Автор: А.М. Добротворский (ЗАО «НПО «Ленкор», СПбГУ), А.В. Балутов, Е.П. Денисенко, Е.П. Шевякова, Д.А. Легостаев (ЗАО «НПО «Ленкор»), А.В. Макаров (ООО «ЛЕНТЕСТ»).
Опубликовано в журнале Химическая техника №12/2014
Трубчатые печи – основное оборудование многих установок крупнотоннажных производств нефтеперерабатывающей и нефтехимической промышленности. Отечественный и мировой опыт проектирования, строительства и эксплуатации трубчатых печей насчитывает более чем вековой опыт. Современные печи характеризуются высокой эффективностью использования тепла сжигаемого топлива, надежностью эксплуатации, оснащенностью средствами автоматического контроля и управления режимом работы, системами противоаварийной защиты. Проектирование и эксплуатация печных агрегатов в РФ регламентируется рядом нормативных документов, включая Федеральные нормы и правила, Государственные стандарты, рекомендательные отраслевые документы [1–5].
В настоящее время в нефтеперерабатывающей и нефтехимической промышленности проектируются, строятся и эксплуатируются трубчатые печи различной конструкции, материального исполнения основных элементов и назначения. По назначению печи разделяются на два основных типа: нагревательные и реакционные печи. При этом до относительно недавнего времени реакционные печи эксплуатировались преимущественно в нефтехимической промышленности, в процессах пиролиза. За последние годы в связи со строительством комплексов глубокой переработки нефти и возникновением дефицита водорода, направляемого на установки крекинга тяжелых углеводородов, реакционными печами получения водорода (парового риформинга) оснащаются многие отечественные нефтеперерабатывающие заводы.
Следует отметить, что в настоящее время отечественная нормативная база, регламентирующая как строительство, так и эксплуатацию реакционных печей, минимальна и сводится к ряду отраслевых документов, в основном представленных техническими условиями на изготовление змеевиков печей пиролиза (например, [6,7]). Строительство печей парового риформинга в нефтепереработке осуществляется исключительно по зарубежным проектам, что создает большой ряд проблем в процессе их эксплуатации и ремонта.
Экспертиза промышленной безопасности (ЭПБ) трубчатых печей нефтеперерабатывающей и нефтехимической промышленности является многоплановой работой, требующей привлечения специалистов разного профиля. Эти работы включают рассмотрение проектной и эксплуатационной документации, техническую диагностику печей, комплексные металловедческие исследования вырезов металла змеевиков, предусмотренные действующими инструкциями, проведение прочностных расчетов и расчетов остаточного ресурса. ЭПБ проектной документации выделяется в отдельный вид экспертных работ. До введения в действие Градостроительного кодексаРФ ЭПБ подлежала проектная документация на строительство, реконструкцию, модернизацию и техническое перевооружение технологических печей. В настоящее время требование проведения ЭПБ распространяется только на небольшую часть проектной документации.
К работам по ЭПБ и технической диагностике печей тесно примыкают работы по техническому аудиту действующих производств, контролю качества изготовления монтажа печного оборудования, прежде всего змеевиков печей, и работы по выявлению причин, отказов и аварий печей.
В ЗАО «НПО «Ленкор» накоплен многолетний опыт работ во всех указанных направлениях, а также в направлении совершенствования их методической базы [8–13]. Далее рассмотрен ряд примеров выполнения экспертных работ и проанализированы возникающие при этом проблемные вопросы.
Опыт ЭПБ проектной документации
Одной из основных проблем, связанных с ЭПБ проектной документации, является постоянно изменяющаяся нормативно-техническая база. Глубокое понимание требований любого нормативного документа требует времени для изучения и накопления опыта применительной практики. При необоснованно частой смене нормативных требований специалисты проектных, эксплуатирующих организаций, эксперты просто не имеют такого времени, что приводит к снижению качества работ всех видов, возникновению большого числа спорных и непроясненных вопросов.
