Автор: А.В. Жулин, Р.А. Евсиков, Д.Е. Васильев, В.Н. Середа, Д.С. Попов (ОАО «НОРЭ).
Опубликовано в журнале Химическая техника №12/2015
Впрыскивающие пароохладители (ВПО) размещаются в необогреваемых паропроводах. Особенность режимов работы ВПО заключается в неравномерности температуры, сохраняющейся при завершении процессов теплои массообмена: температура пара выше на входе в ВПО, чем на выходе, а после впрыска питательной воды температура насыщения пара также выше, т.е. за пароохладителем пар всегда перегретый [1].
Основной задачей впрыска воды в перегретый пар является поддержание заданной (постоянной в ходе работы) температуры пара за следующей после впрыска поверхностью нагрева пароперегревателя. При относительно стабильных давлении, температуре и расходе пара на входе в ВПО режим работы последнего нестабилен даже при постоянной нагрузке котла.
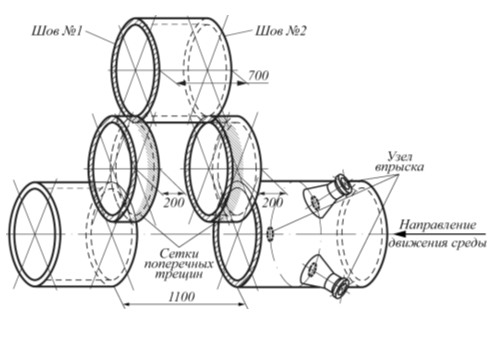
В ходе проведения экспертизы промышленной безопасности трубопровода пара [2] обследовали узел охлаждения (рис. 1), эксплуатирующийся при следующих параметрах:
- до узла охлаждения: рабочее давление – 4,75 МПа, рабочая температура – 440…470°С;
- после узла охлаждения: рабочее давление – 4,75 МПа, рабочая температура – 373°С.
Наработка данного трубопровода на момент проведения обследования составила ~279 000 ч.
Сварные швы коллектора (диаметр 406,4×26,2 мм; сталь марки STPA12 стандарт JIS) узла охлаждения подверглись ультразвуковому контролю (УЗК), в ходе которого установлено, что два сварных шва, расположенных до зоны впрыска, имеют недопустимые дефекты (см. таблицу).
Контролируемый элемент | Описание обнаруженного дефекта | Оценка дефекта в баллах |
Шов №1 | 20,0…26,2Д-120;
19,5…26,2Д-170; 20,0…26,2Д-140 |
1 |
Шов №2 | 20,5…26,2Д-110;
19,5…26,2Д-180 |
1 |
Наличие обнаруженных УЗК дефектов в корне шва было подтверждено при обследовании видеоэндоскопом ViZaar VUMAN X-WAY IK RF). Дефектные сварные соединения ранее подвергались ремонту в месте врезки «катушки» (в остальных сварных швах на данном участке дефектов не зафиксировано). Обнаруженные дефекты – непровар корня шва, подрез (рис. 2) – образовались вследствие несоблюдения технологии сварки в процессе ремонта
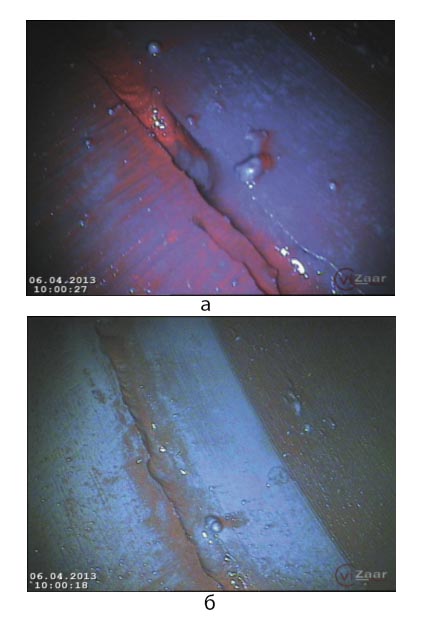
Измерение твердости металла наружной поверхности показало, что фактический предел прочности основного металла обследованных участков соответствует требованиям стандартов JIS.
По результатам исследований микроструктуры наружной поверхности основного и наплавленного металла и металла околошовных зон сварных соединений трубопровода нежелательных эксплуатационных изменений структуры, таких, как микротрещины, поры, структурноизбирательные коррозионные поражения, посторонние включения, расслоения металла и другие микродефекты, не выявлено.
После проведения неразрушающих методов контроля было принято решение о вырезке сварных швов с дефектами (см. рис. 1) и проведении цветной дефектоскопии подготовленных кромок торцов трубы и участков околошовных зон шириной ~200 мм). В результате контроля обнаружены сетки поперечных трещин с ярким индикаторным следом (рис. 3), являющиеся следствием термической усталости металла.
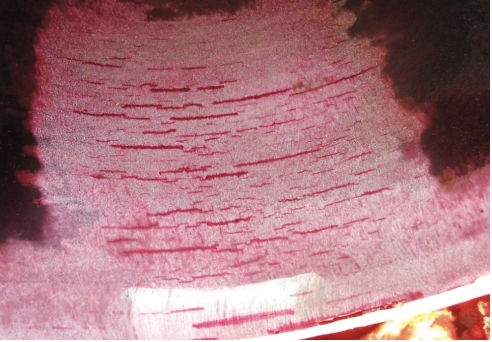
После проведения обследований принято следующее решение: обрезать трубопровод с двух сторон (на 200 мм) с последующей подготовкой кромок и неразрушающим контролем на наличие усталостных трещин. С получением положительных результатов контроля в трубу была вварена катушка длиной 1100 мм (см. рис. 1).
Термическая усталость металла связана с резкими краткосрочными колебаниями температуры стенки трубы при срабатывании узла охлаждения, когда в перегретый пар температурой до 470°С производится впрыск котловой воды температурой не выше 102°С. Участки внутренней поверхности трубопровода до зоны впрыска воды и сразу после нее наиболее подвержены эксплуатационному старению металла и образованию растрескивания как в основном, так и в наплавленном металле.
В связи с этим при проведении экспертизы промышленной безопасности узлов охлаждения необходимо уделять особое внимание внутренней поверхности металла.
Список литературы
- Впрыскивающие пароохладители на ТЭС//Информационный портал «Энергетика. ТЭС и АЭС/ http://tesiaes.ru/.
- СТО 1723082.27.100.005-2008. Основные элементы котлов, турбин и трубопроводов ТЭС. Контроль состояния металла. Нормы и требования.