Авторы: Д.Л. Астановский, Л.З. Астановский, П.В. Кустов (ООО «ФАСТ ИНЖИНИРИНГ»).
Опубликовано в журнале Химическая техника №8/2016
Анализ современных тенденций показывает, что основным направлением модернизации действующих НПЗ является углубление переработки нефтяного сырья, в том числе тяжелых нефтей и нефтяных остатков с получением экологически чистых моторных топлив. Глубина переработки нефти в целом по России сегодня составляет 72–73% против 85–95% в развитых странах. Неконкурентоспособность на мировом рынке основных видов получаемых в России нефтепродуктов объясняется их недостаточно высоким качеством, что в значительной мере зависит от применения устаревших технологий, износа основных фондов, зависимости применяемых технологий, оборудования и катализаторов от зарубежных фирм.
Все более широкое применение в промышленности находит процесс гидрогенизационной обработки нефтепродуктов, а также тяжелых нефтей и нефтяных остатков (гидроочистка, гидрокрекинг), обеспечивающий повышение качества моторных топлив и увеличение выхода легких фракций. При этом имеет место тенденция увеличения давления при проведении гидрогенизационных процессов.
Промышленные технологии гидрогенизационной обработки нефтяного сырья характеризуются потреблением большого количества водорода. При глубине превращения тяжелых нефтяных остатков 80–85% потребление водорода достигает 3,0–3,5% масc. относительно сырья.
При этом удельный вес стоимости водорода в эксплуатационных затратах составляет в среднем 40–75% [1].
Стоимость водорода оказывает существенное влияние на экономические показатели процессов, связанных с его применением, поэтому снижение стоимости водорода приобретает первостепенное значение. Высокая стоимость водорода, получаемого на установках с применением традиционного оборудования, обусловлена большими капитальными вложениями и эксплуатационными затратами.
Производство водорода
Производство водорода по технологии ФАСТ ИНЖИ-НИРИНГ® [2] базируется на использовании созданных фирмой каталитических реакторов [3, 4], теплообменных [5, 6] и массообменных аппаратов [7], беспламенных горелок [8] и другого оборудования нового поколения, а также на применении энергосберегающих технологий получения синтез-газа, высокоэффективного экологически чистого способа сжигания топлива и др.
Преимущества новой технологии получения водорода паровой конверсией природного газа:
- высокая степень конверсии природного газа при относительно низкой температуре теплоносителя (до 1000°С);
- возможность создания эффективных установок на заданную производительность (в том числе малую);
- исключение использования кислорода;
- глубокая утилизация теплоты технологических и энергетических потоков;
- снижение затрат при эксплуатации;
- надежность;
- компактность;
- сокращение капитальных вложений;
- практически полное исключение вредных выбросов (СО и NОх) в окружающую среду;
- снижение стоимости водорода за счет сокращения капитальных вложений и эксплуатационных затрат.
По сравнению с традиционными технологиями новая технология примерно в 2–3 раза сокращает удельные капитальные вложения (в зависимости от мощности установки), а также снижает удельное потребление природного газа на получение 1 кг водорода примерно на 20–30%.
Принципиальная схема получения водорода паровой конверсией природного газа представлена на рис. 1.
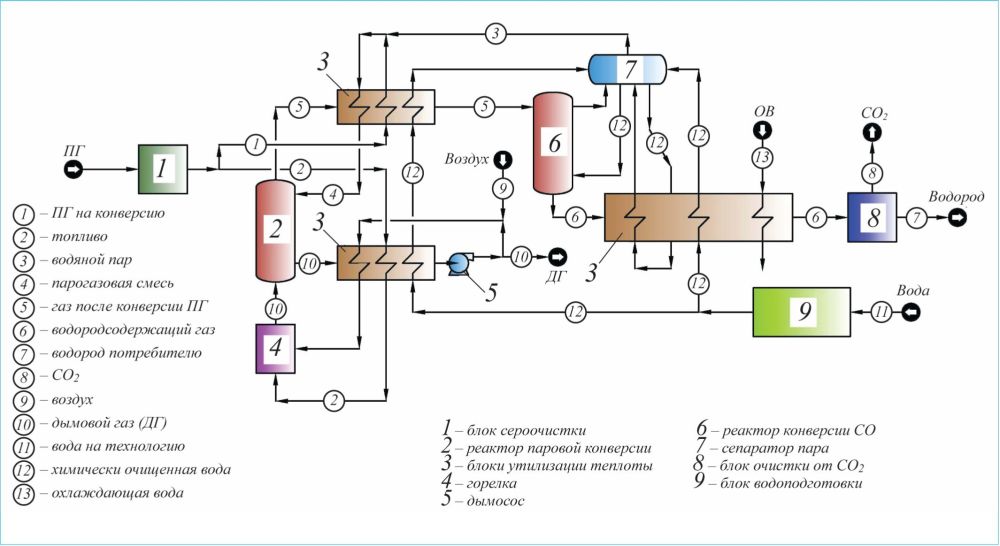
Пилотная установка получения синтез-газа паровой конверсией природного газа представлена на рис. 2.
