Автор: Э.С. Гасанов, С.В. Акулов, А.Г. Чиркова, А.Г. Звенигородский (НИПИ НГ «ПЕТОН»).
Опубликовано в журнале Химическая техника №8/2014
Безопасность – категория многофакторная, поскольку само понятие опасности – это многовекторный динамически развивающийся во времени процесс. Следовательно, подходить к понятию безопасности нефтехимического объекта надо со всех сторон. По этой причине в данной статье рассматривается узкий вопрос безопасности нефтехимического оборудования от воздействия только одного наиболее поражающего фактора (влажный сероводород по отношению к двухслойным сталям), но со всех сторон и во всех фазах жизни этого оборудования: при проектировании, изготовлении, монтаже, эксплуатации, экспертизе, ремонте.
Еще древние философы утверждали, что в любой конструкции столько слабых мест, сколько в ней спаек. Это философское выражение не потеряло своей актуальности и для современных сварных конструкций, особенно, если работают они в коррозионно-активных средах, каковыми без сомнения являются перерабатываемые в нефтехимии продукты. Ведь сварное соединение представляет собой литой металл, обрамленный с двух сторон зонами термического влияния, которые в физико-химическом отношении являются зонами «слабины», в них металл хоть и не расплавляется полностью, но подвергается мощному тепловому воздействию, которое вызывает рост зерна, перекристаллизацию, образование столбчатых кристаллов в зонах неполного расплавления, возникновение остаточных напряжений. Да и металл самого сварного шва из-за превращения его из прокатанного и мелкозернистого с выровненной структурой и изотропией свойств в литой, изобилующий крупнозернистой структурой (зачастую даже видманштеттовой), дендритными образованиями, утратившими химическую однородность, насыщенный порами, шлаковыми включениями, примесями (сера, фосфор), неметаллическими включениями (сульфиды, оксиды, силикаты) становится менее надежным, тем более, что эксплуатация его производится в коррозионно-активных, а зачастую и коррозионно-агрессивных средах.
В последние годы в связи с уменьшением запасов нефти особенно остро стоит вопрос о ее более глубокой переработке, что возможно при повышении параметров проведения различных технологических процессов (температура, давление, скорости перемещения потоков, изменение агрегатного состояния перерабатываемого продукта). Это приводит к увеличению коррозионной активности перерабатываемых сред. Кроме того, резко возросли объемы переработки нефтей с повышенным содержанием сероводорода и минеральных солей, а также добавлением в перерабатываемую нефть газоконденсатов с повышенным содержанием коррозионно-активных компонентов (например, хлора или его соединений), которые в предшествующие годы к переработке не допускались из-за их коррозионной агрессивности. Все это, а также неизбежное старение производственного оборудования и экономические факторы, препятствующие его замене, создают условия, при которых повышается вероятность аварийных ситуаций. И в наибольшей степени это относится к сварным соединениям, как самым слабым участкам любого нефтехимического оборудования.
По указанным причинам металл сварного шва и зон термического влияния в сварных соединениях нефтехимического оборудования подвергается различным видам коррозии (общей, ножевой, сероводородной, межкристаллитной и др.) значительно быстрее, чем основной металл. Самым опасным в данном случае следует считать сероводородную коррозию, поскольку только воздействие сероводорода способно вызывать в металле не только повышенное общее коррозионное поражение его поверхности, но и его расслоение, а также образование в нем сквозных трещин, которые и приводят к неожиданным инцидентам. Тем более что разрушение металла происходит внезапно и носит ярко выраженный локальный характер. Весьма сложно предугадать возможность и место возникновения этого вида разрушения и принять меры, чтобы предотвратить его и связанные с ним опасные последствия.
На конкретных примерах (типичных ошибках) рассмотрим влияние различных факторов на создание потенциально опасных ситуаций при воздействии только одного коррозионного агента (влажный сероводород) на сварные соединения из двухслойных сталей на разных этапах.
1. Организационный этап. Согласно разделу 5 ГОСТ Р 15.201–2000 [1], на проектирование сосуда заказчик должен разработать техническое задание с указанием информации о рабочих параметрах и коррозионной активности среды. Выполняется это не всегда. Так, из-за отсутствия технического задания на проектирование и, следовательно, из-за отсутствия у проектанта сведений о наличии в продукте влажного сероводорода, т.е. из-за непринятия проектантом мер упреждающего характера для предотвращения сероводородного растрескивания сварных соединений биметалла (применение сварочной проволоки с высокой степенью аустенизации, выполнение термообработки сварных соединений и др.) в 2006 г. взорвалась емкость (50 м3) пропановой фракции из-за самопроизвольного разрушения продольного сварного шва ее царги после 17 месяцев эксплуатации.
2. Проектирование. 2.1. Проектанты тоже не спешат докапываться до тонкостей рабочих условий проектируемого оборудования. Так, в случае, изложенном в разделе 1, проектант не запросил у заказчика сведения об условиях эксплуатации емкости, требуемые п. 2.1.3. ПБ03-584–03 [2] и п. 2.1.2. действовавшего на момент проектирования ОСТ 26-291–94 [3]. Вместо этого был разработан чертеж с указанием технических характеристик без учета сероводородного воздействия, который согласовало руководство заказчика, в результате чего были нарушены требования раздела 5 ГОСТ Р15.201–2000 [1] о необходимости «реализации всех обязательных требований, распространяющихся на данную продукцию». 2.2. Кроме того, проект емкости не был подвергнут экспертизе промышленной безопасности согласно требованиям статьи 13 стандарта [1], и на него не было получено разрешение на применение согласно п. 1.5. документа [4], необходимость чего продиктована нестандартностью емкости: она изготавливалась из двухслойного металла, а существующее ТУ относится к емкостям из монометалла (т.е. имеет место несоответствие емкости ГОСТу, ОСТу или ТУ).
