Авторы: А.М. Добротворский (ЗАО «НПО «Ленкор», СПбГУ), А.В. Балутов, Е.П. Денисенко, А.В. Копыльцов, Д.А. Легостаев, А.Г. Саватеев (СПбГУ).
Опубликовано в журнале Химическая техника №1/2016
Основные особенности эксплуатации, технического диагностирования и анализа технического состояния
Особенности эксплуатации печных змеевиков и основные факторы, воздействующие на их материал
Технологическое оборудование нефтеперерабатывающих и нефтехимических производств эксплуатируется в условиях комплексного воздействия повышенных температур, давлений и агрессивных технологических сред, которые в разных количествах могут содержать водород, сероводород, меркаптаны, соединения хлора и другие коррозионно-активные компоненты. Воздействие агрессивных сред, особенно при повышенных температурах, приводит к постепенной деградации конструкционных материалов – сталей разных групп и классов, что может стать причиной отказов и аварий технологического оборудования.
Наиболее уязвимыми, с точки зрения быстрого развития процессов деградации металла, являются змеевики трубчатых печей. В настоящее время в нефтепереработке используют печи разных конструкций, в которых осуществляется нагрев сырья до температуры 300…900°C.
В условиях высоких температур, давлений и объемных скоростей сырьевых потоков, а также воздействия разогретых дымовых газов могут развиваться различные коррозионные и эрозионные процессы, приводящие в совокупности к потере прочности змеевиков, их формоизменению и, в конечном счете, к их разгерметизации и разрушению.
Основной причиной ограничения срока службы печных змеевиков нагревательных печей является тепловое старение под действием температурных и временных факторов, что обусловливает изменение их микроструктуры и снижение длительной прочности металла. В наибольшей степени это касается змеевиков реакционных печей пиролиза и парового риформинга, которые работают при температурах, на несколько сотен градусов превышающих температуру эксплуатации змеевиков нагревательных печей. Для них превалирующим фактором деградации являются высокотемпературная ползучесть и хрупкое разрушение в результате науглероживания металла.
Ускоренному тепловому старению способствуют отклонения от технологического режима эксплуатации нагревательных трубчатых печей, сопряженные со значительным перегревом труб, что неизбежно ведет к аварийным остановкам производств.
Другой причиной снижения долговечности змеевиков нагревательных и реакционных печей является воздействие технологической среды на металл труб. На внутренних поверхностях труб осаждаются продукты конденсации и частичного коксования углеводородов, а также соли недостаточно обессоленной нефти. Отложения снижают теплопередачу, увеличивают локальную температуру стенки и тем самым ускоряют процессы коксования продукта и деградации материала змеевиков.
Отслоение продуктов коррозии приводит к утонению стенки трубы и локальному перегреву в местах утонения.
В стояночных режимах печей стали печных змеевиков подвергаются коррозионному воздействию кислых продуктов разложения технологических отложений при контакте с влажным воздухом. В этих условиях из-за контакта с влагой коррозия протекает по электрохимическому механизму.
По аналогичному автокаталитическому механизму развивается сульфидная коррозия, вызываемая химическим взаимодействием металла с серусодержащими компонентами сырья. Такой вид коррозии наиболее характерен для оборудования, эксплуатирующегося на установках первичной переработки нефти. Помимо образования отложений, воздействие серы может проявляться в виде питтинговой (язвенной) коррозии – локальных язв или их скоплений, имеющих глубину, сравнимую с толщиной стенки.
Для печных змеевиков установок каталитического риформинга и гидроочистки наибольшую опасность представляет водородная коррозия, которая приводит к распаду карбидов и обезуглероживанию сталей. Обезуглероживание существенно снижает механические и особенно пластические свойства материалов.
Указанные факторы ограничивают срок безопасной эксплуатации технологических печей и предъявляют особые требования к применяемым материалам, качеству изготовления и монтажа печного оборудования, надзору за эксплуатацией печей и их техническому диагностированию.
