Автор: А.А. Дубов (ООО «Энергодиагностика»).
Опубликовано в журнале Химическая техника №4/2016
В настоящее время при оценке рисков в эксплуатации опасных производственных объектов (ОПО) в основном используют детерминированный подход. Оценку вероятности аварийных ситуаций осуществляют на основе имеющейся статистики повреждений, которая накопилась за прошедший период эксплуатации ОПО. Такой подход несовершенен и недостаточно объективен, так как оценка рисков делается на будущий период времени, когда техническое состояние ОПО может существенно измениться, и усталостные повреждения отдельных узлов оборудования могут произойти (и, как правило, происходят) в тех зонах, которые не совпадают с расчетными.
Известно, что основными источниками повреждений оборудования и конструкций являются зоны концентрации напряжений (ЗКН), в которых процессы коррозии, усталости и ползучести металла развиваются наиболее интенсивно. ЗКН – это не только заранее известные области, где особенности конструкции создают различные условия для распределения напряжений, создаваемых внешней рабочей нагрузкой, но и случайно расположенные области, где в силу начальной неоднородности структуры металла в сочетании с нерасчетными дополнительными рабочими нагрузками возникли большие деформации.
В 2008 г. опубликован ГОСТ Р 53006–2008 «Оценка ресурса потенциально опасных объектов на основе экспресс-методов. Общие требования», рекомендации именно этого стандарта направлены на реализацию объективного подхода при оценке ресурса и рисков ОПО.
На рис. 1 представлена структурная схема определения остаточного ресурса оборудования с использованием экспресс-методов неразрушающего контроля (НК).
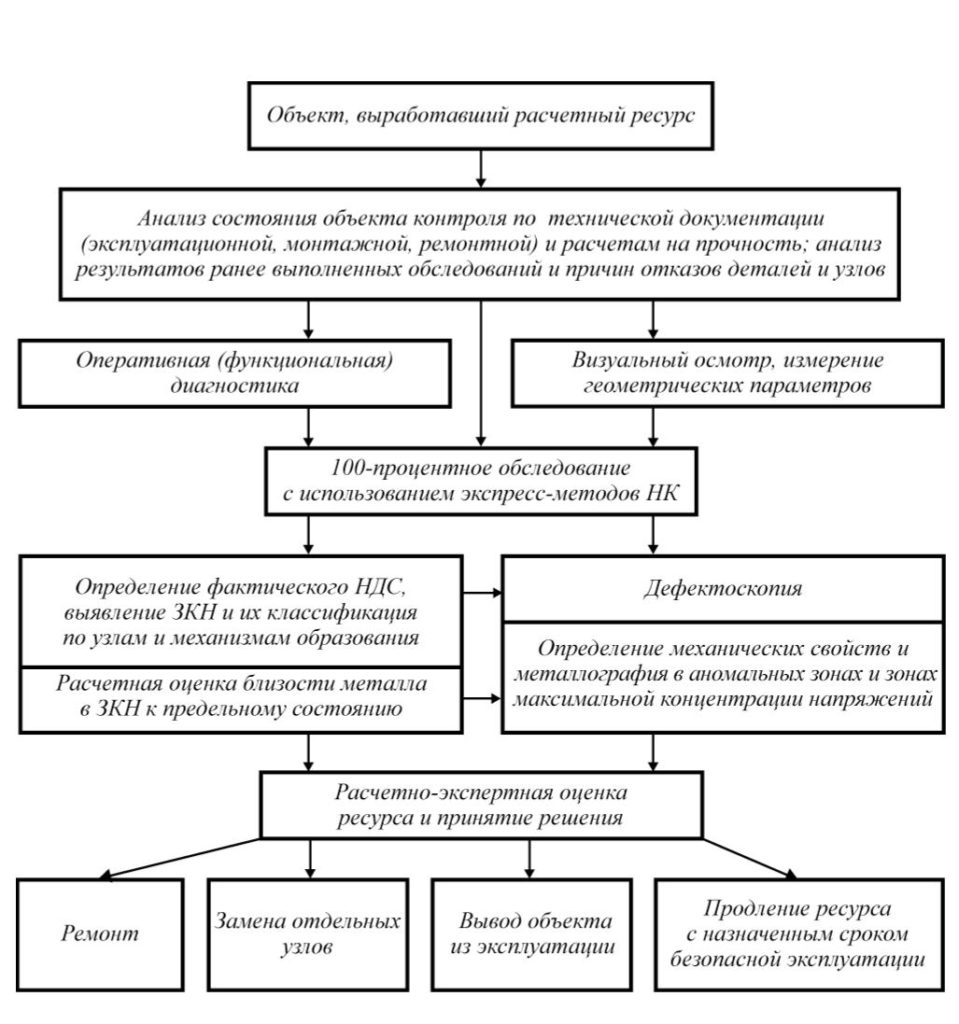
К экспресс-методам отнесены пассивные методы НК, использующие внутреннюю энергию металла конструкций:
- метод акустической эмиссии (АЭ);
- метод магнитной памяти металла (МПМ);
- тепловой контроль.
