Автор: А.Б. Жидков, К.В. Чистяков (ООО «Алитер-Акси»).
Опубликовано в журнале Химическая техника №12/2014
Одним из ключевых устройств любой технологической трубчатой печи является горелочное устройство. В связи с этим еще на стадии разработки технического проекта печи важно понимать, какой тип горелочного устройства не только удовлетворит требованиям технического задания, но и обеспечит качественную передачу тепла от сжигаемого топлива сырью. Именно поэтому ООО «Алитер-Акси» тесно сотрудничает с отечественными (ООО «ПКЦ «ИМДОС-М»; ЗАО «НПЦЭО») и зарубежными (Callidus, John Zink, Ruichang, Zeeco) производителями горелочных устройств. Неоднократное посещение испытательных стендов зарубежных компаний в рамках обучения наших сотрудников позволило определить основные направления развития горелочных устройств.
При этом стремление инженеров фирм – изготовителей горелок к созданию технически совершенных устройств не обходится без влияния общемировых тенденций по сохранению окружающей среды – снижению вредных выбросов при сжигании различных компонентов топлива. Кроме того, в ряде стран (США, ЕС) действуют строгие нормативы по количественным и качественным выбросам загрязняющих веществ.
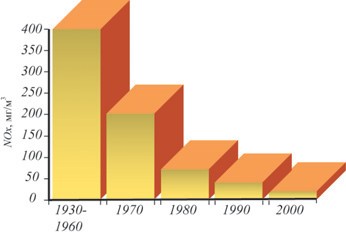
с развитием горелочных устройств
Наиболее распространенными экологически опасными выбросами являются оксиды азота NOx, образующиеся при сжигании топлива любого вида (рис. 1). До 60-х годов прошлого столетия не предпринималось никаких действий по их снижению.
С наращиванием нефтеперерабатывающей промышленностью объемов производства и увеличением глубины переработки нефти путем расширения перечня технологий (каталитический крекинг, бензиновый риформинг, гидроочистка), а также развитием нефтехимии (пиролиз, паровой риформинг и др.) общая экологическая ситуация ухудшалась.
Именно тогда началось пошаговое развитие горелочных устройств, и каждые 10 лет появлялось новое техническое решение, позволяющее снизить выбросы.
Количество выбросов зависит от способа организации топочного процесса, состава топлива, наличия систем очистки уходящих дымовых газов. Оксиды азота при сжигании топлива образуются при окислении атмосферного азота свободным кислородом в процессе горения (высокотемпературный механизмЗельдовича) [1]; по «быстрому» механизму – в результате реакций углеводородных радикалов с азотом воздуха и последующего взаимодействия азотсодержащих и кислородсодержащих радикалов, и в результате окисления азотсодержащих компонентов топлива.
Основная масса NOx образуется по высокотемпературному механизму, поэтому основными действиями по его деактивации является снижение максимальной температуры в зоне горения и сокращение времени пребывания реагентов в ней.
Способы снижения выбросов азота делятся на первичные – проводится оптимизация процесса горения или совершенствование горелочного устройства, и вторичные, представляющие собой системы очистки дымовых газов, которые могут быть каталитическими и некаталитическими.
Системы очистки не получили широкого распространения в технологических трубчатых печах ввиду своей технической сложности и нерентабельности.
Горелочные устройства имеют несколько типов классификации, например: по типу сжигаемого топлива, способу подачи воздуха, расположению на печи и другие. Ко всем этим типам можно причислить горелочное устройство с низкими (<50 мг/м3) и ультранизкими (<20 мг/м3) выбросами NOx. Горелки со сниженным содержанием выбросов NOx могут иметь различные схемы организации горения (газовые горелки).
Раздельная подача топлива в зону горения. Данная схема основана на разделении потока топливного газа на первичный (поступающий в корень факела по центральной части горелки) и вторичный (подаваемый через стволы, расположенные по периметру горелочного камня).
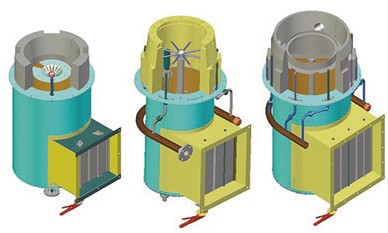
увеличение горелок габаритов в ходе модернизации
За счет избыточного объема воздуха в первичной зоне создается окислительная среда, что приводит к снижению температуры горения и выбросов NOx по температурному механизму. Несмотря на название, объем вторичного топливного газа у некоторых производителей горелочных устройств достигает 80%.
Раздельная подача воздуха в зону горения. Схема аналогична предыдущей, но в этом случае происходит разделение подаваемого воздуха на первичный – в зону горения по центральной части корпуса горелки, и вторичный – воздух подается по каналам в горелочном камне, подача управляется отдельным регулирующим шибером, вмонтированным в корпус устройства. Таким образом, основное сжигание топлива происходит при достехиометрическом отношении (α = 0,8…0,95), что приводит к уменьшению образования топливных окислов азота. Дожигание продуктов сгорания во вторичной зоне проводится со снижением температуры (охлаждение вторичным воздухом), что приводит к снижению выбросов NOx по температурному механизму. Вторичным воздухом можно регулировать (уменьшать) высоту пламени, снижая время пребывания продуктов горения в зоне реакции, что также влияет на количество образующихся загрязняющих веществ.