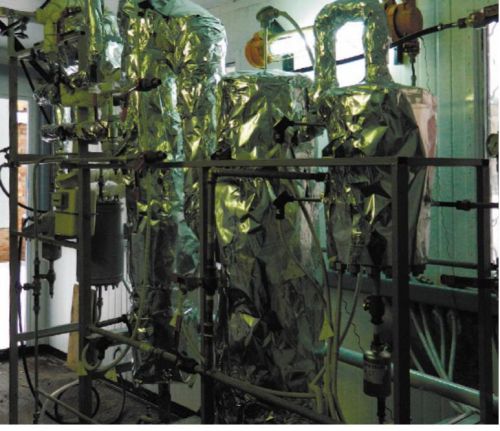
Гидрогенизационная обработка нефтяного сырья
Гидрогенизационную обработку нефтяного сырья, как правило, проводят при температуре 320…480°С и давлении 2,5…20,0 МПа. При этом объемная скорость подачи сырья составляет 0,5…2,0 ч–1 [9].
Процесс гидрогенизационной обработки протекает с выделением теплоты. Величина теплового эффекта таких процессов в зависимости от вида обрабатываемого сырья имеет существенное значение для выбора конструкции реактора.
Известно, что водород плохо растворяется в углеводородном сырье, а особенно плохо в сырье, которое содержит преимущественно ароматические соединения.
Диффузия водорода в тяжелые углеводороды происходит крайне медленно, в результате чего полное насыщение достигается лишь в течение многих часов. С ростом температуры и давления растворимость водорода увеличивается.
Наряду с повышением давления и температуры важным фактором, определяющим скорость растворения водорода в нефтяном сырье, является площадь поверхности контакта газовой фазы водорода и жидкой фазы нефтяного сырья. Чем больше эта площадь, тем выше скорость насыщения нефтяного сырья водородом.
Низкая объемная скорость подачи сырья в применяемых традиционных реакторах гидрогенизационной обработки обусловлена, прежде всего, медленным растворением водорода в нефтяном сырье, неравномерным распределением нефтяного сырья и водорода по зернистому слою катализатора и недостаточной площадью поверхности контакта газовой и жидкой фаз.
В традиционно применяемых в промышленности каталитических реакторах для гидрогенизационной обработки распределение сырья по зернистому слою катализатора при низких объемных скоростях в какой-то мере приближается к равномерному, а распределение водорода по зернистому слою катализатора при объемных скоростях 500…1000 нм3/м3 сырья остается неравномерным [9]. Чем выше давление в реакторе, тем меньше реальный объем водорода, тем равномернее он распределяется по зернистому слою. Неравномерное распределение нефтяного сырья и водорода в зернистом слое катализатора приводит к неравномерному распределению температур в слое катализатора, что приводит к образованию в нем застойных зон и локальных перегревов.
Высокие температуры в застойных зонах способствуют спеканию гранул, коксообразованию с отложением кокса на поверхности катализатора, и, как следствие, к потере активности и необходимости замены катализатора. При проведении процесса гидрокрекинга в каталитическом реакторе образуются углеводородные газы, которые разбавляют водород, подаваемый в реактор, снижая при этом его парциальное давление и уменьшая его растворимость в нефтяном сырье. Для поддержания заданной концентрации водорода в циркуляционном водородсодержащем газе перед реактором часть этого газа после реактора выводится из цикла. Вместе с выводимым из цикла газом теряется часть водорода.
В некоторых схемах для гидрогенизационной обработки нефтяного сырья используют водород концентрацией 99,9%. Необходимость использования водорода такой концентрации для гидрогенизационной обработки нефтяного сырья является спорной, так как при этом значительно увеличиваются капитальные вложения и эксплуатационные затраты, поскольку для получения водорода концентрацией 99,9% используется короткоцикловая адсорбция (КЦА).
Низкие объемные скорости сырья приводят к необходимости загрузки больших объемов катализатора, применения дорогостоящего громоздкого оборудования.
Так, для гидрогенизационной обработки углеводородного сырья используют каталитические реакторы внутренним диаметром до 4,5 м и высотой до 47 м, массой более 1 200 т. В такой реактор загружается 450 м3 катализатора. Температура в слое катализатора поддерживается подачей холодного водорода между катализаторными полками по высоте реактора.