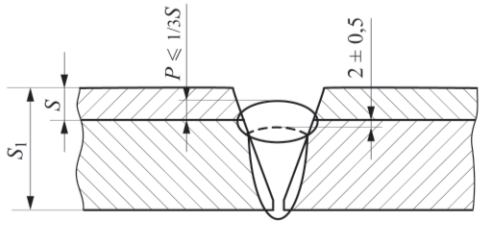
3. Выбор материалов для сосудов и аппаратов. Нормативная база в нефтехимии ориентирует проектанта на применение двухслойных сталей, тогда как ни в системе ОАО «Газпром», ни в ЕЭС России, т.е. отраслях, близких к отрасли нефтехимии по режимам эксплуатации и активности коррозионных сред, для изготовления сварных сосудов и аппаратов двухслойные стали не применяются. Объяснить это можно, видимо, только традицией: ведь когда-то на заре развития нефтехимии двухслойные стали были в несколько раз дешевле коррозионно-стойких. Но, времена, как известно, меняются: в настоящее время двухслойные стали по цене соизмеримы с коррозионно-стойкими, а традиция (а, может быть, это инертность мышления) осталась. Многолетняя практика применения двухслойных сталей в нефтехимии показывает, что использование их допустимо только при одном единственном условии – высокой технической культуре выполнения сварных соединений, в частности недопустимости сварки «черного» металла (основного слоя из углеродистой или низколегированной стали) с «белым» (коррозионно-стойкой сталью, т.е. плакирующим слоем). В п. 6.1.1 ОСТ 26.260.480–2003 [5] сказано: «Если при сварке основного слоя происходит одновременное плавление металла плакирующего слоя, то возможно существенное понижение пластичности сварного соединения, повышение его твердости и даже образование трещин» (рис. 1).
Казалось бы, не такое уж это и завышенное требование. Тем более, что существуют нормы на долю допустимого участия черного металла в составе высоколегированного сварного шва (табл. 1). Тем не менее, практика показывает, что на большом проценте сварочных стыков двухслойных сталей это требование не выполняется.
Таблица 1
Предельная доля участия основного металла конструкционной перлитной стали в высоколегированном металле наплавки
Доля участия, % | Условная группа | Сварочная проволока | Электроды | |
Марка | Тип по ГОСТ 10052 | |||
30 |
А2 |
Св-08Х20Н9Г7Т Св-08Х21Н10Г6 Св-06Х25Н12ТЮ Св-08Х25Н13
Св-07Х25Н12Г2Т Св-08Х25Р13БТЮ Св-30Х25Н16Г7 |
ОЗЛ-6 ЦЛ-9 ЗиО-8 | Э-10Х25Н13Г2 Э-10Х25Н13Г2Б Э-10Х25Н13Г2Б |
45 | А3 | Св-10Х16Н25АМ6 Св-09Х16Н25М6АФ ЭП622(08Х25Н25М3)
ЭП582(07Х15Н35Г7М6Б) ЭП690(01Х19Н18Г10АМЧ) |
ЭА-395/9 АНЖР-3У АНВ-17 НИАТ-5 ЦТ-10 | Э-11Х15Н25М6АГ2 Э-08Х24Н25М3Г2 Э-02Х19Н18Г5АМ3 Э-11Х15Н25М6А12 Э-11Х15Н25М6АГ2 |
60 |
А4 |
ЭП606(09Х25Н60М10) ЭП607(Х35Н40М4) ЭП673(08Х25Н40М7) ЭП829(08Х30Н40М6ТБ) ЭП775(08Х15Н70Г5Б2Т) |
АНЖР-1 АНЖР-2 |
Э-08Х25Н60М10Г2 Э-06Х25Н40М7Г2 |
В разделе 5.3 будет показано, почему так трудно (а зачастую невозможно) обеспечить это требование. А невыполнение этого требования ведет к перемешиванию в сварочной ванне большей, чем допустимо, доли «черного» металла с «белым» и, как следствие, образованию мартенсита (см. раздел 5.1 данной статьи) с последующим растрескиванием его в среде, содержащей влажный сероводород.
4. Разработка нормативной документации. По сравнению с ЕЭС России, в которой за последние десятилетия нормативная документация не претерпела никаких изменений, и ОАО «Газпром», где созданная ранее базовая нормативная документация кардинально не менялась, а только добавлялась новая, в нефтехимии дела обстоят прямо противоположно. Основополагающая нормативная документация (НД) по конструированию нефтехимического оборудованию на протяжении последних 8 лет подвергается постоянному реформированию (ведущему зачастую к резкому послаблению устоявшихся за долгие годы ограничений). Так, если в основном рабочем документе по проектированию сварных сосудов и аппаратов ОСТ 26-291–79 для сред, вызывающих сероводородное коррозионное растрескивание, применение двухслойных сталей не допускалось, то в следующих изданиях этого же документа ОСТ 26-291–87 и ОСТ 26291–94 было разрешено применение двухслойных сталей для сред, вызывающих сероводородное коррозионное растрескивание, но при условии высокого отпуска (2 ч при 620…650°С,) сварных швов (см. п. 3.12.5 ОСТ 26-291–94). А вот уже ГОСТ Р 52630–2006, разработанный взамен ОСТ 26-291–94 и вступивший в силу с 2007 г., отменил обязательность выполнения термообработки по признаку коррозионного растрескивания биметалла от воздействия перерабатываемой среды, т.е. какое бы коррозионное растрескивание рабочая среда ни вызывала, термообрабатывать сварные соединения двухслойных сталей не требуется (за исключением сварных соединений биметалла с основным слоем из сталей 12ХМ, 12МХ, 20Х2М). Нет этого требования и в ПБ 03584–03. При этом требование обязательности выполнения термообработки сварных соединений по признаку склонности к коррозионному растрескиванию при изготовлении сосудов из монометаллов осталось неизменным (см. п. 6.11.1 ГОСТ Р52630–2012), хотя вероятность образования трещин в сварных соединениях двухслойных сталей гораздо больше, чем в сварных соединениях монометаллов. Почему в ГОСТ Р52630–2006 и затем в ГОСТ Р52630–2012 биметаллы с основным слоем из перлитной стали, т.е. наиболее применяемые в нефтехимии, попали в опалу? Ведь атомарный водород, образующийся из влажного сероводорода, по-прежнему приводит к разрушению твердых или напряженных участков металла сосудов, в частности зон термического влияния сварных соединений, т.е. физика разрушительного процесса осталась неизменной. Следовательно, в данном случае нормативная документация заведомо ведет к снижению надежности и безопасности сварных соединений двухслойных сталей.
