Авторы:
А.М. Добротворский, М.А. Добротворский (ЗАО «НПО «Ленкор», СПбГУ),
Е.П. Шевякова (ЗАО «НПО «Ленкор»), С.Ф. Самков, Ю.А. Бахмат (ОАО «Газпромнефть-ОНПЗ).Опубликовано в журнале Химическая техника №1/2016
Водород является активным коррозионным агентом, воздействующим на конструкционные стали технологического оборудования нефтеперерабатывающей промышленности [1]. В результате ошибочного выбора материального оформления гидрогенизационных технологических процессов, низкого качества используемых материалов, а также нарушения технологических режимов эксплуатации воздействие водорода может привести к разрушению элементов аппаратов и технологических трубопроводов, в ряде случаев с катастрофическими последствиями. В нефтепереработке до 25% всех отказов оборудования так или иначе связано с воздействием водорода [2].
Коррозионное воздействие водорода может протекать по различным механизмам в зависимости от условий эксплуатации оборудования и типа конструкционных сталей. В частности, при повышенных температурах и давлениях углеродистые и низколегированные стали подвержены высокотемпературной коррозии [3–5]. При электролитическом насыщении водородом эти стали подвержены блистерингу – расслоению под воздействием внутреннего давления молизованного растворенного водорода [6]. Высокопрочные легированные стали в определенных условиях подвержены водородному охрупчиванию [7–9].
Выявление технических причин отказов оборудования, в том числе работающего в водородсодержащих средах, является актуальной задачей, решение которой стимулирует разработку новых конструкционных материалов, методов защиты от коррозии, компенсирующих мероприятий и в конечном счете способствует повышению надежности и безопасности эксплуатации нефтеперерабатывающих производств [10–12].
Предметом настоящей работы является выявление причин отказа (растрескивание) отвода газопродуктовой линии установки гидроочистки дизельного топлива ГОДТ Омского НПЗ.
Отвод, как и весь трубопровод, изготовлен из сталиА403GWP347S (отечественный аналог – сталь 08Х18Н12Б).
Рабочая среда – газопродуктовая смесь (водород + дизельное топливо + промывочная вода). После 1,8 года эксплуатации в одном из отводов трубопровода было обнаружено несколько пропусков. Коррозионного утонения не наблюдалось. Было установлено, что пропуски произошли через сетку сквозных трещин, расположенных по верхней образующей отвода вблизи сварного шва с горизонтальным участком трубопровода (вне зоны термического влияния шва). Продольные ветвящиеся макротрещины с большим раскрытием и длиной до 100 мм появились и стали расти как с внутренней поверхности отвода, так и с наружной. Трещина с внутренней поверхности значительно превосходила по размерам трещину с наружной поверхности.
Анализ эксплуатационной документации показал, что в процессе работы технологической установки в трубопроводе, соединяющем два последовательно включенных кожухотрубчатых теплообменника, происходило временное повышение давления. Причиной повышения давления могло быть вскипание промывочной воды, подаваемой в прямолинейный участок трубы, примыкающей к отводу со стороны направления потока газопродуктовой водородсодержащей смеси. Однако превышение давления в данных эпизодах не выходило за пределы расчетного давления трубопровода и не могло быть непосредственной причиной его растрескивания. В связи с этим было принято решение о проведении комплексного металловедческого исследования дефектного отвода.
Программа исследования металла отвода включала химический анализ состава стали, определение содержания ферритной фазы, рентгенофазный анализ внутренних и наружных отложений, металлографические исследования, измерения твердости, растровую электронную микроскопию с рентгеновским микроанализом, определение содержания водорода в стали.
Химический анализ стали отводов показал его соответствие сертификату и требованиям стандарта [13], однако по содержанию всех легирующих элементов (хром, никель, ниобий) сталь отвода находится вблизи нижнего предела, установленного стандартом.
Химический состав образца П-288, %
C | Si | Mn | Ni | S | P | Cr | Ti | Cu | Nb | N | Mo |
0,042 | 0,410 | 1,310 | 9,600 | 0,001 | 0,025 | 17,400 | – | – | 0,550 | – | – |
Механические свойства стали, полученные при испытании образцов металла, изготовленных из неповрежденной части дефектного отвода (табл. 1), также подтверждают его соответствие сертификату и требованиям стандарта [13].
