Автор: Т.В. Мякишев (ООО «ВТМ-Инжиниринг»).
Опубликовано в журнале Химическая техника №11/2014
Группа компаний INTRATOOL представляет специализированный комплекс для автоматизированной очистки нефтяных резервуаров (резервуаров хранения нефти и нефтепродуктов) от донных отложений и остатков нефтепродуктов вместимостью от 100 до 120 000 м3.
Комплекс был разработан по заказу компании ООО «ЭнерДжет Системс», входящей в состав группы компаний, которая с 2003 г. оказывает услуги по комплексной очистке технологического оборудования и нефтяных резервуаров от отложений любой твердости. Проект был реализован в рамках программы группы компаний по использованию оборудования отечественного производства. Разработка проекта и подготовка к производству была осуществлена компанией ООО «ВТМ-Инжиниринг», также входящей в состав группы компаний INTRATOOL.
Комплекс для автоматизированной очистки предназначен для работы в нефтяной и нефтехимической отраслях промышленности, а также на предприятиях транспорта нефти и нефтепродуктов, для железнодорожного, морского и речного транспорта, а также для регенерации и восстановления природной окружающей среды в зонах экологических бедствий.
Уникальность предлагаемого комплекса заключается в его мобильности, энергонезависимости, технологической гибкости, а также в высокой эффективности и производительности. С работой, которую обычно выполняют большие бригады, порой до пятидесяти и более человек, справляются всего два – четыре обученных оператора предлагаемого комплекса. Присутствие человека во вредных и опасных условиях резервуара сведено к минимуму, а в большинстве случаев вообще исключено.
Комплекс максимально автоматизирован, прост в обслуживании и не зависит от внешних источников энергии (ни электроэнергии, ни пара), так как он оснащен собственным дизельным двигателем. Комплекс не только осуществляет высококачественную очистку объектов, но и обеспечивает извлечение полезных продуктов из донных осадков и отложений.
Технология очистки
В зависимости от конкретной задачи в качестве разжижающего агента может быть использована либо вода, либо дизельное топливо или погоны. Использование воды целесообразно в тех случаях, когда в удаляемых шламах уже имеется определенное количество воды (подтоварные воды или вода, проникшая в резервуары через уплотнения в «плавающих крышах»). В этом случае для фазоразделения должна использоваться «трехфазная» центрифуга, что позволит получить «товарный» нефтепродукт, оборотную воду (на рециркуляцию в системе), а также твердую фазу.
В случае очистки резервуаров на нефтеперерабатывающих заводах и при отсутствии на них значительного количества воды более целесообразным является использование в качестве размывающего (разжижающего) агента дизельное топливо или погоны. Это позволит не только увеличить степень извлечения углеводородов, но и получить твердую фазу с меньшим содержанием тяжелых углеводородов за счет их растворения горячим потоком более «легкой» углеводородной фракции.
В этом случае используется «двухфазная» центрифуга для отделения твердой фракции (в основном минерального характера) от жидкой. Полученная в этом случае после центрифугирования жидкая фаза имеет качество не ниже качества печного мазута и может быть либо продана, либо переработана на заводе совместно с исходным углеводородным сырьем – сырой нефтью.
Основные технические характеристики комплекса
Средняя производительность комплекса по донным отложениям, извлекаемым из хранилищ нефти и нефтепродуктов, м3/ч: |
|
с помощью роботизированной пушки | 7,0 |
с помощью шламового экстрактора | 15 |
Расход дизельного топлива на обеспечение работы дизельного двигателя, л/ч: главного процессного модуля (Caterpillar C13) |
18 |
модуля центрифугирования (Caterpillar C9) | 14 |
Средний расход дизельного топлива всего комплекса (главный процессный модуль и модуль центруфугирования) при использовании топочного теплообменника, л/ч |
70 |
Общий объем разжижающего агента в системе, м3 | 27,5 |
Вместимость резервуаров масла в гидроприводных системах, л: |
|
модуля очистки | 680 |
модуля центруфугирования | 680 |
Запас топлива для всего комплекса (объемы топливных баков), л |
2270 + 2270 |
Номинальное значение наружной температуры окружающей среды в режиме нормальной эксплуатации, °С |
–15… +400 |
Технология очистки с использованием дизельного топлива в качестве разжижающего агента
В соответствии с показанной на рис. 1 схемой разжижающий агент (дизтопливо или другой нефтепродукт) объемом 10…15 м3 закачивается в главную процессную емкость комплекса. Операторы заносят в очищаемый резервуар через люк разобранную роботизированную пушку, собирают ее и устанавливают в рабочую позицию.