В этом плане, как положительный пример, можно отметить Федеральный закон №116-ФЗ «О промышленной безопасности опасных производственных объектов». Специалисты, разрабатывавшие его текст, учли практически все вопросы, с которыми приходится сталкиваться при практическом его использовании. Законом даны определения объектов промышленной безопасности, определен порядок правового регулирования, задачи Федеральных органов исполнительной власти, основы промышленной безопасности и др. В течение 10 лет в текст документа не вносилось принципиальных исправлений и дополнений, а все корректировки были вызваны изменением структуры административного управления вопросами промышленной безопасности.
Существенные изменения текста Закона начались в связи необходимостью его приведения в соответствие с другими действующими правовыми Актами, на первом этапе – с Градостроительным кодексом (Федеральный закон №190 от 29.12. 2004 г.). Главное несоответствие двух законодательных актов состояло в том, что, как уже отмечалось, по Градостроительному кодексу вся экспертиза промышленной безопасности проектной документации стала функцией Главгосэкспертизы.
За Ростехнадзором сохранена ЭПБ проектной документации на техническое перевооружение, не входящей в состав проектной документации, представляемой на государственную экспертизу, капитальный ремонт, консервацию и ликвидацию опасных производственных объектов. В развитие положений Федерального закона №190-ФЗ были приняты несколько подзаконных актов. Указанные правовые акты, на наш взгляд, отодвинули на второй план важнейшие вопросы, определяющие принципы проектирования опасных производственных объектов, в том числе технологических печей, которые нужно рассматривать не только как объект капитального строительства, но и как техническое устройство, задействованное в сложном и опасном технологическом процессе. Эти вопросы, на наш взгляд, не достаточно учтены и в требованиях к содержа-нию соответствующих разделов проектной документации, предусмотренных Постановлением №87 Правительства РФ от 16.02.2008 г. [14]. Безусловно, назрела необходимость создания документа, определяющего требования к технологическому проектированию. Устарел и требовал переработки СНиП 11-01–95 [15].
Следует отметить несоответствие статей 8 и 13 Закона №116-ФЗ положениям Градостроительного кодекса.
По непонятной причине требования Градостроительного кодекса не были распространены на техническое перевооружение объектов, что вызывало споры о необходимости и правовой обоснованности проведения ЭПБ соответствующей документации.
Переход от разрешений на применение технических устройств, в том числе печей, к системе сертификации и добровольной аккредитации машин и оборудования на соответствия требованиям Технических регламентов Таможенного союза также, на наш взгляд, не способствует повышению уровня промышленной безопасности. Сертификация не учитывает всех особенностей применения технических устройств в составе опасных производственных объектов. То же можно сказать и об отказе от лицензирования проектирования опасных производственных объектов. Либерализация требований к проектным организациям проявляется в снижении качества проектной документации.
Рассматривая различные этапы внедрения новых печных агрегатов на предприятиях отрасли, можно с уверенностью сказать, что обеспечение их безопасности, а также экономии средств на их строительство и эксплуатацию должны достигаться на этапе проектирования. Если при проектировании учтены все требования норм и правил, все затраты, связанные с подключением печи к инженерным коммуникациям, то стоимость строительства окажется минимальной при обеспечении требуемого уровня безопасности.
Важным документом, регламентирующим общие технические требования к нагревательным установкам, стал ГОСТ Р 52682 [2]. Однако он не отражает отдельные моменты, подлежащие обязательному учету при проектировании. Особенно это проявляется при подготовке технических заданий на проектировании новых печей с привязкой к сетям действующего предприятия.
В задании на проектирование, в частности, могут отсутствовать данные по результатам инженерногеологических и инженерно-геодезических изысканий на площадке будущего строительства, которые должен представлять заказчик на стадии подготовки проектирования, что является требованием Градостроительного кодекса, не позволяющего осуществлять проектирование при отсутствии таких данных.
Проектные организации зачастую приступают к проектированию, не имея необходимых исходных данных, что в дальнейшем приводит к переработке выполненной ранее документации.
Следующим моментом, на котором следует остановиться, является недостаточное освещение в задании на проектирование вопросов по уровню автоматизации работы печного агрегата. Если при проектировании не учтены затраты, связанные с проектированием и закупкой обязательных приборов контроля и автоматизации, на последующих стадиях возникнут вопросы удорожания проектных и строительно-монтажных работ, снижения необходимого уровня безопасности объекта.