Таблица 1
Результаты испытаний образцов металла, изготовленных из неповрежденной части дефектного отвода
Образец |
Материал |
Фактические значения по результатам испытаний (нормируемые значения по НТД – ASTMA 403) | ||
sт, МПа | sп, МПа | y, % | ||
№1 | A403 | 371 | 618 | 47,6 |
(не менее | (не менее | (не менее | ||
205) | 515) | 35) | ||
№2 | WP347 | 397 | 643 | 47,8 |
(не менее | (не менее | (не менее | ||
205) | 515) | 35) |
Выполненные металлографические исследования свидетельствуют об удовлетворительном характере микроструктуры образца, вырезанного на некотором расстоянии от места разрушения трубы (образец №1), при высокой степени загрязненности металла неметаллическими включениями. Результаты замеров твердости в исследуемом образце находятся в пределах допустимых значений для стали данной марки. Данные рентгенофазового анализа (рис. 1), выявляют наличие в металле единственной фазы – аустенита. Вместе с тем значительное уширение дифракционных пиков свидетельствуют о высокой дефектности структуры: двойники, дефекты упаковки, дислокации, остаточные микронапряжения, неметаллические включения.
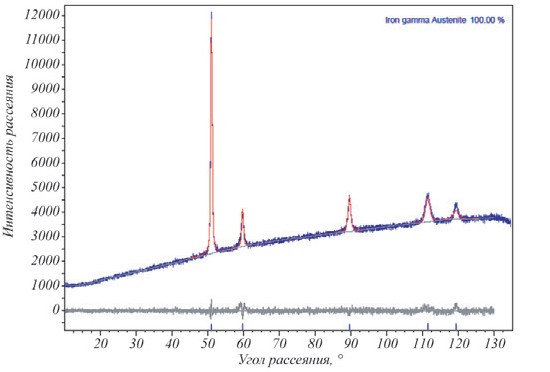
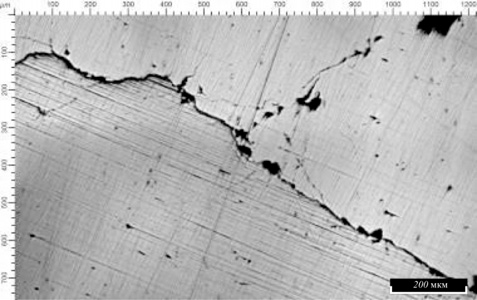
Исследования микроструктуры образца, вырезанного в месте разрушения металла (образец №2), выявили большое количество пор и трещин (рис. 2). Размер пор достигает 200 мкм. Микроструктура образца с трещинами – аустенит и неметаллические включения. Трещины расположены по границам аустенитных зерен (рис. 3), внутри которых имеются многочисленные полосы скольжения, что указывает на наличие больших механических напряжений, возникших вследствие холодной деформации, в данном фрагменте отвода. Учитывая состав технологической среды (водородсодержащий газ + дизельное топливо), наличие крупных пор и полос скольжения, можно предположить, что разрушение металла произошло в результате водородного растрескивания под напряжением.
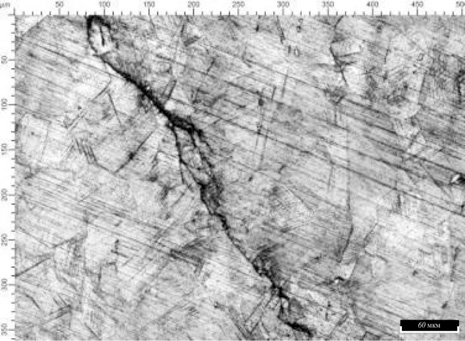
С целью более детального исследования микроструктуры образца №2 и определения химического состава включений проводилось специальное исследование методом растровой электронной микроскопии с рентгеновским микроанализом, позволившее выявить распределение химических элементов в области растрескивания и в основном металле (рис. 4).
