Автор: Т.Д. Алеференко, М.А. Квантов, А.Г. Александров, Е.А. Садовский (ООО «НПО ЛЕНКОР-НЕФТЕХИМ»).
Опубликовано в журнале Химическая техника №3/2016
В настоящее время на нефтеперерабатывающих заводах в эксплуатации находится определенное количество импортного оборудования и оборудования, изготовленного из сталей импортного производства. При проведении экспертизы промышленной безопасности такого оборудования, работающего в водородсодержащих средах, в некоторых случаях оказывается, что материальное оформление оборудования с учетом условий эксплуатации не соответствует рекомендациям ныне действующих нормативных документов.
В частности, это касается хромомолибденовой стали A387 Gr11 Cl1 (отечественный аналог – сталь 12ХМ).
Хромомолибденовая сталь 12ХМ – теплоустойчивая сталь с рекомендованной температурой эксплуатации до 560 °С [1]. Однако в водородосодержащих средах максимально допустимая температура эксплуатации такой стали заметно ниже и уменьшается с ростом парциального давления водорода [2].
Для реакторов риформинга DR – 311…314, изготовленных из стали A387 Gr11 Cl1 фирмой Construction Metalliques de Provence (Франция) в 1979 г. (входят в состав комплекса по производству ароматических углеводородов), расчетная температура составляет 543 °С, температура эксплуатации – 525 °С при давлении среды около 1 МПа. В то же время согласно [2–4] максимально допустимая температура применения сталей типа 12ХМ, 15ХМ в водородсодержащих средах при таких условиях составляет 475 °С.
Исследование образцов, вырезанных из стенки одного из упомянутых реакторов после эксплуатации в течение 200 000 ч, выявило существенные изменения металла в тонком слое (~ 0,4…0,6 мм) с внутренней поверхности корпуса реактора: зафиксировано снижение содержания углерода (примерно вдвое по сравнению с содержанием углерода в наружной поверхности реактора), снижение твердости и появление повреждений в виде пор и микротрещин в слое толщиной 0,1…0,3 мм.
Наличие обезуглероженного слоя с внутренней поверхности реактора означает, что начался процесс водородного разрушения стали. Кинетика водородной коррозии характеризуется двумя параметрами: индукционным периодом, в течение которого она никак себя не проявляет, и скоростью водородной коррозии после окончания индукционного периода [2]. К сожалению, для сталей типа 12ХМ, 15ХМ отсутствуют надежные данные по кинетике водородной коррозии. Установленный факт наличия результатов водородной коррозии (обезуглероженного слоя) на внутренней поверхности аппарата свидетельствует о том, что индукционный период водородной коррозии для сталей типа 12ХМ, 15ХМ при температуре эксплуатации 525 °С меньше 200 000 ч. Но для прогнозирования ситуации и оценки остаточного ресурса оборудования нужно знать еще и скорость развития этого процесса.
Для стали 12ХМ в указанных условиях эксплуатации характерна и тепловая деградация – значения длительной прочности, используемые в прочностном расчете при оценке остаточного ресурса оборудования, заметно снижаются при достижении времени эксплуатации 300 000 ч.
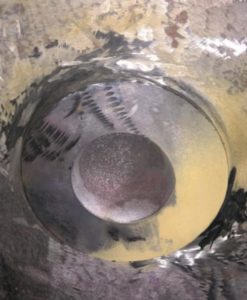
а – вид изнутри; б – вид снаружи аппарата
При таком времени эксплуатации расчетное значение толщины стенки для вышеупомянутых реакторов практически совпадает с фактическим. С учетом наличия обезуглероженного слоя оборудование формально следует выводить из эксплуатации. В то же время известно, что нормативные значения длительной прочности представляют собой достаточно консервативную оценку, фактические прочностные свойства металла конкретного аппарата могут оказаться заметно выше.
Для решения вопросов подобного рода актуальным для оборудования из стали A387 Gr11 Cl1 становится проведение лабораторных исследований длительной прочности и водородной коррозии на вырезанных из действующего оборудования образцах металла. Технология вырезки темплетов диаметром 100 мм и последующей заделки образовавшегося отверстия заглушкой известна и приведена в нормативной документации [5]. В настоящее время появился определенный опыт применения этой технологии, усовершенствованы некоторые ее аспекты. Внешний вид отремонтированного места после вырезки темплета приведен на рисунке.
Имеется положительный опыт длительной эксплуатации оборудования с такими заглушками в ОАО «Уфанефтехим» с 2007 г., на Омском НПЗ – с 2008 г.
Из темплета диаметром 100 мм изготавливаются образцы для механических испытаний на длительную прочность и для металлографических исследований (водородная коррозия). Методики проведения ускоренных испытаний на длительную прочность при нескольких температурах позволяют ограничиться небольшим числом образцов (12) и сократить время испытаний до 3…4 мес.
В зависимости от толщины стенки аппарата может потребоваться 1…2 темплета.
Исследование структуры металла такого темплета позволяет оценить глубину ослабленного водородной коррозией слоя металла.
Анализ результатов исследования двух механизмов ослабления металла (тепловая деградация и водородная коррозия) позволяет оценить вклад каждого и корректно рассчитать остаточный ресурс металла оборудования для обоснованного планирования его замены.
Список литературы
- ГОСТ Р 52630–2012. Сосуды и аппараты стальные сварные. Приложение А.
- СА 03-005–07. Технологические трубопроводы нефтеперерабатывающей, нефтехимической и химической промышленности. Требования к устройству и эксплуатации.
- Арчаков Ю.И. Водородоустойчивость стали. М.: Металлургия, 1978.
- Сосуды и трубопроводы высокого давления. Справочник/Под ред. Е.Р. Хисматулина и др. М.: Машиностроение, 1990.
- ТУ–Регламент по эксплуатации и обследованию оборудования установок каталитического риформинга и гидроочистки, работающих в водородсодержащих средах при повышенных температуре и давлении. СПб, 1998.