Автор: Д.С. Москаленко, В.С. Татаринов, А.Н. Боровков, Д.А. Пестов (ООО «ХЁРБИГЕР»).
Опубликовано в журнале Химическая техника №11/2014
Четырехрядные оппозитные поршневые компрессоры типа 4М16М производства Сумского НПО им. М.В. Фрунзе широко распространены на нефтехимических предприятиях России и СНГ. По данным компании HOERBIGER, в эксплуатации находится по меньшей мере 70 таких машин, большая часть из которых была произведена во времена СССР. Компрессоры применяются для сжатия и обеспечения циркуляции водородсодержащего газа (ВСГ) и водорода, поэтому к их надежности предъявляются очень высокие требования: компрессоры должны быть не только безопасными, но и иметь высокий коэффициент готовности, поскольку каждый внеплановый останов машины дорого обходится собственникам предприятия.
Узлы и детали | B | A |
1. Приводной двигатель | ||
2. Система охлаждения и смазки | ||
3. Клапаны | ||
4. Цилиндры и поршни | ||
5. Поршневые и опорные кольца | ||
6. Штоки | ||
7. Газовые сальники | ||
8. Маслосъемные сальники | ||
9. Группа движения (коленчатый вал, шатуны, крейцкопфы) | ||
10. Подшипники шатунных и коренных шеек коленчатого вала |
Отчет о проведении технического аудита:
B – состояние компонент до его проведения; А – после проведения аудита; n – «Хорошо»/«Удовлетворительно»; n – требует дополнительных действий; n – обнаружены проблемы
За годы эксплуатации каждое эксплуатирующее предприятие выработало собственную стратегию обслуживания компрессоров, обеспечивая попеременную эксплуатацию машин, своевременное техническое обслуживание и наличие необходимых запасных частей на складе. Зачастую оказывается проще и быстрее изготавливать мелкие изнашивающие детали, например поршневые кольца, по месту из закупаемых оптом материалов, чем применять специализированные изделия компанийизготовителей. К сожалению, из-за нестабильности качества материала и отсутствия серийного производства качество изготавливаемых по месту уплотнительных материалов варьируется. В свою очередь, это негативно сказывается на продолжительности межремонтного пробега компрессоров, при этом самым худшим является не сама периодичность остановов, а неравномерное изнашивание узлов машины. Если компрессор не оборудован системой мониторинга состояния, то практически невозможно предсказать, в каком из цилиндров в первую очередь выйдут из строя поршневые кольца или сальники.
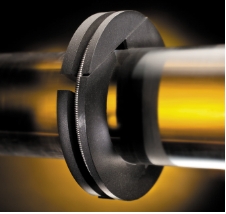
С целью систематизирования сведений о наработке критичных узлов конкретных машин, разработки корректирующих мер и тем самым облегчения эксплуатации компрессоров компания HOERBIGER разработала систему аудита компрессорного парка REE-аудит. При проведении REE-аудита проводится всестороннее обследование компрессора, изучение реальных условий эксплуатации и проверка их соответствия проектным параметрам.
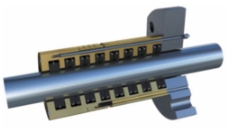
Результатом аудита является REE-отчет, в котором перечислены конкретные технические меры по повышению надежности, энергоэффективности и экологической безопасности каждой обследованной машины. Затем проводится модернизация компрессора.
Один из проектов модернизации компрессора 4М16М-45-35/55, используемого для сжатия ВСГ в установке получения бензола, был проведен компаниейHOERBIGER на одном из предприятий в Нижегородской области, входящих в нефтехимический холдинг «СИБУР».
Компрессор 4М16М-45-35/55 до проведения модернизации имел смазываемые цилиндры, средний расход масла составлял 15 л/день, что более чем в 3 раза выше нормы по регламенту. Техническое обслуживание компрессора проводилось в соответствии с ОТУ–85, но при этом при каждом плановом останове полностью заменялись поршневые кольца, кольца газовых сальников и маслосъемников. Заказчика не устраивало такое быстрое изнашивание уплотнительных элементов и связанный с этим перерасход средств на закупку запасных частей.
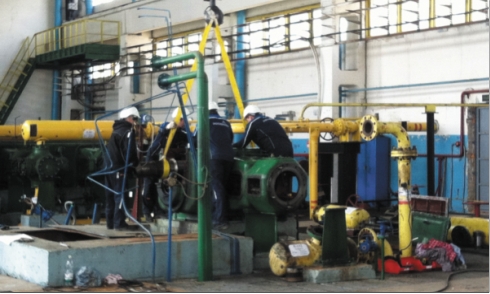
В ходе проведения REE-аудита специалистами компании HOERBIGER был обнаружен неравномерный износ поршневых колец и внутренних поверхностей цилиндров, износ сальников и маслосъемников, скопление масла в корпусах уплотнений. Конструкция системы смазки предусматривала подачу масла в две точки на цилиндре, смазка сальника осуществлялась по остаточному принципу маслом, выходящим из цилиндра. Часто изнашивались баббитовые башмаки на поршнях.