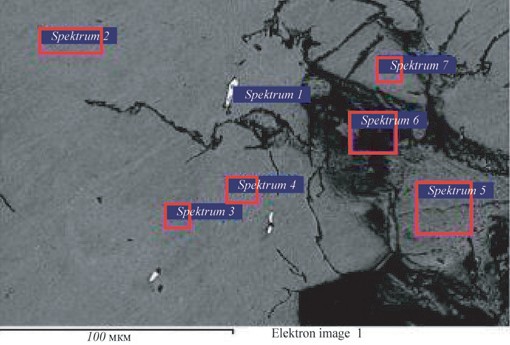
Результаты замеров локального химического состава, %
Обозначение
(см. рис. 4) |
точки
C |
O | Al | Si | Cr | Mn | Fe | Ni | Nb |
Spectrum 1 | 8,72 | – | – | – | 0,54 | – | 0,73 | – | – |
Spectrum 2 | – | – | – | 0,89 | 19,08 | 1,32 | 69,73 | 8,98 | – |
Spectrum 3 | 8,99 | – | – | 1,05 | 17,18 | 1,58 | 62,47 | 8,72 | – |
Spectrum 4 | 8,27 | – | – | 0,85 | 17,11 | 1,32 | 63,98 | 8,48 | – |
Spectrum 5 | 16,08 | – | – | 0,77 | 16,12 | 1,31 | 57,15 | 8,57 | – |
Spectrum 6 | 45,88 | 20,59 | 7,98 | 0,44 | 5,34 | 0,48 | 17,44 | 1,86 | – |
Spectrum 7 | 10,98 | – | – | 0,87 | 16,54 | 1,23 | 61,76 | 8,61 | – |
Наибольшее значение |
45,88 |
20,59 |
7,98 |
1,05 |
19,08 |
1,58 |
69,73 |
8,98 |
90,02 |
Наименьшее значение |
8,27 |
20,59 |
7,98 |
0,44 |
0,54 |
0,48 |
0,73 |
1,86 |
90,02 |
Полученные результаты свидетельствуют о том, что содержание основных легирующих элементов в матрице металла близко к определенному методом рентгенофлуоресцентного анализа: хром 18-19%, никель – 8,5–9%. Содержание углерода, определенное методом рентгеновского микроанализа, завышено вследствие технологии изготовления образцов с использованием углеродсодержащих материалов. Распределение ниобия, как и следовало ожидать, является крайне неоднородным. Он сосредоточен во вкраплениях карбидов. Сильно отличается от основного металла участок с нечетким очертанием, окруженный сеткой микротрещин. Он, помимо углерода, обогащен алюминием и кислородом (точка Spectrum 6 на рис. 4). Это позволяет идентифицировать данный участок как включение оксида и карбоната алюминия (шлаковое включение).
Еще более четко природа аналогичного включения выявляется на карте распределения химических элементов (рис. 5). Можно предположить, что в шлифе сохранилась только небольшая часть шлакового включения (яркие желто-зеленые участки). Основная часть включения выпала при шлифовке образца.
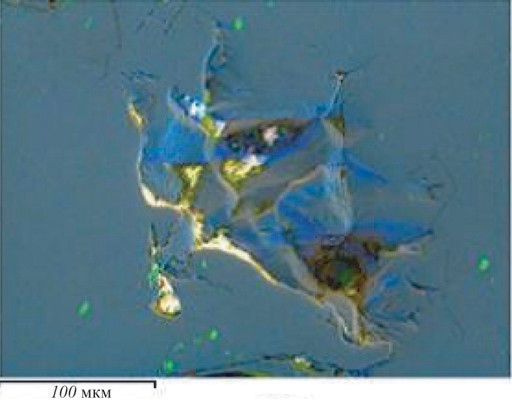
Следует отметить, что в отличие от шлаковых включений частицы карбида ниобия (рис. 6) имеют малые размеры (5…10 мкм), хорошо окристаллизованы и когерентно встроены в матрицу аустенита. Они не являются источником образования трещин.
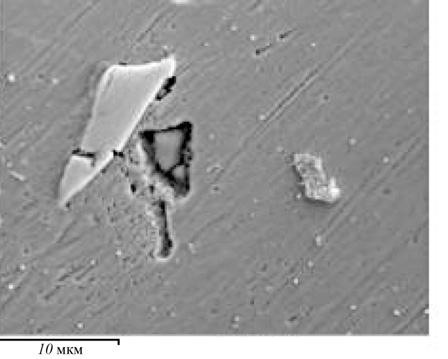
Данные рентгенофазового анализа, полученные для образца дефектной зоны, выявляют в металле кроме аустенита наличие альфа-железа до 10%, а также другие фазы в малом количестве.
