Авторы: А.М .Добротворский (ЗАО «НПО «Ленкор», СПбГУ), В.Л. Соколов (ООО «ПО «Киришинефтеоргсинтез»), М.И. Антонов (СПбПУ), Е.П. Шевякова, М.А. Караваева, М.А. Симанов, А.С. Борзенко (СПбПУ).
Опубликовано в журнале Химическая техника №1/2016
Трубы из стали 15Х5М (и стали 15Х5МУ, имеющей тот же химический состав) широко используют в нефтеперерабатывающем производстве в змеевиках печей, работающих при температурах 200…400°C [1, 2]. Проектный срок службы печных змеевиков из стали 15Х5М – 100 000 ч. Но, как показал опыт эксплуатации, этот срок не является для них предельным, и в настоящее время на многих установках достигнута их надежная работа до 200 тыс. ч.
Поскольку процесс длительного воздействия жестких рабочих условий и агрессивных сред приводит к структурным изменениям материала, которые, в свою очередь, сопровождаются снижением его жаропрочности и длительной пластичности, постольку вопрос оценки работоспособности металла печных змеевиков по фактическому состоянию имеет важное практическое значение [3].
В ранее опубликованных работах было показано, что эксплуатация стали 15Х5М в режимах тепловой нагрузки, не обеспечивающих термодинамическую стабильность ее исходного состояния, приводит к деградации структуры и механических свойств. Отмечалось также, что процессы коагуляции карбидов, локального разупрочнения и охрупчивания ускоряют процесс уменьшения содержания углерода и хрома в объеме зерна стали.
Ускоренному снижению предела текучести способствует формирование неравновесной структуры при изготовлении труб [4–7].
В настоящей работе обобщены данные исследования большого числа вырезок образцов стали 15Х5М из печных змеевиков технологических установок АТ-1, АТ-6, Л-24/6, Л-35-11-300, Л-35-11/600, Г-43-107, Парекс-1 нескольких нефтеперерабатывающих заводов. Исследования металла включали изучение химического состава и микроструктуры, определение механических свойств при нормальной и рабочей температурах, испытание на длительную прочность.
Таблица 1
Условия эксплуатации печных змеевиков
Установка | Образец | Условия эксплуатации | |||
Время эксплуатации, ч | Среда | Температура, °С | Давление, МПа | ||
АТ-1 | 1 | 264 000 | Бензин НК-180 | 235 |
1,40 |
АТ-6 |
2 | 304 000 | Нефть | 370 | 1,00 |
3 | 304 000 | Нефть | 260 | 1,00 | |
4 | 340 000 | Нефть | 370 | 1,00 | |
5 | 360 000 | Флегма | 225 | 1,20 | |
6 | 360 000 | Флегма | 260 | 2,00 | |
7 | 360 000 | Флегма | 225 | 1,20 | |
8 | 360 000 | Нефть | 375 | 1,56 | |
Л-24/6 | 9 | 400 000 |
Стабильное дизельное топливо |
350 | 0,20 |
Л-35-11-300 | 10 | 368 000 | Газопродуктовая смесь | 360 | 3,48 |
11 | 368 000 | Газопродуктовая смесь | 200 | 2,77 | |
Г-43-107 | 12 | 248 000 | Гидроочищенный вакуумный гайзоль | 340 | 1,60 |
Парекс-1 | 13 | 80 000 | Газосырьевая смесь | 415 | 1,40 |
Л-35-11/600 | 14–17 | 260 000 | Бензин + ВСГ | 302 | 5,30 |
Сопоставление полученных данных осложнено из-за различий в сроках и условиях эксплуатации печных змеевиков (табл. 1), а также из-за отсутствия в большинстве случаев достоверных данных об исходных характеристиках металла. Выявленное разнообразие структурномеханического состояния стали 15Х5М обусловлено рядом факторов:
- колебаниями в пределах марочного состава (табл. 2);
- различием способов изготовления и режимов термической обработки;
- различием расположения труб в печи относительно горелочных устройств;
- различием условий и частоты профилактического паровыжига кокса.
Тем не менее, анализ данных, накопленных при исследовании вырезок, позволяет сделать ряд общих выводов.