Содержание солей в нефти, поступающей на первичную переработку, мг/л
Обессоленная | 9,17 |
Западно-Сибирская | 32,87 |
Арланская | 65,16 |
Сливная НГДУ ООО «Башнефть Добыча» | 203,58 |
НГДУ «Ишимбайнефть», Приютово | 87,13 |
Такое положение дел следует считать особенно недопустимым, поскольку нефтехимия изначально работает со средами намного более коррозионно-активными, чем, скажем, ЕЭС России, и коррозионная активность этих сред в нефтехимии из года в год только растет. Так, если в 1970–1990-х годах основной объем нефтепереработки приходился на западно-сибирскую нефть (в которой нет сероводорода и небольшое содержание солей) лишь с небольшой добавкой Арланской нефти, то в последнее десятилетие доля Арланской нефти в общем объеме переработки составляет 65–70%, а остальное – нефть Ишимбайская и НГДУ «Башнефть Добыча», которые в значительной мере насыщены солями, как это можно видеть из следующих данных:
Кроме того, в переработку совместно с нефтью начал поступать и газовый конденсат Карачаганакского месторождения, содержащий довольно много хлора, который, согласно литературным источникам, усиливает разрушительное действие сероводорода на металл в 3–3,5 раза.
5. Изготовление. 5.1. Сварка. 5.1.1. Практика эксплуатации нефтехимического оборудования из двухслойных сталей в средах, вызывающих сероводородное коррозионное растрескивание, показывает, что применение этих сталей без термообработки после сварки резко увеличивает аварийность указанного оборудования.
Одной из главных причин этого является образование мартенсита в переходном слое сварного шва из-за высокой доли участия в нем «черной» стали при автоматической сварке [5]. Это обусловлено большим вводом теплоты в ходе процесса сварки (большой ток при малой скорости сварки). Влияние мартенсита проявляется в усилении склонности к растрескиванию при относительно малой нагрузке в результате создания дополнительных внутренних напряжений в самом металле переходного слоя. Скорость образования и последующего развития этих трещин достаточно высока, и поэтому современными диагностическими методами (за исключением АЭ-мониторинга) трещины в подавляющем большинстве случаев при эксплуатации оборудования не выявляются: межремонтный период для большинства нефтехимического оборудования составляет 4 года, а выполнять диагностику на работающем оборудовании недопустимо (согласно требованиям НД). 5.1.2. В нашей стране все сварные швы нормированы соответствующими ГОСТами на их типы, конструктивные элементы и размеры. Однако в ГОСТ 16098–80 на выполнение сварных соединений из двухслойной стали нет ни упоминания о переходном слое, ни обозначения его на эскизах, ни указания на необходимость его выполнения, ни его размеров, ни расположения его относительно основного и плакирующего слоев. Видимо, этот ГОСТ создавался в те времена, когда в выполнении переходного слоя еще не было необходимости, и все сварное соединение двухслойной стали представлялось элементарно простым: черный металл сваривай черным электродом, белый металл – белым. И только в 2003 г. появился ОСТ 26.260.480–2003, в котором впервые прозвучало понятие переходного слоя, являющегося по своей физической и химической сути местом зарождения трещин. От правильности выполнения переходного слоя зависит, возникнут внутри него трещины в процессе эксплуатации во влажном сероводороде или нет. (Скорее всего, основанием для разработки этого ОСТа послужили накопленные данные по выявлению причин разрушений сварных соединений двухслойных сталей, эксплуатировавшихся во влажном сероводороде). Тем не менее, в современных чертежах часто встречается ссылка на ГОСТ 16098–80. И везде, где эта ссылка приводится, приходится заставлять проектанта обозначать переходный слой на чертеже по ОСТ 26.260.480–2003.
Возникают споры из серии «кто главнее»: ГОСТ или ОСТ. Аргументы о том, что ОСТ в данном случае более совершенный, отвергаются, потому что ГОСТ «главнее», у него «папаха» выше: ведь только на ГОСТах, на их первой странице всегда пишется фраза «Несоблюдение стандарта преследуется по закону». В ОСТе этой записи нет, следовательно, он «проигрывает» ГОСТу. Естественно, что наилучшим вариантом в данном случае следует считать отмену устаревшего ГОСТ 16098–80 с заменой его более совершенным ОСТ 26.260.480–2003. Тем более, что в ГОСТ 16098–80 приведены только основные типы, конструктивные элементы и наружные размеры сварных соединений из двухслойных сталей, а в ОСТ 26.260.480–2003, кроме установления размеров переходного слоя, сварных швов, приведены еще и все возможные технологии выполнения сварных соединений с вариантами подбора присадочных проволок, методами контроля, исправления дефектов. 5.1.3. Металл при работе в среде влажного сероводорода насыщается атомарным водородом. Сквозь кристаллическую решетку низкопрочных металлов (Ст.3, Сталь 10, Сталь 20) атомы водорода проходят, а в высокопрочных металлах или в напряженных участках металла они застревают, не имея достаточной энергии, чтобы пройти ее насквозь. Здесь одиночные атомы водорода образуют молекулы (молизуются), т.е. увеличиваются в объеме, что и вызывает трещинообразование металла (кроме этой существует еще три теории, объясняющие растрескивание напряженного металла от воздействия атомарного водорода). А сварные соединения, как указано в начале статьи, отличаются неоднородностью структуры и напряженностью металла. Максимум напряженности приходится на зоны термического влияния сварного соединения, поскольку при остывании расплавленный металл сварного шва уменьшается в объеме и, следовательно, «стягивает» металл зон термического влияния к себе, вызывая в них растягивающие напряжения, называемые остаточными. Именно в этих самых напряженных местах атомы водорода, молизуясь, и вызывают растрескивание. После растрескивания атомарный и молекулярный водород еще в большом количестве остается в металле берегов трещины. И многолетняя практика показывает, что если его не удалить, то при повторной сварке (заварке трещины) он спровоцирует растрескивание, если не сразу после сварки, то в течение некоторого непродолжительного времени.
