Автор: Ю.А. Бадьин (ОАО «ВНИКТИнефтехимоборудование»).
Опубликовано в журнале Химическая техника №3/2015
Промышленные трубчатые печи с огневым обогревом являются одним из наиболее нагруженных видов оборудования нефтеперерабатывающих и нефтехимических предприятий. Печное оборудование эксплуатируется в условиях высоких температур и давлений, в нем перерабатываются в больших количествах пожароопасные и взрывоопасные продукты, при этом эксплуатация оборудования проводится в условиях открытого огня.
Аварии на промышленных трубчатых печах практически всегда по характеру развития быстротечны, сопряжены с риском возникновением пожара. Для обеспечения безопасности эксплуатации на всех этапах жизненного цикла промышленных трубчатых печей должны приниматься во внимание все особенности их эксплуатации.
Одной из важнейших особенностей, как показывает практика экспертизы промышленной безопасности трубчатых печей, является фазовая неоднородность нагреваемых сред.
Промышленные трубчатые печи в общем случае могут быть предназначены как для простого нагрева жидких сред, например, в установках атмосферной перегонки нефти, так и для отгона легких фракций, например, на установках вакуумной перегонки тяжелых нефтяных остатков.
Также печи могут использоваться для нагрева с целью проведения нефтехимических процессов, реакций гидроочистки и риформинга бензиновых и дизельных фракций в среде водородсодержащего газа. В последнем случае с самого начала речь идет о наличии двухфазной газожидкостной смеси. Но в процессе нагрева жидкого сырья любого вида происходит не только нагрев жидкости, но и образование паровой (газообразной) фазы.
Это соответствующим образом учитывается при определении тепловой производительности печей в действующих НТД по тепловым расчетам трубчатых печей [1].
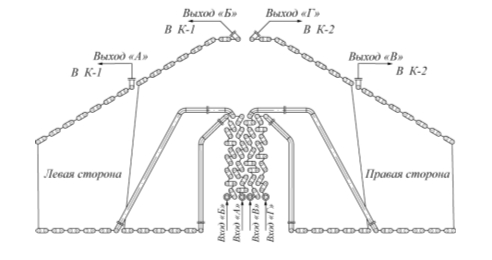
Обычно при проектных расчетах доля отгона принимается на основе технологических расчетов. При этом влияние образования паровой фазы неявным образом учитывается при использовании формул расчета процесса теплообмена, поскольку эти формулы получены на основе статистической обработки большого количества экспериментальных данных. Но при эксплуатации трубчатых печей возможны ситуации, когда образование паровой фазы оказывает дополнительное воздействие на процесс теплообмена и требует учета возникающей фазовой неоднородности нагреваемого продукта. Такая ситуация возможна, например, в случае эксплуатации трубчатых печей, оборудованных подовыми трубными экранами (рис. 1). В данном случае на газофракционирующей установке (блок стабилизации установки каталитического риформинга) производится нагрев сырья (бензин) в печи с целью создания горячей струи во фракционирующих колоннах (левая сторона печи для колонны К-1 и правая сторона для колонны К-2). Тип печи – двускатная шатровая радиантно-конвекционная. Змеевик печи – двухпоточный (по левой и правой стороне печи). Размер труб змеевиков камер радиации и камеры конвекции – ∅152×8. Материал змеевика – сталь 20.
Параметры эксплуатации | Левая сторона | Правая сторона |
Давление, МПа | 1,5 | 0,9 |
Температура, °С: | ||
на перевале печи | Не более 750 | Не более 750 |
на выходе (фактическая) | 225…235 | 190…198 |
Сырье | Бензин | Бензин |
Расход сырья, м3/ч | 114…115 | 90…112 |
Печь эксплуатировалась с 1968 г. Змеевик печи был заменен в 2003 г. До 2010 г. змеевик камеры конвекции был полностью задействован только в правой стороне печи. В 2010 г. проведена реконструкция печи; в рамках ее проведена реконструкция змеевиков с организацией нагрева сырья для левой стороны печи в половине змеевика камере конвекции.
