Автор: В.Б. Овандер (АО «ЦНИИАГ»).
Опубликовано в журнале Химическая техника №3/2016
Традиционные фланцевые соединения с торцовыми уплотнениями (рис. 1) получили широкое распространение в арматуростроении и гидроприводах благодаря своей простоте и возможности использования простейших плоских или круглых уплотнителей из самых разных материалов. Совершенствование фланцевых соединений в первую очередь касается уменьшения их габаритных размеров в несколько раз переходом от прямой стяжки фланцев болтами к стяжке посредством бугелей [1].
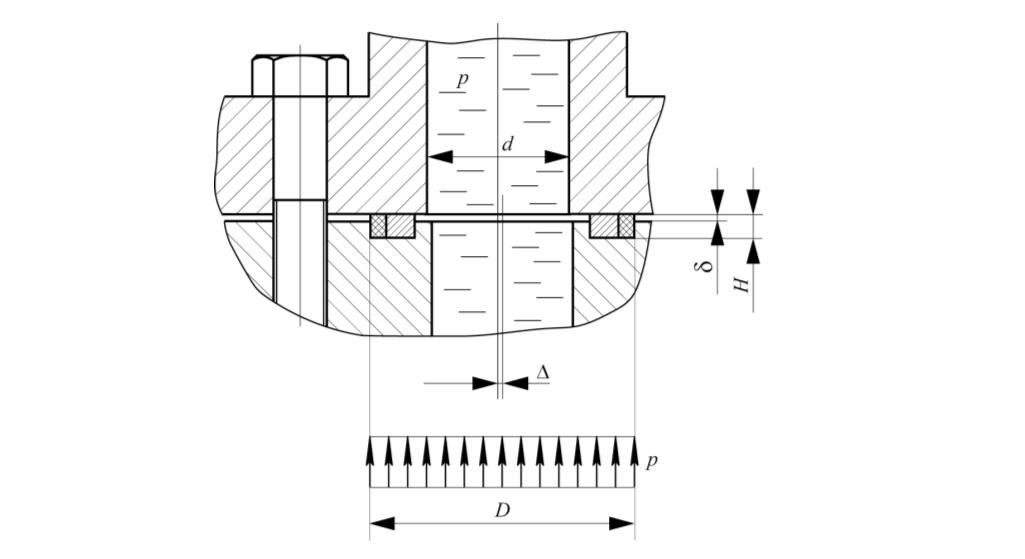
Однако с ростом рабочих давлений жидкостей в гидросистемах, с расширением температурных диапазонов работы все отчетливее проявляются недостатки торцовых уплотнений фланцев, препятствующие тенденции снижения массы и габаритных размеров фланцевых соединений. Эти недостатки состоят в следующем:
- значительные начальные нагрузки на фланцы и их стяжные устройства, связанные с созданием контактных давлений в торцовых уплотнителях, необходимых для поддержания их герметичности при всех эксплуатационных режимах;
- зависимость нагрузки на фланцы от ширины контакта уплотнителей, с ростом которой увеличивается площадь действия давления жидкости;
- высокая чувствительность торцовых уплотнений к деформациям торцов фланцев и зазоров между ними, в результате чего снижается надежность фланцевых соединений под воздействием давления жидкости и внешних нагрузок на фланцы, а также при температурных деформациях болтов и фланцев.
Борьба с этими недостатками развернулась прежде всего в гидроприводостроении, где внедрение блочномодульной компоновки гидроаппаратов с корпусами из легких сплавов и многочисленными многоканальными фланцами, работающими при высоких давлениях (до 40 МПа) и температурах (от –60 до +100°С), потребовала перехода от торцовых уплотнений к более надежным радиальным муфтовым уплотнениям фланцев.
Наглядным примером такого перехода может служить конструкция самолетного рулевого гидропривода [2].
В этой конструкции в многоканальных фланцевых соединениях использованы муфтовые уплотнения в виде металлической втулки с канавками, внутри которых установлены стандартные резиновые кольца в паре с защитными фторопластовыми кольцами, контактирующими с внутренней поверхностью посадочных колодцев во фланцах (рис. 2). В такой конструкции резиновые уплотнители сжимаются радиально при проходе через заходные фаски в колодцах фланцев в процессе сборки фланцевого соединения и затем не нагружают фланцы осевыми силами.