Особенности и опыт технического диагностирования трубчатых печей
Специалисты ЗАО «НПО «Ленкор» ежегодно выполняют работы по экспертизе промышленной безопасности и техническому диагностированию технологических печей, отработавших установленный ресурс, для выяснения возможности их дальнейшей эксплуатации. Кроме того, они осуществляют работы по контролю качества монтажных и ремонтных работ, производимых для вновь изготавливаемого оборудования, а также исследования металла с целью выявления причин отказов и инцидентов, связанных с технологическими печами.
Техническое диагностирование печных змеевиков требует применения современных методов неразрушающего контроля, включая рентгенографический, являющийся чрезвычайно эффективным методом, которым на «экспертном» уровне владеют лишь немногие организации.
Существенную роль играют и лабораторные исследования конструкционных материалов. Они имеют два основных направления. Во-первых, это определение фактического состояния и механических свойств материалов печных змеевиков после длительной эксплуатации при воздействии температурных и силовых нагрузок, а также влияния среды, что необходимо для установления возможности и сроков эксплуатации печных змеевиков при заданных параметрах технологического процесса. Во-вторых, лабораторные исследования необходимы для определения причин инцидентов и аварий, произошедших при эксплуатации печей.
Для выполнения задач металловедческих исследований вырезок металла необходимо привлечение самого современного оборудования и методов, таких, как электронная микроскопия, рентгеновский микроанализ, рентгенофазовый анализ и др. Для определения механических характеристик материалов выполняется комплекс механических испытаний, включая испытания на длительную прочность.
Рассмотрим несколько конкретных примеров работ, выполненных за последнее время.
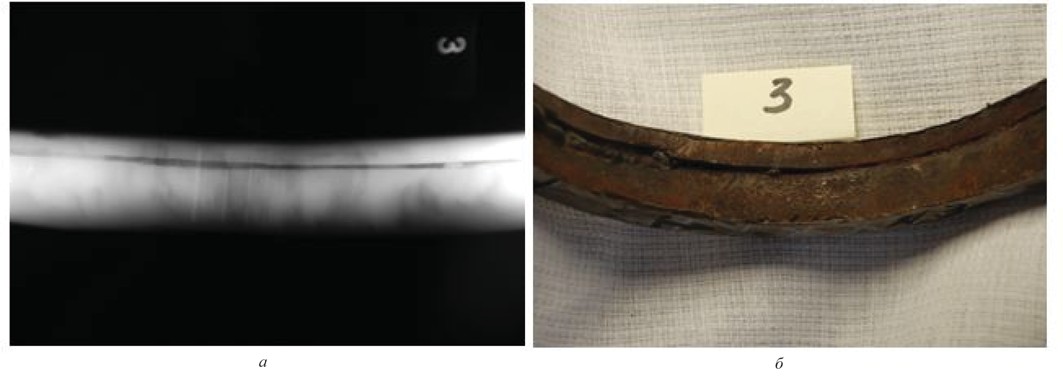
Дефекты, выявляемые при радиографическом контроле печных змеевиков. При выполнении рентгенографического контроля в ходе технического диагностирования печных змеевиков (сталь 08Х18Н10Т, труба диаметром 219Ч14 мм) установки гидроочистки дизельного топлива Л-24-10/2000 были выявлены дефекты в корнях швов со стороны стенки печи. Снимок типичного дефекта приведен на рис. 1, а. Вырезка дефектного стыка (рис. 1, б) полностью подтвердила результат дефектоскопии. Следует отметить, что установить наличие такого дефекта альтернативным методом – с помощью ультразвуковой дефектоскопии – крайне затруднительно как из-за класса стали (аустенитная сталь), так и из-за расположения дефекта.
