Автор: А.И. Швиндин (ООО «Сумский машиностроительный завод»).
Опубликовано в журнале Химическая техника №3/2015
Номенклатура насосного оборудования нефтеперерабатывающих и нефтехимических производств стран СНГ состоит в основном из центробежных насосов – однои двухступенчатых консольных и многоступенчатых двухопорных с выносными опорами. В их числе есть группа насосов, которые применяются в установках первичной переработки нефти, а также в установках термических и термокаталитических процессов для откачивания тяжелых остатков с низа колонны. Во всех перечисленных технологических процессах тяжелым остатком в колонне являются кипящие мазут или гудрон при температуре 360…380°С. При этом рекомендуемое время пребывания мазута в нижней части атмосферной колонны – 5 мин, гудрона внизу вакуумной колонны – 2…5 мин. Исходя из этих рекомендаций, подбираются параметры специальных, так называемых «печных» насосов, которые должны отбирать эти остатки и направлять их или в печь для дальнейшей переработки, или на коксование в установки замедленного коксования [1]. «Печные» насосы, предназначенные для загрузки печей соляровым дистиллятом, мазутом или гудроном температурой до 400°С и давлением до 6,5 МПа, считаются самыми проблемными в нефтепереработке.
Проблема конструирования горячего насоса высокого давления заключается в решении следующих основных задач:
- обеспечение полной герметичности вала и разъемов корпусных деталей;
- обеспечение необходимой прочности и жесткости применяемых конструкционных материалов в условиях высоких температур и давлений, а также их коррозионной и эрозионной стойкости, так как тяжелые остатки богаты сернистыми соединениями и мелкодисперсными абразивными примесями;
- обеспечение температурных расширений роторных и статорных деталей без расцентровки и заедания ротора в корпусе насоса;
- обеспечение высокой ремонтопригодности, так как для демонтажа, ремонта и последующего монтажа насоса в установке отводится от двух до четырех суток [2];
- обеспечение требуемой нормативными документами наработки на отказ и двух-, трехлетнего межремонтного пробега [3].
Обеспечение последнего требования трудно выполнимо, так как насосы, отбирающие тяжелые остатки с низа колонны, работают в предкавитационном или уже в кавитационном режимах. Причиной этому является следующее: эти кипящие остатки находятся под давлением собственных паров, т.е. в состоянии равновесия с давлением паров, поэтому на входе в насос будет только геодезический подпор жидкости в колонне. С учетом возможных потерь во входном трубопроводе и для исключения возможного газообразования в насосе при этих условиях значение геодезического подпора рекомендуется держать в пределах 2,0…2,5 м [2]. Другими словами, эти значения являются кавитационным запасом системы для насоса. Такие значения кавитационного запаса при подачах более 300 м3/ч трудно обеспечить центробежными насосами без специальных мероприятий, и кавитационные явления в какой-то мере всегда присутствуют.
Фундаментальные научные исследования кавитационных явлений в гидромашинах (насосах и гидротурбинах) активно проводились в 50–70-х гг. ХХ века во многих специализированных предприятиях и НИИ бывшего СССР, а также за рубежом. Особое внимание в этих работах уделялось топливным насосам для авиации и космоса, где вопросы кавитации были очень злободневными [4–6].
Было установлено, что характер кавитации зависит от многих факторов, которые зачастую трудно установить.
Существует несколько концепций зарождения и развития кавитации, например, гидродинамическая, термодинамическая, ядерная. И каждая из них как-то обосновывалась и выражалась соответствующими критериями. К концу ХХ века сформировалось общее утверждение, что кавитация является гидродинамическим явлением и зависит как от гидродинамических качеств гидромашины, так и от физических свойств жидкости. Кавитация начинается при падении давления до значения, равного или меньшего упругости пара. Она сопровождается нарушением сплошности потока и образованием пузырьков-каверн, наполненных паром. При попадании каверны в зону повышенного давления пар конденсируется в капельки жидкости, причем конденсация происходит мгновенно. При подобном устремлении массы жидкости с огромным ускорением в смыкающиеся пустоты возникают удары, происходит местное повышение давления в этих точках, достигающее 30 МПа.
Эти удары повторяются десятки тысяч раз в секунду.
В насосе явление кавитации сопровождается шумом, повышенной вибрацией, следствием которой является преждевременный выход из строя торцовых уплотнений и подшипников. Также возможно снижение подачи, напора, мощности и КПД. При длительной работе в кавитационном режиме возможно разрушение поверхностей лопастей рабочего колеса, входного трубопровода, а иногда и стенок отвода.
В результате многих экспериментальных исследований появились объяснения многих кавитационных явлений и процессов, выработаны некоторые рекомендации для практических расчетов и эксплуатации гидромашин.