После проведения реконструкции печь запущена в работу. В январе 2014 г. проведена внеочередная остановка печи из-за пропуска продукта в трубе №5 левого подового экрана. По результатам проведенной ревизии на змеевике левого подового экрана и верхнего ряда труб змеевика камеры конвекции выявлено сильное утонение труб в верхней части. Проведена замена смежной трубы №4 и труб верхнего ряда камеры конвекции №4, №5, №6 (причина замен труб – сильное утонение в верхней части труб). Печь запущена в работу. В мае 2014 г. проведена внеочередная остановка печи из-за пропуска продукта в трубе №20 левого подового экрана. По результатам проведенной ревизии проведена замена труб №1, №8, №16 левого подового экрана и трубы №2 верхнего ряда труб змеевика камеры конвекции правой стороны печи и труб №12, №15 подового экрана правой стороны печи. Эксплуатация печи ограничена сроком 3 месяца; в сентябре 2014 г. проведена полная замена змеевиков печи с изменением материального исполнения змеевиков (сталь 15Х5М).
Результаты замеров, сделанных при ревизии (минимальные значения для каждой трубы)
Левый подовый экран
Номер трубы | Толщина трубы, мм | |
Январь 2014 г. | Май 2014 г. | |
1 | 4,2 | 3,5 |
2 | 5,6 | 5,4 |
3 | 5,4 | 5,4 |
4 | 3,5 | 7,7 (новая) |
5 | Пропуск | 8,2 (новая) |
6 | 4,9 | 4,9 |
7 | 4,3 | 4,0 |
8 | 4,2 | 3,5 |
9 | 4,7 | 4,3 |
10 | 5,0 | 5,0 |
11 | 5,4 | 5,2 |
12 | 5,6 | 5,4 |
13 | 4,7 | 4,7 |
14 | 5,5 | 5,2 |
15 | 6,3 | 4,3 |
16 | 4,2 | 3,5 |
17 | 5,2 | 4,9 |
18 | 5,5 | 5,3 |
19 | 4,7 | 4,4 |
20 | 4,2 | Пропуск |
21 | 4,7 | 4,4 |
22 | 6,3 | 6,3 |
Левый потолочный экран
Номер трубы
|
Толщина трубы, мм
|
|
Январь 2014 г. | Май 2014 г. | |
1 | 7,2 | 7,2 |
2 | 6,7 | 6,7 |
3 | 6,4 | 6,4 |
4 | 6,5 | 6,4 |
5 | 7,0 | 6,2 |
6 | 5,9 | 4,7 |
7 | 7,1 | 6,2 |
8 | 6,2 | 4,8 |
9 | 6,9 | 6,8 |
10 | 7,1 | 7,1 |
11 | 7,1 | 7,1 |
12 | 7,4 | 7,4 |
13 | 7,4 | 7,4 |
14 | 7,8 | 7,5 |
15 | 7,2 | 6,4 |
16 | 6,4 | 6,4 |
17 | 6,8 | 6,4 |
18 | 6,4 | 6,4 |
19 | 6,8 | 6,8 |
20 | 7,5 | 7,4 |
21 | 7,5 | 7,4 |
22 | 7,1 | 7,1 |
23 | 7,1 | 7,1 |
24 | 7,4 | 7,2 |
25 | 7,8 | 7,6 |
26 | 7,6 | 7,1 |
27 | 7,1 | 7,1 |
28 | 7,6 | 7,2 |
29 | 7,4 | 7,2 |
30 | 7,4 | 7,3 |
Из анализа проведенных замеров можно сделать следующие выводы:
- на змеевиках печи происходит интенсивное эрозионно-коррозионное изнашивание; рассчитанная максимальная оценка скорости коррозии составляет до 1,5 мм/год;
- наиболее интенсивно эрозионно-коррозионное изнашивание происходит в подовом экране змеевика, где наблюдаются случаи сквозного износа и пропуска продукта.
Таким образом, видно, что сильное утонение труб змеевика ограничивается подовым экраном, хотя в общем случае коррозионный процесс как химическая реакция в значительной степени зависит от температуры и увеличивается по ходу движения среды ближе к концевым трубам змеевика. Все это позволило выдвинуть предположение, что причиной интенсивного изнашивания змеевиков печи является перегрев верхней части труб змеевика вследствие расслоения парожидкостной фазы в трубах змеевика (рис. 2).