Техническое диагностирование технологических печей Ачинского НПЗ. В результате аварии, произошедшей 15 июня 2014 г. на территории секции С-400 установки ЛК-6У «АНПЗ ВНК», помимо основных разрушений, вследствие воздействия ударной волны, огня, конвективного воздействия теплового потока, дыма, воды при пожаротушении частичное повреждение могло получить технологическое оборудование смежных секций С-100, С-200 и С-300 установки. Для оценки необходимых ремонтно-восстановительных мероприятий и возможности дальнейшей эксплуатации специалисты
ЗАО «НПО «Ленкор» выполнили комплексное обследование технологических печей этих секций.
Техническое диагностирование печей секции С-100 (первичная переработка сырья) не выявило поражений от воздействия ударной волны и пожара, влияющих на безопасную эксплуатацию печей. Наружный осмотр змеевиков показал, что состояние основных элементов змеевиков удовлетворительно: прогары, отдулины, свищи и трещины отсутствуют, изменений геометрических размеров и форм основных элементов змеевиков не обнаружено. В то же время результаты ультразвуковой толщинометрии змеевика радиантной камеры печи П-101/3 этой секции выявили значительное локальное утонение стенок (до 6 мм при исполнительной толщине 12 мм), связанное с эксплуатационными факторами, при том, что змеевики камеры радиации были заменены в 2008 и 2010 гг. На этих участках произведены вырезки катушек, осмотр которых показал наличие глубоких раковин и вымывание внутренней поверхности калачей и отводов (рис. 2, а). Вырезка катушек позволила провести осмотр внутренней поверхности змеевиков с применением телевизионной эндоскопии. Осмотр подтвердил данные толщинометрии (рис. 2, б).
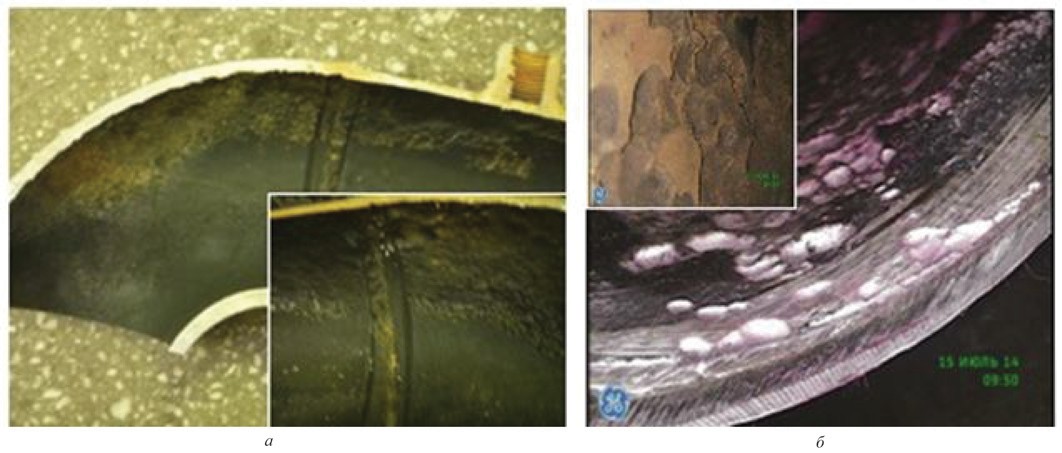
Обследование печей секции С-200 (каталитический риформинг) и С-300 (гидроочистка) также не выявило механических дефектов, связанных с аварией. Однако, учитывая, что печь П-203/3-2 этой секции находилась ближе всего к очагу аварии, было принято решение произвести контрольную вырезку металла из змеевика камеры радиации для лабораторных металловедческих исследований. По результатам проведенного исследования установлено, что твердость труб выше максимально допустимых значений для стали 15Х5М по СТО – СА 03004–2009. Микроструктура соответствует стали 15Х5М после быстрого охлаждения от температуры выше критической точки А1. Изменения в структуре (рис. 3) – образование бейнита и, как следствие, повышение твердости – могут быть связаны с нарушением режима эксплуатации при тушении пожара, возникшего вследствие аварии.
