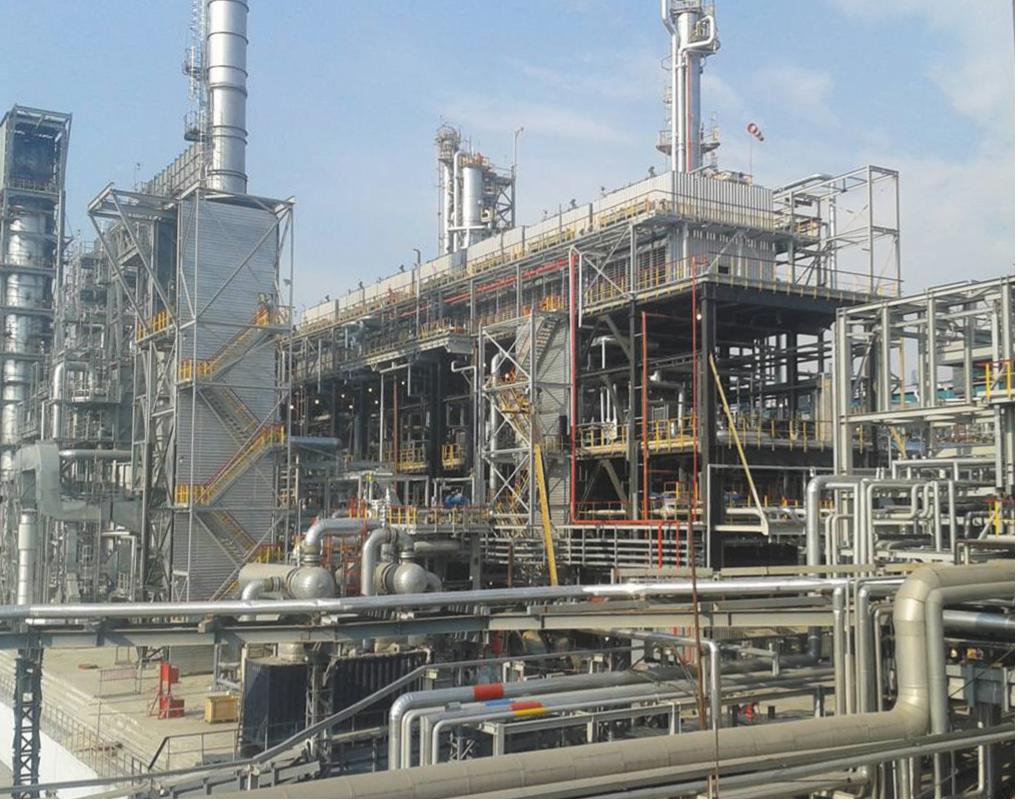
В результате совместной деятельности сотрудников завода и лаборатории компании Shell Global Solutions с 2006 г. на фирменных заправках НК «Альянс» стали продавать бензин «АИ-95 – зимний», с которым в зимних условиях проще заводить транспортные средства, а срок службы двигателей увеличивается. Более того, с 2007 г. мы наладили производство новых автобензинов АИ-95 и АИ-98 марки «GreenEco».
Проведенная за 7 лет работа помогла нам расширить ассортимент продукции до более чем 20 наименований.
– Какие проекты вам предстояло реализовать на втором этапе реконструкции?
– Второй этап реконструкции предусматривал реализацию двух довольно масштабных проектов. Один из них – «Проект 800». Генеральный подрядчик – международная инжиниринговая компания Técnicas Reunidas.
На территории завода был построен комплекс гидрокрекинга и гидроочистки (ГКГО). Он включает несколько установок: гидроочистки авиационного керосина и дизельного топлива (1 180 000 т в год); гидрокрекинга вакуумного газойля (506 000 т в год) и производства водорода (22 000 т в год). Более того, мы теперь можем ежегодно производить в год до 13 400 т новой для нас продукции – гранулированной серы, выделяемой в процессе производства из нефтепродуктов. В производственных процессах комплекса ГКГО применены передовые технологии по лицензиям известных компаний – Shell, Foster Wheeler, Technip KTI.
Параллельно был реализован «Проект 190». В его реализации были задействованы мы сами и российские подрядчики. Были переоборудованы действующие производства и объекты общезаводского хозяйства для обеспечения работы комплекса ГКГО. Кроме того, в 2010 г. провели 1-й этап реконструкции установки каталитического риформинга. а также построили установку висбрекинга мощностью 750 000 т в год с сырьевым блоком вакуумной переработки мазута мощностью 1,8 млн. т в год.
В рамках реализации экологической программы завод планомерно избавляется от старых клепаных резервуаров, построенных еще в конце 30-х годов. Всего их было более 100, осталось разобрать еще 12. Работы планируется завершить в 2018 г. Новых резервуаров почти в полтора раза меньше (78), зато они в два раза выше и достигают 24 м в высоту, т.е. способны вмещать гораздо больше продукции на тех же производственных площадях. В прежнем резервуарном парке мы могли хранить 98 000 м3 продукции, в нынешнем – 198 000 м3 продукции. Для постройки новых резервуаров на месте старых нам пришлось пререобвязать множество резервуаров для хранения необходимого (потребного в определенное время) нефтепродукта.
В 2009 г. заработала первая очередь новой химводоподготовительной установки (ХВПУ). На установке готовят воду, которая подается в котельную завода для выработки пара. В 2010 г. построен новый блок электрообессоливания сырья на установке первичной переработки, новая бойлерная. В эксплуатацию пущена вторая очередь химводоподготовительной установки.