Таблица 2
Химический состав металла исследуемых печных змеевиков
Установка | Образец | Химический состав, % | |||||
Fe | Cr | Ni | Mo | Mn | Si | ||
АТ-1 | 1 | 92,63 | 5,40 | 0,20 | 0,56 | 0,43 | 0,40 |
АТ-6 |
2 | 92,35 | 5,57 | 0,18 | 0,59 | 0,39 | 0,42 |
3 | 92,77 | 5,45 | 0,13 | 0,52 | 0,41 | 0,27 | |
4 | 92,43 | 5,63 | 0,13 | 0,54 | 0,46 | 0,45 | |
5 | 92,42 | 5,33 | 0,51 | 0,34 | 0,56 | 0,20 | |
6 | 93,08 | 5,02 | 0,52 | 0,49 | 0,39 | 0,14 | |
8 | 92,42 | 5,45 | 0,51 | 0,51 | 0,59 | 0,11 | |
Л-24/6 | 9 | 92,42 | 5,72 | 0,49 | 0,39 | 0,32 | 0,19 |
Л-35-11-300 |
10 | 93,30 | 4,70 | 0,13 | 0,46 | 0,45 | 0,44 |
11 | 92,50 | 5,80 | 0,35 | 0,50 | 0,31 | 0,33 | |
Г-43-107 | 12 | 92,78 | 5,19 | 0,09 | 0,49 | 0,53 | 0,51 |
Парекс-1 | 13 | 92,92 | 4,90 | 0,17 | 0,45 | 0,35 | 0,49 |
Л-35-11/600 | 14, 15 | 92,78 | 4,91 | 0,13 | 0,48 | 0,34 | 0,55 |
Л-35-11/600 | 16, 17 | 91,92 | 5,43 | 0,11 | 0,45 | 0,39 | 0,34 |
ГОСТ 20072 для стали 15Х5М | – | Основа | 4,50…6,00 | £0,60 | 0,45…0,60 | £0,50 | £0,50 |
По результатам химического анализа (см. табл. 2) исследованных образцов их состав по основным легирующим элементам соответствует стали 15Х5М по ГОСТ 20072 [8].
Эволюция структурного состояния стали 15Х5М всех вырезок была исследована в сопоставлении с эталонной исходной микроструктурой стали 15Х5М (отпуск при температуре 740…770°С), состоящей из феррита со средним размером зерна, соответствующим 4 баллу по ГОСТ 5639 [9], и равномерно распределенных карбидов (рис. 1, а).
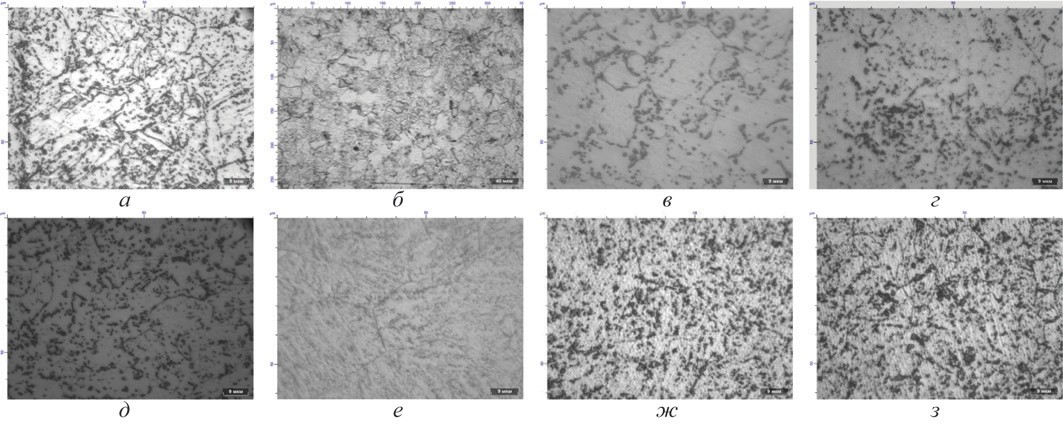
а – исходная структура; б – АТ-1; в – АТ-6; г – Л-24/6; д – Л-35-11-300; е – Г-43-107; ж – Парекс-1; з – Л-35-11/600
В процессе длительной эксплуатации в агрессивной среде микроструктура металла печных змеевиков деградирует в разной степени в зависимости от рабочей температуры и длительности эксплуатации.