Далее операторы заносят в этот резервуар через люк бустерный насос и устанавливают его напротив роботизированной пушки. Затем они собирают линии шлангов подачи горячего разжижающего агента на роботизированную пушку и откачивания бустерным насосом разжиженных донных отложений в главную процессную емкость.
После того, как все линии собраны, главный моющий насос начинает подавать разжижающий агент через теплообменник на роботизированную пушку, с помощью которой производится разжижение донных отложений.
Разжиженные отложения откачиваются из резервуара бустерным насосом и поступают в систему рециркуляции разжижающего агента.
Разжиженные осадки поступают в сетчатый вибросепаратор, где от них отделяются твердые частицы размером более 1,2 мм. Далее разжиженные осадки поступают в главную процессную емкость комплекса, где происходит осаждение твердых частиц размером менее 1,2 мм из разжиженного донного осадка и периодическая выгрузка осевшего на дно емкости шлама с помощью шнекового конвейера и грязевого насоса, а разжиженный мазут (или нефть) отводится с помощью плавающего скиммера и комплектующего его насоса в соответствующий сборник (по мере отвода разжиженных донных осадков из процессной емкости последняя должна пополняться пропорциональным количеством «свежего» разжижающего агента).
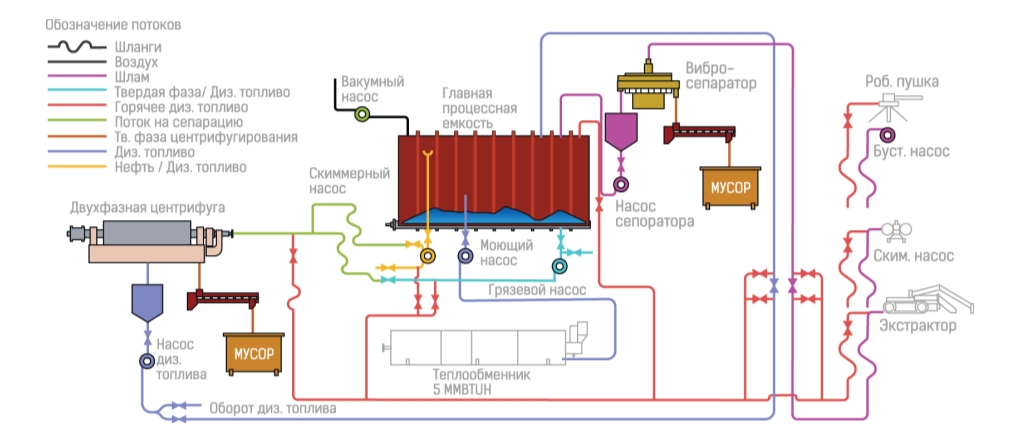
Отсепарированный от твердых частиц рециркулирующий разжижающий агент, выходящий из процессной емкости, подается главным моющим насосом через сетчатый фильтр в теплообменник и далее поступает в роботизированную пушку, установленную внутри очищаемого резервуара. Рециркуляция разжижающего агента производится до полного разжижения всего объема донных отложений.
После извлечения из резервуара основной массы отложений операторы демонтируют роботизированную пушку и эвакуируют ее из резервуара. Затем операторы вносят в резервуар орбитальные моющие головки и монтируют их внутри, распределяя равномерно по его площади. После монтажа орбитальных головок и их подсоединения к шлангам включается подача на них горячего разжижающего агента. Моющий раствор откачивается из резервуара бустерным насосом и подается в систему его рециркуляции. После промывки поверхностей резервуара (при необходимости подготовки резервуара под огневые работы или под хранение светлых продуктов) их ополаскивают горячей водой, после чего орбитальные головки также демонтируются и выносятся из резервуара. После окончания процессов очистки, ополаскивания и проветривания резервуара операторы ручными брандспойтами производят детальную зачистку труднодоступных мест резервуара горячей водой. Удаление воды со дна резервуара осуществляется с помощью технологических шлангов за счет создания вакуума в главной процессной емкости. После завершения финальной зачистки и демонтажа всего очистного оборудования резервуар ставится на естественную осушку.