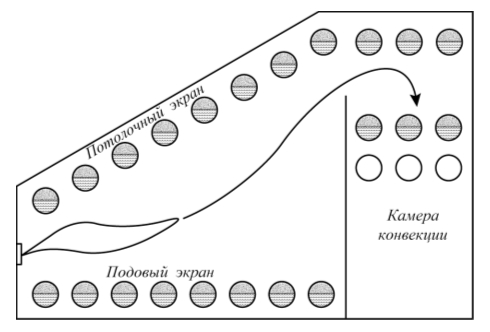
В том случае, если производится нагрев достаточно легкой жидкой среды (например, бензиновых фракций) до температуры, при которой происходит интенсивное образование паровой фазы, возможна следующая ситуация: в подовом экране трубчатого змеевика происходит интенсивное парообразование или в подовый экран уже поступает среда со значительным количеством паровой фазы после нагрева в предыдущей части трубчатого змеевика (например, в змеевике камеры конвекции). Тогда при движении газожидкостной фазы в подовом трубном экране происходит ее расслоение в гравитационном поле и образование газовой «подушки» в верхней части труб. В дальнейшем жидкая и газообразная фазы начинают двигаться раздельно. Трубы подового экрана и верхнего ряда труб змеевика конвекционной части находятся в наиболее неблагоприятном положении, поскольку обращены стороной, занятой паровой (газообразной) фазой, к излучающим факелам горелок и раскаленным дымовым газам топочного пространства печи и подвергаются интенсивному нагреву излучением.
Для труб потолочного экрана процесс расслоения газожидкостной смеси обычно не имеет места, поскольку потолочный экран имеет значительный наклон, и при движении газовой и жидкой фазы вверх по змеевику постоянно происходит их интенсивное перемешивание, и даже в случае расслоения при движении в отдельно взятой трубе змеевика к стороне излучения труба расположена стороной, где находится жидкость, что обеспечивает необходимый процесс охлаждения стенки труб.
Подобный процесс интенсивного перемешивания происходит и в трубах змеевика камеры конвекции. Хотя для верхнего ряда змеевика камеры конвекции такой процесс перемешивания может оказаться недостаточно интенсивным, поскольку трубы верхнего ряда подвергаются сильному нагреву излучением раскаленных дымовых газов на «перевале» печи и нагревом конвективным путем при омывании током раскаленных газов (это составляет особенность конструкции шатровых печей).
Поскольку коэффициент теплоотдачи и теплопередачи к стенке труб со стороны газовой фазы по сравнению с коэффициентом теплоотдачи от стенки труб к жидкой фазе значительно меньше (более чем в 10 раз [2]), общий процесс теплообмена для части наружной поверхности трубы, где находится парообразная фаза, в значительной степени затрудняется. Это вызывает сильный перегрев этой части трубы, что, в свою очередь, вызывает повышенное коррозионное изнашивание изнутри, обгорание снаружи этих частей змеевика, а также деградацию металла труб. Все это может привести к аварии змеевика.
Таким образом, можно сделать вывод, что основной причиной возникновения ситуации повышенного коррозионного изнашивания змеевика подового экрана печи и верхнего ряда труб змеевика камеры конвекции является следующее: при проведении реконструкции, связанной с увеличением площади поверхности змеевиков, не было принято во внимание то, что в трубах змеевика камеры конвекции при нагреве достаточного легкого сырья может начаться интенсивный отгон паровой фазы, и в змеевик подового экрана будет поступать нагретое сырье со значительным количеством пара. В процессе движения парожидкостной среды в горизонтально расположенных трубах происходит расслоение парожидкостной смеси с образованием в верхней части труб пространства, занятого паровой фазой, что приводит к перегреву этой части труб и интенсивному эрозионнокоррозионному изнашиванию.
Дополнительно ситуацию усугубило то, что материальное исполнение змеевика было определено согласно нормам [3] в виде углеродистой стали 20, не рассчитанной на работу в условиях сильного перегрева. Все это привело к тому, что вместо определенной нормами [3] скорости коррозии до 0,3 мм/год фактическая скорость коррозии значительно превысила указанное значение.
Возможным решением проблемы в данном случае могло служить увеличение внутреннего давления в системе змеевиков печи, что снижает общий объем, занимаемый паровой фазой. Но увеличение давления требует повышенных энергетических затрат и в общем случае нежелательно, поскольку увеличивает риск разрыва трубы в ходе эксплуатации с последующей аварией.