В разработанном ОАО «ВНИКТИнефтехимоборудование» нормативном документе ОТУ 2–92 была оговорена обязательность обезводороживания перед сваркой кромок металла, работавшего в сероводородсодержащей среде, путем отжига их при температуре 400°С в течение 30 мин. Однако в новой редакции этого же нормативного документа ОТУ3–01 этого требования уже нет.
Хотя на наш запрос ОАО «ВНИКТИнефтехимоборудование» прислало ответ, в котором четко указано, что обезводороживание делать надо. Согласитесь, что очень трудно доказать руководству ремонтируемого объекта необходимость выполнения обезводороживания свариваемых кромок в условиях дефицита времени и финансов, отведенных на проведение ремонта, тем более, что обязательность этого обезводороживания не оговорена в нормативной документации. 5.2. При контроле сварного соединения во время изготовления сосуда гарантированно определить наличие мартенсита в переходном слое сварного шва можно только путем обеспечения эффективного металлографического контроля образцов-свидетелей каждого сварного соединения, выполненного автоматической сваркой. Однако здесь остро встает вопрос идентичности образцов-свидетелей при выполнении автоматической сварки кольцевых сварных соединений. Так, если идентичность образцов-свидетелей продольных сварных соединений можно гарантировать, поскольку каждый образец-свидетель при выполнении автоматической сварки является продолжением шва свариваемого изделия, то при выполнении автоматической сварки кольцевых сварных соединений образец-свидетель не может быть сварен заодно со сварным швом свариваемого изделия, и поэтому идентичность его не гарантируется.
Следовательно, не обеспечивается гарантия отсутствия мартенсита в кольцевых сварных соединениях изделия, выполненных автоматической сваркой.
Контроль по твердости на наличие мартенсита также малоэффективен, так как сварному шву плакирующего слоя принято придавать товарный вид, накладывая на него облицовочный валик. Особенно этот валик стремятся выполнить в тех случаях, когда предыдущий валик (или слой шва) выполнен небрежно и даже с нарушением режима. В этом случае облицовочный валик покрывает собой предыдущий слой шва, в котором могут быть отклонения не только по внешнему виду, но также и по свойствам. Таким образом, полученный уровень твердости на поверхности облицовочного валика не гарантирует такую же твердость в металле переходного слоя сварного шва, из которого и берут свое начало все трещины [6]. Все это искажает истинную картину измерения твердости и затрудняет определение мест возможного трещинообразования в переходном слое сварного шва. Контроль твердости только переходного слоя сразу после его выполнения также не представляется возможным, так как он требует невысокой температуры замеряемой поверхности (5…50°С), что приводит к значительным перерывам в работе при сварке конкретного аппарата. Таким образом, реального надежного способа контроля металла переходного слоя на наличие мартенсита (источника будущих трещин) нет. Тем более, что в нем при сварке и после нее трещин может и не быть: ведь эти трещины в подавляющем большинстве случаев возникают в процессе эксплуатации под воздействием коррозионно-активной среды (например, влажного сероводорода) и распространяются с высокой скоростью. 5.3. При стыковке обечаек и днищ второй причиной высокой доли участия «черной» стали в переходном слое сварного шва, выполненного автоматической сваркой, является разнотолщинность кромок под сварку, овальность и отклонения диаметральных размеров стыкуемых обечаек. Даже в допустимых пределах это в сумме составляет до 2% диаметра, т.е. 30 мм при диаметре 1,5 м (применительно к диаметру взорвавшейся емкости, см. раздел 1), когда «черный» металл одной царги «вынужден» в некоторых зонах частично стыковаться с «белым» (плакирующим слоем) ответной соединяемой царги обечайки с последующей автоматической сваркой по этому месту. Кроме того, толщина днища в месте приварки его к обечайке в большинстве случаев на 10–15% превышает толщину обечайки (днище делают толще из-за опасности утонения его в центральной части во время горячей штамповки), а допуск на гофрирование цилиндрической части днища составляет 4,0…8,0 мм в зависимости от толщины. К тому же согласно ГОСТ 10885–85 [7] неплоскостность на 1 м длины двухслойных листов толщиной 8 и более мм не должна превышать 15 мм, а для листов толщиной менее 8 мм неплоскостность не должна превышать 20 мм. В итоге образуется значительная разнотолщинность кромок под сварку. Условия автоматической сварки требуют совпадения свариваемых кромок по наружной поверхности обечайки (отсюда и центрирование свариваемых обечаек выполняется наружными рольгангами, т.е. по наружной поверхности обечаек), тем самым выводя все несовпадения кромок внутрь аппарата. Таким образом, заведомо обеспечивается ступенька свариваемых кромок изнутри, что приводит к сварке «белого» металла (плакирующий слой) одной свариваемой царги с «черным» металлом (основной слой) другой, чем нарушается требования (см. также п. 6.1.12 [5]) по выполнению переходного шва. Это ведет к значительному повышению доли участия «черного» металла в сварном шве переходного слоя и, как следствие, к образованию мартенсита и последующему неизбежному растрескиванию сварного соединения при эксплуатации во влажном сероводороде. Так, для взорвавшейся емкости, оговоренной в разделе 1, согласно диаграмме Шеффлера–Шнейдера и данным табл. 1, допустимая доля участия черного металла в переходном слое сварного шва не должна превышать 30%, тогда как фактически в разрушенном сварном шве она составила 45%.