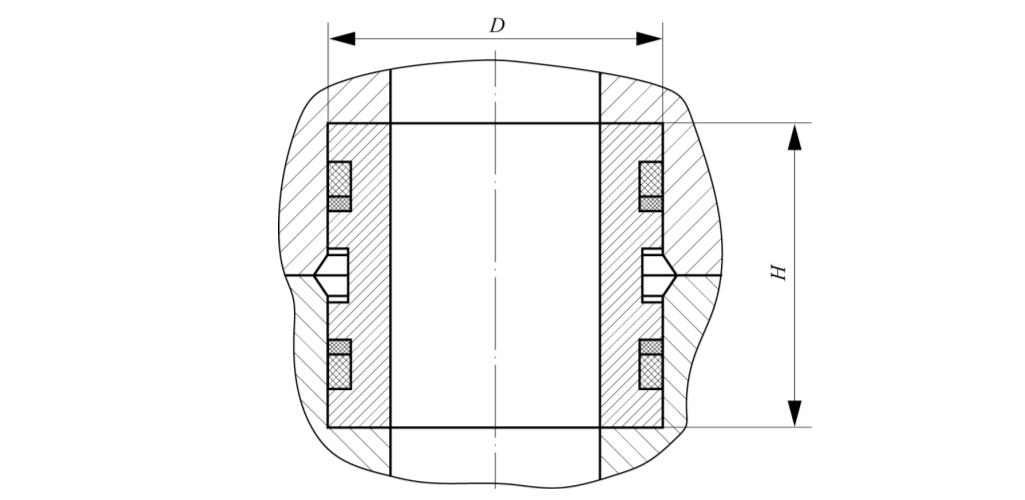
со стандартными резиновыми кольцами
Ширина контакта уплотнителей влияет лишь на осевую протяженность муфтовых уплотнений. Допустимые зазоры между фланцами многократно увеличиваются.
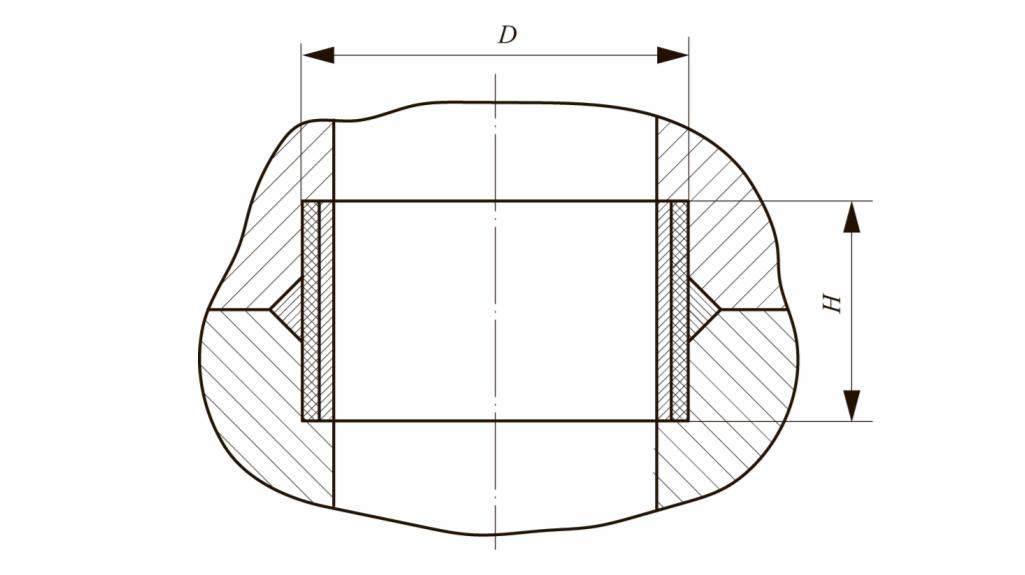
Использование муфтовых уплотнений в авиации наглядно демонстрирует перспективность их применения и в других областях техники. Кроме того, у этого типа уплотнений есть большие резервы для совершенствования. Так, габаритные размеры (D ×H) муфтовых уплотнений могут быть существенно уменьшены переходом от втулок со стандартными резиновыми кольцами к обрезиненным втулкам (рис. 3). Контактные давления на наружной поверхности таких втулок создаются сжатием их по наружному диаметру, аналогично монтажному сжатию резиноармированных манжет для вращающихся валов по ГОСТ 8752–79. При этом сжимается как резиновый слой, так и металлическая втулка, выполняя роль дополнительного генератора контактных давлений. Многолетняя практика применения таких манжет [3] показала высокую надежность гермосоединения шириной всего 5 мм по их наружному диаметру и повышенную морозостойкость по сравнению с резиновыми кольцами из той же резины. Воздействие давления жидкости на внутреннюю поверхность втулок муфтовых уплотнений передается на их наружную поверхность, обеспечивая эффект самоуплотнения, сохраняющий их герметичность при высоких давлениях. Для защиты от экструзии резинового слоя в зазор между фланцами могут использоваться клинопрофильные металлические кольца, заполняющие заходные фаски у колодцев фланцев (см. рис. 3).