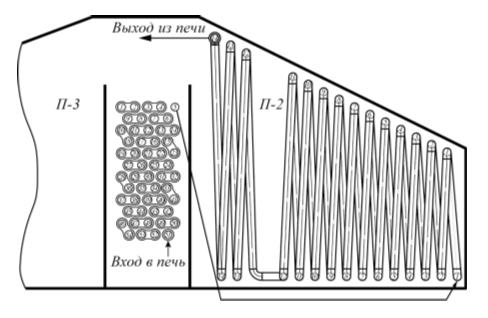
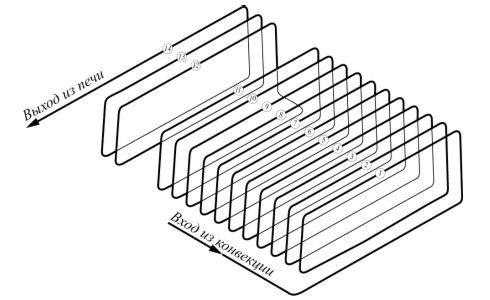
Представляется, что реконструкция змеевиков печи должна была заключаться в установке спиралевидного змеевика в печи (рис. 3, 4). В этом случае попеременное направление продукта в вертикальные трубы способствует интенсивному перемешиванию, так что процесс расслоения может не успевать произойти при движении в отдельной горизонтальной трубе змеевика. Но и в этом случае сохраняется возможность расслоения потока в случае большой доли отгона паровой фазы, большой протяженности горизонтальных труб и при условиях, способствующих процессу отгона паровой фазы, например, при низких значениях внутреннего давления в змеевиках.
Последнее характерно для печей вакуумных блоков отгона легких фракций.
В данном случае на установке АВТ на вакуумном блоке производится нагрев сырья (мазута) в печи с целью создания горячей струи во фракционирующей колонне. Тип печи – коробчатая вертикально-факельная радиантноконвекционная. Змеевик печи – четырехпоточный. Размер труб змеевика камеры радиации – ∅325×16. Материал змеевика – сталь 15Х5М.
Параметры эксплуатации
Давление на входе в печь, МПа | 0,21 |
Температура, °С: | |
на входе/выходе | 345…370/Не более 400 |
на перевале печи | Не более 950 |
Сырье | Мазут |
Расход сырья, т/ч | 100…200 |
Печь выполнена в виде металлического прямоугольного корпуса. Снизу в поду печи расположены горелки.
На боковых панелях закреплен радиантный змеевик.
Конвекционная камера располагается сверху. Сверху печи расположены дымоход для отвода дымовых газов и дымовая труба.
Эксплуатация печи проводилась с 2000 г. По итогам эксплуатации можно сделать вывод, что змеевики камеры радиации не вырабатывают установленный проектный ресурс. В 2009 и 2014 гг. проведена полная замена змеевиков камеры радиации печи. Причина замены – перегрев труб по всей длине, сизый цвет труб в холодном состоянии, толстый (до 5 мм) слой наружной окалины, утонение труб.
Результаты проведенного тепловизионного контроля позволили выдвинуть предположение, что причиной преждевременного износа служит процесс расслоения парожидкостной смеси в змеевиках печи. Расслоение происходит при движении среды по ходу в одной горизонтальной трубе, ближе к ее концу, а также в местах с резким изменением направления потока, что подтверждается результатами тепловизионного контроля (рис. 5).
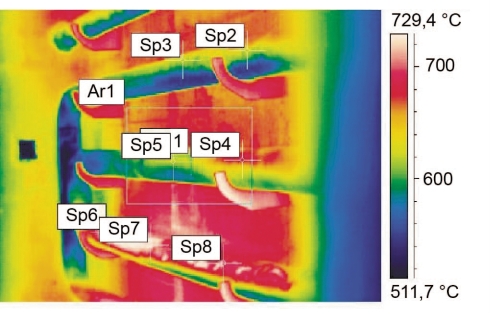
Место проведения тепловизионного контроля и схема потоков камеры радиации печи показаны на рис. 6 для случая, когда тепловизионному контролю подвергались последние по ходу движения среды трубы. В поле зрения прибора находился участок змеевика непосредственно перед выходом труб из камеры радиации. Как видно, расслоение газожидкостной смеси определяется по четкой границе поля распределения температур для горизонтальных труб. Объемную долю отгона продукта можно оценить по распределению температур в выходной трубе змеевика, где четко прослеживается линия раздела фаз; объемная доля отгона продукта в данном случае составляет не менее 0,5 (т.е. паровая фаза занимает 50% внутреннего объема труб). Разница температур в верхней и нижней части горизонтальных труб составляет ~100°С и выше; вертикальные перетоки за счет перемешивания имеют относительно невысокие температуры, равномерно распределенные по поверхности труб.