Эти методы получили в настоящее время наибольшее распространение на практике для ранней диагностики повреждений оборудования и конструкций. Принципиальным отличием такого подхода к оценке ресурса является выполнение 100%-ного обследования объекта с выявлением всех потенциально опасных ЗКН – источников возникновения повреждений при дальнейшей эксплуатации оборудования.
В экспериментальных исследованиях установлено, что уровень напряжений в локальных ЗКН, размеры которых колеблются от десятков микрометров до нескольких миллиметров, могут значительно превышать не только предел текучести, но и предел прочности металла.
Опыт 100%-ного обследования различного оборудования, трубопроводов, конструкций, вращающихся механизмов с использованием метода МПМ показывает, что только 5–10% всего объема металла оборудования выходит на развитие повреждений в ЗКН после длительной его эксплуатации. Однако, как правило, заранее неизвестны места образования ЗКН и уровень деградации металла в этих зонах.
Рассмотрим пример из практики применения метода МПМ на трубопроводах обвязки газоперекачивающего агрегата компрессорной станции с целью определения фактического напряженно-деформированного состояния (НДС) и выявления ЗКН. На рис. 2 представлен участок трубопровода обвязки (диаметр 529×12 мм) такого газоперекачивающего агрегата.
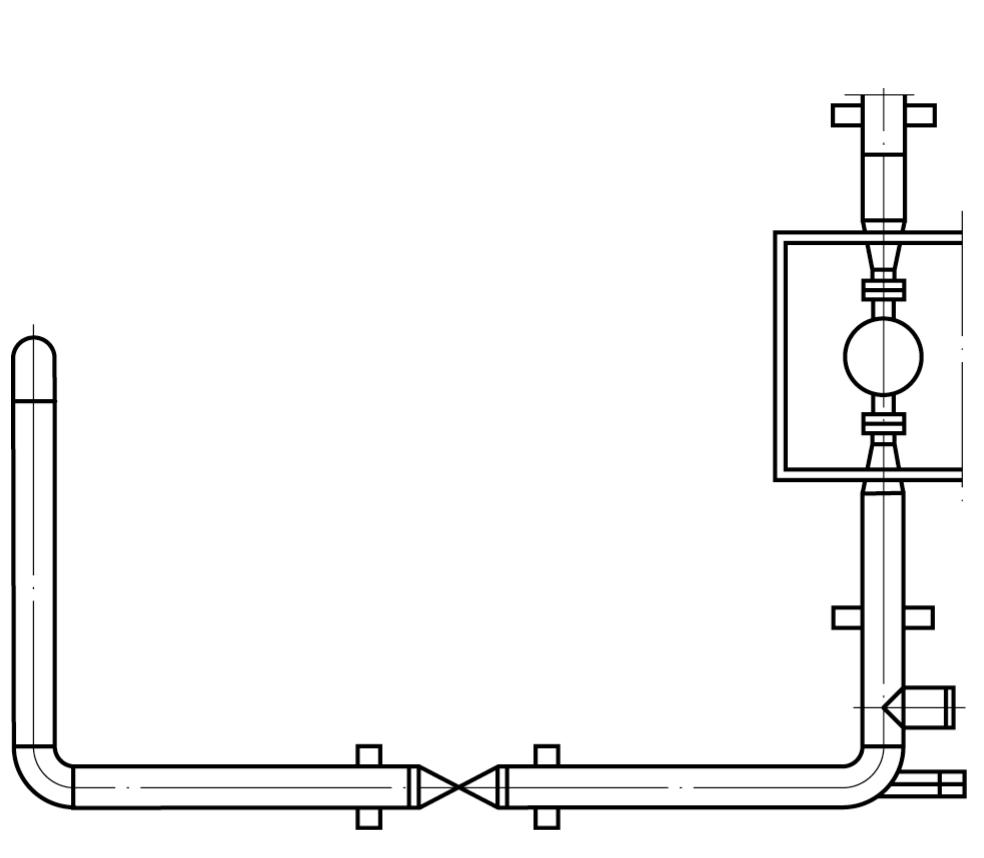
На рис. 3 представлены результаты контроля методом МПМ в виде линий смены знака нормальной составляющей собственного магнитного поля, которые соответствуют линиям максимальной деформации трубопровода, находящегося под давлением газа. При этом на линиях деформации были выявлены зоны максимального градиента магнитного поля dH/dx, которые по методике соответствуют зонам максимальной концентрации напряжений. На левом колене трубопровода обвязки методом МПМ были выявлены две зоны максимальной концентрации напряжений ЗКН1 и ЗКН2 и одна ЗКН3 на правом колене трубопровода.
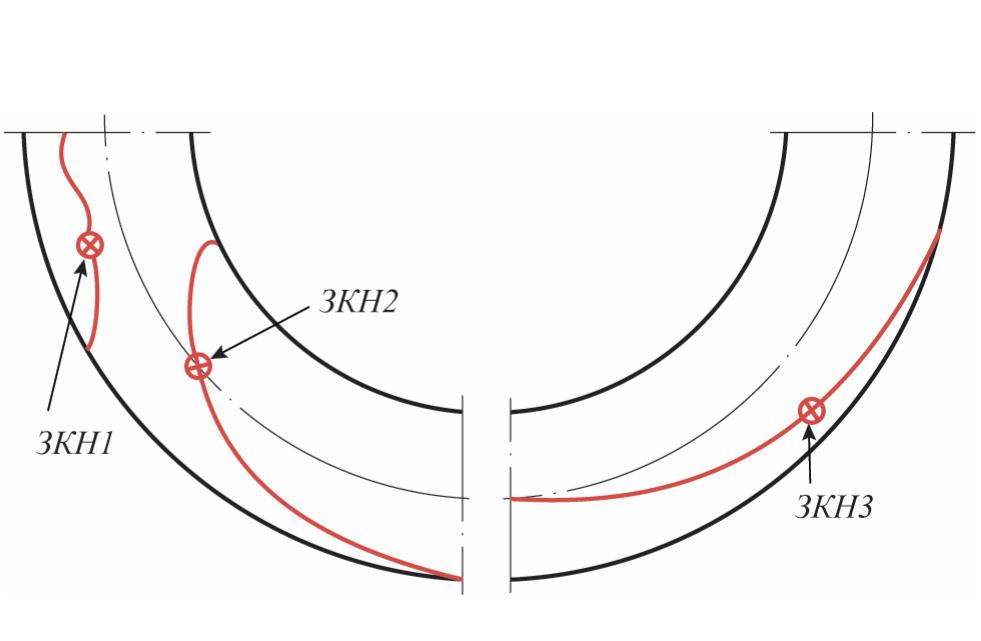
На рис. 4 представлены фрагменты магнитограмм, зафиксированные в ЗКН1 и ЗКН2 при контроле левого колена гиба в осевом направлении.