При наличии диаметрального натяга по их наружной поверхности клинопрофильные кольца выполняют функцию дополнительного резервного уплотнения фланцев.
Конструкция клинопрофильных уплотнений фланцев подробно описана в работе [4].
Характеристики уплотнений фланцев (D = 16 мм)
Параметр | Вариант уплотнения | |||
Рис. 1 | Рис. 2 | Рис. 3 | Рис. 4 | |
Габаритные размеры
DxH, мм |
30´1,7 | 25´28 | 19´13 | 20´13 |
Площадь действия давления, см2 | 7,1 | 4,9 | 2,8 | 3,1 |
Допустимый зазор между фланцами, мм | 0,01 | 0,5 | 0,3 | 0,3 |
Допустимое смещение осей фланцев, мм | 0,5 | 0,02 | 0,1 | 0,1 |
Испытания опытных образцов муфтовых уплотнений фланцев (см. рис. 3) внутренним диаметром 16 мм показали их работоспособность при температурах от –60 до +100°С и давлении масла до 40 МПа. Сопоставление характеристик фланцевых уплотнений торцового и муфтового типов с внутренним диаметром 16 мм представлено в таблице, из которой следует, что наружный диаметр зоны действия давления жидкости, распирающей фланцы при использовании муфтовых уплотнений, уменьшается в несколько раз. Увеличивается и допустимый зазор между фланцами. Соответственно снижаются нагрузки на фланцы и требования к их жесткости, что позволяет существенно уменьшить габариты и массу фланцевых соединений и повысить их надежность.
Простота конструкции обрезиненных муфтовых уплотнений определяет их невысокую стоимость и допустимость одноразового применения. Если требуется снизить монтажные усилия и обеспечить повышенную сохраняемость резинового слоя при многократных сборках с фланцами, то можно использовать применяемое с этой же целью в резиноармированных манжетах оребрение наружной поверхности резинового слоя с помощью кольцевых канавок [3].
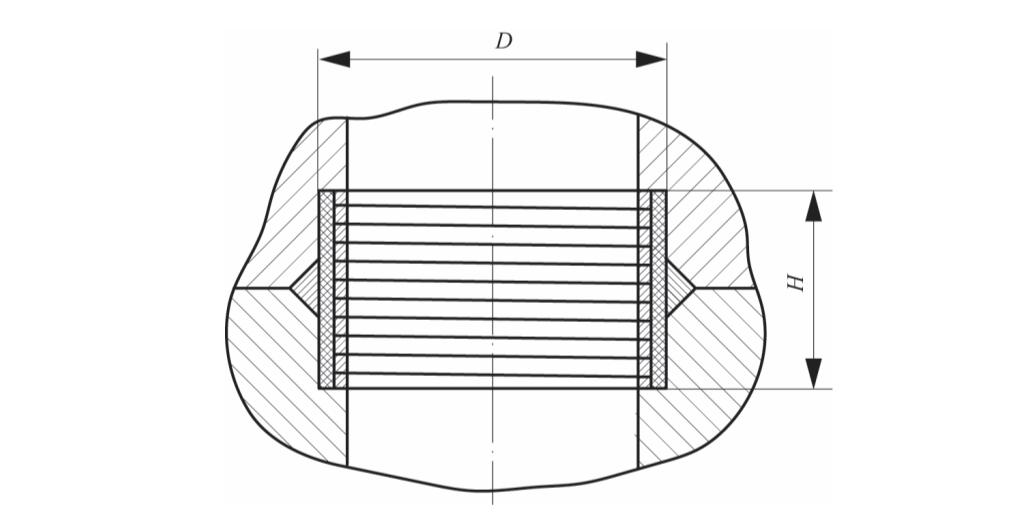
с фторопластовой втулкой на пружине
Химическую стойкость муфтовых уплотнений можно повысить, используя вариант конструкции, показанный на рис. 4, с фторопластовой (Ф-4) тонкостенной втулкой, покрывающей винтовую пружину, работающую на сжатие витков по наружному диаметру [5]. При этом фторопластовая втулка может быть выполнена навивкой из ленточного материала, например из ленты ФУМ. Работоспособность таких уплотнений проверена при давлении масла до 60 МПа и температурах от –60 до +130°С.