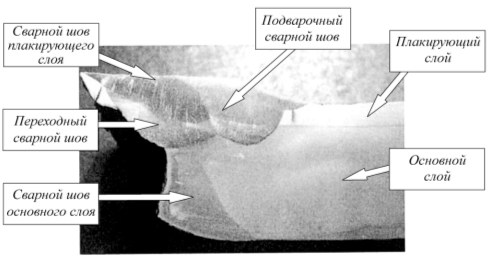
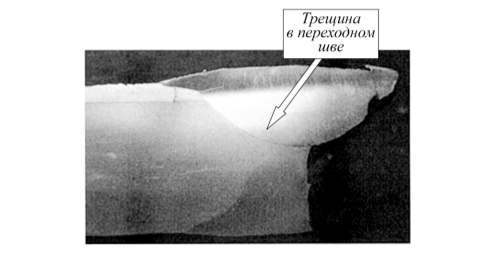
По этой причине сварной шов на взорвавшейся емкости разрушился после 17 месяцев с начала ее эксплуатации (рис. 2, 3) при гарантированном безаварийном сроке эксплуатации 20 лет. 5.4. Образование мартенсита в сварном шве неминуемо ведет к растрескиванию, особенно при эксплуатации в среде, содержащей влажный сероводород. Скорость развития этих трещин и расслоений достаточно высока (от недель до нескольких лет). Влияние мартенсита проявляется в усилении склонности к растрескиванию при относительно малой нагрузке. Это обусловлено следующим:
- созданием дополнительных внутренних напряжений в металле, поскольку мартенсит имеет объемно-центрированную решетку (занимающую сравнительно большой объем) в отличие от окружающей его перлитной структуры, имеющей гранецентрированную решетку (занимающую меньший объем);
- остроигольчатой структурой зерен мартенсита и, как следствие, высокой степенью анизотропии механических свойств, т.е. в разных направлениях свойства мартенсита сильно отличаются (в направлении длины зерен прочностные свойства высокие, в поперечном направлении – минимальные);
- высокой твердостью (до 400…430 НВ) и, как следствие, недостаточной пластичностью зерен мартенсита.
При термообработке, которой до выхода в свет ГОСТР 52630–2006 обязательно после сварки подвергали все сварные соединения биметаллов, предназначенные для работы в средах, вызывающих коррозионное растрескивание (согласно требованиям ОСТ 26-291–94), в сварных соединениях происходили следующие физические процессы, благотворно сказывающиеся в процессе последующей эксплуатации:
- остаточные сварочные напряжения, возникшие при усадке расплавленного металла, наибольший объем которого имеет место при автоматической сварке, снимались (точнее, сглаживались пики за счет перераспределения эпюры);
- мартенситные зерна, подвергнутые термообработке по режиму высокого отпуска, получали по своему периметру бейнитную оторочку, которая играла роль демпфера (пружинистый смягчитель) при распределении внешних нагрузок;
- сами мартенситные зерна, представляющие остроигольчатую структуру, после этой термообработки приобретали округлости по своим острым краям, что повышало стойкость сварного соединения против трещинообразования и также благоприятно сказывалось при распределении внешних нагрузок;
- ферритные структуры с относительно мелкими равномерно распределенными сфероидальными карбидами, образующимися после отпуска мартенсита, обладали наибольшей стойкостью в сероводородсодержащих средах.
Таким образом, применение термообработки аппаратов для получения отпущенного мартенсита в переходном слое сварного шва значительно снижает вероятность образования трещин при работе в средах, вызывающих сероводородное коррозионное растрескивание. Как показывает практика, сварное соединение, облагороженное четырьмя перечисленными физическими процессами, происходящими при термообработке, может благополучно работать в сероводородсодержащих средах долгие годы.
Таблица 2
Сталь |
Температура, °С |
|||||||
100 | 200 | 300 | 400 | 500 | 600 | 700 | 800 | |
08Х13 | 10,5 | 11,1 | 11,4 | 11,8 | 12,1 | 12,3 | 12,5 | 12,5 |
12МХ | 11,2 | 12,5 | 12,7 | 12,9 | 13,2 | 13,5 | – | – |
12ХМ | 11,9 | 12,5 | 13,1 | 13,6 | 14,0 | 14,4 | – | – |
20ХМ | 11,9 | 12,6 | 13,2 | 13,7 | 14,0 | 14,3 | – | – |
Ст3сп5 | 11,9 | 12,5 | 13,1 | 13,6 | 14,0 | 14,4 | – | – |
09Г2С | 11,9 | 12,5 | 13,1 | 13,6 | 14,0 | 14,4 | – | – |
16ГС | 11,1 | 12,1 | 12,9 | 13,5 | 13,9 | 14,1 | – | – |
12Х18Н9Т | 16,6 | 17,0 | 17,6 | 18,0 | 18,3 | 18,6 | 18,9 | 19,3 |
Таким образом, нормативная документация до 2007 г. соответствовала требованиям, обусловленным физикой металлов. С начала 2007 г. все изменилось: если стандарт [5] (п. 11.2) однозначно указывал на необходимость термообработки сварных соединений любых двухслойных сталей в соответствии с требованиями стандарта [3], то в стандарте [9], отменившем стандарт [3], это требование отсутствует (см. п. 6.11.5 [9], который отменил п. 6.11.1 «г», т.е. требование термообработки после сварки сосудам, предназначенным для эксплуатации в средах, вызывающих коррозионное растрескивание).
Отсутствует оно и в документе [2]. Создается двойственное положение: ОСТ [5] требует проведения термообработки, ссылаясь на отмененный норматив [3], а нормативы [9] и [2] разрешают не выполнять термообработку сварных соединений из двухслойных сталей, предназначенных для работы в средах, вызывающих коррозионное растрескивание.
