Автор: С.В. Панченко, В.А. Платонов, Ю.Н. Тюрин, М.С. Трещева, С.В. Дьяконов (ОАО «НОРЭ»).
Опубликовано в журнале Химическая техника №5/2015
Стеклопластик обладает рядом преимуществ перед металлическими конструкционными материалами: относительно небольшая масса при высокой прочности; хорошая коррозионная стойкость, которая обеспечивается применением химически стойких связующих и нанесением химзащитных покрытий; монолитная конструкция (отсутствие сварных швов); высокая вибрационная устойчивость; небольшой коэффициент линейного расширения.
В химической промышленности аппаратура из стеклопластиков заменяет аппаратуру из коррозионностойких и высоколегированных сталей, сплавов и цветных металлов.
При этом она легче и в ряде случаев более долговечна. Из стеклопластика изготавливают емкости для хранения и транспортировки кислот и щелочей, газоходы, абсорберы, корпусы насосов для агрессивных веществ и др.
Оболочечные конструкции чаще всего изготавливают методом намотки на оправку стекловолоконной основы, пропитанной полимерным связующим. В качестве примера на рис. 1 показана нижняя часть корпуса абсорбера, применяемого в производстве минеральных удобрений.
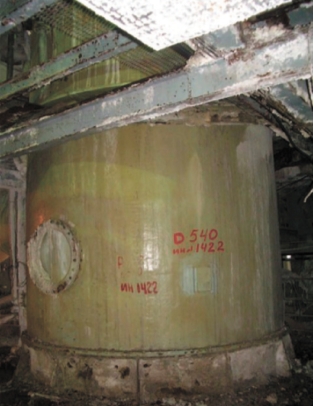
Высота аппарата – 9 м, внутренний диаметр – 2,5 м, рабочая среда – смесь фосфорной и серной кислот. Срок эксплуатации – 30 лет.
В связи с широким распространением стеклопластикового оборудования возникла необходимость определения принципов диагностирования его технического состояния и прогнозирования возможности дальнейшей эксплуатации изделий из стеклопластика, выработавших проектный срок службы.
По своим физическим свойствам композиционные материалы существенно отличаются от металлических, что обусловлено структурными особенностями полимеров и стекловолокна, а также особенностями взаимодействия структурных составляющих композита.
Одним из значимых свойств стеклопластика является анизотропия прочностных свойств в зависимости от направления волокон основы, поэтому направление намотки стекловолокна, определяемое при проектировании оболочечных стеклопластиковых конструкций, обычно совпадает с направлением наибольшей нагрузки.
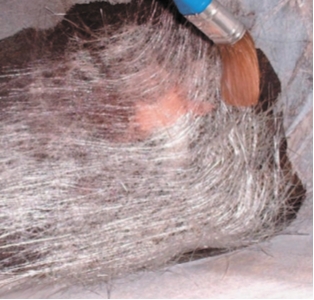
Для сосудов и аппаратов цилиндрической формы, работающих под избыточным внутренним давлением или при наливе, наибольшим является растягивающее тангенциальное напряжение, в связи с чем намотка чаще всего производится спиралеобразно под небольшим углом вокруг оси обечайки. Для сосудов, работающих под действием наружного давления и осевой сжимающей силы, которые могут приводить к потере устойчивости оболочки, наиболее рациональной является спиральная косая перекрестная намотка.
Механизм повреждения стеклопластика также имеет свои особенности.
Стеклопластиковые конструкции не подвержены коррозионному износу в обычном понимании. Срок службы стеклопластика определяется его долговременной прочностью – способностью сопротивляться пластической деформации под действием нагрузки и потере механических свойств при взаимодействии с рабочей и окружающей средой.
При работе стеклопластика (под работой подразумевается сопротивление материала приложенной нагрузке) в начальный момент времени часть нагрузки воспринимается стекловолокном, а другая часть – связующим полимером. В дальнейшем происходит перераспределение усилий между стекловолокном и связующим. Последнее постепенно разгружается в силу большей, чем у стекловолокна, пластичности, а стекловолокно – догружается.