Нами были выявлены случаи, когда в задание на проектирование не были включены мероприятия, связанные с паровой защитой печного агрегата, которые включают комплекс мер по предотвращению влияния аварийных ситуаций и инцидентов, возникающих в ходе эксплуатации печей, которые предусмотре ны. ФНП «Общие правила взрывобезопасности для взрывопожароопасных химических, нефтехимических и нефтеперерабатывающих производств». Многие из этих требований проверены практикой, и во всех предыдущих редакциях «Общих правил…», а также в ведомственных нормах ВУПП-88 [16] они содержались. Рассматривая этот вопрос, также рекомендуется использовать положения, касающиеся нагревательных печей, содержащиеся в ВНТП 81–85 [17] и инструкции по проектированию паровой защиты технологических печей [18]. Последний документ содержит требование о том, что в случае устройства непрерывной паровой завесы распределяющий коллектор прокладывается на высоте порядка 300…400 мм на самостоятельных опорах по периметру каркаса печи или наружной границе рабочей площадки с выпускными отверстиями под углом 45° к горизонтали.
Среди других средств, исключающих образование взрывоопасных смесей в нагревательных элементах (змеевиках), топочном пространстве и рабочей зоне печи, следует выделить средства автоматической или дистанционной подачи водяного пара или инертного газа в топочное пространство и в змеевики при прогаре труб. При этом не стоит забывать, что такой способ защиты змеевиков не допускается при осуществлении каталитических процессов, и его применение подлежит обоснованию в проектной документации [1].
В проектной документации должно предусматриваться аварийное освобождение змеевиков печей от нагреваемого жидкого продукта при повреждении труб или при прекращении его циркуляции.
Если хоть один из указанных выше способов защиты печных агрегатов не реализован в проектной документации, то возникает необходимость обоснования безопасности, принятых проектных решений в соответствии с требованиями действующей редакции Федерального закона №116-ФЗ.
Еще одним моментом, встречающимся при ЭПБ проектной документации, является отсутствие указаний по устройству противопожарной защиты опор и по организации площадок обслуживания по периметру печного агрегата, обоснования числа аварийных выходов.
В ходе проводимых ЗАО «НПО «Ленкор» работ по техническому аудиту технологических установок, в состав которых входят и трубчатые печи, был выявлен ряд нарушений, связанных с невыполнением требований промышленной безопасности.
В значительной степени это относится к проектной документации, а, следовательно, и к строительству комплектно поставляемых из-за рубежа технологических печей. Так, на одном из предприятий отрасли на установке производства водорода отключающая арматура на топливном газе была установлена на расстоянии менее 10 м от печного агрегата, подогреватель топлива располагается не на нулевой отметке, а поднят на отметку 15 м, не соблюдены расстояния от печи до соседних сооружений, которые должны быть не менее 10 м, коллектор паровой завесы проложен по опорам без соблюдения необходимых требований безопасности.
Опыт ЭПБ и технического диагностирования трубчатых печей
Технологическое оборудование нефтеперерабатывающих и нефтехимических производств эксплуатируется в условиях комплексного воздействия повышенных температур, давлений и агрессивных технологических сред, которые могут содержать разное количество водорода, сероводорода, меркаптанов, соединений хлора и других коррозионноактивных компонентов. В первую очередь это относится к реакторным блокам технологических установок и технологическим печам. Воздействие агрессивных сред, особенно при повышенных температурах, приводит к постепенной деградации конструкционных материалов – сталей разных групп и классов, что может стать причиной отказов и аварий.
Наиболее уязвимыми с точки зрения быстрого развития процессов деградации металла являются змеевики трубчатых печей. В настоящее время в нефтепереработке используются печи разных конструкций, в которых осуществляется нагрев сырья до температур 300…900°С.
В условиях высоких температур, давлений и объемных скоростей сырьевых потоков, а также воздействия разогретых дымовых газов могут развиваться различные коррозионные и эрозионные процессы, приводящие в совокупности к потере прочности змеевиков, их формоизменению и в конечном счете к их разгерметизации и разрушению.