Микроструктура металла змеевика установки АТ-1 – феррит и карбиды. Карбиды распределены неравномерно и образуют скопления, в том числе и по границам зерен. Следует отметить высокую загрязненность неметаллическими включениями. Кроме того, по всему сечению наблюдается пониженная плотность карбидов, что связано с равномерным частичным обезуглероживанием (рис. 1, б).
Микроструктура металла змеевика установки АТ-6 – феррит и коагулированные карбиды, расположенные в теле зерна и по границам ферритных зерен. В металле прошло сквозное обезуглероживание (рис. 1, в).
Микроструктура металла змеевика установки Л-24/6 – феррит и коагулированные карбиды. Плотность карбидов низкая по сравнению со структурой, характерной для стали марки 15Х5М, имеются отдельные крупные карбиды по границам зерен. По сечению исследуемого образца наблюдается равномерное частичное обезуглероживание, вызванное эксплуатацией металла в окислительной среде дымовых газов при высокой температуре (рис. 1, г).
Микроструктура металла змеевика установки Л-3511-300 – феррит и коагулированные карбиды (рис. 1, д).
Со стороны внутреннего края труб имеются технологические отложения и выкрашивания по границам зерен.
Карбиды, по сравнению с центральной частью образца, сильно укрупнены.
Микроструктура металла змеевика установки Г-43107 – основной металл – игольчатый сорбит и карбиды.
Местами карбиды образуют цепочки по границам ферритных зерен (рис. 1, е).
Микроструктура металла змеевика установки Парекс1 в центральной части сечения трубы – феррит + карбиды (рис. 1, ж), со стороны внутреннего края сечения трубы на глубину 547 мкм структура – бейнит, феррит и карбиды. По границам ферритных зерен обнаружены горячие микротрещины.
Микроструктура образца змеевика установки Л-3511/600 – феррит и карбиды (рис. 1, з). Наблюдается коагуляция карбидов и частичное распределение их по границам ферритных зерен.
Характеристики прочности и пластичности металла при температуре испытания 20°C всех печных змеевиков, кроме змеевика установки Л-24/6, несмотря на длительный срок эксплуатации, находятся в пределах минимальных значений, установленных ГОСТ 550 [10] для стали марки 15Х5М (табл. 3). У металла печных змеевиков установки Л-24/6 условный предел текучести несколько ниже минимально допустимых значений для стали 15Х5М при температуре испытаний 20°C, что указывает на большую степень деградации структуры металла и хорошо согласуется с результатами металлографических исследований. Возможной причиной этого является то, что из всех исследованных змеевиков они находились в эксплуатации наибольшее время. Аномально высокая прочность образца №13 (установка каталитического крекинга) при существенно пониженных значениях характеристик пластичности дает основание предположить, что этот образец был поставлен для исследования в закаленном состоянии, для которого механические свойства обладают указанными особенностями [2]. Аналогичные выводы можно сделать и для характеристик прочности, полученных нами в испытаниях при повышенных температурах (235…470°C). Для образцов большинства змеевиков полученные характеристики превышают минимальные значения, приводимые в справочной литературе для стали 15Х5М [11].
Таблица 3
Механические свойства металла труб змеевиков, стали 15Х5М при температуре 20°C и требования ГОСТ на материал
Установка | Образец | Свойства | ||||
s0,2, МПа | sв, МПа | d, % | y, % | KCU, Дж/см2 | ||
АТ-1 | 1 | 225 | 500 | 36 | 73 | 234 |
АТ-6 | 2 | 246 | 502 | 36 | 77 | 236 |
АТ-6 | 3 | 216 | 473 | 34 | 73 | 159 |
АТ-6 | 4 | 293 | 503 | 25 | 78 | 261 |
АТ-6 | 5 | 236 | 524 | 32 | 68 | 122 |
АТ-6 | 6 | 293 | 503 | 33 | 74 | 209 |
АТ-6 | 8 | 244 | 499 | 32 | 75 | 223 |
Л-24/6 | 9 | 209 | 456 | 33 | 76 | 185 |
Л-35-11-300 | 10 | 286 | 524 | 36 | 71 | 162 |
Л-35-11-300 | 11 | 243 | 454 | 36 | 70 | 125 |
Г-43-107 | 12 | 1011 | 1223 | 17 | 65 | 80 |
Парекс-1 | 13 | 579 | 693 | 22 | 74 | – |
ГОСТ 550 | – | 216 | 392 | 22 | 50 | 118 |
Одним из важнейших механических свойств конструкционных сталей, работающих при повышенных температурах, является длительная прочность. Для низколегированных сталей типа 15Х5М при расчетах на прочность змеевиков нагревательных печей при температуре эксплуатации более 425°C исходят из этой характеристики [12]. Длительная прочность определяет способность материала сопротивляться разрушению в условиях длительного статического нагружения. При испытаниях на длительную прочность образец проходит все стадии ползучести вплоть до разрушения.