Чем больше диаметр реактора, тем труднее организовать в нем равномерное распределение реакционной среды по зернистому слою катализатора, тем неравномернее будет в нем распределение температур, тем больше будут температурные перекосы, локальные перегревы, сокращающие срок эксплуатации катализатора.
Технология ФАСТ ИНЖИНИРИНГ® гидрогенизационной обработки нефтяного сырья
Технология ФАСТ ИНЖИНИРИНГ® гидрогенизационной обработки нефтяного сырья характеризуется следующим:
- насыщение водородом исходного нефтяного сырья, подлежащего гидрогенизационной обработке, осуществляется при принятых температуре и давлении в массообменном аппарате, обеспечивающем развитую площадь поверхности контакта газовой фазы водорода и жидкой фазы исходного нефтяного сырья;
- гидрогенизационная обработка нефтяного сырья (гидроочистка и гидрокрекинг) осуществляются при принятых температуре и давлении в каталитическом реакторе, обеспечивающем равномерное распределение сырья по всему объему катализатора; при этом поддержание заданной температуры процесса в зернистом слое катализатора реализуется путем отвода теплоты из реакционной зоны через теплопередающую стенку внешним теплоносителем;
- процессы насыщения водородом нефтяного сырья проводят в массообменном аппарате путем пропускания через него нефтяного сырья и циркулирующего водорода. Нерастворенный в углеводородном сырье водород циркулирует через массообменный аппарат, а насыщенное водородом углеводородное сырье направляют на гидроочистку или на гидрокрекинг;
- процессы гидроочистки и гидрокрекинга проводят при высоких объемных скоростях нефтяного сырья только за счет водорода, растворенного в этом сырье, без дополнительной подачи газообразного водорода в углеводородное сырье перед реакторами гидроочистки и гидрокрекинга и в эти реакторы;
- степень извлечения серы и азота из нефтяного сырья при гидроочистке, а также глубину переработки нефтяного сырья при гидрокрекинге обеспечивают путем рециркуляции этого сырья через стадии насыщения водородом и соответствующие реакторы;
- для гидрогенизационной обработки нефтяного сырья может быть использован водород концентрацией 93–97%.
Выбор параметров процесса гидрогенизационной обработки (давление и температура) определяется с учетом содержания серы, азота, ароматических соединений, высокомолекулярных и других компонентов обрабатываемого нефтяного сырья. Сырьем для гидрогенизационной обработки могут быть легкие нефтяные фракции, тяжелая нефть, нефтяные остатки и т.д., независимо от содержания в нем серы, азота и др.
Принципиальная технологическая схема технологии ФАСТ ИНЖИНИРИНГ® гидрогенизационной обработки нефтяного сырья представлена на рис. 3.
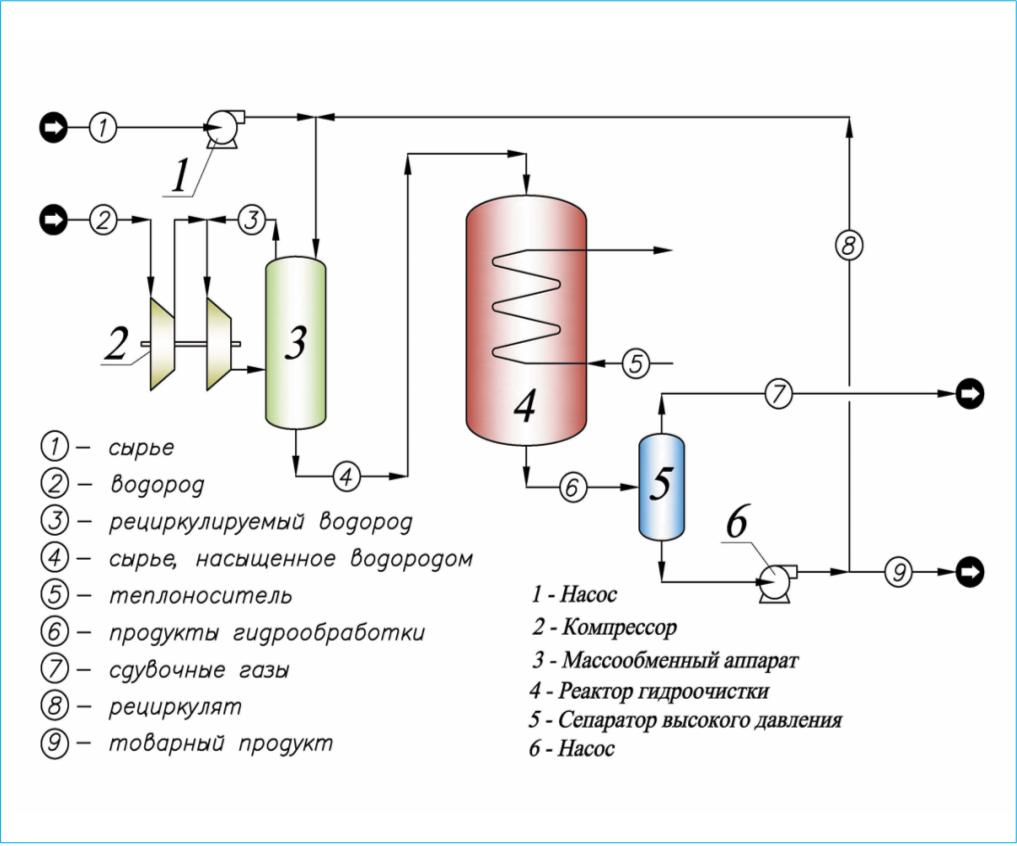
Процесс насыщения нефтяного сырья водородом можно проводить в массообменных аппаратах любого типа. Однако для достижения быстрого и наиболее полного насыщения нефтяного сырья водородом при принятых температуре и давлении предпочтительно использовать массообменный аппарат конструкции ФАСТ ИНЖИНИРИНГ®, хорошо зарекомендовавшим себя в промышленности [7].