Основной причиной ограничения срока службы печных змеевиков нагревательных печей является тепловое старение под действием температурных и временных факторов, что приводит к изменению их микроструктуры и снижению длительной прочности металла [13]. Этому способствуют отклонения от технологического режима эксплуатации нагревательных трубчатых печей, сопряженные со значительным перегревом труб, что неизбежно ведет к аварийным остановкам производств.
Другой причиной снижения долговечности змеевиков нагревательных и реакционных печей является воздействие технологической среды на металл труб. На внутренних поверхностях труб осаждаются продукты конденсации и частичного коксования углеводородов, а также соли недостаточно обессоленной нефти.
Отложения снижают теплопередачу, увеличивают локальную температуру стенки и тем самым ускоряют процессы коксования. По аналогичному автокаталитическому механизму развивается сульфидная коррозия, вызываемая химическим взаи модействием металла с серусодержащими компонентами сырья. Отслоение продуктов коррозии приводит к утонению стенки трубы и локальному перегреву в местах утонения. Воздействие водорода приводит к обезуглероживанию сталей – водородной коррозии, связанной с распадом карбидов. В стояночных режимах печи подвергаются коррозионному воздействию кислых продуктов разложения технологических отложений при их контакте с влажным воздухом, в частности карбоновых и политионовых кислот.
Змеевики реакционных печей пиролиза и парового риформинга работают при температурах, на несколько сот градусов превышающих температуру эксплуатации змеевиков нагревательных печей. Поэтому для них превалирующим фактором деградации являются высокотемпературная ползучесть и хрупкое разрушение в результате науглероживания металла [19–21].
Указанные факторы ограничивают срок безопасной эксплуатации технологических печей и предъявляют особые требования к применяемым материалам, качеству изготовления и монтажа печного оборудования, надзору за эксплуатацией печей и к их техническому диагностированию.
Специалистами ЗАО «НПО «Ленкор» ежегодно выполнятся работы по ЭБП и техническому диагностированию десятков технологических печей на предприятиях отрасли. Кроме того, проводятся работы по контролю качества монтажных и ремонтных работ, а также по выявлению причин отказов и инцидентов, связанных с технологическими печами.
В этих работах используются все современные методы неразрушающего контроля, включая рентгенографический контроль, являющийся чрезвычайно эффективным методом, которым на «экспертном» уровне владеют лишь немногие организации.
Для металловедческих исследований вырезок металла привлекаются самое современное оборудование и методы, в том числе электронная микроскопия, рентгеновский микроанализ, рентгенофазовый анализ и др. Выполняется комплекс механических испытания, включая испытания на длительную прочность.
Рассмотрим несколько конкретных примеров выполненных за последнее время работ.
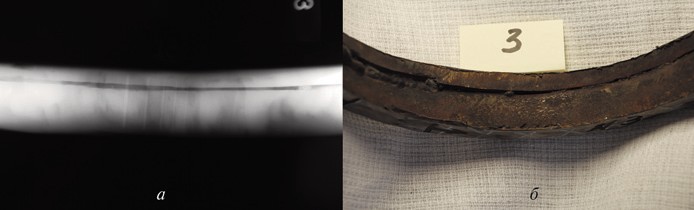
Дефекты, выявляемые при радиографическом контроле печных змеевиков. При выполнении рентгенографического контроля в ходе технического диагностирования печных змеевиков (сталь 08Х18Н10Т, труба 219×14) установки гидроочистки дизельного топлива Л-24-10/2000 был выявлены дефекты в корнях швов со стороны стенки печи. Снимок типичного дефекта приведен на рис. 1, а.
Вырезка дефектного стыка (рис. 1, б) полностью подтвердила результат дефектоскопии. Следует отметить, что установить наличие такого дефекта альтернативным методом – с помощью ультразвуковой дефектоскопии – крайне затруднительно как из-за класса стали (аустенитная сталь), так и из-за положения дефекта.