Во многом отказ от термообработки сварных соединений двухслойных сталей, видимо, можно объяснить бытующим на машиностроительных заводах мнением о том, что во время термообработки из-за разности коэффициентов термического расширения между «черной» и «белой» сталями возникают дополнительные напряжения в сварном соединении. Фактических данных о величине возникающих остаточных напряжений в сварных соединениях двухслойных сталей в литературе ([10] и др.) нет, и кроме «теоретизирования» и фантазирования это мнение ничем не подтверждается. Мало того, есть доказательство обратного: так, согласно требованиям современной нормативной документации (ГОСТ Р 52630–2006, ГОСТ Р52630–12 и др.) двухслойные стали с основным слоем из сталей 12МХ, 12ХМ, 20Х2М после сварки должны подвергаться термообработке в обязательном порядке независимо от диаметра и толщины стенки сосуда (из-за склонности этих сталей к подкаливанию), а термообработка остальных двухслойных сталей (с основным слоем из Ст3, 09Г2С, 16ГС и других неподкаливающихся сталей) после сварки не требуется. Авторами проведен анализ коэффициентов термического расширения в двухслойных сталях с основными слоями как из сталей12МХ, 12ХМ, 20ХМ, так и из сталей Ст3, 09Г2С, 16ГС, который показывает (табл. 2), что они практически ничем не отличаются. Отсюда вытекает вывод о том, что термообработка двухслойных сталей с основным слоем из углеродистой или низколегированной стали (Ст.3, 09Г2С, 16ГС и т.д.) также допустима, поскольку разница в коэффициентах термического расширения у них по сравнению со сталями 12МХ, 12ХМ, 20ХМ практически отсутствует, следовательно, во время термообработки в них будут возникать одинаковые остаточные напряжения. Но обязательность термообработки этих неподкаливающихся сталей по признаку коррозионного растрескивания в действующей нормативной документацией снята с 2007 г. и снятие этой обязательности в ГОСТ Р 52630–2006 и ГОСТ Р52630–12 ничем не обосновано. А вот термообработка двухслойных сталей по признаку стойкости против межкристаллитной коррозии оставлена (см. п. 4.11.6 ПБ 03-584–03, п. 6.11.5 ГОСТ Р52630–2012), хотя разрушения по этому признаку встречаются во много раз реже, чем по признаку коррозионного растрескивания.
6. Монтаж. Как следует из официальных документов, в нефтепродукте, проходящем по монтируемому трубопроводу, сероводорода достаточно много, но влаги нет абсолютно (ни паров, ни конденсата). И эта ситуация также была представлена в письме НПЗ на разработку сварочной технологии. Получалось, что абсолютно сухой сероводород не должен подвергаться диссоциации и, следовательно, не будет вызывать расслоения и коррозионного растрескивания металла трубопровода. Значит, термообработку сварных стыков можно не делать.
Пришлось искать истину в институте, выполнявшем технологическую схему проекта установки. Оказалось, что кроме генеральной схемы, где продукт движется по трубопроводу, есть еще, как минимум, два обходных пути (байпасные), проходя по которым, продукт с сухим сероводородом может насыщаться и парами воды, и водяным конденсатом в большом количестве. Следовательно, сероводородное растрескивание по околошовным зонам сварных швов возникнет неизбежно, если их оставить без термообработки. Ведь для сероводорода нет разницы, откуда напитаться влагой: из трубопровода генеральной схемы движения продукта или из байпасной.
Спрашивается: на что ориентироваться сварщику при решении вопроса с термообработкой сварных соединений?
На генеральную схему, зафиксированную в паспорте, техническом регламенте, письме и других официальных документах, или на фактическое состояние дел, т.е. наличие влажного сероводорода. Поэтому, чтобы избежать ошибки, приходится чуть ли не овладевать профессией разведчика и окольными путями выведывать истинное состояние дел.
7. Ремонт. 7.1. Циклон из стали 09Г2С + 08Х13 был изготовлен без термообработки сварных соединений, хотя перерабатываемый продукт содержал влажный сероводород, и термообработка их при изготовлении согласно действовавшему в то время ОСТ 26-291–94 (по признаку коррозионной активности среды, вызывающей коррозионное растрескивание металла в эксплуатации) должна была выполняться обязательно. За несколько лет эксплуатации циклона было три его возгорания, и всякий раз источником протечки продукта была трещина в зоне термического влияния сварного соединения.
После каждого пожара циклон подваривали в месте растрескивания в соответствии с технологической картой на сварку. Термообработку подваренного шва в технологию не закладывали, поскольку в паспорте нет отметки, что циклон при изготовлении подвергался термообработке.
После третьего пожара к вопросу безопасности при эксплуатации циклона была подключена исследовательская организация. Выяснилось, что в графе «рабочая среда» в паспорте циклона было написано «фракция №1», которая никоим образом не отвечала на вопрос, есть ли в продукте среда, вызывающая коррозионное растрескивание.
Так, в п. 2.12 ОСТ 26-291–94, по которому был изготовлен циклон, записано: «При выборе материалов для изготовления сосудов (сборочных единиц, деталей) должны учитываться: расчетное давление, температура стенки (минимальная отрицательная и максимальная расчетная), химический состав и характер среды, технологические свойства и коррозионная стойкость материалов». Таким образом, конструктором не были установлены «химический состав и характер среды», требуемые п. 2.12 ОСТ 26-291–94. Отсюда все и «покатилось»: не зная, этих свойств, он не заложил термообработку сварных соединений, а инженер-сварщик, который писал технологическую карту на подварку циклона после первого и второго пожаров, тоже не предусмотрел термообработку сварных соединений, поскольку циклон при изготовлении не подвергался термообработке (согласно записи в паспорте). Сварное соединение, выполненное в полном соответствии с требованиями нормативной документации (т.е. термообработанное после сварки), при дальнейшей эксплуатации в течение 10 лет не разрушалось. 7.2. При длительной эксплуатации аппаратов из двухслойных сталей в средах, содержащих влажный сероводород, происходит деградация их плакирующего слоя в местах сварки, приводящая к сквозной коррозии корпусов и протечке перерабатываемого продукта. Ремонт таких мест выполняют путем вварки латки в основной металл или наплавки основного металла с последующей вставкой латки из коррозионно-стойкой стали и обваркой ее по периметру (без последующей термообработки). Так вот, коррозионное растрескивание сварного шва вварки латки плакирующего слоя происходит уже через один–два года от начала ее эксплуатации после ремонта. Этот факт лишний раз подтверждает целесообразность выполнения термообработки сварных соединений двухслойных сталей с целью предотвращения их растрескивания. При этом растрескивание может происходить и без воздействия влажного сероводорода. Так, п. 6.1.1. ОСТ 26.260.480–2003 гласит: «Если при сварке основного слоя происходит одновременное плавление металла плакирующего слоя, то возможно существенное понижение пластичности сварного соединения, повышение его твердости и даже образование трещин». Естественно, что растрескивание происходит из-за высокого уровня остаточных напряжений в зонах термического влияния сварного соединения, которые снимаются термообработкой.