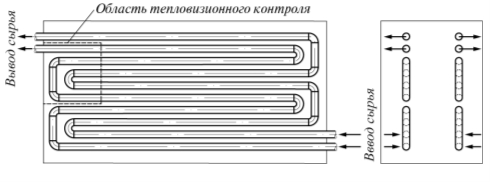
Как сказано ранее, процесс теплообмена с поверхности труб в пространстве, занятом паровой фазой, затрудняется, что приводит к перегреву таких участков.
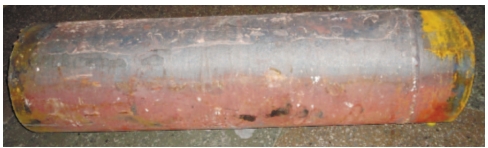
Характерная картина перегрева верхней части труб, соответствующая объему, занятому паровой фазой, представлена на рис. 7, где показан образец для исследования. Верхняя и нижняя часть образца визуально различаются наличием окалины различного цвета. Внизу – плотная окалина темно-бурого цвета, вверху – темносерая окалина толщиной до 5 мм. Различие окалины по цвету и толщине свидетельствует о неравномерном нагреве поверхности трубы в ходе эксплуатации и локальном перегреве до температур выше 700°С. Увеличение наружного диаметра трубы отсутствует. Минимальное значение толщины стенки в нижней зоне составляет 15,6 мм, в верхней – 10,8 мм (при первоначальной толщине 16 мм). Внутренняя поверхность трубы в верхней части покрыта плотными коксовыми отложениями, которые, очевидно, образовывались в ходе эксплуатации в процессе коксования сырья на перегретой поверхности труб. В свою очередь, образование коксовых отложений еще более затрудняет теплообмен и способствует дальнейшему перегреву.
Выполненный комплекс исследований физико-механических свойств металла также подтвердил различие в физико-механических свойствах и структуре металла труб в верхней и нижней половине труб, обусловленное различием фактических рабочих температур в ходе эксплуатации. В целом при наличии структурно-механической неоднородности, оформившейся в ходе эксплуатации, механические свойства металла исследуемого участка трубы не ниже требований НТД на сталь 15Х5М.
Анализ результатов предыдущих ревизий и тепловизионного контроля позволяет сделать вывод, что причиной перегрева труб змеевиков камеры радиации является сочетание ряда неблагоприятных факторов. Малое внутреннее давление, достаточно высокие температуры нагрева сырья обусловливают большой отгон паровой фазы, а горизонтальное расположение труб в камере
Рис. 5. Результаты проведенного тепловизионного контроля радиации приводит к расслоению парожидкостной фазы при движении в трубах с образованием в верхней части труб значительного пространства, занятого паровой фазой (до 50% внутреннего объема труб). Вследствие затрудненного теплосъема в верхней части труб происходит перегрев этих частей труб с высоким эрозионно-коррозионным износом с внутренней стороны труб, обгоранием наружной поверхности труб, образованием коксовых отложений внутри труб. По итогам рассмотрения можно сделать вывод, что перегрев труб приводит к высоким (до 1,5 мм/год) скоростям эрозионно-коррозионного износа стенок труб змеевиков. Таким образом, можно отметить, что применение жаропрочной и жаростойкой стали 15Х5М не предотвратило развитие интенсивного эрозионно-коррозионного процесса в трубах змеевика вследствие перегрева до высоких температур.
Все это приводит к тому, что змеевики камеры радиации не отрабатывают проектный срок службы. Для улучшения условий эксплуатации змеевиков была рекомендована переобвязка змеевиков печи с изменением горизонтального расположения труб вертикальным с уменьшением диаметра труб змеевиков. Такая реконструкция предотвратит процесс расслоения парожидкостной смеси в трубах змеевиков и перегрев труб змеевиков, обеспечит длительную и безаварийную эксплуатацию.