Техническое диагностирование технологических печей Ачинского НПЗ. В результате аварии, произошедшей 15 июня 2014 г. на территории секции С-400 установки ЛК-6У «АНПЗ ВНК», помимо основных разрушений вследствие воздействия ударной волны, огня, конвективного воздействия теплового потока, дыма, воды при пожаротушении, частичное повреждение могло получить технологическое оборудование смежных секций С-100, С-200 и С-300 установки. Для оценки необходимых ремонтно-восстановительных мероприятий и возможности дальнейшей эксплуатации специалистами ЗАО «НПО «Ленкор» было выполнено комплексное обследование технологических печей этих секций.
Техническое диагностирование печей секции С-100 (первичная переработка сырья) не выявило поражений от воздействия ударной волны и пожара, влияющих на их безопасную эксплуатацию. Наружный осмотр змеевиков показал, что состояние основных элементов змеевиков удовлетворительное: прогары, отдулины, свищи и трещины отсутствуют, изменений геометрических размеров и форм труб и отводов не обнаружено. В то же время результаты ультразвуковой толщинометрии змеевика радиантной камеры печи П-101/3 этой секции выявили значительное локальное утонение стенок (до 6 мм при исполнительной толщине 12 мм), связанное с эксплуатационными факторами, при том, что змеевики камеры радиации заменялись в 2008 и 2010 гг. На этих участках произведены вырезки катушек, осмотр которых показал наличие глубоких раковин и вымывание внутренней поверхности калачей и отводов (рис. 2, а). Вырезка катушек позволила произвести осмотр внутренней поверхности змеевиков с применением телевизионной эндоскопии, который подтвердил данные толщинометрии (рис. 2, б).
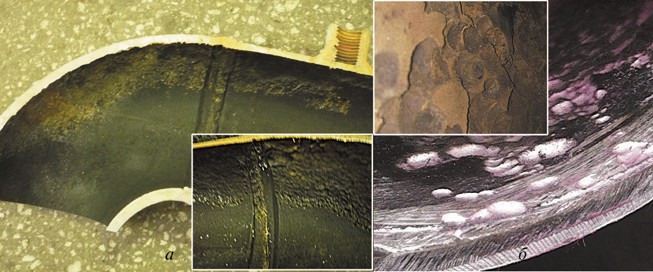
Обследование печей секции С-200 (каталитический риформинг) и С-300 (гидроочистка) также не выявило механических дефектов, связанных с аварией. Однако, учитывая, что печь П-203/3-2 этой секции находилась ближе всего к очагу аварии, было принято решение произвести контрольную вырезку металла из змеевика камеры радиации для лабораторных металловедческих исследований.
По результатам проведенного исследования установлено, что твердость труб выше максимально допустимых значений для стали 15Х5М по СТО СА 03-004–2009 [4]. Микроструктура соответствует стали 15Х5М после быстрого охлаждения от температуры выше критической точки А1. Изменения в структуре (рис. 3) – образование бейнита и, как следствие, повышение твердости – могут быть связаны с нарушением режима эксплуатации при тушении пожара, возникшего впоследствии аварии.
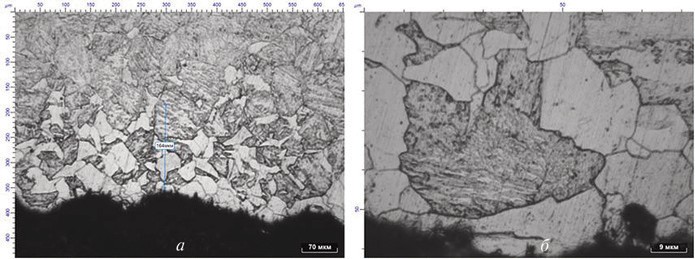
Исследование металла змеевика печи П-1 установки каталитического риформинга ЛГ-35/8-300Б с целью выяснения причин выявленного пропуска. Установка эксплуатируется с 1972 г. При плановом обследовании блока гидроочистки установки в 2012 г. был обнаружен пропуск газосырьевой смеси в змеевике радиантной камеры печи П-1 (сталь Х12CrMo9.1; рабочие параметры: давление 3,9 МПа, температура 420°С).