Для большинства исследованных образцов были проведены испытания на длительную прочность на базе 20 000 ч при температуре 550°C. Для нескольких образцов испытания проводили при других температурах (табл. 4).
Таблица 4
Результаты испытаний металла змеевиков на длительную прочность для сталей 15Х5М, 15Х5МУ
Установка | Образец | Температура испытаний, °С | Напряжение sв/долговечность, МПа/ч |
АТ-1 | 1 | 500 | 300/0,2; 241/5,5; 240/20; 195/5,5; 194/107; 169/139; 169/319; 150/2600 |
АТ-6 | 2 | 550 | 107/67; 122/71; 95/126; 115/242; 86/306; 106/380; 94/489; 77/529; 76/1196 |
АТ-6 | 3 | 550 | 281/22; 238/139; 257/142; 146/936; 199/1992; 180/2410 |
АТ-6 | 4 | 550 | 124/42; 105/105; 109/117; 93/260; 94/281; 60/576; 75/727; 75/1176 |
АТ-6 | 5 | 550 | 96/221; 98/334; 111/477; 88/713; 65/890; 77/966; 77/1133; 87/1579 |
АТ-6 | 6 | 550 | 108/96; 114/141; 122/220; 107/504; 85/578; 93/670; 82/1204; 94/1243; 75/1316 |
АТ-6 | 7 | 550 | 225/43; 225/58; 264/69; 221/138; 182/477; 160/582; 160/634; 182/816 |
АТ-6 | 8 | 550 | 123/56; 98/75; 109/82; 82/190; 98/455; 82/579; 69/697 |
Л-24/6 | 9 | 550 | 114/43; 97/196; 98/225; 93/462; 82/579; 69/692 |
Л-35-11-300 | 10 | 550 | 106/42; 91/216; 106/250; 91/432; 75/816; 75/1272; 65/1319; 65/1963; 57/2532 |
Л-35-11-300 | 11 | 550 | 105/46; 105/61; 91/98; 90/212; 75/265,5; 90/288; 60/288; 75/505; 60/632; 41/1320 |
Г-43-107 | 12* | 550 | 300/21; 233/202; 186/502; 187/506; 168/525; 215/672; 155/717; 139/1056; 167/1202 |
Парекс-1 | 13 | 500 | 232/21; 218/144; 188/203; 187/722; 150/930; 171/1052; 172/1362; 158/1471; 160/1484 |
Л-35-11/600 | 14* | 525 | 204/21; 174/96; 153/360; 153/239; 126/1755; 110/2136; 110/1680; 126/1440 |
Л-35-11/600 | 15* | 650 | 85/24; 82/51; 26/783; 34/505; 34/312; 60/31; 60/60; 20/1012; 25/771; 48/384 |
Л-35-11/600 |
16* |
525 |
207/95; 240/27; 135/664; 166/740; 153/708; 125/1047; 180/285; 134/1898; 153/985;
166/567 |
Л-35-11/600 | 17* | 650 | 78/68; 78/52; 54/164; 64/163; 54/130; 40/455; 26/729; 39/374 |
* – Образец из стали 15Х5МУ |
Кривые длительной прочности можно аппроксимировать стандартной логарифмической зависимостью σ = a – blog10(t), (1) где σ – приложенное напряжение; t – время до разрушения; a, b – подгоночные коэффициенты, определяемые методом наименьших квадратов.
Результаты испытаний приведены в табл. 4; параметры зависимости (1) – в табл. 5, графики – на рис. 2.