Данная схема в части технической реализации и эксплуатации горелки является самой сложной. Рециркуляция дымовых газов.
Используя различные формы горелочного камня либо расположение сопл подачи вторичного топливного газа рядом со специальными отверстиями в камне (принцип эжекции), можно организовать подвод продуктов горения в корень факела.
Рециркуляцию дымовых газов можно также обеспечить более дорогим и технически сложным способом – путем отбора части дымовых газов из газохода и подачи их на форсунки с дутьевым воздухом. Наличие инертных компонентов в дымовых газах, в частности N2, снижает концентрацию реагирующих веществ и уменьшает скорость цепных реакций. Дополнительным фактором, влияющим на снижение образующихся оксидов азота по термическому принципу, является содержание в дымовых газах СО2 и Н2О. Эти компоненты имеют высокую теплоемкость и эффективно отбирают теплоту из зоны горения, снижая ее температуру.
Следует отметить, что объединение приведенных схем организации горения в одном горелочном устройстве приводит к значительному снижению образованию NOx [2].
Одной из проблем, с которой столкнулись производители горелок при разработке устройств с пониженным содержанием NOx, а затем и проектировщики технологических трубчатых печей, – это значительное усложнение конструкции горелок, а также их массы и габаритов (рис. 2).
В ходе проведения тестовых испытаний горелок нового поколения было выявлено, что увеличенный горелочный камень дестабилизирует пламя, в результате чего могут произойти локальные перегревы змеевика работающей печи и аварии. В итоге работы над данной проблемой появилось большое число разнообразных геометрически сложной формы конструкций горелочного камня зарубежных производителей. В связи с этим ООО «Алитер-Акси» пришлось пересмотреть конструкцию печей в части крепления таких «крупных» горелок к корпусу печи с использованием локальных усилений, организации подвода топливных трубопроводов и обеспечения возможности обслуживания их эксплуатирующим персоналом.
Логично, что следующим шагом производителей горелок по модификации горелочных устройств с низким содержанием NOx стала попытка сократить габариты горелочного камня.
Однако уменьшение диаметра устья горелки привело к нестабильной работе устройств номинальной мощностью от 4 МВт из-за нехватки воздуха, подаваемого на горение инжекционным способом, так как стабилизатор пламени (рис. 3), устанавливаемый в центральной части, создавал повышенное сопротивление.
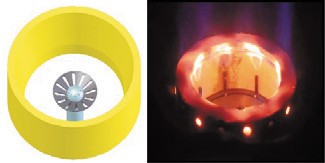
Рис. 3. Стабилизация пламени формой горелочного камня
В аналогичных горелках, работающих с принудительно подаваемым воздухом (дутьевых), пламя было нестабильно, не имело правильной формы, что также недопустимо для нормальной эксплуатации устройств.
Было принято решение изменить геометрию стабилизатора пламени с расположением его по внутреннему периметру и сохранением конструктивных особенностей горелочного камня, что в совокупности позволило сократить общие габариты горелочного устройства с нормальным количественным обеспечением воздуха, подаваемого на горение любом способом.
На наш взгляд, наиболее современным устройством на сегодняшний является газовая горелка фирмы Callidus (рис. 4), объединившая в себе все перечисленные конструкционные особенности, а также использующая принцип Вентури [3].

На этом же принципе основана подача газовоздушной смеси (premix) на горение у панельных горелочных устройств, однако внедрение его в устройство с круглым факелом, безусловно, технологический прорыв.
Основным достоинством горелок с трубками Вентури в корпусе можно считать увеличенную мощность за счет подачи большего объема воздуха (с сохранением высокой скорости) в зону горения при большем расходе топлива по сравнению с аналогичным по конструкции и номинальной мощности устройством. При этом сохраняются компактность устройства, стабильность пламени в широком диапазоне регулирования, низкие выбросы NOx и техническая возможность по оснащению уже смонтированных горелок внутренними устройствами в виде трубок Вентури.
Подводя итоги, хотелось бы отметить, что технологии, используемые в горелочных устройствах импортного производства, опережают отечественные на 20–30 лет. Надеемся, что данный факт послужит стимулом для активной работы отечественных производителей в этом направлении, в том числе и по созданию новых, еще не открытых технологий по снижению выбросов NOx. В свою очередь,ООО «Алитер-Акси» как компания, которая ищет свои ключевые конкурентные преимущества в инновациях и изменениях, готово оказывать всестороннюю поддержку.
Список литературы
- Зельдович Я.Б., Садовников П.Я., Франк-Каменецкий Д.А. Окисление азота при горении. М.-Л.: Издательство АН СССР, 1947.
- The John Zink. Combustion handbook. Edited by Chafes E. Baukal//Jr CRC Press LLC, 2001.
- Авиация: Энциклопедия. М.: Большая Российская Энциклопедия, 1994.