В частности, кавитационные качества рабочих колес центробежных насосов в 30-х гг. ХХ века проф. С.С. Руднев (НПО «ВНИИГидромаш», Москва) предложил оценивать критерием, названным кавитационным коэффициентом быстроходности Скр, который для практических расчетов приведен к виду
где n – частота вращения, об/мин; Qр – расчетная подача рабочего колеса, м3/ч; Δhкр – критический (3%ный срывной) кавитационный запас рабочего колеса по ГОСТ 6134–2009, м (соответствует NPSHr по ISO 13709:2003/API 610).
Также определились пути и методы устранение вредного воздействия кавитации в центробежных насосах. Они могут быть мероприятиями как относящимися к системе, в которой работает насос, так и конструкторскими решениями в самом насосе. К первым можно отнести увеличение геодезического подпора в колонне и уменьшение гидравлических потерь во входном трубопроводе. Известными конструкторскими решениями являются следующие:
- уменьшение частоты вращения;
- уменьшение расчетной подачи за счет применения рабочего колеса двухстороннего входа;
- специальное проектирование рабочего колеса и профилирование лопасти;
- установка предвлюченного колеса (шнека) перед рабочим колесом;
- в многоступенчатых насосах применение рабочего колеса первой ступени двухстороннего входа.
Все перечисленные решения имеют свои преимущества и недостатки. Например, применение шнеков существенно снижает значения критического кавитационного коэффициента быстроходности. Если для рабочего колеса с коэффициентом быстроходности ns = 80…120 коэффициент Скр = 800…1000, то для шнекоцентробежной ступени такой же быстроходности Скр = 2000…2200. Но шнек по своей гидродинамической природе рассчитывается на очень узкий диапазон подач, и поэтому нормальная работа насоса со шнекоцентробежной ступенью во всем рабочем диапазоне подач не обеспечивается. Применение шнекоценробежных ступеней оправдано, например в энергетических насосах – конденсатных и крупных питательных, которые практически весь ресурс работают на расчетных режимах [7]. В нефтепереработке применяемые насосы подбираются на режим максимально возможной (гипотетически) проектной нагрузки установки, и поэтому они длительное время работают на недогруженных режимах (частичная подача). При работе шнекоцентробежной ступени на частичных подачах в каналах шнека возникают так называемые обратные токи – противотоки, которые существенно изменяют картину течения в шнеке вплоть до образования локальных зон с пониженным давлением и, как следствие, с местной кавитацией в каналах шнека [4]. Самым опасным следствием кавитации в шнеке может быть возникновение пульсаций потока и автоколебаний, которые «раскачивают» всю систему, и этот процесс становится неуправляемым. ООО «СМЗ» в своих разработках конструкций нового поколения нефтяных насосов – консольных и двухопорных [8, 9] – применяет шнекоцентробежные ступени, но с ограничением рабочего диапазона подач в рамках, рекомендуемых стандартом API 610.
Снижение частоты вращения является очень эффективным способом уменьшения воздействия кавитации, но этот способ не всегда оправдан, так как для достижения заданного напора необходимо увеличивать как число ступеней, так и диаметр рабочих колес. Такое решение ведет к существенному ухудшению массогабаритных характеристик насоса, поэтому в каждом конкретном случае требуется оптимизация вариантов.
Более оптимальным решением в высоконапорных многоступенчатых насосах является применение в качестве первой ступени рабочего колеса двухстороннего входа.
Отечественным представителем такой конструкции является нефтяной насос НТ 560/335-300 производства ОАО «Волгограднефтемаш» (рис. 1).
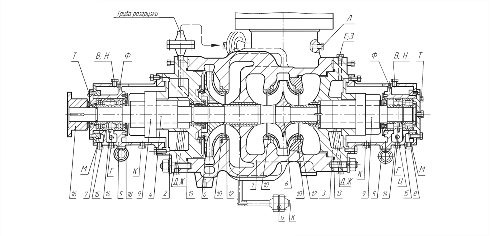
А самым оптимальным решением для такого случая является комбинация двух предшествующих – снижение частоты вращения и применение двухпоточной первой ступени. Такое решение реализовано, например, в двухкорпусных насосах AD L 8″×4 германской компании RUHR PUMPEN (рис. 2) и «Kirloskar 250/200» индийской компании Kirloskar (рис. 3).


Указанные насосы при частоте вращения 1 500 об/мин на подачах 350 м3/ч имеют значения допускаемого кавитационного запаса (Δhдоп, NPSHa) на уровне 2,0 м, что приемлемо для условий «печных» насосов. Усложнение конструкции оправдано обеспечением надежной и долговечной безкавитационной работы.
Следует отметить, что такая конструктивная схема проточной части довольно часто встречается в насосах ведущих компаний мира (рис. 4–6).