Результаты металлографических исследований двух образцов металла, вырезанных из отвода, позволяют сделать следующие выводы: в целом микроструктура всех исследованных образцов соответствует российскому аналогу стали 08Х18Н12Б; микроструктура образца вдали от растрескавшегося участка отвода в целом удовлетворительная, однако следует отметить повышенную загрязненность неметаллическими включениями. Микроструктура образца, вырезанного в месте разрушения металла, изобилует неметаллическими включениями, микротрещинами и имеет более крупное зерно. Заметное различие структуры и фазового состояния металла двух образов свидетельствует о его неоднородности по телу отвода, что может являться следствием технологии его изготовления (холодная деформация) и термообработки. Вероятная причина наличия большого числа микротрещин во втором образце – растрескивание под напряжением металла, охрупченного вследствие воздействия водорода.
Нержавеющие хромоникелевые стали аустенитного класса обладают высокой стойкостью к водородной коррозии в широком интервале температур и давлений [3–5]. Это обусловлено высокой стабильностью карбидов хрома (и ниобия) по отношению к водороду, в отличие от цементита углеродистых и кремнемарганцевых сталей, которые разлагаются водородом с образованием метана. Вместе с тем, водородная коррозия – не единственный механизм, приводящий к растрескиванию сталей. Другим механизмом, который в определенных условиях поражает аустенитные стали, является водородная хрупкость [7–9]. Растворимость водорода, быстро возрастающая при повышении температуры, в аустенитных сталях выше, чем ферритных. Растворенный водород диффундирует в объеме металла и частично захватывается ловушками, в качестве которых выступают дислокации, большеугловые межзеренные границы, микротрещины. При повышенной температуре, как, например, в случае исследованного дефектного трубопровода, из-за высокой диффузионной подвижности влияние водорода на рост трещин невелико. Однако при понижении температуры (близкой к температуре окружающей среды) доля водорода, захваченного ловушками, в частности микротрещинами, возрастает. Скопление водорода в трещинах, при наличии напряжений, способствует ускорению их роста. В литературе рассматриваются два механизма такого влияния водорода: декогезионный механизм и механизм роста локальной пластичности металла [14–16].
1 – максимальный уровень содержания металлургического водорода в сталях, выплавленных при различных способах производства [18]; 2–4 – температурные зависимости равновесного содержания растворенного водорода в сталях: 304 и 304L (2), 316 и 316L (3), 321 и 347 (4) [19];
5 – равновесное содержание водорода в стали при температуре 470 K и давлении 69 МПа[20];
6 – содержание водорода в образце металла отвода вне зоны растрескивания; 7 – содержание водорода в образце металла отвода в зону растрескивания
По сталям А304 и А316 имеются прямые сопоставительные данные, которые показывают, что, в отличие от водородостойкой стали А316 (российский аналог 08Х17Н13М2) с более высоким содержанием никеля, сталь А304 склонна к водородному охрупчиванию [21].
Учитывая, что сталь А347 разработана на основе стали А304, этот вывод, с большой долей уверенности, справедлив для нее тоже. Водородной хрупкости сталей А304 и А347 посвящено также исследование [22].
В нашем случае равновесное содержание водорода в металле отвода при рабочих температуре и давлении достаточно велико. При быстром охлаждении значительная его часть остается в металле, что создает условия водородного охрупчивания. Если внутри трубы сохраняется избыточное давление, то в совокупности с остаточными микронапряжениями, водородная хрупкость способствует подрастанию трещин, особенно при снижении температуры. По показаниям контроля такое снижение имело место в отдельные кратковременные периоды в процессе эксплуатации. Следует отметить, что наиболее уязвимы для водородного охрупчивания отводы, так как на линейных участках, за счет кольцевого течения углеводородов, стенки труб в какой-то мере защищены от прямого контакта с водородсодержащим газом. Дополнительным фактором, повышающим их склонность к охрупчиванию, является загрязненность металла включениями и остаточные напряжения.
Таким образом, основными факторами разрушения отвода явились: неоптимальный химический состав стали отвода; наличие дефектов металлургического происхождения; неоднородность фазового состава и микроструктуры стали; остаточные напряжений холодного деформирования, не снятые при термообработке.
