Автор: И.М. Гольдин (Компания ROTEX).
Опубликовано в журнале Химическая техника №8/2016
Процесс грохочения сухих сыпучих материалов основан на разделении частиц материала, имеющих разный размер. Грохочение можно условно разделить на два основных процесса: классификацию по размеру, дающую несколько фракций, и на удаление комков или пыли из уже готовой товарной фракции.
Для того, чтобы оценить, насколько эффективно работают грохоты и сита-классификаторы, надо ответить на два вопроса (традиционно на предприятиях стран бывшего СССР легко отвечают на первый из них и практически никогда не пытаются ответить на второй):
- позволяет ли грохот получать требуемую чистоту товарной фракции?
- какова эффективность работы грохота, а именно: какой процент товарной фракции, содержащейся в исходном материале, был извлечен грохотом и не попал в отсев крупной или мелкой фракции?
Эффективность грохота (степень извлечения продукта) – это процентное отношение массы извлеченной товарной фракции к массе целевого продукта, содержавшегося в исходном материале.
Надежность оборудования грохочения, получение заданной чистоты фракции и эффективность извлечения продукта являются тремя основными критериями выбора того или иного оборудования. При этом, если о надежности оборудования можно судить по репутации компании и отзывам коллег с других предприятий, а чистоту фракции можно получить на любом типе оборудования, то для определения эффективности необходимо до выбора оборудования проводить испытания в лаборатории. Подобные испытания позволяют определить экономический эффект от эксплуатации того или иного грохота и проводятся в лаборатории ROTEX бесплатно для заказчика.
Эффективность работы грохота – это производная от нескольких факторов:
- типа движения сит грохота;
- производительности грохота (скорость подачи материала на грохот) и производительности грохота на 1 м2 в единицу времени (т/м2⋅ч);
- угла наклона грохота и связанного с ним реального размера ячейки сита;
- классифицируемого продукта и его характеристик (гранулометрический состав, насыпной вес, сыпучесть и др.).
Рассмотрим, как влияют некоторые из этих факторов на работу оборудования грохочения и классификации на примере грохотов двух разных типов: наклонного вибрационного с вибромоторами и качательного грохота типа ROTEX с сочетанием кругового и возвратно-поступательного типов движений сит (рис. 1).
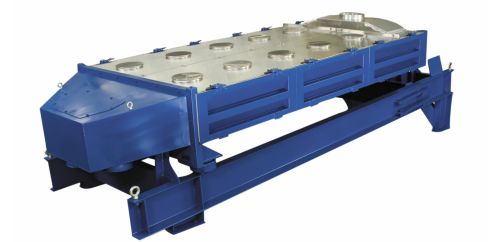
Тип движения сита. Наклонный вибрационный грохот с вибромоторами имеет несколько вибромоторов, возбуждающих ситовую поверхность за счет передачи импульса либо напрямую на сетку, либо через корпус грохота. Угол наклона может варьироваться в среднем от 20 до 35°.
Грохоты типа ROTEX имеют с угол наклона от 4 до 8° с приводом и эксцентриком на конце загрузки и продольными тягами на разгрузочном конце. Преимущества качательного грохота типа ROTEX заключаются в следующем:
- вращательное движение сита на загрузочном конце позволяет материалу быстро и при этом равномерно распределяться по поверхности сита. В большинстве случаев для грохотов даже не требуются специальные питатели;
- линейное возвратно-поступательное движение сит на разгрузочном конце позволяет особо тщательно делать самую трудную работу, а именно просеивание частиц/гранул, близких по размеру, к необходимой отсечке. Например, если необходимо отсечь частицы размером менее 2 мм, то самая трудная задача – отделить друг от друга частицы с размером 1,8; 1,9; 2,0; 2,1; 2,2 мм. До конца сита доходят именно такие сложно просеиваемые частицы. За счет линейного возвратно-поступательного движения большой амплитуды материал постоянно возвращается назад и просеивается несколько раз.
