Автор: С.Ю. Филиппов ((ООО «Стратегия НК»).
Опубликовано в журнале Химическая техника №5/2015
Большая часть оборудования трубопроводов пара и горячей воды имеет длительный срок эксплуатации и зачастую уже неоднократно продленный в результате проведения экспертизы промышленной безопасности ресурс.
Согласно действующему законодательству эксплуатация и обслуживание трубопроводов пара и горячей воды ведется в соответствии с Федеральными нормами и правилами «Правила промышленной безопасности опасных производственных объектов, на которых используется оборудование, работающее под избыточным давлением».
По истечении срока эксплуатации трубопроводы должны быть подвергнуты экспертизе промышленной безопасности. Объем технического диагностирования трубопроводов определяется нормативными документами СО 153-34.17.464-2003, РД 10-577-03 и др.
Указанная нормативная документация предполагает проведение на объекте выборочного локального контроля. При этом большая часть диагностических работ проводится на выведенном из эксплуатации объекте.
Это связано с температурными ограничениями применимости оборудования неразрушающего контроля и безопасностью для персонала.
Для контроля, как правило, выбираются доступные участки трубопровода, вблизи площадок обслуживания, арматуры, спусков трубопровода с эстакад. Данные ограничения в конечном итоге приводят к пропуску существующих опасных дефектов (рис. 1), а также зачастую не выявляют негерметичность отдельных узлов и запорно-регулирующего оборудования.
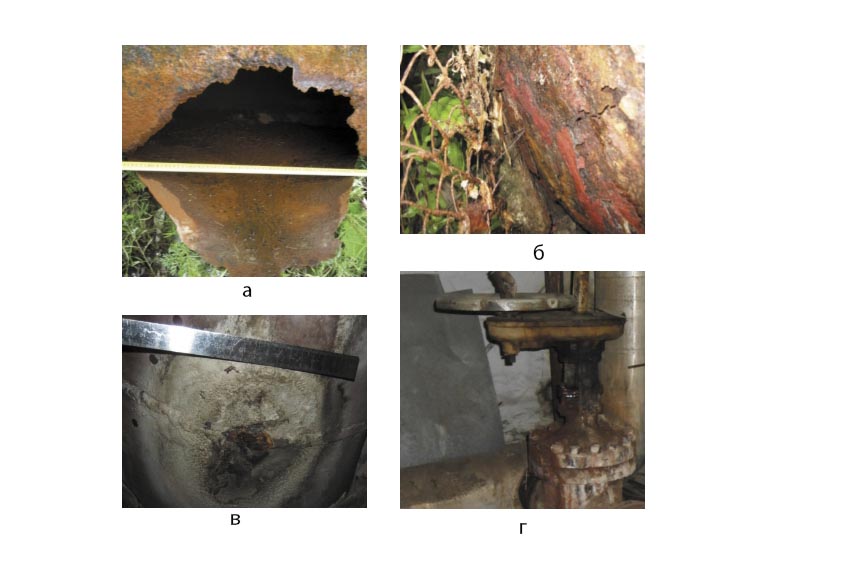
а – разрыв трубопровода горячей воды; б – сквозная коррозия стенки трубопровода; в – локальная коррозия на сварном соединении; г – течь через шток ЗРА
Кроме того, необходимо отметить, что при эксплуатации трубопроводов особую опасность представляет локальная, неоднородная коррозия, которая может образовываться как в результате механических повреждений изоляционного покрытия и попадания влаги в пространство между трубопроводом и защитным покрытием, так и в результате напряжений, существующих в металле – стресс-коррозии. Без проведения специальных диагностических мероприятий такие дефекты практически невозможно выявить, вплоть до возникновения аварии.
Специалистами ООО «Стратегия НК» был проведен ряд экспериментальных работ по диагностике технического состояния трубопроводов пара с применением метода акустической эмиссии без вывода их из эксплуатации (рис. 2).
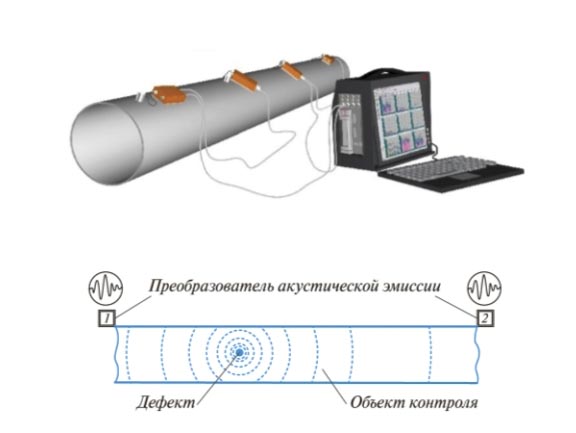
Метод АЭ относится к интегральным методам НК, т.е. при его проведении контролируются сразу все участки трубопровода от начала и до конца, включая все элементы, запорную и регулирующую арматуру, а также состояние фланцевых и сварных соединений.