Таблица 5
Значения эталонных параметров a0, b0 для разных температур
Параметр | Марка стали | |||||
15Х5М | 15Х5МУ | |||||
Температура, °C | 500 | 550 | 600 | 650 | 550 | 650 |
a0 | 301 | 234 | 164 | 115 | 315 | 115 |
b0 | 42,7 | 40,1 | 28,7 | 20,0 | 50,0 | 19,7 |
Зависимости напряжения разрушения от логарифма времени, полученные для всех образцов, близки к линейным. При этом для большинства образцов графики этих зависимостей, как и следовало ожидать, лежат ниже графиков, соответствующих испытаниям сталей 15Х5М и 15Х5МУ в состоянии поставки [2]. Для некоторых образцов, например для образца 3, были получены неожиданно высокие характеристики длительной прочности.
Это может объясняться отсутствием точных данных о материале труб в исходном состоянии и о способе их термообработки. Возможно, змеевики, на которые отсутствуют сертификаты, были изготовлены из стали 15Х5МУ, имеющей тот же химический состав, что и сталь 15Х5М, но обладающей более высокой длительной прочностью.
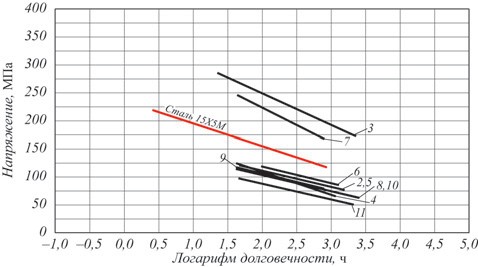
Обращает на себя внимание тот факт, что при заметном относительном смещении кривых длительной прочности они имеют примерно одинаковый наклон (см. рис. 2). Различие лежит в пределах погрешности проведенных экспериментов при относительно короткой базе испытаний. Это позволяет провести общую математическую обработку экспериментальных данных и свести все кривые зависимости к единому углу наклона b0, который имеет эталон – сталь в состоянии поставки при той или иной температуре испытания на длительную прочность (рис. 3). Эталонные значения параметров a0 и b0 для разных температур приведены в табл. 5. В этом случае каждая из полученных зависимостей характеризуется единственным параметром, а именно сдвигом Δa по отношению к принятой за эталон кривой.
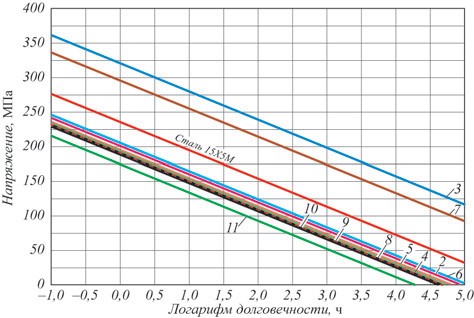
от времени до разрушения, приведенные к единому наклону при температуре испытаний образцов 550°C. Нумерация кривых соответствует нумерации образцов (см. табл. 1)
Очевидно, что значения сдвигов должны определяться температурой и временем эксплуатации змеевика.
В процессе длительной эксплуатации хромомолибденовых сталей при высоких температурах в металле происходит целый ряд физико-химических процессов: химические превращения карбидов, образование сигма-фазы, процессы диффузии, приводящие к коагуляции карбидов хрома по границам зерен, изменение размеров зерна и т.д. Каждое из таких превращений характеризуется соответствующими кинетическими параметрами или коэффициентами диффузии компонентов стали [13, 14]. В случае реакций первого порядка, например карбидных, уменьшение содержания исходной фазы во времени описывается экспоненциальным законом [15, 16]. Для процессов, контролируемых диффузией (отвод углерода из зоны распада карбидов, сегрегация легирующих элементов и примесей по границам зерен), зависимость от времени при одномерном движении фронта диффундирующего компонента выражается через функцию ошибок (функция Лапласа) [17]. В целом совокупность перечисленных процессов приводит к старению стали под воздействием эксплуатационных факторов. Для описания кинетики старения сталей часто используют уравнение Колмогорова–Джонсона–Мела–Аврами [18–20], в котором степень старения ϕ является функцией времени τ и абсолютной температуры T: ϕ(T, τ) = 1 – e –[k(T)τ] n , (2) а константа скорости имеет вид аррениусовской зависимости k(T) = k0e –ΔE/RT, (3) где R – газовая постоянная.