8. Эксплуатация. 8.1. Наложение остаточных напряжений (например, сварочных, деформационных и др.) на рабочие приводит к увеличению действующих в материале конструкции общих напряжений, а повышение уровня макронапряжений вызывает уменьшение стойкости материалов в сероводородсодержащей среде. Релаксация поля микронапряжений может происходить путем перераспределения микродеформаций. Однако в средах, вызывающих коррозионное растрескивание, релаксация реализуется за счет образования трещин. Локальная концентрация микронапряжений способствует повышению поглощения водорода металлом и приводит к образованию микротрещин, которые впоследствии распространяются посредством серии химико-механических процессов. Приведем примеры некоторых инцидентов, произошедших с нетермообработанными сосудами из биметалла под воздействием влажного сероводорода. 30 апреля 1972 г. емкость из биметалла (16ГС + 10Х17Н13М2Т без термообработки сварных соединений) взорвалась на газовом заводе г. Оренбурга. Погибло 7 человек (вся антикоррозионная лаборатория). После этого поставили емкость из термообработанного после сварки монометалла (сталь 16ГС), и проблем с ней не было. 2 января 1987 г. взорвался теплообменник на гелиевом заводе г. Оренбурга также из биметалла и также без термообработки сварных соединений. Жертв и пострадавших не было. После этого поставили теплообменник из монометалла, термообработанного после сварки, и проблем с ним не было.
В ноябре 2005 г. произошла разгерметизация емкости 50 м3 (сталь 09Г2С + 08Х13 без термообработки сварных соединений) для хранения пропановой фракции и утечка этой фракции из-за образования сквозной трещины по продольному сварному шву длиной 150 мм снаружи и 700 мм по внутренней поверхности царги.
Обошлось без возгорания. По этой причине данную емкость и еще одну аналогичную ей с трещинами по околошовным зонам сварных соединений вывели из эксплуатации в январе 2006 г. (при этом две такие же емкости остались в эксплуатации, поскольку АЭ-контроль, выполненный в ноябре 2005 г., показал допустимость их дальнейшей эксплуатации). 7 февраля 2006 г. взорвалась аналогичная емкость для хранения пропановой фракции. За 2 ч 35 мин 22 пожарных машины затушили пожар.
Постоянно выявляется растрескивание сварных соединений биметаллов атмосферно-вакуумной трубчатки, но из-за низкого давления 0,07…0,1 МПа взрывов не бывает, хотя пожары случаются.
В ходе образования и распространения коррозионных трещин важную роль играют не только остаточные и рабочие макронапряжения, но и микронапряжения, к которым приводят пластическая деформация, фазовые превращения, микроструктурная неоднородность, дефекты, неравномерный нагрев при эксплуатации и другие факторы. Эти напряжения вызываются скоплениями дислокаций, границами сброса и наклона, возникающими при обработке металла, двойниками деформации и другими дефектными конфигурациями, которые появляются при бездиффузионных сдвиговых превращениях.
Микронапряжения уравновешиваются в объемах единичных кристаллитов или их частей. Возникновению их способствует значительная величина скрытой энергии деформации, которая может оказаться существенной даже при ранних стадиях образования трещин. Даже если эта энергия не приводит к макроскопическому их распространению, она решающим образом влияет на работоспособность материала. Если в зоне возникновения трещин величина имеющейся энергии превышает ту, которая может быть поглощена материалом, то следует ожидать образования и распространения трещины.
Релаксация поля микронапряжений может происходить путем перераспределения микродеформаций. Однако в средах, вызывающих коррозионное растрескивание, релаксация реализуется за счет образования трещин: локальная концентрация микронапряжений способствует повышению поглощения водорода металлом и приводит к образованию микротрещин, которые впоследствии с высокой скоростью распространяются посредством серии химико-механических процессов.
Одна из вероятных причин зарождения трещин в металлах, работающих во влажном сероводороде, – заметное уменьшение истинного значения разрывного напряжения, отмечающегося для сталей, насыщенных водородом. Проникающий в сталь водород вызывает снижение пластичности металла пропорционально его концентрации в стали. После снижения пластичности до указанного минимального значения начинается рост всех зародившихся микротрещин и микродеформаций.
При этом в более мягких сталях для наступления этого момента требуется большая потеря пластичности, чем в более прочных сталях, поскольку в мягких сталях отношение истинного разрывного напряжения к истинному пределу текучести имеет большую величину, чем в более прочных сталях. 8.2. Отсутствие в паспортах сосудов и аппаратов записей об изменениях коррозионной активности перерабатываемого продукта на протяжении жизни сосуда вводит в заблуждение экспертов при выполнении экспертизы промышленной безопасности. В качестве примера следует привести следующий показательный случай.
При экспертизе промышленной безопасности колонны, проработавшей более 55 лет, в справке об ее фактическом технологическом режиме работы, выданной НПЗ, было записано: «сероводорода нет». В паспорте колонны в графе «коррозионная активность перерабатываемой среды» еще перед запуском колонны в эксплуатацию было написано «среда слабокоррозионная, скорость коррозии менее 0,1 мм/год». Поскольку значительных коррозионных поражений при выборочной толщинометрии выявлено не было, эксперт назначил продолжительность остаточного ресурса 8 лет. При последующей эксплуатации колонны в течение 1,2 года корпус колонны дал течь в двух местах по признакам коррозионного растрескивания металла. Из расспросов «старожила», проработавшего на этом производстве около 40 лет, было выяснено, что данная колонна подвергалась значительным воздействиям влажного сероводорода на протяжении значительного времени (десятки лет), но в паспорте отметок об этом не делалось. За 1–2 года перед экспертизой промышленной безопасности колонны подаваемый в нее продукт стали очищать от сероводорода, в связи с чем в справке о фактическом технологическом режиме работы было указано, что сероводорода в перерабатываемом продукте нет. Фактически получилось так, что только в начале своей жизни и за 1–2 года до экспертизы колонна эксплуатировалась без воздействия сероводорода, а середина ее жизни прошла под мощным воздействием сероводорода, что и привело к накоплению повреждающих факторов в металле ее корпуса.