Принцип передвижения частиц по ситу. Для того чтобы частица двигалась по ситу, ей необходимо придать ускорение. Можно выделить два основных принципа ее передвижения. В первом случае необходимо создать вибрацию сита в вертикальной плоскости, чтобы частица подпрыгнула и упала на наклонную поверхность, чтобы снова подпрыгнуть и упасть дальше. Так работает оборудование классификации вибрационного типа. Во втором случае можно заставить частицу двигаться по ситу, не поднимая ее в воздух. Рассмотрим, как это реализовано в оборудовании качательного типа ROTEX (рис. 2).
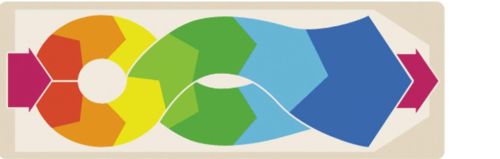
Этап 1. На загрузочном конце грохота, там, где гранула попадает на сито, установлен привод с эксцентриком, который приводит в движение корпус грохота.
Сито движется по кругу, и поток материала равномерно распределяется по всей поверхности сита благодаря этому непрерывному круговому движению.
Этап 2. В середине сита движение приобретает форму эллипса, материал уже распределен по ситу, происходит классификация по размеру.
Этап 3. Ближе к разгрузочному концу сито приобретает исключительно линейное возвратно-поступательное движение за счет продольных тяг, установленных в этой части грохота. Это помогает достигать идеального качества товарной фракции и искусственно увеличивать полезную площадь поверхности сита без увеличения его габаритных размеров. Дело в том, что самая сложная работа по классификации состоит не в отделении крупной фракции (например, гранул размером 2,0 мм) от мелкой (например, пыли размером 0,5 мм).
Эта задача довольно проста: в ячейку 2,0…2,2 мм легко просыпается пыль размером 0,5 мм. Самая сложная работа состоит в том, чтобы отделить фракции, близкие по размеру: если точкой сепарации становится 2,0 мм, то необходимо эффективно отделить гранулы размером 1,7…1,99 мм от гранул размером 2,0…2,3 мм.
Именно близкие по размеру частицы доходят до конца сита из-за того, что их сложно просеять. Возвращая их обратно снова и снова за счет линейного возвратно-поступательного движения большой амплитуды (70…80 мм) на конце грохота, можно достичь тщательного грохочения и при этом не увеличивать размеры оборудования.
Против забивания сит материалом работает технология самоочистки: под ситом находятся шары, которые постоянно отбивают сито и очищают его. Для эффективной работы шаров следует учитывать много факторов: температуру подаваемого материала, его абразивность, липучесть, влажность, материал и размер шаров, размер шаров и многое другое (это может стать темой отдельной статьи).
Важным преимуществом подробно описанного принципа движения сит является то, что гранулы не подпрыгивают на сите, так как принцип движения иной.
Что происходит с частицей, которая попадает на вибросито? Половину времени она проводит в воздухе, а половину на сите, что сокращает вероятность ее попадания в ячейку сита. Именно этот факт является одной из причин, почему для грохочения одного и того же количества материала при прочих равных условиях для качательного грохота необходима меньшая площадь грохочения по сравнению с виброгрохотом.
Угол наклона ситовой поверхности. Принцип классификации частиц по размеру основан на том, что частица продвигается по ситовой поверхности и находит отверстие соответствующего размера, через которое просеивается. Проблема заключается в том, что частица не «видит» номинальный размер ячейки сита, который может быть, к примеру, 2,0 мм. Частица «видит» только проекцию, которая, в свою очередь, зависит от угла наклона сита.
Реальный размер ячейки равен номинальному размеру ячейки, умноженному на косинус угла наклона.