Таким образом, можно сделать вывод, что при конструировании промышленных трубчатых печей для нагрева жидких сред в случае организации движения продукта в змеевиках, собранных из горизонтальных труб, необходимо исключать ситуацию расслоения нагреваемой среды на паровую и жидкую фазы.
Другим случаем иллюстрации необходимости учета фазовой неоднородности нагреваемых сред при конструировании промышленных трубчатых печей являются печи нефтехимических процессов.
В данном случае на установке гидроочистки дизельных топлив производится нагрев газосырьевой смеси в печи для проведения процесса гидроочистки дизельного топлива в среде водородсодержащего газа. Тип печи – коробчатая, вертикально-факельная радиантно-конвекционная. Змеевик печи – четырехпоточный.
Размер труб змеевика камеры радиации и конвекции – ∅152×16мм. Материал змеевика – сталь 08Х18Н10Т.
Параметры эксплуатации
Давление на входе в печь, МПа | 7,7 |
Температура, °С: | |
на входе/выходе | Не более 325/Не более 370 |
на перевале печи | 820 |
Сырье | Дизельное топливо, водо- родсодержащий газ (ВСГ) |
Расход жидкого сырья, т/ч | 40…100 |
Расход ВСГ в тройник смешения, м3/ч | Не менее 29 000 |
Печь выполнена в виде металлического прямоугольного корпуса. Снизу в поду печи расположены три горелки. На боковых панелях закреплен радиантный змеевик. Конвекционная камера располагается сверху.
Сверху печи расположены дымоход для отвода дымовых газов и дымовая труба.
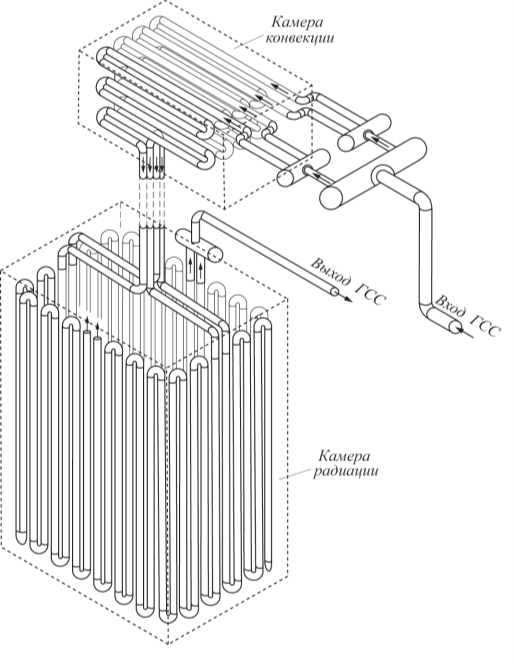
Схема змеевиков печи показана на рис. 8. Газосырьевая смесь (ГСС) после узла смешения жидкой среды и водородсодержащего газа направляется в коллектор диаметром 426×20 мм, далее двумя потоками в трубах диаметром 219×14 мм направляется в коллекторы из труб диаметром 325×16 мм. Из этих коллекторов двумя потоками в трубах диаметром 152×8 мм смесь направляется в камеру конвекции. После прохождения камеры конвекции через перетоки, смонтированные внутри печи, ГСС четырьмя равнозначными потоками направляется в змеевики камеры радиации, а затем через коллекторы в реактор Р-1-201.
Эксплуатация печи проводится с 2006 г. Согласно имеющейся на предприятии документации инцидентов и нарушений режимов эксплуатации не происходило.
В процессе эксплуатации проводились периодические ревизии печи в соответствии с требованиями нормативно-технической документации. Замен элементов змеевиков не производилось.
В 2013 г. произошел разрыв трубы перетока из камеры конвекции в камеру радиации, что привело к возгоранию печи. Схема труб перетока показана на рис. 9, внешний вид аварийной трубы – на рис. 10.