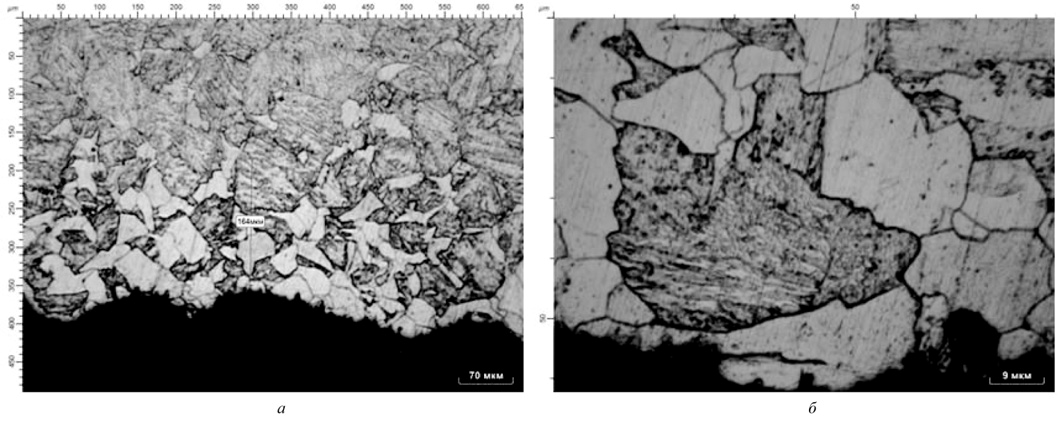
Исследование металла змеевика печи П-1 установки каталитического риформинга ЛГ-35/8-300Б с целью выяснения причин выявленного пропуска. Установка эксплуатируется с 1972 г. При плановом обследовании блока гидроочистки установки в 2012 г. был обнаружен пропуск газосырьевой смеси в змеевике радиантной камеры печи П-1 (сталь Х12CrMo9.1. Рабочие параметры: давление – 3,9 МПа, температура – 420°С). Для выявления причин пропуска выполнены комплексные металловедческие исследования катушки, вырезанной из дефектной части змеевика (рис. 4). Химический анализ отложений на внутренней поверхности змеевика показал наличие в них значительного содержания серы. По данным рентгенофазового анализа отложений установлено, что основную долю в них составляет сульфид железа FeS, далее (в порядке убывания) – смешанные сульфиды и оксиды железа и хрома: FeCr2S4, Cr2O3FеO, Cr2S3 (рис. 5).
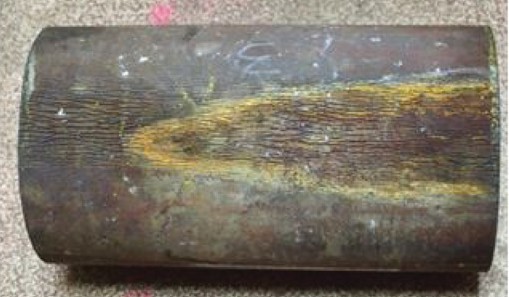
Сульфиды, по всей видимости, образовались в результате длительного взаимодействия металла змеевика с сероводородом и серусодержащими компонентами прямогонной бензиновой фракции при повышенных температурах. Образование оксидов на внутренних поверхностях труб является результатом окисления металла и серусодержащих отложений в процессе выжига кокса.
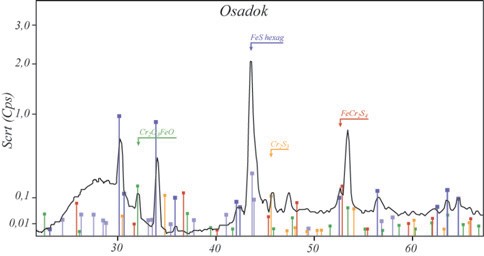
Результаты исследования внутренней поверхности и сечения труб методом растровой электронной микроскопии с рентгеновским микроанализом (исследования методом растровой электронной микроскопии проведены в МРЦ «Нанотехнологии» СПбГУ) подтвердили данные выводы о природе отложений (рис. 6, а), а также показали, что причиной растрескивания металла является воздействие коррозионно-активных соединений, содержащих серу, и солей натрия, попадающих в змеевик вместе с водой при гидравлических испытаниях (рис. 6, б).