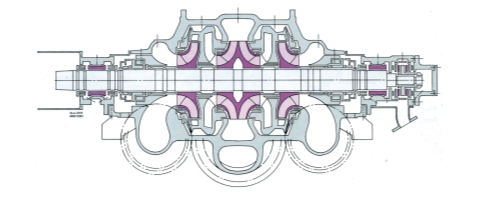
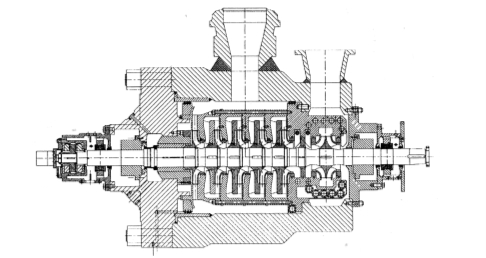
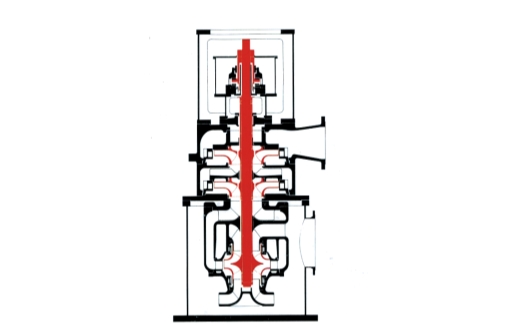
В 70-х гг. ХХ века в ОАО «ВНИИАЭН» был создан конденсатный насос КсВ 200-130, в котором реализованы описанные решения и дополнительно применены предвключенные рабочие колеса (рис. 7), что позволило получить значения NPSHa также на уровне 2,0 м.
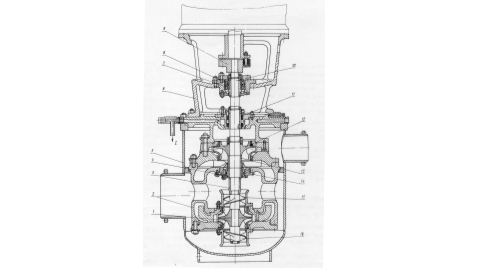
ООО «СМЗ» для аналогичных условий предложил нефтяной двухкорпусный однопоточный четырехступенчатый с предвключенным колесом (шнеком) насос НДМг 360-350 по типу ВВ5 API 610 (рис. 8), который при частоте вращения 1 500 об/мин на подачах 380 м3/ч имеет допускаемый кавитационный запас (Δhдоп, NPSHa) на уровне 2,5 м.
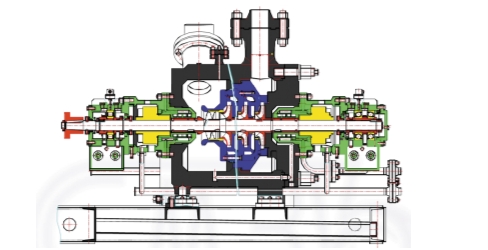
Обобщая приведенную информацию, для условий работы высоконапорных печных насосов с подачами 300…600 м3/ч можно дать следующие рекомендации:
- конструкция насоса должна соответствовать типам ВВ2 или ВВ5 по API 610;
- при применении в конструкции насоса однопоточной схемы проточной части со шнекоцентробежной первой ступенью должно быть оговорено ограничение рабочего диапазона по подаче: 0,7…1,1Qопт (здесь Qопт – режим максимального КПД).
Более перспективной считается конструкция многоступенчатого насоса с рабочим колесом первой ступени двухстороннего входа.
Список литературы
- Справочник нефтепереработчика/Под ред. Ластовкина Г.А., Радченко Е.Д., Рудина М.Г. Л.: Химия, 1986.
- Айзенштейн М.Д. Центробежныенасосы для нефтяной промышленности. М.: ГНТИ нефтяной и горно-топливной литературы, 1957.
- Микерин Б.И. Проблемы системы ППР и ремонтов по техническомусостоянию//Мат. отрасл. совещ. гл. механиков нефтеперерабатывающих и нефтехимическихпредприятий 17 – 21 ноября 2008. Кириши:2009.
- Шапиро А.С. Структура реального течения в центробежных и осевых насосах. М.: МГИУ, 2004.
- Овсянников Б.В., Боровский Б.И. Теория и расчет агрегатов питания жидкостных ракетныхдвигателей. М.: Машиностроение, 1986.
- Степанов А.И. Центробежные и осевые насосы. М.: Машгиз, 1960. 7. Визенков Г., Твердохлеб И., Куценко В., Иванюшин А. и др. Насосы специального и общепромышленного назначения с предвключенными осевыми колесами//Насосы и оборудование. 2008. №3.
- Швиндин А.И. Центробежные насосы для нефтеперерабатывающих и нефтехимических производств. М.: ООО «НТЦ при СГМ», 2012.
- Насосы центробежные и насосные агрегаты на их основе. Каталог продукции ООО «СМЗ». Сумы: 2008.