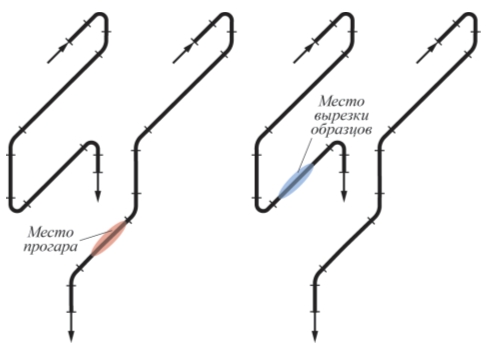
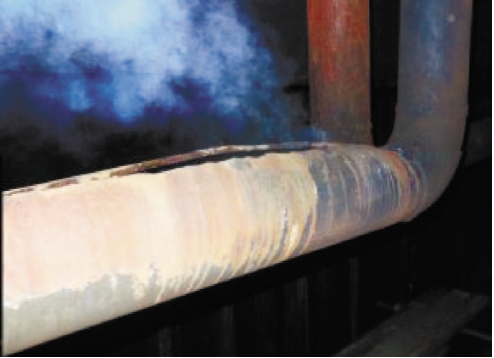
В ходе последующей ревизии был проведен полный комплекс исследований змеевиков печи (наружный и внутренний осмотры, замеры толщин, неразрушающий контроль сварных соединений), исследование физико-механических свойств металла по результатам контрольной вырезки образцов разрушившейся трубы (см. рис. 9) и из других частей змеевика, исследование режимов эксплуатации печи, содержащихся в электронной базе данных.
Характер произошедшего разрушения имеет следующие особенности:
- разрушение произошло в наиболее напряженной части змеевика, где трубы перетоков находятся на пути потока дымовых газов и испытывают всесторонний обогрев; при этом в той части змеевика, которая значительно удалена от выхода из печи (поскольку температура нагреваемой среды должна постепенно повышаться по ходу движения среды, температура в месте разрыва трубы должна была быть значительно ниже, чем на выходе из печи);
- разрушение носило характер продольной трещины, т.е. разрушение происходило в направлении действия максимальных рабочих (окружных) напряжений, при этом зона разрушения ограничена длиной до 600 мм; начало трещины находится на расстоянии около 30 мм от шва приварки отвода к горизонтальной трубе перетока;
- разрушение происходило со стороны противоположной стороне топочного пространства в менее нагретой излучением раскаленных дымовых газов зоне.
Результаты исследований физико-механических свойств металла разрушенного образца выявили в зоне непосредственного разрушения наличие сигма-фазы.
Последнее однозначно свидетельствует о перегреве металла трубы в ходе эксплуатации до высоких температур (600°С и выше). При проведении исследований физикомеханических свойств металла из других частей змеевика (аналогичного места смежного потока и выходной трубы змеевика потока, где произошел разрыв) наличие сигма-фазы не выявлено.
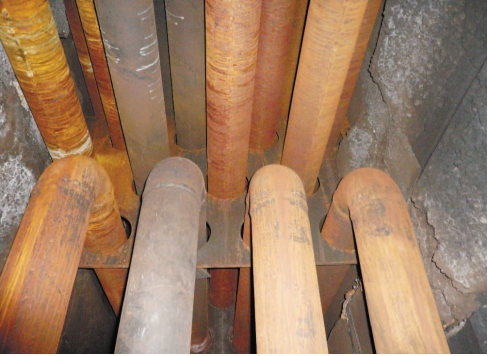
По результатам наружного и внутреннего осмотра печи можно сделать вывод о перегреве потока, на котором произошел разрыв (рис. 11). Наружная поверхность труб и отводов данного потока значительно темнее, чем у остальных потоков, что говорит о значительном перегреве частей змеевика.
Указанные особенности разрушения позволили сделать вывод, что разрушение происходило от действия рабочих нагрузок, но в локальной зоне, где имелся значительный местный перегрев трубы от не предусмотренного проектом сочетания факторов эксплуатации. Это позволило выдвинуть предположение, что основной причиной аварии послужила неравномерность распределения расхода ГСС по потокам печи, что является следствием отсутствия в общем перечне оснащения печи систем противоаварийной защиты системы измерения и контроля равного распределения расходов печи, требуемой согласно п.1 табл. 6.1 «Правил технической эксплуатации трубчатых печей нефтеперерабатывающих и нефтехимических предприятий (Теплотехническая часть). [6]».
Поскольку узел смешения – единый для всех потоков печи, распределение расхода по потокам печи в данном случае не регулируется, в результате такая ситуация могла явиться одной из основных причин, способствующих развитию аварийной ситуации.