Технология очистки с использованием воды
Технологию очистки резервуаров с использованием воды иллюстрирует схема, представленная на рис. 2.

До начала процесса извлечения донных осадков из резервуара главная процессная емкость комплекса на 80% объема заполняется водой, которая главным моющим насосом подается в теплообменник, где она нагревается и возвращается в процессную емкость. Такая рециркуляция по малому контуру продолжается до тех пор, пока вода в процессной емкости не достигнет требуемой температуры. После этого нагретая вода начинает циркулировать по большому контуру: процессная емкость – главный моющий насос – теплообменник – роботизированная пушка и бустерный насос, с помощью которого она вместе с размытым пушкой донным осадком из резервуара возвращается назад в процессную емкость, расположенную на расстоянии 100…150 м от резервуара.
Соотношение донный осадок/вода перед откачиванием составляет примерно 1:4. Смесь нефти, воды и твердых частиц, откачиваемая бустерным насосом, при поступлении в комплекс в первую очередь проходит через вибросепаратор, где на сетке отделяются крупные твердые частицы размером более 6 мм, которые удаляются с помощью шнекового конвейера в контейнер для мусора. Прошедшая через вибросепаратор смесь поступает в главную процессную емкость.
Поступившая в процессную емкость смесь под действием силы тяжести проходит первичное фазоразделение: на дне осаждаются твердые частицы, легкие нефтяные углеводороды всплывают, а в средней части емкости собирается осветленная вода. Эта вода забирается главным моющим насосом и циркулирует по большому контуру.
Всплывшая в главной процессной емкости нефтяная фракция собирается с помощью плавающего скиммерного механизма и скиммерным насосом подается на центрифугу, при этом к нефти добавляется также донный осадок из процессной емкости, откачиваемый грязевым насосом. Содержание воды в нефтяной «фазе», удаляемой из процессной емкости, составляет 10…15% мас.
Перед поступлением этой смеси на центрифугу в нее добавляется горячая вода для улучшения процесса сепарации. Для улучшения процесса фазоразделения в линию подачи этой смеси может инжектироваться полимерный флокулянт. При поступлении потока в центрифугу происходит его фазоразделение в поле центробежных сил с ускорением ~3100 g.
Более тяжелые, чем жидкие, твердые частицы отбрасываются центробежными силами к стенке вращающегося ротора центрифуги. Перемещение твердой фазы к выгружному отверстию, а через него – в приемный сборник твердой фазы центрифуги производится посредством шнека, вращающегося внутри ротора центрифуги со скоростью на 1,5–2,0% меньшей скорости вращения ротора, что достигается с помощью дифференциального редуктора. Из приемного сборника твердая фаза выгружается шнековым конвейером в контейнер для последующего обезвреживания или захоронения.
Вода, содержащая суммарно до 1,5% мас. нефтяной «фазы» и твердых частиц, выводится из центрифуги в приемную емкость, откуда она насосом перекачивается в процессную емкость комплекса и начинает циркулировать в системе по большому контуру.
Поскольку количество воды в системе растет за счет поступления содержащейся в донном осадке очищаемого резервуара избыточной «подтоварной» воды, последняя сбрасывается насосом из приемной емкости центрифуги на очистные сооружения или в отстойные емкости.
Нефтяная «фаза», выделенная в процессе центрифугирования, выходит из центрифуги самотеком и под действием силы тяжести сливается в приемную емкость, откуда насосом откачивается в сборники заказчика для последующего использования или продажи.
Суммарное содержание воды и твердых частиц в нефтяной «фазе» центрифугирования обычно составляет не более 5,0 % мас. без применения химических реагентов, а с применением химических реагентов – 1,5– 2,0% мас. Твердая фаза центрифугирования содержит суммарно до 50% мас. воды и жидких углеводородов.