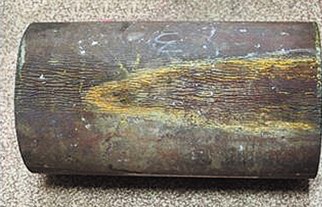
Для выявления причин пропуска выполнены комплексные металловедческие исследования катушки, вырезанной из дефектной части змеевика (рис. 4). Химический анализ отложений на внутренней поверхности змеевика показал наличие в них значительного содержания серы. По данным рентгенофазового анализа отложений установлено, что основную долю в них составляет сульфид железа FeS, далее (в порядке убывания) смешанные сульфиды и оксиды железа и хрома: FeCr2S4; Cr2O3FеO, Cr2S3 (рис. 5). Характер отложений свидетельствует о том, что они образовались в результате длительного взаимодействия металла змеевика с сероводородом и серусодержащими компонентами прямогонной бензиновой фракции при повышенных температурах. Образование оксидов на внутренних поверхностях труб является результатом окисления металла и серусодержащих отложений в процессе выжига кокса.
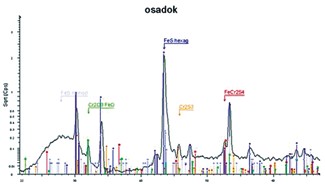
Результаты исследования внутренней поверхности и сечения труб методом растровой электронной микроскопии с рентгеновским микроанализом1 подтвердили данные выводы о природе отложений (рис. 6, а), а также показали, что причиной растрескивания металла является воздействие коррозионно-активных соединений, содержащих серу и соли натрия, попадающих в змеевик при гидроиспытаниях (рис. 6, б).
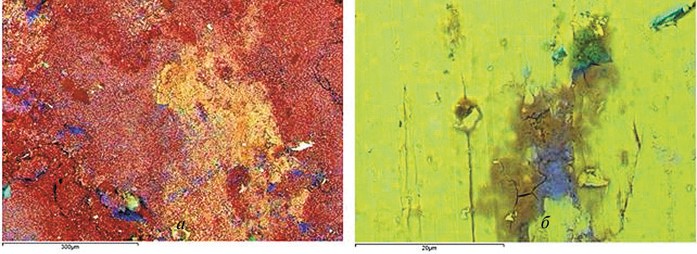
с микротрещиной (б). Синий – сера, голубой – кремний, зеленый – натрий, желто- зеленый – железо, оранжевый – кислород, красный – углерод
Образование трещины произошло из-за структурно-механической неоднородности металла змеевика вследствие локального высокотемпературного перегрева, обусловленного накоплением отложений на внутренней поверхности змеевика в наиболее теплонапряженной зоне.
Наличие отложений привело к снижению интенсивности отвода тепла сырьевым потоком, к местному перегреву трубы, образованию отдулины и затем – к разгерметизации змеевика.
Исследования вырезок металла коллектора печи Н-4101-В установки получения водорода (УПВ). ПечьН-4101-В предназначена для проведения реакции парового риформинга природного газа и легкой бензиновой фракции, разбавленных водяным паром, с целью получения водорода, направляемого на установку гидрокрекинга. Рабочие параметры печи: давление 2,87 МПа, температура 890°С. Комплексное исследование вырезок металла коллектора печи проводилось с целью определения работоспособности оборудования в связи с локальными перегревами. Корпус выполнен из сталиА516Gr65 (российский аналог стали 16ГС), футерован бетоном и защищен кожухом из коррозионно-стойкой стали. В июне 2014 г. зафиксирован перегрев коллектора до температуры 655°С (рис. 7) продолжительностью не более 70 ч.
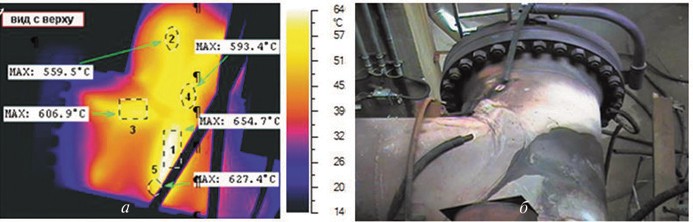
Исследование вырезок металла из зоны перегрева методом оптической металлографии показало, что микроструктура исследованного металла характерна для кремнемарганцовистой стали. В структуре произошла частичная сфероидизация перлита и снижение твердости металла в результате обезуглероживания металла (рис. 8). Данные электронной микроскопии позволили выявить развитие водородной коррозии стали со стороны внутренней поверхности на глубину 20…30 мкм (рис. 9).