Процесс гидрогенизационной обработки насыщенного водородом нефтяного сырья можно проводить в каталитических реакторах любого типа. Однако предпочтительно использовать каталитический реактор конструкции ФАСТ ИНЖИНИРИНГ®, обеспечивающий равномерное распределение реакционной среды по всему объему зернистого слоя катализатора, поддержание заданной оптимальной температуры в катализаторном слое путем отвода теплоты реакции теплоносителем через теплопередающие стенки и успешно опробованный в промышленности [3, 4].
Требуемая глубина переработки нефтяного сырья в легкие фракции высокого качества с минимальным содержанием серы и азота достигается путем рециркуляции этого сырья через стадии насыщения водородом и гидрогенизационной обработки.
Сокращение потребления водорода достигается за счет уменьшения его потерь при насыщении водородом нефтяного сырья в массообменном аппарате. При этом исключается разбавление водорода газами, образующимися в реакторе гидрогенизационной обработки нефтяного сырья, и потери водорода с газами, выводимыми из реактора.
Каталитический реактор нового поколения обеспечивает поддержание в зернистом слое катализатора оптимальной температуры проведения технологического процесса, исключает локальные перегревы катализатора и увеличивает срок его службы.
Увеличение объемной скорости подачи нефтяного сырья при гидрогенизационной обработке достигается исключением лимитирующей стадии растворения водорода в нефтяном сырье непосредственно в каталитическом реакторе. Благодаря этому время контакта катализатора и нефтяного сырья, насыщенного водородом, для проведения процессов гидрогенизационной обработки значительно сокращается, что позволяет увеличить объемную скорость. Увеличение объемной скорости подачи сырья приводит к уменьшению объема загружаемого катализатора, что позволяет уменьшить массогабаритные характеристики каталитических реакторов.
Снижение давления процесса гидрогенизационной обработки уменьшает количество водорода, растворенного в нефтяном сырье. Однако это компенсируется увеличением циркуляции нефтяного сырья через стадии насыщения сырья водородом и гидрогенизационной обработки. Снижение давления процесса гидрогенизационной обработки приводит к сокращению потребления энергии на компримирование водорода.
Таким образом, технология ФАСТ ИНЖИНИРИНГ® гидрогенизационной обработки нефтяного сырья позволяет:
- сократить потребление водорода за счет уменьшения его потерь;
- обеспечить равномерное распределение нефтяного сырья и водорода по всему объему зернистого слоя, поддержание оптимальной температуры в зоне катализа, исключить локальные зоны перегрева и увеличить срок службы катализатора;
- увеличить объемную скорость подачи нефтяного сырья при гидрогенизационной обработке и уменьшить массогабаритные характеристики каталитических реакторов и объем загружаемого катализатора;
- обеспечить возможность снижения давления процесса гидрогенизационной обработки нефтяного сырья и сократить потребление энергии для компримирования водорода;
- обеспечить возможность достижения требуемой степени очистки нефтяного сырья от серы и азота, а также требуемой глубины переработки нефтяного сырья в легкие фракции высокого качества.