Возникшая неравномерность расхода по потокам печи проявилась в недостаточном уровне расхода ГСС по жидкой фазе в одном из потоков печи, в результате эксплуатация печи в течение продолжительного времени происходила с перегревом частей змеевика одного из потоков.
Исследование распределения температуры на момент аварии подтвердили наличие неравномерности распределения расхода по потокам печи. Согласно записям системы автоматического управления установки температура потоков №№1, 2, 4 на выходе из печи на момент аварии находилась в пределах 243…247°С, поток №3 согласно показаниям имел температуру 229°С. Такая относительно низкая температура может говорить о том, что поток №3 имел низкое содержание жидкой фазы, что обусловило затрудненный теплосъем и перегрев стенок элементов змеевика потока.
При уменьшении общей загрузки печи расход в потоке печи с минимальным расходом уменьшился настолько, что это вызвало сильный перегрев в локальных частях змеевика, одним из которых является переток из камеры конвекции в камеру радиации. В месте с резким изменением направления движения потоков наблюдается естественный процесс отбоя жидкой фазы (рис. 12).
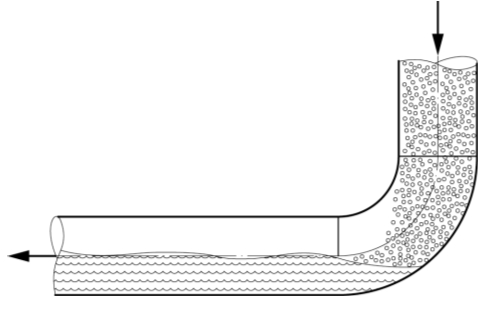
В ситуации малого расхода ГСС в потоке жидкая фаза перераспределяется на нижнюю сторону трубы; в верхней стороне трубы, обтекаемой только газообразной фазой, теплосъем затрудняется, в результате чего наблюдается перегрев верхней зоны трубы. Зона перегрева ограничивается зоной, непосредственно примыкающей к месту резкой перемены направления движения потока. При достаточно высоком нагреве произошло разрушение трубы в виде продольной трещины в перегретой зоне с последующей разгерметизацией змеевика, вызвавшей пожар.
Как следует из изложенного, основной причиной аварийной ситуации явилось недостаточное оснащение печи системами противоаварийной защиты, а также конструкция узла перетоков, смонтированная внутри топочного пространства печи, приводящая к большим тепловым нагрузкам со стороны излучения топочного пространства и конвекционного нагрева поверхностей элементов перетоков от всестороннего омывания раскаленными дымовыми газами.
По итогам обследования были выданы рекомендации по переносу узлов перетоков из топочного пространства наружу печи и по оснащению печи дополнительными системами противоаварийной защиты.
К сожалению, в современных НТД [4, 5], регламентирующих требования к оснащению промышленных печей системами ПАЗ, данное требование по оснащению печей системами контроля равномерности расходов не отражено. В этой связи можно высказать пожелание, чтобы такое требование в них имелось.
Выводы
Обеспечение безопасности промышленных трубчатых печей должно проводиться на различных этапах жизненного цикла оборудования (принятие и обоснование проектных решений, изготовление и монтаж оборудования, контроль его соответствия требованиям соответствующих НТД, контроль состояния оборудования во время эксплуатации и определение его технического состояния, а также оснащение системами противоаварийной защиты, средствами ликвидации аварийных ситуаций и локализации последствий в случае возможных аварий).
Список литературы
- РТМ 26-02-40–77. Нормативная методика теплового расчета трубчатых печей.
- Дытнерский Ю.И. и др. Основные процессы и аппараты химической технологии. М.: Химия, 1991.
- РТМ 26-02-42–76. Методы защиты от коррозии и выбор материалов для основных элементов и узлов аппаратов установок каталитического риформинга
- Общие правила взрывобезопасности для взрывопожароопасных химических, нефтехимических и нефтеперерабатывающих производств. М.: Металлургия, 1988.
- ПБ 09-563–03. Правила промышленной безопасности для нефтеперерабатывающих производств. 6. Правила технической эксплуатации трубчатых печей нефтеперерабатывающих и нефтехимических предприятий (Теплотехническая часть). ТП 01.88.