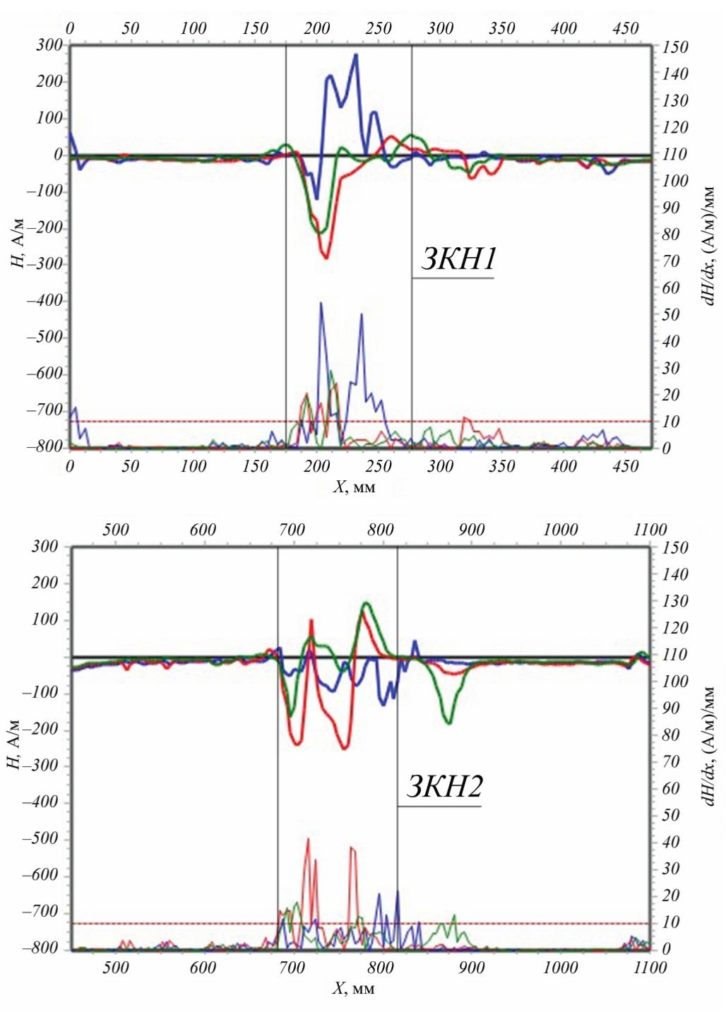
в ЗКН1 и в ЗКН2 на входном трубопроводе обвязки агрегата компрессорной станции
Методика оценки уровня напряжений и предельного состояния металла в ЗКН, выявленных методом МПМ по градиенту магнитного поля, представлена в работе [1].
При реализации предлагаемого ГОСТ Р 53006–2008 представляется возможным в большинстве случаев без выполнения сложных поверочных расчетов на прочность делать экспертную оценку ресурса на основе комплексного обследования оборудования и назначать срок безопасной эксплуатации (см. рис. 1).
На основе рекомендаций указанного стандарта для конкретного оборудования возможна разработка методик оценки риска с учетом особенностей и требований к ОК, существующих в данной отрасли промышленности.
При этом оценка риска становится более конкретной, так как на основе 100%-ного обследования оборудования становятся известными зоны потенциальных повреждений и степень их опасности для развития аварий.
Например, на современной тепловой электростанции (ТЭС) повреждение котельной трубы, расположенной внутри топки котла, приводит к аварийному останову этого котла с простоем в ремонте не более 2…3 суток.
Расчет экономического ущерба от аварийного простоя котла в течение 2…3 суток не представляет проблемы, и такая методика расчета имеется на большинстве современных ТЭС. Если же повреждение происходит на паропроводе, соединяющем одновременно несколько энергетических котлов (ТЭС с поперечными связями), то расчет экономического ущерба при оценке риска представляет уже значительно более сложную задачу, так как повреждение паропровода, как правило, вызывает одновременный аварийный останов сразу нескольких котлов ТЭС (рис. 5). В отдельных случаях разрыв паропровода и развитие аварии может привести к останову всей электростанции (посадка ТЭС на «0»). Экономический ущерб в таком случае на порядок больше. Таким образом, ранняя диагностика зон потенциальных повреждений на ОПО имеет большое значение и при оценке рисков.