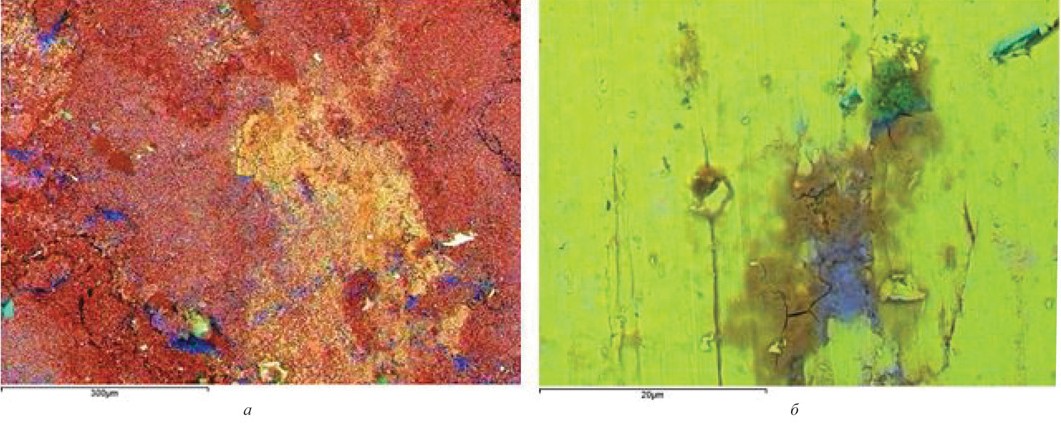
синий цвет – сера, голубой – кремний, зеленый – натрий, желто-зеленый – железо, оранжевый – кислород, красный – углерод
Образование трещины произошло из-за структурно-механической неоднородности металла змеевика вследствие локального высокотемпературного перегрева, обусловленного накоплением отложений на внутренней поверхности змеевика в наиболее теплонапряженной зоне. Наличие отложений привело к снижению интенсивности отвода теплоты сырьевым потоком, к местному перегреву трубы, образованию отдулины и далее к разгерметизации змеевика.
Исследования вырезок металла коллектора печи
Н-4101-В установки получения водорода (УПВ). Печь
Н-4101-В предназначена для проведения реакции парового риформинга природного газа и легкой бензиновой фракции, разбавленных водяным паром, с целью получения водорода, направляемого на установку гидрокрекинга. Рабочие параметры печи: давление – 2,87 МПа, температура – 890°С. Целью комплексного исследования вырезок металла коллектора печи было определение работоспособности оборудования в связи с локальными перегревами. Корпус выполнен из стали А516Gr65 (российский аналог 16ГС), футерован бетоном и защищен кожухом из коррозионно-стойкой стали. В июне 2014 г. зафиксирован перегрев коллектора до температуры 655°C (рис. 7) продолжительностью не более 70 ч.