Деминерализованная вода, которую мы получаем из нее, необходима для производства водорода. Началась реализация проекта перевода заводских потребителей топлива на использование природного газа от газопровода «ГРС-3 – ХТЭЦ-2». В эксплуатацию введена воздушно-кабельная ЛЭП 110 кВ от Хабаровской ТЭЦ-3 до врезки в существующие линии электроснабжения завода. В то же время закончили сооружение трансформаторной подстанции «НПЗ–2» 110/6 кВ. ЛЭП и подстанции создают запас мощности, необходимый для электроснабжения объектов реконструкции завода, а также для присоединения к энергосистеме дополнительных электрических нагрузок. Это позволяет повысить надежность электроснабжения потребителей и дает дополнительные возможности для развития промышленности и инфраструктуры Хабаровска.
В 2011 г. мы реконструировали реагентное хозяйство, приведя его в соответствие с требованиями современных норм и правил, а также значительно увеличив и расширив парк емкостей для хранения возросшего количества и ассортимента различных реагентов.
В 2012 г. был сдан в эксплуатацию промежуточный резервуарный парк, который помогает распределять вырабатываемую продукцию по видам. Кроме того, был построен блок деизопентаризации (ДИП) на АГФУ с целью получения сырья для секции изомеризации требуемого качества. На секции изомеризации установили дополнительный блок стабилизации готовой продукции, увеличили мощность реакторного блока, заменили реакторы и катализатор. Это позволило заводу в 2013 г. приступить к выпуску автомобильных бензинов стандарта Евро-5.
Осенью 2013 г. заработала новая установка по производству азота мощностью 4 млн. м3 в год. В 2013 г. была введена в эксплуатацию закрытая факельная установка (разработана американской фирмой Zeeco inc), мощностью 150 т газа в час и эффективностью удаления продуктов разрушения газообразных отходов почти 100%. Надо сказать, что раньше факел раздражал жителей города, особенно когда дымил. Теперь его работа вне поля зрения горожан.
В феврале 2013 г. мы перевели два котла котельной №2 на природный газ и тем самым завершили второй этап проекта по переводу заводских котельных на этот вид топлива. В 2013 г. заменили оборудование на установке риформинга и все насосы на установке ЭЛОУ-АВТ заменили новыми (44 насоса), где входит блок СПБ, который готовит сырье для риформинга. В результате производительность риформинга увеличилась до 450 000 т в год. В 2013 г. реконструкции подвергся вакуумный блок установки ЭЛОУ-АВТ, после чего его производительность увеличилась до 1 080 тыс. т мазута в год.
В 2013 г. в рамках строительства комплекса ГКГО были введены в эксплуатацию дополнительная система оборотного водоснабжения, локальные очистные сооружения (ЛОС) для комплекса ГКГО. В 2014 г. мы вошли в состав АО ННК «Независимая нефтегазовая компания», это дало уверенность в завершении реконструкции.
В 2014 г. сданы в эксплуатацию комплекс гидропроцессов (ГКГО-500/1000); установка по производству водорода (УПВ-22); установка по производству элементарной серы (КУС-13) для регенерации аминов и отпарки кислых стоков с блоком очистки хвостовых газов; первая очередь блока подготовки сырья битумной установки – вакуумный блок производительностью 1800 тыс. т в год и сдана в эксплуатацию установка сплитер нафты. На сегодняшний день без увеличения площадей оборудование завода увеличилось в 2,6 раза.
Один из главных проектов модернизации Хабаровского НПЗ был завершен 1 сентября 2015 г. Завод подключили к системе ВСТО (Восточная Сибирь – Тихий океан), от нефтепровода построили отвод длиной в 28 км, девять из которых проходят в микротоннеле прямо под городом на глубине 14 м с системой обеспечения полной безопасной перекачки нефти (труба в трубе с заполнением межтрубного пространства инертным газом с датчиками перепада давления), тем самым обеспечив надежную поставку нефти на завод. В перспективе – увеличить перекачку нефти до 6 млн. т в год и закончить реконструкцию эстакады для вывоза готовой продукции. Осталось завершить строительство установки висбрекинга производительностью 700 тыс. т в год для подготовки высококачественного сырья для существующей битумной установки. Необходимо дооснастить старые установки отсечными автоматическими устройствами, которые в непредвиденных ситуациях будут отсекать перемещение нефтепродуктов.
– Александр Викторович, реализация всех проектов должна завершиться к 2018 г. Но наверняка уже можно говорить о каких-то результатах?
– Да, конечно. У нас увеличился выпуск светлых нефтепродуктов, а качество автобензина и дизельного топлива соответствуют всем требованиям Евро-5. Кроме того, завод теперь выпускает авиационное топливо международного стандарта Jet A-1. Еще один важный итог – мы стали безопаснее для окружающей среды. Интегральный показатель технологической сложности завода (индекс Нельсона) почти утроится и достигнет 9,9. Благодаря грамотному руководству ННК, это будет один из самых передовых уровней нефтепереработки в отрасли.
Качество продукции увеличилось, а значит, выросла и ее конкурентоспособность. Нам есть чем гордиться.
– Ну что ж, спасибо за подробный рассказ о вашем заводе. Мы искренне желаем вам успехов в работе.