С увеличением напряжения в стекловолокне деформации в нем увеличиваются, а, следовательно, увеличиваются деформации оболочки.
Такой процесс во многом аналогичен высокотемпературной ползучести металлов, сопровождающейся деградацией микроструктуры и приростом деформации.
По мере эксплуатации под действием рабочих нагрузок в композитном материале происходит постепенное накопление различных повреждений. Повреждения могут быть самыми разными: разрыв отдельных стеклянных волокон и нитей, нарушение структуры связующего (образование микротрещин в связующем и т.д.), расслоение. В тот момент, когда суммарные повреждения достигают опасного уровня, происходит разрушение материала. На рис. 2 приведена зависимость уменьшения прочности стеклотекстолита марки ВФТ при выдержке под нагрузкой при температуре 200°С.
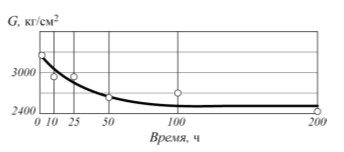
Из-за неизбежной деструкции длительная прочность стеклопластика значительно ниже кратковременной прочности. На прочность материала, помимо температуры, активно влияет влажность (в жидких средах, даже химически нейтральных, процесс потери прочности протекает интенсивнее). Это связано с тем, что влага ухудшает адгезию стекловолокна к связующему и может снижать прочность стекловолокна.
Усталостная прочность стеклопластиков зависит в большей степени от свойств связующего. Так, стеклопластики из эпоксидной смолы обладают большей усталостной прочностью, чем стеклопластики из полиэфирных смол. При этом понятия предела усталости для стеклопластиков не существует, прочность их снижается равномерно с увеличением количества циклов нагрузки и времени эксплуатации. Из-за достаточно низкой теплопроводности и достаточно высокой вязкости стеклопластиков при действии знакопеременных нагрузок происходит нагрев нагруженного материала, что также отрицательно сказывается на его долговечности. Положительным свойством стеклопластика является гораздо меньшая, чем у металлов, чувствительность к влиянию трещин на несущую способность. Это объясняется эффективным затуплением краев растущей трещины волокнами основы [1]. Таким образом, стеклопластиковые конструкции менее опасны в плане возможности развития быстрых катастрофических разрушений.
Прочностные свойства стеклопластиков и их изменение при эксплуатации значительно зависят от технологии изготовления, свойств исходного сырья, соотношения компонентов композита (основы и связующего), значения действительной нагрузки, воздействия рабочей температуры и окружающей среды [2].
До настоящего времени не существует достоверной расчетной методики, позволяющей оценить степень изменения свойств стеклопластика по комбинации перечисленных критериев и воздействий, поэтому при определении технического состояния стеклопластиковых конструкций в ходе эксплуатации на первый план выходит натурное обследование.
Традиционные принципы неразрушающего контроля металлических материалов неприменимы к стеклопластиковым изделиям, так как подразумевают однородные акустические свойства среды (ультразвуковой контроль) и однородную структуру (радиографический контроль), электрическую проводимость (вихретоковый контроль) и т.п. В связи с этим алгоритм диагностики сводится к определению деформации оболочки, подробному визуальному осмотру с целью обнаружения видимых повреждений и испытаниям образцов.
Отбор образцов желательно производить с участков, где проведение ремонта максимально упрощено.
Механические испытания образцов проводят в соответствии с требо-ваниями нормативных документов и рекомендациями изготовителя оборудования. При этом оценивают предел прочности материала и его соответствие техническим условиям изготовителя. Число образцов определяется в зависимости от способа изготовления изделия и условий его работы и с учетом анизотропии прочностных свойств материала.
Оптимальным с точки зрения достоверности результатов испытаний является образец, содержащий все сечение элемента оболочки (стенки сосуда, например), отобранный из зоны с максимальным влиянием повреждающих факторов (температура, механические напряжения, агрессивное воздействие среды или влаги).
Однако на практике отбор образцов производится с участков вспомогательных элементов конструкции (ребра жесткости, малонагруженные фланцы и т.п.). Это делается для максимально возможного сохранения несущей способности сосуда.