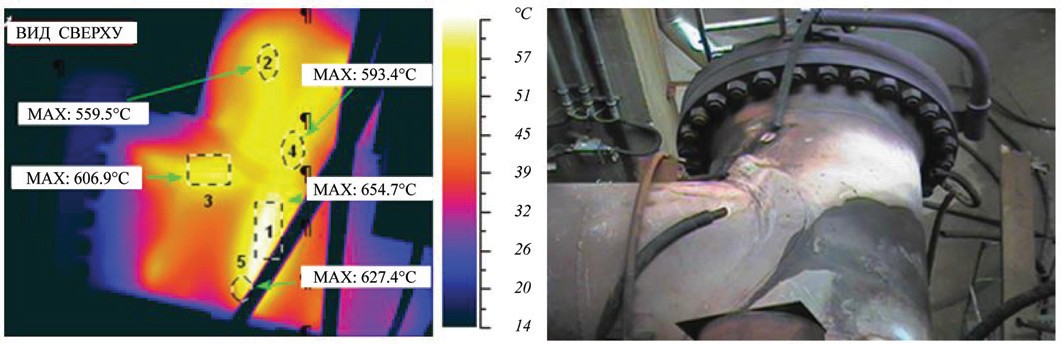
Исследование вырезок металла из зоны перегрева методом оптической металлографии показало, что микроструктура исследованного металла характерна для кремнемарганцовистой стали. В структуре произошла частичная сфероидизация перлита, зафиксировано снижение твердости металла в результате его обезуглероживания (рис. 8). Данные электронной микроскопии позволили выявить развитие водородной коррозии стали со стороны внутренней поверхности коллектора на глубину 20…30 мкм (рис. 9).
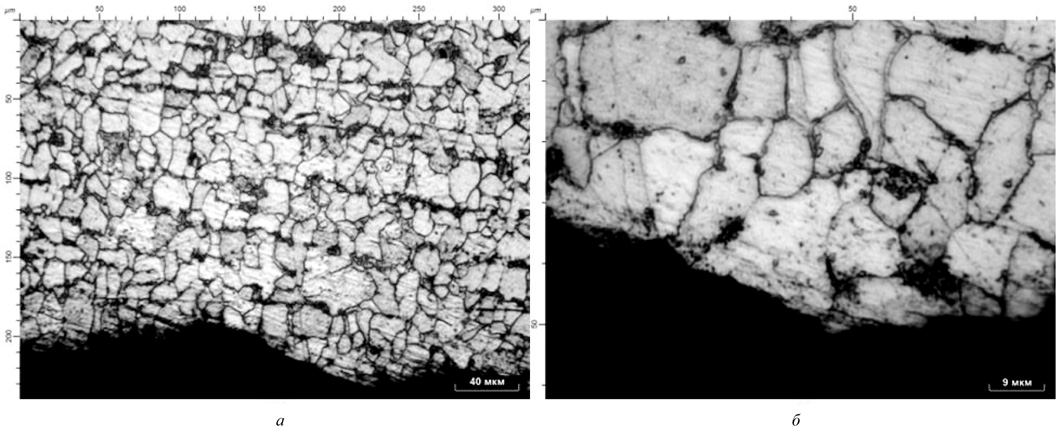
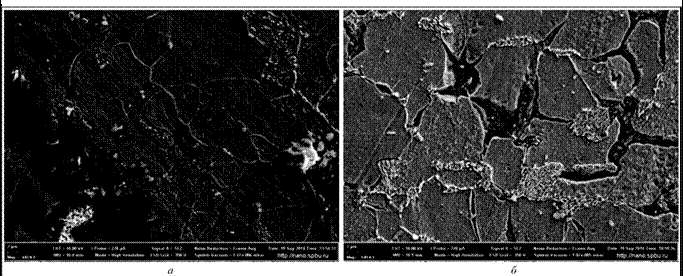
Локальные перегревы в корпусе коллектора, возникшие в зонах несплошности футеровки, привели к развитию водородной коррозии углеродистой стали на участках возникновения прямого контакта металла с горячим синтез-газом. Выявляемые процессы воздействия коррозионно-активной среды являются необратимыми и в случае дальнейшего перегрева могут привести к резкому изменению механических характеристик металла. Указанное позволяет рекомендовать замену коллектора изготовленным из более водородостойкой стали.
Таким образом, экспертиза промышленной безопасности и техническое диагностирование технологических печей как наиболее опасных частей технологических установок необходимо выполнять наиболее квалифицированными экспертными организациями с привлечением современных и наиболее эффективных средств неразрушающего контроля. Это позволяет выявлять дефекты, возникающие как на стадии изготовления и монтажа оборудования, так и развивающиеся в процессе эксплуатации при рабочих условиях.