Первая работа была проведена на действующем трубопроводе пара. Контроль осуществлялся с применением акустико-эмиссионной системы A-LINE 32D (DDM).
Техническая характеристика паропровода
Диаметр, мм 273
Толщина стенки, мм 6
Рабочая температура, °С 250
Материал Сталь Ст20
Рабочая среда Водяной пар
Давление, МПа
В ходе подготовки к проведению данной работы необходимо было решить ряд задач, основной из которых была установка преобразователя акустической эмиссии на трубопровод. Для проведения АЭ контроля использовался стандартный АЭ-преобразователь с рабочей температурой до 110°С.
Для решения этой задачи был рассчитан волновод (рис. 3, а) изготавливаемый из металлической трубы и пластины и устанавливаемый посредством сварки на трубопровод пара. Места установки были выбраны таким образом, чтобы обеспечить контроль всей протяженности паропровода (рис. 3, б). Применение волновода позволило использовать стандартные преобразователи, так как температура в верхней его части не превышала 70 °С.
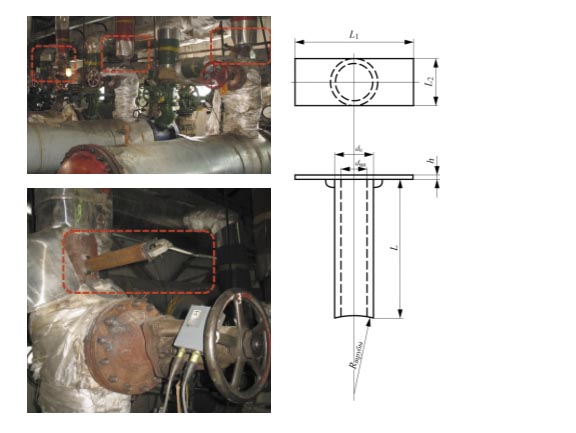
Во время проведения диагностических работ эксплуатирующая организация временно остановила подачу пара в контролируемый трубопровод, а затем возобновила ее вновь. В итоге было реализовано изменение внутреннего давления с 0,2 до 0,6 МПа. Данная процедура не повлияла на общую работу предприятия, так как отключение носило кратковременный характер.
В результате проведения данной работы был выявлен активный источник акустической эмиссии. При этом источник проявлял себя во всех циклах изменения давления.
На месте регистрации указанного источника был обнаружен значительный коррозионный износ металла трубопровода (рис. 4). Данный дефект был обнаружен на участке перехода трубопровода через бетонное перекрытие, на высоте 5 м над уровнем пола. Точное положение источника было установлено по характерной локационной диаграмме между 17-м и 18-м измерительными каналами.
По результатам АЭ-диагностики эксплуатирующие службы заказчика были немедленно осведомлены об обнаруженном дефекте. После проведения акустико-эмиссионного контроля на данном участке трубопровода была проведена подробная толщинометрия, по результатам которой было выявлено утонение более чем на 50% от номинальной толщины стенки. Данный участок трубопровода был рекомендован к замене.
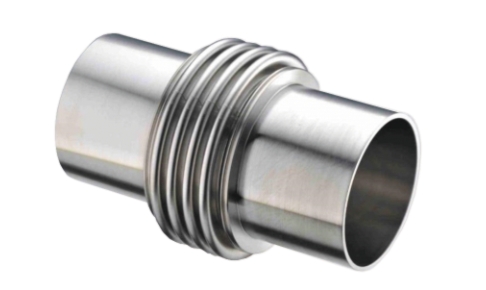
В 2013 г. специалисты ООО «Стратегия НК» были приглашены для технического диагностирования компенсаторов (рис. 5) горячей обвязки реакторного блока.
Характеристики обследуемого объекта приведены ниже:
Объект контроля Осевой сильфонный компенсатор
Диаметр, мм 830
Толщина стенки, мм 15
Рабочая температура, °С 800
Материал Incoloy 800H (аналог стали ХН32Т)
Рабочая среда Перегретый водяной пар
Давление, МПа 0,1
В ходе эксплуатации реакторного блока заказчиком были выявлены разрушения компенсаторов (рис. 6). Разрушения имели локальный характер и присутствовали в той или иной степени на всех компенсаторах.
