Авторы: Д.В. Рубцов, Д.С. Ланько (ЗАО «ЛОТОС»).
Опубликовано в журнале Химическая техника №5/2016
Как решить одно уравнение с двумя неизвестными?
Задача подобной сложности возникла при разработке испарителя кубовой жидкости в составе установки вакуумной ректификации. Эта установка получения пара-третбутилфенола (ПТБФ) построена и запущена в 2015 г. в рамках увеличения мощности производства ПТБФ-2000 в АО «Новокуйбышевская нефтехимическая компания».
Сов-местными усилиями специалистов ЗАО «ЛОТОС» и АО «Новокуйбышевская нефтехимическая компания» была расширена область исследования, определены дополнительные граничные условия, и указанная задача была успешно решена.
Сложность разработки определялась особенностями физической картины процесса, объединяющего взаимодействие ректификационной колонны (с ее периферией) и кубового испарителя.
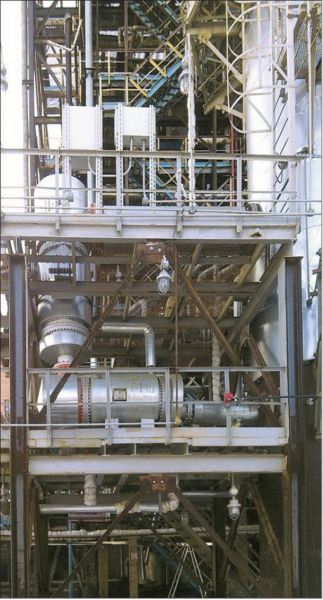
При ограниченном давлении греющего водяного пара до 1,6 МПа (температура насыщения 202,6°С) и при проектной температуре кипения кубовой жидкости на уровне 180°С (рабочее давление – 0,0133 МПа) кипение кубового продукта осложнено соизмеримостью рабочего давления в колонне с гидростатическим давлением в кубе, что препятствует кипению в нижних слоях жидкости на входе в трубный пучок. Это влияние тем сильнее, чем длиннее трубный пучок вертикального испарителя.
В этом случае кипение начинается ближе к выходу из трубчатки, когда влияние гидростатического столба ослабевает, и температура насыщения продукта опускается ниже температуры источника теплоты.
До настоящего момента широкое практическое применение получили два основных конструктивных решения подвода теплоты в цикл вакуумной ректификации при получении ПТБФ:
- испарение в термосифонных аппаратах, где движение кубовой жидкости через испаритель осуществляется посредством разницы давления гидростатического столба кубовой жидкости и веса парожидкостной смеси в трубчатке теплообменника;
- испарение в роторно-пленочном испарителе [1], куда жидкость подается насосом в верхнюю часть аппарата на орошение трубчатки, при котором исключается дифференциальное влияние гидростатического столба на смещение равновесия пар-жидкость.
Оба решения имеют свои преимущества и недостатки:
- термосифонный испаритель не требует внешних источников давления на жидкость для ее принудительной подачи в аппарат, но не имеет возможности комплексного функционирования, при котором обеспечиваются высокая кратность циркуляции и требуемая тепловая нагрузка;
- роторно-пластинчатый испаритель обеспечивает в совокупности высокие показатели кратности циркуляции и тепловой нагрузки, однако используемые насосы не способны надежно работать в части уплотнительных устройств и устранить риск полимеризации ПТБФ при контакте с окружающей средой.
Учитывая изложенные факты, перед специалистами ЗАО «ЛОТОС» была поставлена следующая задача: разработать и поставить термосифонный испаритель с повышенной кратностью циркуляции для обеспечения тепловой нагрузки до 0,94 МВт в условиях вакуумной ректификации ПТБФ.
При этом должны быть решены следующие задачи:
- обеспечение максимального перегрева кубовой жидкости перед кипением в верхних слоях трубчатки;
- использование эффекта объемного кипения продукта с одновременным подводом теплоты от греющего пара;
- интенсификация конденсации греющего пара в кожухе аппарата;
- экономия пара посредством использования теплоты охлаждения конденсата;
- обеспечение необходимой и достаточной кратности циркуляции кубовой жидкости через испаритель;
- упрощение механизма управления работой испарителя и стабилизация технологического режима.
Основным приемом решения поставленных задач в данном случае является применение нестандартного подхода к аппаратурному оформлению, позволяющему искать оптимумы вне области параметров, продиктованных известными конструкциями испарителей.
В ходе вариационных расчетов разработан комплексаппарат, обеспечивающий в первой секции перегрев кубовой жидкости на 18,5°С относительно температуры куба в 180°С (на практике со 155,4°С).