Вибрационные грохоты имеют наклон ситовой поверхности в среднем от 17 до 35°, в то время как грохоты ROTEX качательного типа работают обычно в диапазоне 4…6°. Таким образом, если в грохоте с углом наклона 30° стоит сито с ячейкой 2,0 мм, то через сито смогут просеяться частицы 1,77 мм (2,0 × cos30° = 2,0 × 0,887 = 1,77 мм).
В грохотах с малым углом наклона типа ROTEX смогут просеяться частицы размером 1,99 мм (2,0 × cos4° = 2,0 × × 0,998 = 1,99 мм). Приведенные расчеты относятся к ситу, находящемуся в статике, но при движении сита соотношение остается таким же.
Таким образом, единственное решение при работе с наклонными ситами – это увеличение номинального размера ячейки. Учитывая фактор движения сит, на нижней деке это приводит к просыпанию, а значит к потерям товарной фракции в отсев мелкой фракции, а на верхней деке приводит к просыпанию крупной фракции в товарную, а значит, к ее загрязнению. Сложность состоит в том, что можно выбрать одно из двух: либо сохранить чистоту фракции, но потерять много продукта в отсеве, либо не потерять продукт в отсеве, но засорить товарную фракцию. Очевидно, что заводы выбирают самое важное для них – сохранение чистоты товарной фракции, часто не обращая внимания на потери продукта в отсеве. Это обычно приводит к двум результатам:
- значительному увеличению ретурного числа, перегрузу системы, большому расходу электроэнергии на тонну выпускаемой продукции;
- невозможности увеличить выпуск готовой продукции, а значит, к значительным экономическим потерям предприятия.
Так, вибрационные грохоты, позволяя получить необходимую чистоту фракции, теряют много целевого продукта, который направляется в отсев вместе с мелкой и крупной фракциями. Используя грохоты качательного типа с сочетанием кругового и возвратно-поступательного типов движений сит, можно увеличить извлечение целевой фракции на 10–30% в единицу времени, а следовательно, увеличить производительность линии, цеха, завода. При увеличении даже на 1% производительности гранулятора производительностью, например 100 т/ч, экономический эффект составит (100 т/ч × 1% × 24 ч/сут × × 300 сут/год) × 250 USD/т = 7200 т/год × 250 USD/т = = 1 800 000 USD/год.
А если продукт стоит более 250 USD/т, подача исходного продукта на грохоте более 100 т/ч, рабочих дней в году более 300, то экономический эффект от каждого дополнительного процента объема продукции, полученного за счет более эффективного грохочения, еще масштабнее. Иными словами, если получение дополнительного 1% продукции за счет более качественного грохочения дает такой экономический эффект, то предприятиям имеет смысл бороться за эти проценты и производить еще больше продукции в единицу времени, что и называется эффективностью (рис. 3).
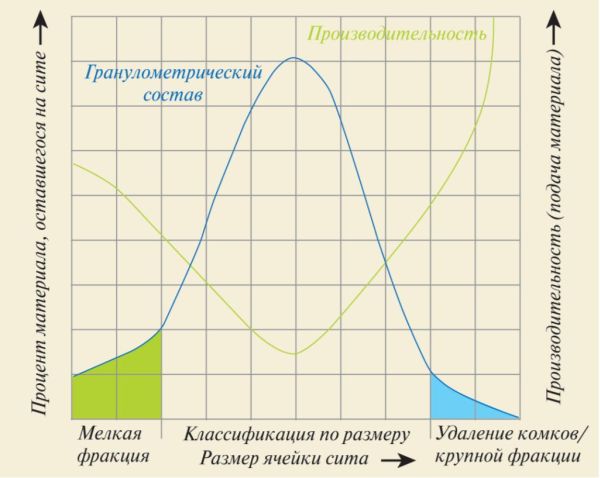
Таким образом, напрашивается вывод, что выбор грохота определяет работу всей производственной линии и либо приводит к потерям, либо позволяет получить значительный экономический эффект от снижения потерь продукции в процессе рассева и увеличения производительности линии при прочих равных условиях.