Уравнение (2) описывает асимптотическое приближение от исходного состояния (ϕ = 0) к предельному состоянию системы (ϕ = 1) во времени. При повышении температуры значения кинетических параметров растут, что ведет к ускорению процесса эволюции системы в направлении предельного состояния. Можно предположить, что сдвиг кривых длительной прочности Δa = a – a0 (как интегральная характеристика процесса деградации стали) также протекает от исходного значения (кривая эталона) до некоторого предельного значения, приближаясь к пределу асимптотически, т.е. может быть описан зависимостью типа (2). Такую зависимость можно записать в следующем виде:
Δa = Δamaxϕ(T, τ) = [Δa0 + α(t – t0)]ϕ(T, τ), (4) где T – абсолютная температура; τ – время эксплуатации змеевика (×106, ч); α – поправочный коэффициент; t – температура, для которой рассчитывается кривая длительной прочности; t0 – температура, условно принятая за базовую для испытаний (в данной работе принято значение t0 = 550°С).
После оптимизации параметров модели получим:
Δa0 = 67,5 МПа, α = –0,26 МПа⋅K–1, k0 = 0,18⋅10–6, 1/ч;
ΔE = 9,98 кДж/моль;
n = 1,5. В качестве эталонов во всех случаях принимали зависимости (1) для сталей 15Х5М и 15Х5МУ в исходном состоянии, построенные для тех же температур, при которых проводили испытания образцов (см. табл. 4). Логарифмические зависимости напряжений от времени до разрушения, приведенные к единому наклону для образцов стали 15Х5М, испытанных при температуре 550°C, показаны на рис. 3.
Для большинства исследованных труб просматривается достаточно четкая корреляция (с учетом возможных неточностей в исходных данных об их эксплуатации) между рассчитанными и фактическими сдвигами кривых длительной прочности относительно эталонных (рис. 4).

При построении корреляционной зависимости не учитывались данные для тех труб, у которых оказались завышенные значения прочностных показателей, что может быть связано с ошибочностью исходных данных об эксплуатации змеевиков.
Все параметры уравнений (2) – (3) являются подгоночными, и вряд ли им можно приписать какой-либо определенный физический смысл. Однако, поскольку эти уравнения косвенно описывают старение стали по сумме приводящих к нему механизмов, энергию активации
ΔE можно сопоставить с энергиями активации отдельных топохимических процессов, например, диффузии углерода или легирующих элементов в сталях [17, 19, 20].
При этом оказывается, что полученное нами значение примерно на порядок меньше энергии активации, характерной для диффузионного переноса. Возможной причиной этого является то, что лабораторные исследования диффузии или других механизмов старения сталей проводятся при существенно более высоких температурах, чем рабочие температуры эксплуатации змеевиков, а длительность соответствующих экспериментов в десятки раз короче времени эксплуатации печного оборудования нефтеперерабатывающих заводов. В более мягких условиях кинетика деградации стали может иметь иные закономерности. Кроме того, изменение свойств металла змеевиков происходит в условиях их нагружения внутренним давлением, что может вносить особенности в протекание процесса старения.
Полученная зависимость (2) совместно с уравнением σ = a – b0log10(t) = a0 + Δa – b0log10(t) (5) позволяет приближенно оценивать значение длительной прочности сталей 15Х5М и 15Х5МУ после длительных сроков эксплуатации при разных температурах. Так, через 200 000 ч эксплуатации при температуре 450°C для стали 15Х5М ожидаемое значение смещения кривой длительной прочности от эталонной кривой, соответствующей расчетной температуре 500°C, Δa = 6,9 МПа. Соответственно, длительная прочность при расчетной температуре и сроке дальнейшей эксплуатации змеевика 50 000 ч составит 93,4 МПа. Полученные данные дают также возможность оценивать остаточный ресурс печных змеевиков.
Значения эмпирических параметров уравнений (2) – (4) будут уточняться по мере накопления экспериментальных данных по длительной прочности металла змеевиков, отслуживших продолжительные сроки эксплуатации.
При этом для труб, у которых кривые длительной прочности значительно отличаются от рассчитанных по данным уравнениям, следует перепроверять и уточнять исходные данные по длительности и рабочей температуре эксплуатации.
Установлено, что в процессе длительной эксплуатации печных змеевиков из сталей 15Х5М и 15Х5МУ в условиях повышенной температуры и агрессивной среды происходит деградация микроструктуры металла – коагуляция карбидов, выстраивание крупных карбидов в цепочки по границам ферритных зерен, а также равномерное частичное обезуглероживание, вызванное эксплуатацией металла в окислительной среде при высокой температуре. Степень деградации стали зависит от срока эксплуатации и рабочей температуры змеевика. Следствием микроструктурных изменений сталей змеевиков является падение параметров длительной прочности металла.