Дополнительно к этому, разрушение инициировалось динамическим фактором – циклическими знакопеременными изменениями напряжений в отводе, связанными с перепадами внутреннего давления.
Особенности состава и структуры стали обусловили ее склонность к водородной хрупкости, которая способствует росту усталостных трещин при охлаждении трубопровода до температур, близких к температуре окружающей среды, и одновременном сохранении высоких внутренних напряжений.
Список литературы
- API Recommended Practice 571, Damage Mechanisms Affecting Fixed Equipment in the Refining Industry, 2009.
- Z. Shirband , M. R. Shishesaz, A. Ashrafi. Hydrogen degradation of steels and its related parameters, a review, Phase Transitions//A Multinational Journal. 84:11–12.
- Арчаков Ю.И. Водородная коррозия стали. М.: Металлургия, 1985.
- Арчаков Ю.И., Седов В.М., Добротворский А.М. и др. Технические указания-регламент по эксплуатации и обследованию оборудования установок каталитического риформинга и гидроочистки, работающих в водородсодержащих средах при повышенных температуре и давлении. СПб.: 1998.
- API 941. Steels for Hydrogen Service at Elevated Temperatures and Pressures in Petroleum Refineries and Petrochemical Plants. STANDARD STANDARD published 08/01/2008 by American Petroleum Institute.
- E. Shekari, M. R. Shishesaz, Gh. Rashed, M. Farzam, E. Khayer. Failure Investigation of Hydrogen Blistering on Low-strength Carbon Steel//Iranian Journal of Oi l & Gas Science and Technology. Vol. 2 (2013). №2.
- Колачев Б.А. Водородная хрупкость металлов. М.: Металлургия, 1985.
- R. Gibala, R.F. Hehemann. Hydrogen embrittlement and stress corrosion cracking. A Troiano Festschrift, ASM International. 2002.
- С′wiek J. Prevention methods against hydrogen degradation of steel//Journal of Achievements in Materials and Manufacturing Engineering. 2010. Vol. 43. №1.
- Добротворский А.М., Шевякова Е.П., Масликова Е.И., Михайловский В.Ю. Современные методы выявления причин отказов нефтеперерабатывающего и нефтехимического оборудования//Химическая техника. 2013. №12.
- ASM. Handbook. Vol. 11. Failure Analysis and Prevention, ASM International, 2002; Vol. 19. Fatigue and Fracture, ASM International, 2002.
- Wulpi D.J. Understanding How Components Fail, 3rd EditionPublisher, ASM International, 2013.
- Designation: A 240/A 240M – 04a. Standard Specification for Chromium and Chromium-Nickel Stainless Steel Plate, Sheet, and Strip for Pressure Vessels and for General Applications
- Добротворский А.М., Арчаков Ю.И. Теоретическое исследование влияния водорода на механические свойства железа// Физ.-хим. механика материалов. Т. 25, вып. 3. 1989.
- Novak P.M. A dislocation-based constitutive model for hydrogen– deformation interactions and a study of hydrogen-induced intergranular fracture, Dissertation submitted in partial fulfillment of the requirements for the degree of Doctor of Philosophy in Theoretical and Applied Mechanics in the Graduate College of the University of Illinois at Urbana-Champaign, 2009, Urbana, Illinois.
- Barmoush A. Hydrogen embrittlement, 2011.
- Hideo Cho, Mikio Takemoto. Hydrogen related brittle cracking of metastable type-304 stainless seel//J. Acoustic Emission, 25 (2007).
- Гуляев А.П. Металловедение. М.: Металлургия, 1986.
- C. San Marchi, B.P. Somerday Technical Reference for Hydrogen Compatibility of Materials//SANDIA REPORT. SAND 20127321. Unlimited Release Printed September 2012.
- G.R. Caskey, Jr., R. D. Sisson, Jr. Hydrogen Solubility in Austenitic Stainless Steels//Scripta Metallurgica Vol. 15.
- Hideo Cho, Mikio Takemoto. Hydrogen related brittle cracking of metastable type-304 stainless steel//J. Acoustic Emission. 25 (2007).
- Chuan Pan, Zhengbang Li, Zhiling Tian And Dongtu Liang. Hydrogen-induced Cracking of Weld Metal of Austenitic Stainless Steels//J. Mater. Sci. Technol. 2002. Vol. 14, №4.