Лабораторные исследования конструкционных материалов – единственный надежный метод, позволяющий получить достоверную информацию о текущем состоянии материалов печных змеевиков. Это является основой для прогнозирования возможности и сроков дальнейшей эксплуатации печных змеевиков.
Комплексное исследование и анализ причин инцидентов и отказов печного оборудования, прежде всего змеевиков, создает основу повышения надежности эксплуатации технологических печей.
Список литературы
- ГОСТ Р 53682–2009. Установки нагревательные для нефтеперерабатывающих заводов. Общие технические требования
- СТО 00220302-002–2011. Методические указания по контролю технического состояния и оценке остаточного ресурса змеевиков трубчатых печей.
- СА-03-004–2009. Трубчатые печи, резервуары, сосуды и аппараты нефтеперерабатывающих и нефтехимических производств. Требования к техническому надзору, ревизии и отбраковке.
- РТМ 26-02-67–84. Методика расчета на прочность элементов печей, работающих под давлением
- ТУ 1333-078-00220302–2004. Трубы реакционные и их элементы из жаропрочных сталей и сплавов для нефтехимического высокотемпературного оборудования
- ТУ 1333-094-00220302–2005 Трубы центробежно-литые из коррозионностойких и жаропрочных сталей и сплавов для реакционных трубчатых печей высокотемпературного нефтехимического оборудования.
- Добротворский А.М., Соколов В.Л., Ульянов П.Г., Копыльцов А.В., Масликова Е.И., Шевякова Е.П., Рыбкин А.Г., Бондаренко А.С., Адамчук В.К. Перспективы применения современных физических методов для оценки состояния конструкционных материалов оборудования нефтеперерабатывающих производств. В кн. Актуальные задачи нефтехимиии и нефтепереработки. СПб.: НПО «Профессионал», 2010.
- Добротворский А.М., Корнилов В.В., Балутов А.В., Денисенко Е.П., Копыльцов А.В., Григорьева Т.Н. ЗАО «НПО «Ленкор»: десятилетие работы в области экспертизы промышленной безопасности технических устройств ООО «Сибур-Нефтехим»// Энергетическая стратегия. 2011. Сентябрь 2011.
- Добротворский А.М., Шевякова Е.П., Масликова Е.И., Михайловский В.Ю., Дубик А.А, Симанов М.А., Караваева М.А. Современные методы выявления причин отказов нефтеперерабатывающего и нефтехимического оборудования//Материалы совещания «Современные подходы к выбору оборудования и материалов при проектировании, эксплуатации и строительстве технологических установок на нефтеперерабатывающих и нефтехимических предприятиях». М.: ООО «НТЦ при Совете главных механиков», 2014.
- Добротворский А.М. Диагностика оборудования НПЗ: современное состояние и перспективы//Технополис XXI. 2014. Вып. 30.
- А.M. Добротворский, Е.И. Масликова, В.Д. Андреева. Влияние эксплуатационных факторов на структуру материала змеевиков технологических печей//Заводская лаборатория. Диагностика материалов. 2014.
- Alvino A., Lega D, Giacobbe F., Mazzocchi V., Rinaldi A. Damage characterization in two reformer heater tubes after nearly 10 years of service at different operative and maintenance conditions// Eng. Fail. Anal. 2010. Vol. 17. №7–8.
- Quickel G., Jaske C., Rollins B., Beavers J. Failure Analysis and Remaining Life Assessment of Methanol Reformer Tubes//J Fail. Anal. and Preven. 2009. Vol. 9.
- Tawancy H.M. Degradation of mechanical strength of pyrolysis furnace tubes by high-temperature carburization in a petrochemical plant//Eng. Fail. Anal. 2009. Vol. 16. №7.