Создание головной экспериментальной установки гидрогенизационной обработки нефтяного сырья по предлагаемой технологии
Применяемые для создания установки каталитические реакторы, теплообменные и массообменные аппараты нового поколения уже многие годы эксплуатируются в промышленности. Отдельные стадии технологического процесса успешно проверены на пилотных установках.
В составе установки предусматривается блок получения водорода по новой технологии.
Головная экспериментальная установка гидрогенизационной обработки нефтяного сырья может быть создана на производительность, например, 20 кг/ч по перерабатываемому сырью.
При создании установки гидрогенизационной обработки нефтяного сырья будут использованы патенты РФ на изобретения, авторские права на которые принадлежат ООО «ФАСТ ИНЖИНИРИНГ».
Ряд заводов РФ по лицензии ООО «ФАСТ ИНЖИНИ-РИНГ» освоили производство оборудования нового поколения.
Заключение
В настоящее время в области нефтепереработки складывается такая ситуация, при которой нефтяные остатки становятся все худшего качества, а традиционные технологии их переработки с точки зрения экономики и экологии почти не улучшаются. В условиях снижения ресурсов легких и средних нефтей и наличия больших ресурсов тяжелой нефти становится чрезвычайно актуальным поиск новых подходов к повышению эффективности технологий, обеспечивающих глубокую переработку тяжелых нефтяных остатков в легкие фракции.
Не стоит рассчитывать на закупку новых технологий за рубежом, так как известно, что фирма, обладающая высокоэффективной технологией завтрашнего дня, никогда не продаст ее, если можно при определенных условиях продать устаревшие технологии и оборудование.
Такой подход при закупке технологий и оборудования за рубежом обрекает на вечное отставание.
Повышение эффективности нефтеперерабатывающей промышленности России, обеспечение конкурентоспособности отечественных технологий, оборудования, катализаторов, а также продуктов нефтепереработки возможно при широком развертывании работ, направленных на создание новых и внедрение имеющихся принципиально новых отечественных высокоэффективных технологий, оборудования и катализаторов.
Для ликвидации отставания России от развитых стран в области нефтепереработки, обеспечения ускоренного развития отрасли, государству, а также крупным ВИНК следует поддерживать организации, которые имеют высокоэффективные отечественные разработки и содействовать их внедрению.
Внедрение новых разработок во многом зависит от поддержки при создании пилотных или головных опытно промышленных установок.
Как и любые другие реальные инновации, так и созданные нами высокоэффективные технологии и оборудование, при внедрении сталкиваются с консерватизмом потребителей и скепсисом конкурентов. Тем не менее, наши разработки внедряются в промышленность, в том числе когда нет альтернативы для решения конкретной технической проблемы или при необходимости замены неудовлетворительно работающего импортного оборудования. Внедрению инновационных разработок также способствует наличие технически грамотных и дальновидных заказчиков, обладающих прозорливостью и вполне обоснованной смелостью.
Создание отечественных инновационных технологий и оборудования, конкурентоспособных на мировом рынке – это одновременно создание многих тысяч рабочих мест в разных отраслях промышленности России.
Список литературы
- Каминский Э.Ф., Хавкин В.А. Глубокая переработка нефти: технологический и экологический аспекты. М.: Издательство «Техника», 2001.
- Астановский Д.Л., Астановский Л.З. Энергосберегающее компактное производство водорода//Химическое и нефтегазовое машиностроение. 2000. №5.
- Astanovsky D.L. and Astanovsky L.Z. Revolutionary reactor// Nitrogen. 232. Р. 33–39 (March–April 1998).
- Астановский Д.Л., Астановский Л.З. Реактор новой конструкции для проведения каталитических процессов//Катализ в промышленности. 2004. №3.
- Астановский Д.Л., Астановский Л.З. Новая конструкция теплообменного аппарата//Химическое и нефтегазовое машиностроение. 2003. №4.
- Астановский Д.Л., Астановский Л.З. Теплообменные аппараты радиально-спирального типа конструкции ФАСТ ИНЖИНИРИНГ®//ХИМАГРЕГАТЫ. 2015. №4 (32).
- Астановский Д.Л., Астановский Л.З. Высокоэффективный аппарат для очистки газа//Химическое и нефтегазовое машиностроение. 2003. №8.
- Астановский Д.Л., Астановский Л.З., Кустов П.В. Использование беспламенных горелок и теплообменных аппаратов новой конструкции для эффективного сжигания топлива//Энергобезопасность и энергосбережение. 2013. №1.
- Альбом технологических схем процессов переработки нефти и газа/Под ред. Б.И. Бондаренко. М.: Изд-во РГУ нефти и газа им. И.М. Губкина, 2003.