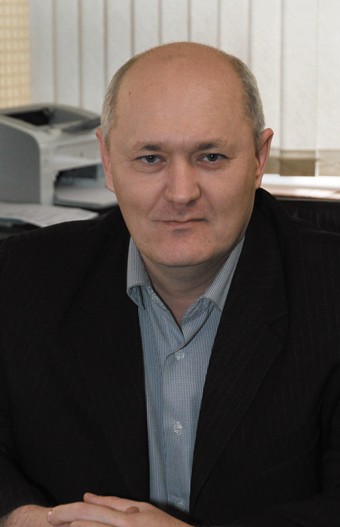
Опубликовано в журнале Химическая техника №12/2014
Подавляющее большинство российских предприятий вне зависимости от сферы деятельности объединяют одни и те же проблемы. Одна из основных касается технической базы. Оборудование, установленное еще в советские времена, выходит из строя. Постоянные ремонты помогают до поры до времени, поскольку любая техника имеет свой ресурс, который рано или поздно вырабатывается. Кроме того, оборудование и технологии, бывшие лет 30–50 назад суперсовременными, в наше время безнадежно устарели. Для эффективной деятельности компании, которая рассчитывает не только работать, но и зарабатывать, нужны новые, более совершенные агрегаты. Ни для кого не секрет, что без модернизации своего предприятия сегодня не обойдется ни один здравомыслящий руководитель. В качестве примера можно привести ОАО «КуйбышевАзот», расположенное в г. Тольятти. Последнее десятилетие предприятие активно инвестирует в свое развитие, а к приближающемуся полувековому юбилею завод подойдет к завершению нового этапа крупномасштабного обновления и расширения. Подробнее об этом расскажет начальник цеха слабой азотной кислоты Владимир Николаевич Гусак.
Владимир Николаевич, какова цель модернизации вашего предприятия?
Цель модернизации – сократить потребление сырья, теплои энергоресурсов, снизить воздействие на окружающую среду и повысить безопасность. Кроме того, предприятие последовательно наращивает выработку продукции более высоких переделов, у которой доходность больше, строит новые производства.
За последние годы мы существенно увеличили свой ассортимент. Это позволяет нам гибко реагировать на рыночную ситуацию и запросы потребителей, регулируя объемы выпуска по всей линейке продуктов.
Какие направления деятельности были основными, и на что ориентируется завод сегодня?
У «КуйбышевАзот» два основных направления деятельности. Первое – это производство капролактама и его производных, а второе – аммиак и азотные удобрения. Еще вырабатываем технические газы.
С 2003 г. предприятие реализует программу по глубокой переработке капролактама, было построено несколько линий по производству полиамида-6, высокопрочных технических нитей и кордной ткани.
К настоящему времени «Куйбышев-Азот» стал крупнейшим производителем в России всех этих продуктов.
А на заводах в Курске и Балашове, которые были в 2007 и 2010 гг. приобретены на грани остановки, мы смогли сначала восстановить, а потом и модернизировать производство текстильных нитей и тканей.
В этом году мы запустили установку пропитки кордной ткани. На новом производстве применяются современные технологические решения, обеспечивающие эффективный расход пропиточных материалов и улучшение физико-механических свойств ткани. Поставщик оборудования – компания Benninger Zell (Германия). Теперь «КуйбышевАзот» может предложить российским шинникам более конкурентоспособный продукт. Мощность производства составляет до 30 миллионов погонных метров в год. Установка рассчитана на пропитку кордной ткани, выпускаемой и в Тольятти, и в Курске. Сейчас наша ткань проходит испытания у потребителей, например в Нижнекамске. Планируются и экспортные поставки.
Много проектов и в стадии реализации. Ведется строительство агрегата УКЛ для получения слабой азотной кислоты. Завершается реконструкция отделения ректификации на производстве капролактама.
В первом полугодии 2015 г. планируется ввести в эксплуатацию новое энергоэффективное производство циклогексанона по технологии «Royal DSM N.V.» (Нидерланды). Этот проект можно смело отнести к числу ключевых в реализации стратегической программы развития предприятия.