При использовании вместо Ф-4 более упругих материалов, например полиэфирэфиркетона (РЕЕК), необходимость во внутренней пружине отпадает, так как этот материал в отличие от Ф-4 не имеет псевдотекучести и сам выполняет функцию пружины. Муфтовое уплотнение может быть целиком металлическим, однако для снижения жесткости такой втулки и увеличения ее упругого хода при сжатии по диаметру ее наружную поверхность целесообразно гофрировать сетью лунок (рис. 5) [6]. При этом следует учитывать, что повышение твердости контактных поверхностей требует для сохранения высокой герметичности снижения их шероховатости с Ra = 1,6 мкм до Ra = 0,2 мкм.
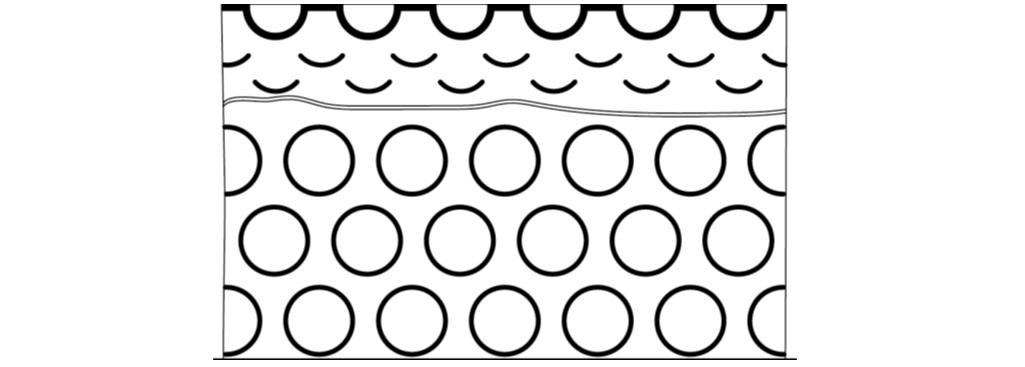
Таким образом, рассмотрены традиционные фланцевые соединения с торцовыми уплотнениями, отмечена тенденция уменьшения их габаритных размеров и выявлены недостатки торцовых уплотнений, препятствующие этой тенденции.
На примере фланцевых соединений самолетных рулевых гидроприводов показаны преимущества радиальных муфтовых уплотнений, повышающих компактность и надежность фланцевых соединений за счет снижения нагрузки на фланцы и роста допустимых зазоров между ними.
Проанализированы конструкции существующих муфтовых уплотнений и их характеристики и представлены пути их дальнейшего совершенствования.
Список литературы
- Погодин И.К., Трутаев С.Ю., Трутаева И.И. Разработка методов оптимального проектирования разъемных соединений высокого давления//Химическое и нефтегазовое машиностроение. 2015. №9.
- Шумилов И.С. Системы управления рулями самолетов. М.: Изд. МГТУ им. Н.Э. Баумана, 2009.
- Голубев Г.А., Кукин Г.М., Лазарев Г.Е., Чичинадзе А.В. Контактные уплотнения вращающихся валов. М.: Машиностроение, 1976.
- Овандер В.Б., Никитин О.Ф. Компактные клинопрофильные уплотнения для валов и фланцев гидромашин//Вестник арматурщика. 2015. 5.
- А.с. №1588965. Уплотнение фланцевого соединения 6. А.с. №1610161. Контактный уплотнитель.