В том случае, если при проектировании было предусмотрено наличие нагруженных образцов-свидетелей, проведение испытаний значительно облегчается и увеличивается информативность результатов испытаний.
Среди емкостного оборудования, применяемого в агрессивных по отношению к стеклопластику средах, достаточно часто встречаются сосуды с внутренней футеровкой из термопластов – полиэтилена, полипропилена и др. Футеровка может быть изготовлена из листов или колец, сваренных или склеенных между собой. На долговременную прочность корпуса сосуда в таком случае напрямую влияет герметичность футеровки. Сварные швы футеровки контролируют электроискровым методом.
Для обеспечения возможности проведения контроля при монтаже футеровки под сварные швы подкладывают полоски металлической фольги.
Вдоль поверхности готового сварного шва футеровки перемещают электрод, который подключается к выходу источника напряжения (высоковольтный трансформатор). Токопроводящая подкладка шва подключается ко второму выходу источника напряжения. Пробой электрического разряда при контроле свидетельствует о наличии дефектов в сварном шве.
Преобразованные электрические импульсы фиксирует устройство световой и звуковой сигнализации электроискрового дефектоскопа.
В том случае, если химическая стойкость достигается за счет внутреннего антикоррозийного покрытия стеклопластиковой оболочки, рекомендуется проведение подробного визуального осмотра и, при необходимости, цветной дефектоскопии.
При большой площади контролируемой поверхности рекомендуется акустико-эмиссионный контроль изделия. Во время нагружения оболочечной конструкции испытательным давлением или наливом под действием растягивающих напряжений возможны проявления непластической деформации, сопровождающиеся акустической эмиссией.
В процессе деформирования возможно образование различных дефектов стеклопластиков. Как правило, первым формируется расслоение из-за разрушения адгезии стекловолоконной основы и полимера. «Подрастание» расслоения сопровождается характерными импульсами акустической эмиссии. Большие по интенсивности сигналы соответствуют разрушению связующего, наиболее сильные импульсы связаны с разрывами волокон основы.
Таким образом, акустико-эмиссионный контроль позволяет выявить участки конструкции сосуда, обладающие наименьшим запасом несущей способности, и оптимизировать объем и содержание контроля. Формализованной методики проведения АЭК стеклопластиковых изделий не существует, поэтому способ проведения контроля и критерии оценки результатов контроля в каждом случае должны определяться индивидуально.
Еще один метод контроля стеклопластиковых изделий – это тепловой. Его применение возможно в том случае, если при работе стеклопластиковой конструкции существует разница температур между рабочей средой и окружающим воздухом. При осмотре стеклопластиковой конструкции с использованием тепловизора могут быть обнаружены крупные расслоения с достоверной оценкой их площади.
Важным этапом диагностирования является расчет запаса прочности стеклопластиковой конструкции с учетом снижения прочности в ходе эксплуатации под действием нагрузки, среды и температуры.
При прогнозировании снижения прочностных свойств следует помнить, что действие разных повреждающих факторов носит различный характер. Если деструкция полимерного связующего под действием температуры (при стационарном нагреве) снижает прочность относительно линейно, то воздействие среды определяется нелинейной скоростью диффузии и влагопоглощением материала, а также агрессивностью компонентов среды. Влияние рабочих напряжений на деструкцию материала зависит от распределения напряжений по объему изделия и неодинаково для различных участков конструкции.
Из-за сложности учета влияния разных факторов наиболее точным остается экспериментальное определение изменения прочностных свойств в процессе эксплуатации с экстраполяцией на момент окончания планируемого срока эксплуатации. Образцы, используемые для определения прочностных свойств, следует отбирать с максимально нагруженных участков.
Список литературы
- Бажанов В.Л., Гольденблант И.И., Копнов В.А., Поспелов Ф.Д., Синюков А.М. Сопротивление стеклопластиков. М.: Машиностроение, 1968.
- Степанов Р.Д., Шленский О.Ф. Расчет на прочность конструкций из пластмасс, работающих в жидких средах. М.: Машиностроение, 1981.