Еще одна очень серьезная стройка – это агрегат аммиака мощностью 1340 тонн/сутки. Возводится еще одна установка для разделения воздуха. Последние два проекта реализуются в режиме совместных предприятий с крупнейшими мировыми компаниями в этой области – Linde (Германия) и Praxair (США). На всех производствах используются прогрессивные ресурсосберегающие технологии с уровнем экологической и промышленной безопасности, соответствующим уровню лучших мировых аналогов.
Как видите, у нас очень большая инвестиционная программа, затраты на нее составляют более 20 миллиардов рублей. Наш генеральный директор В.И. Герасименко всегда контролирует техническое перевооружение, развитие компании планируется на многие годы вперед. Только так можно обеспечить конкурентоспособность завода.
Это только то, что касается новых производств. Параллельно модернизируется действующее оборудование. Конкретно: в моем цехе отремонтирован каждый аппарат одиннадцати агрегатов слабой азотной кислоты. Это абсорбционные колонны, турбокомпрессоры, контактные аппараты и многое другое.
Были частично заменены подогреватели хвостовых газов. Меры довольно затратные, но необходимые.
Межремонтный период на предприятии невелик – не более года. Основательный капитальный ремонт проводится 1 раз в два года. Ремонтируется или меняется «начинка» каждого аппарата агрегата.
Ведется постоянный мониторинг работы всего оборудования. Все должно работать даже лучше, чем часы. Нарушение технологических параметров – это сбой в работе и, значит, потеря денег. Нельзя подводить коллектив.
Попадает ли на ваше предприятие контрафактная продукция?
Главный критерий в выборе поставщиков – это надежность и качество. Служба комплектации оборудования рассматривает все предложения претендентов на сотрудничество и выбирает наиболее приемлемый вариант. Если речь идет о компании – производителе оборудования, то пристальное внимание уделяется каждой мелочи.
При этом каждый случай индивидуален – иногда продукция отечественных производителей лучше, чем их зарубежных коллег, иногда наоборот. Проводится и входной контроль.
Какие меры предпринимает завод для того, чтобы быть максимально безопасным для окружающей среды?
Это обязательное условие развития. Ведется постоянный мониторинг по всем экологическим параметрам: наши сертифицированные лаборатории в год различных анализов делают более 40 тысяч. Надо сказать, что внедрение современных технологий, постоянная модернизация и природоохранные мероприятия дают свои результаты – снижаются объемы и выбросов, и сбросов, и потребления ресурсов.
Отслеживается и безопасность работы каждого цеха. В конце этого года будет сдан узел охлаждения конденсата сокового пара в производстве аммиачной селитры. Фактически это завершающий этап по созданию локальных очистных сооружений, в которых применяются технологии ионной очистки. После ввода их в строй, вопервых, прекратится сброс химически загрязненных стоков с производства аммиачной селитры, а во-вторых, общий объем подобного рода отходов уменьшится на треть. Ну и наконец, предприятие сократит потребление речной воды. Затраты на этот проект составили порядка 300 млн. руб.
Владимир Николаевич, модернизация и ремонт требуют немалых средств. Где вы их берете?
Несмотря на все кризисы, перестройку, постперестроечные трудности и развал Советского союза на предприятии ни разу не было задержки с получением заработной платы. Грамотное планирование, правильные стратегические цели, эффективный менеджмент – залог успешной работы. У нас очень сильная управленческая команда. Руководство компании всегда очень гибко и своевременно реагирует на ситуацию. Мы никогда не останавливаемся, всегда идем вперед, хоть это довольно трудно. Конечно, привлекаем и кредитные средства, но всегда четко оцениваем свои возможности. Бывает, что какие-то проекты приходится и откладывать.
В последние годы удалось привлечь иностранных партнеров и создать совместные предприятия. В этом нас поддерживает и оказывает помощь Губернатор и Правительство Самарской области, руководство Приволжского федерального округа.
Например, наш проект по строительству энергоэффективного производства циклогексанона входит в число приоритетных в ПФО. Сейчас ситуацию простой не назовешь, но надо работать, только так все может получится.
Те изменения, которые проводит в жизнь ОАО «КуйбышевАзот, помогут не только увеличить объемы производимой продукции и снизить ее себестоимость, но и повысить ее качество. Это те факторы, которые на рынке по-прежнему определяют, с кем из поставщиков предпочтет сотрудничать потребитель.
Большое спасибо, Владимир Николаевич! Успешной деятельности Вам и коллективу ОАО «Куйбышев-Азот»!