9. Экспертиза промышленной безопасности.
В серо-водородсодержащих средах помимо повышенной общей и язвенной коррозии металла сосуда могут происходить коррозионное растрескивание и расслоение металла, вызванные водородом, образующимся в результате электрохимических процессов (диссоциация) на поверхности стали при участии сероводорода и влаги.
В отличие от хлоридного коррозионного растрескивания, которое начинается с поверхности, сероводородное растрескивание под напряжением (СРН) и расслоение начинаются внутри металла, вдали от поверхности – в переходном слое сварного шва.
Наиболее часто СРН наблюдается в зонах термического влияния сварного шва при рН водной фазы < 5, в наиболее опасном интервале температур 30…40°С.
Кроме того, склонность к СРН определяется особенностью структуры самого металла: наличием структурных неоднородностей (особенно мартенсита), количеством и распределением неметаллических включений, химическим составом, зонами напряженности металла.
Сероводородное расслоение (СР) металла проявляется в образовании трещин в направлении прокатки стали даже при отсутствии внешних напряжений.
Обычно вследствие этого возникает расслоение металла и образуются «пузыри» на поверхности. Иногда трещины распространяются ступеньками – такой вид растрескивания называют ступенчатым растрескиванием, инициированным водородом. Скорость образования и последующего развития этих трещин достаточно высока, поэтому трещины в подавляющем большинстве случаев не выявляются диагностикой при эксплуатации оборудования.
Для проведения диагностирования сосудов по признаку сероводородной коррозии нормативная документация рекомендует использовать «Методику диагностирования технического состояния сосудов и аппаратов, эксплуатирующихся в сероводородсодержащих средах», утвержденную Минтопэнерго России 30.11.93 г. и согласованную с Ростехнадзором [11]. Предписываемая ею организация контроля с наружной стороны металла сосудов традиционными видами и методами контроля (твердометрия, цветная дефектоскопия, ультразвуковой, магнитно-порошковый контроль и др.) по выявлению зарождающихся трещин в процессе эксплуатации неэффективна, поскольку место их зарождения – переходный слой сварного шва (см. рис. 1), расположение которого максимально приближено к внутренней поверхности (плакирующему слою). С внутренней стороны сосуд можно контролировать только в моменты ремонта, да и то только в доступных местах. Видимо, есть только один надежный выход – это АЭ-мониторинг. Только этот метод может гарантированно и своевременно выявлять начальные фазы растрескивания, возникающего в металле в процессе эксплуатации под воздействием влажного сероводорода. Но охватить каждую единицу нефтехимического оборудования АЭ-мониторингом в процессе эксплуатации – это очень дорогое «удовольствие».
А устоявшаяся практика выполнения АЭ-контроля только во время экспертизы промышленной безопасности сосуда или даже во время его плановых ремонтов (т.е. один раз в четыре года) – слишком рискованное мероприятие. Например, трещины, приведшие к взрыву емкости с пропановой фракцией, спустя 17 месяцев после начала ее эксплуатации, развивались очень быстро: АЭ-контроль этой емкости, проведенный за 2 месяца до ее разрушения, показал допустимость ее дальнейшей эксплуатации.
Таким образом, ситуацию, когда нормативная документация не обязывает термообрабатывать сварные соединения сосудов из двухслойных сталей по признаку коррозионного трещинообразования, а они по физическим причинам без термообработки не могут выдерживать длительной эксплуатации без растрескивания, следует считать патовой. И выход из нее только один: вернуть в нормативную документацию требование об обязательности высокого отпуска сварных соединений двухслойных сталей, предназначенных для эксплуатации в средах, вызывающих коррозионное растрескивание, либо отказаться от двухслойных сталей, предназначенных для эксплуатации в указанных средах.
Список литературы
- ГОСТ Р 15.201–2000. Продукция производственного назначения. Порядок разработки и постановки продукции на производство.
- ПБ 03-584–03. Правила проектирования, изготовления и приемки сосудов и аппаратов стальных сварных.
- ОСТ 26-291–94. Отраслевой стандарт. Сосуды и аппараты стальные сварные. Общие технические условия.
- РД 03-485–02. Положение о порядке выдачи разрешений на применение технических устройств на опасных производственных объектах.
- ОСТ 26.260.480–2003. Отраслевой стандарт. Сосуды и аппараты из двухслойных сталей. Сварка и наплавка.
- Кириличев Н.В., Арчаков С.В., Кононов П.А., Никулина Т.С. Некоторые особенности технической экспертизы сварного корпусного оборудования из двухслойных сталей для продления срока службы Волгоград: ОАО «ВНИКТИнефтехимоборудование». 2008.
- ГОСТ 10885–85. Сталь листовая горячекатаная двухслойная коррозионно-стойкая. Технические условия».
- ПНАЭ Г-7-002–86. Нормы расчета на прочность оборудования и трубопроводов атомных энергетических установок.
- ГОСТ Р52630–2012. Сосуды и аппараты стальные сварные. Общие технические условия.
- Чаев А.М., Кириличев Н.В., Едигаров В.С. Сварка разнородных сталей при ремонте нефтеперерабатывающего и нефтехимического оборудования. Обзорная информация. Вып. 6. М.: 1989г.
- Методика диагностирования технического состояния сосудов и аппаратов, эксплуатирующихся в сероводородсодержащих средах. Утв. Минтопэнерго России 30.11.93 г. и согл. с Госгортехнадзором России.