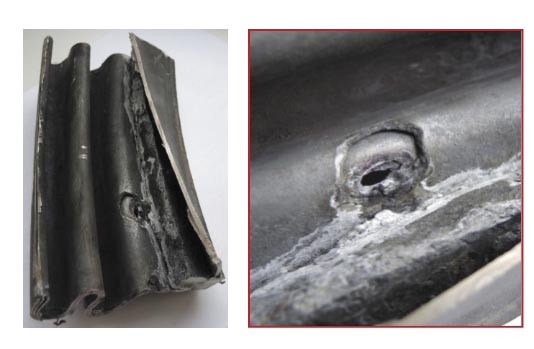
Установка была остановлена и был заменен большой ряд данных элементов, после чего реактор был вновь запущен в работу. Перед специалистами ООО «Стратегия НК» была поставлена задача контроля технического состояния вновь установленных компенсаторов на рабочих параметрах. Были продиагностированы пять компенсаторов.
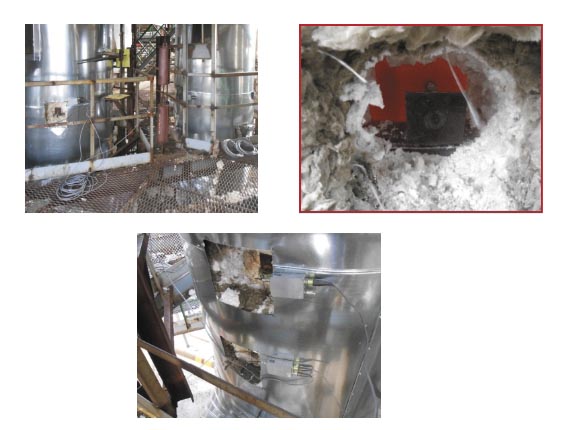
Для построения локационной картины была использована планарная локация (рис. 7). ПАЭ были установлены в двух поясах перед и после каждого компенсатора по три штуки в поясе (рис. 8). Для снижения температуры в местах установки преобразователей АЭ также использовались волноводы.
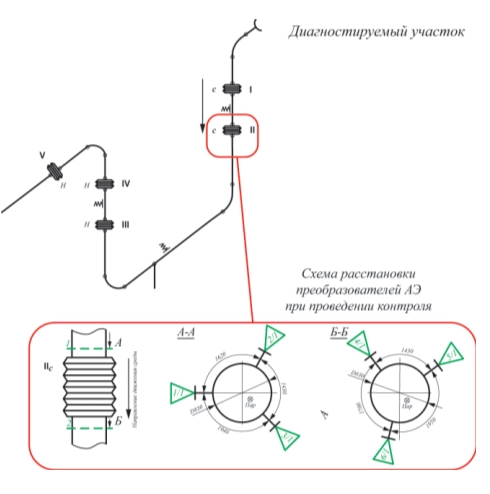
для построения локационной картины
В результате проведения акустико-эмиссионного контроля в режиме мониторинга компенсатора II и IV выявлены источники АЭ, соответствующие развивающимся дефектам (рис. 9). На компенсаторах I, III, V источники АЭ, соответствующие развивающимся дефектам, не обнаружены.
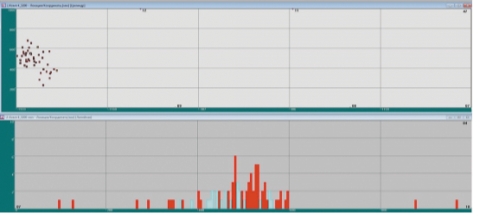
В ходе выполненной работы было установлено, что вновь установленные компенсаторы также подвержены разрушению. Удалось определить координаты источника акустической эмиссии на действующем оборудовании при наличии значительного уровня внешних шумов.
Результаты контроля были переданы заказчику, с рекомендациями о проведении дополнительного дефектоскопического контроля обнаруженных источников АЭ.
Кроме того, для установки причины возникновения разрушения металла, было рекомендовано провести металлографические исследования разрушенного участка компенсатора, а также химический анализ на соответствие марки стали.
Проведенная специалистами ООО «Стратегия НК» работа позволяет сделать однозначный вывод о следующем:
- акустико-эмиссионный контроль на рабочих параметрах оборудования позволяет выявлять дефекты и определять потенциально опасные участки оборудования;
- применение интегрального АЭ-контроля позволяет контролировать объект на всей его протяженности, что исключает возможный пропуск опасных развивающихся дефектов;
- диагностика во время эксплуатации позволяет выявить потенциальные дефекты, проявляющие себя только рабочем, так называемом «горячем» режиме, зарегистрировать негерметичность отдельных узлов трубопроводов и запланировать их замену или ремонт в очередной останов;
- периодическое проведение АЭ диагностики трубопроводов на рабочих параметрах без вывода оборудования из эксплуатации предотвращает развитие дефектов до критических параметров и осуществляется без нарушения нормального режима функционирования оборудования, без дополнительных затрат на остановы, разогревы и пуски оборудования.