В этом процессе осуществляется подвод теплоты в количестве ~0,36 МВт при теплопередаче порядка 700 Вт/(м2⋅К). Эта теплота аккумулируется в перегретой жидкости за счет кратности циркуляции на уровне 8,4 единицы, когда 7,4 единицы потока – циркулирующая жидкость без фазового преобразования.
В стандартном вертикальном испарителе площадь живого сечения трубчатки постоянна и в лучшем случае оптимизирована для потока в точке выхода из пучка, когда в зоне подачи жидкости режим течения ламинарный со всеми вытекающими следствиями, включая практическую неработоспособность теплообменной поверхности в нижних уровнях трубного пучка термосифонного испарителя.
В зоне отсутствия подвода теплоты от греющего пара между секциями аппарата на практике выявлено снижение температуры, что обусловлено объемным кипением из-за ранее аккумулированной теплоты в первой секции при снижении полного давления в рассматриваемом объеме. Высотный уровень канала между секциями аппарата определен вариационно. На этом участке достигалось выполнение условия практического выравнивания температуры потока и температуры горячего источника, а также контролировалось насыщение жидкости, подготовленной к активному объемному кипению.
Здесь не происходит интенсивного кипения из-за малого числа центров кипения на поверхности нержавеющих тянутых трубок и высокой скорости потока [2].
При вхождении потока в следующую секцию насыщенная жидкость кипит в объеме и получает через теплообменную стенку теплоту греющего пара. В таком режиме процесс кипения углеводородов отличается повышенной интенсивностью. На входном срезе трубчатки данной секции поток имеет уже существенную долю пара, и скорость его достаточно высока вплоть до выхода из аппарата. Это минимизирует количество участков с пленочным и пробковым кипением.
Достижение описанных эффектов невозможно без организации высокоинтенсивного процесса конденсации греющего пара и охлаждения его конденсата. Особенности интенсификации конденсации за счет перевода процесса в капельный режим описаны в статье [3]. Рациональное распределение и организация потока водяного пара обеспечивают высокий тепловой поток к кипящей среде, определяя интенсивность процесса кипения (по уравнению Г.Н. Кружилина).
Предметом оптимизации комплекс-аппарата также стало обеспечение высокой кратности циркуляции как фактора, влияющего на чистоту кубового остатка, снижающего нагрузку на тарелки колонны, а также минимизирующего интенсивность образования полимерных, коксовых и других отложений в трубах. Оптимизацию конструкции в этой части также производили вариационно.
Здесь учитывали площадь живого сечения пучка, диаметр трубок, длину каналов, высоту гидравлического столба, физические свойства среды, гидравлическое сопротивление и многое другое.
Для надежной, эффективной и устойчивой работы испарителя рекомендовано управление работой аппарата посредством регулировки расхода отводимого парового конденсата при полностью открытой задвижке паропровода [4], что обеспечивает стабильный подвод теплоты, отсутствие гидроударов, экономию пара, исключает необходимость в конденсатоотводчиках и обеспечивает плавность регулирования работы всей системы.
В середине февраля 2016 г. были сняты характеристики испарителя в рабочих условиях. По показаниям пирометра температура на штуцерах отвода конденсата практически равнялась температуре штуцера подвода кубовой жидкости, что говорит о затоплении избыточной для рабочего режима поверхности. При расходе пара 1 350 кг/ч и его температуре на входе и выходе соответственно 222,2 и 156°С (рабочее давление 1,526 МПа) тепловая нагрузка составила ~0,82 МВт, что близко к проектным значениям. Очевидно и большее значение тепловой нагрузки, что подтверждается практически нулевой недорекуперацией конденсата и кубовой жидкости.
При этом экономия греющего пара составила примерно 9,4%, а время выхода на рабочий режим сократилось на 4 ч благодаря высокой эффективности совокупной работы подогревающей ступени испарителя и ступени объемного кипения.
В результате наблюдений за работой аппарата подтверждены принятые при разработке устройства допущения для процесса кипения в кубовых испарителях при вакуумной ректификации. Эти допущения предусматривают перегрев жидкости с дальнейшим ее объемным кипением в условиях изменения параметров фазового равновесия в многокомпонентных смесях, движущихся в сложных каналах испарителя (комплекс-аппарата), для условий малых температурных напоров между источником теплоты и продуктом.
Список литературы
- Патент RU №2502718. Способ получения пара-третбутилфенола и устройство для его осуществления
- Байдаков В.Г. Перегерев криогенных жидкостей. Екатеринбург: УрО РАН, 1995.
- Шершевский А.Г., Рубцов Д.В. Конденсация под контролем LOTUS//Химическая техника. 2010. №10.
- Рубцов Д.В., Терентьев С.Л., Карпов Д.Н. Испарители типа LOTUS® как средство управления ректификацией//Химическая техника. 2014. №8.