Для сокращения расходов на смазочные материалы и повышения надежности машины было предложено провести модернизацию компрессора с переводом на мини-смазку. Перевод компрессора на бессмазочный («сухой») режим работы оказался нецелесообразным, поскольку потребовалось бы применить дорогостоящие синтетические уплотнительные материалы, осуществлять контроль температуры на каждой ступени и даже вносить изменения в процедуру пуска компрессора.
Кроме того, конструкция компрессора 4М16М-45-35/55 имеет ограничения, препятствующие переводу на сухой режим: расстояние между фланцами уплотнительных узлов меньше хода поршня, а кинематика сопряжения поршень–гильза не позволяет разместить достаточное для надежного уплотнения цилиндра число колец на поршне. Таким образом, целевой показатель безостановочной работы компрессора в 8000 ч оказался бы труднодостижимым. Проведенное технико-экономическое обоснование для компрессора 4М16М-45-35/55 на мини-смазке показало возможность экономии до 3000 л масла в год и повышения коэффициента готовности машины.
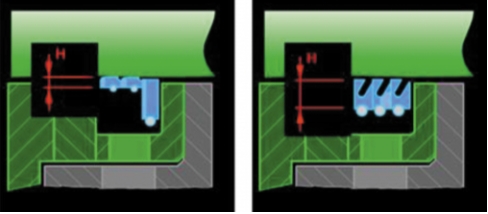
и сальник традиционной конструкции (б)
В ходе выполнения проекта специалистами компанииHOERBIGER были проведены следующие работы: восстановление цилиндров, проектирование новых поршней вместе с компрессионными и опорными кольцами из высокотехнологичных полимеров, изготовление новых штоков и модернизация соединения шток–поршень, модернизация системы смазки, применение неохлаждаемых сальников, применение уплотняющих маслосъемников.
Применение поршней новой конструкции позволило в качестве материала опорных колец выбрать специальную марку полимерного композита HY-54, который имеет повышенную нагрузочную способность и низкий коэффициент трения. Соединение шток–поршень выполнено с помощью гайки «Superbolt» с предварительным натяжителем резьбы, которая позволяет надежно фиксировать детали друг относительно друга. Новые штоки имеют необходимые для работы полимерных уплотнительных колец шероховатость и твердость поверхности.
Поверхность штоков упрочнена карбидом вольфрама, нанесенным методом высокоскоростного газопламенного напыления (HVOF). По сравнению с азотированием методHVOF обеспечивает более высокую поверхностную твердость деталей, отсутствие деформации деталей после обработки, повышение предела выносливости с увеличением износостойкости обработанных деталей. Кроме того, газоплазменное напыление HVOF ведется при низкой температуре, благодаря чему отсутствуют структурные изменения в обрабатываемых деталях.
Газовый сальник выполнен в неохлаждаемом патронном корпусе типа Thermosleeve. Теплоотвод в таком сальнике достигается за счет применения проводящих мостиков, которые передают тепло через корпусные детали компрессора к рубашке охлаждения. Не требуется подключение сальника к контуру охлаждения. Уплотнительные кольца – сегментные сбалансированные кольцаBCD, которые отличаются более плотным прилеганием к штоку и при этом меньше подвержены естественному изнашиванию, чем распространенные радиально-тангенциальные уплотнительные пары. Отдельный штуцер подачи масла в сальник обеспечивает комфортные условия работы уплотнения и практически полное отсутствие износа.
В маслосъемном узле применен сальник ОТ, сочетающий в себе уплотнение и набор скребковых колец.
Маслосъемник ОТ исключает попадание картерного масла в дистанционный фонарь и полностью разделяет контуры смазки цилиндров и группы движения.
Изменение режима работы системы смазки позволило оптимально распределить точки ввода смазки и настроить лубрикатор соответствующим образом.
В итоге проведенных работ компрессор 4М16М-4535/55 достиг требуемых показателей надежности:
- фактическая экономия компрессорного масла составила 3300 л в год;
- замена поршневых и сальниковых колец производится по их фактическому состоянию. Проведенная плановая инспекция подтвердила, что срок их непрерывной эксплуатации превышает 8000 ч;
- внеплановых остановов, вызванных изнашиванием поршневых и сальниковых колец, с 2011 г. не зарегистрировано.
По итогам выполненного проекта был заключен договор с компанией HOERBIGER на модернизацию других компрессоров парка ОАО «СИБУР холдинг».