В первом приближении такое изменение можно охарактеризовать сдвигом кривых длительной прочности относительно кривых, построенных для сталей в исходном состоянии, в сторону более низких значений напряжений.
Зависимость таких сдвигов от рабочей температуры и срока эксплуатации змеевиков может быть описана уравнением Колмогорова–Джонсона–Мела–Аврами.
Полученные данные позволяют дать предварительную оценку остаточного ресурса змеевиков по их эксплуатационным характеристикам.
Список литературы
- Ентус Н.Р., Шарихин В.В. Трубчатые печи в нефтеперерабатывающей и нефтехимической промышленности. М.: Химия, 1987.
- Дьяков В.Г., Медведев Ю. С., Абрамова З.А., Бочаров А.Н., Пупелис В.Н. Легированные стали для нефтехимического оборудования. М.: Машиностроение, 1997.
- Добротворский А.М., Балутов А.В., Денисенко Е.П., Шевякова Е.П., Легостаев Д.А., Макаров А.В. Опыт экспертизы промышленной безопасности на строительство технологических печей, технического диагностирования и анализа технического состояния печного оборудования//Химическая техника. 2014. №12. 4. Ватник Л.Е., Тришкина И.А., Трыков Ю.П, Гуревич Л.М. Эволюция структурно-механических состояний стали 15Х5М в процессе эксплуатации печных змеевиков//Известия ВолгГТУ. 2007. №5.
- Мухин В.Н. Тришкина И.А., Трыков Ю.П. Структурно-механические состояния металла труб печных змеевиков с пониженной твердостью//Известия ВолгГТУ. 2011. Т.8., №15.
- Мухин В.Н. Влияние нерегламентных термических воздействий на физико-механические свойства металла нефтеперерабатывающего оборудования//Химическая техника. 2012. №7.
- Добротворский А.М., Масликова Е.А., Андреева В.Д. Влияние эксплуатационных факторов на структуру материала змеевиков технологических трубчатых печей//Заводская лаборатория. Диагностика материалов, 2015. Том 81. №9.
- ГОСТ 20072–74. Сталь теплоустойчивая. Технические условия
- ГОСТ 5639–82. Стали и сплавы. Методы выявления и определения величины зерна
- ГОСТ 550–75. Трубы стальные бесшовные для нефтеперерабатывающей и нефтехимической промышленности. Технические условия.
- Сорокин В.Г., Волосникова А.В., Вяткин С.А. и др. Марочник сталей и сплавов/Под общ. ред. В. Г. Сорокина. М.: Машиностроение, 1989.
- РТМ 26-02-67–84. Методика расчета на прочность элементов печей, работающих под давлением. М.: ВНИИнефтемаш, 1983.
- Пигрова Г.Д. Кинетика карбидных реакций в Cr-Mo-V-стали //Металловедение и термическая обработка металлов. 1995. №8.
- Vodopivec F., Jenko M., Vojvodiс J. Stability of MC carbide particles size in creep resisting steels//METABK. 2006. Vol.45. №3.
- Bhadeshia H. K. D. H. Advances in the Kinetic Theory of Carbide Precipitation//Materials Science Forum, 2003. Vol. 426–432.
- Baltusnikas A., Levinskas R., Lukosiute I. Kinetics of Carbide Formation During Ageing of Pearlitic 12X1MФ Steel//Materials Science (Medziagotyra). 2007. №4.
- Гюлиханданов Е.Л., Кисленков В.В., Хайдоров А.Д. Термическая обработка металлов. СПб.: Изд. Политех. ун-та, 2014.
- Кристиан Дж. Теория превращений в металлах и сплавах. Ч. 1. Термодинамика и общая кинетическая теория. М.: Мир, 1978.
- Buono V.T.L., Andrade M.S., Gonzalez B.M. Kinetics of Strain Aging in Drawn Pearlitic Steels//Metallurgical and Materials Transactions A. Vol. 29a, May 1998.
- Mirzadeh H., Najafizadeh A. Aging kinetics of 17-4 PH stainless steel//Materials Chemistry and Physics, 2009. Vol. 116.