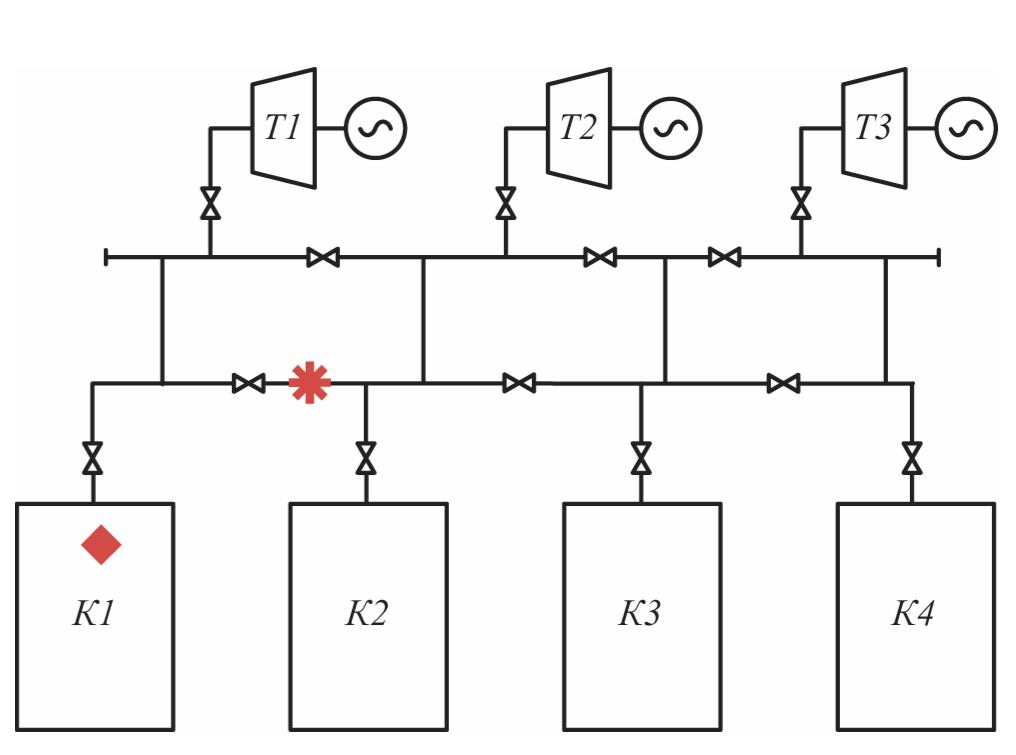
◆ – условное обозначение аварийного останова котла (К1) из-за повреждения трубы внутри топки; – условное обозначение места повреждения паропровода ТЭС
Известно [2], что критерии приемлемых рисков определяются соотношением
R(τ) = FR{Σ[Pi(τ)Ui(τ)]} ≤ [R(τ)], где Pi(τ) – вероятность возникновения опасных ситуаций (повреждения, отказы, аварии); Ui(τ) – возможный ущерб от каждой опасной ситуации; [R(τ)] – приемлемый (допустимый) риск.
При оценке показателя Pi(τ) в настоящее время используется вероятностный детерминированный подход, основанный на статистике уже случившихся повреждений и аварий. Применение методов ранней диагностики оборудования и конструкций, к которым относится метод МПМ, позволит сделать оценку рисков более определенной.
Список литературы
- Дубов А.А., Дубов Ал.А., Колокольников С.М. Метод магнитной памяти металла и приборы контроля. Учеб. пособие. М.: ЗАО «Тиссо», 2012.
- Махутов Н.А., Гадеин М.М. Техногенная безопасность. Диагностика и мониторинг состояния потенциально опасного оборудования и рисков его эксплуатации. Федеральный справочник: Информационно-аналитическое издание. Т. 26. М.: НП «Центр стратегического партнерства», 2012.