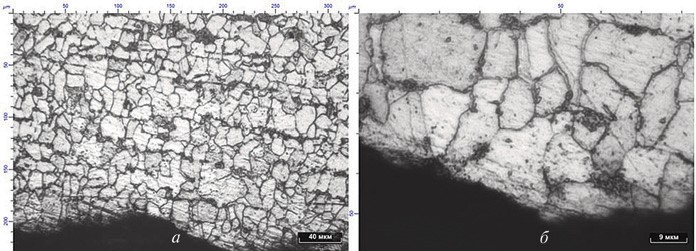
Локальные перегревы в корпусе коллектора, возникшие в зонах несплошности футеровки, привели к развитию водородной коррозии углеродистой стали на участках возникновения прямого контакта металла с горячим синтез-газом. Выявляемые процессы воздействия коррозионноактивной среды являются необратимыми и в случае дальнейшего перегрева могут привести к резкому изменению механических характеристик металла. Указанное позволяет рекомендовать замену коллектора изготовленным из более водородостойкой стали.
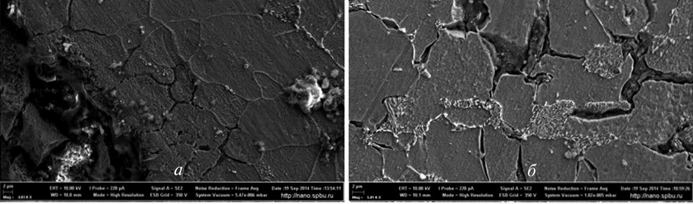
Таким образом, на основании изложенного можно сделать следующие выводы.
Сложившееся положение с экспертизой проектной документации на строительство, реконструкцию, модернизацию и техническое перевооружение технологических печей, как и других объектов нефтеперерабатывающих и нефтехимических предприятий, нуждается в существенной корректировке с целью повышения внимания к качеству выполнения технологических разделов, определяющих безопасность эксплуатации ОПО.
Технический аудит является эффективным инструментом установления отступлений от требований федеральных норм и правил на ОПО и выработки компенсирующих мероприятий.ЭПБ и техническое диагностирование технологических печей, как наиболее опасных составляющих технологических установок, должно выполняться наиболее квалифицированными экспертными организациями с привлечением современного и наиболее эффективного инструментария неразрушающего контроля и лабораторных исследований.
Комплексное исследование причин инцидентов и отказов печного оборудования, прежде всего, змеевиков печей, создает основу повышения надежности прогнозирования работоспособности технических устройств, в том числе технологических печей.
Список литературы
- Федеральные нормы и правила в области промышленной безопасности «Общие правила взрывобезопасности для взрывопожароопасных химических, нефтехимических и нефтеперерабатывающих производств».
- ГОСТ Р 53682–2009. Установки нагревательные для нефтеперерабатывающих заводов. Общие технические требования
- СТО 00220302-002–2011. Методические указания по контролю технического состояния и оценке остаточного ресурса змеевиков трубчатых печей.
- СА-03-004–2009. Трубчатые печи, резервуары, сосуды и аппараты нефтеперерабатывающих и нефтехимических производств. Требования к техническому надзору, ревизии и отбраковке.
- РТМ 26-02-67–84. Методика расчета на прочность элементов печей, работающих под давлением.
- ТУ 1333-078-00220302–2004. Трубы реакционные и их элементы из жаропрочных сталей и сплавов для нефтехи мического высокотемпературного оборудования.
- ТУ 1333-094-00220302–2005. Трубы центробежнолитые из коррозионностойких и жаропрочных сталей и сплавов для реакционных трубчатых печей высокотемпературного нефтехимического оборудования.
- Добротворский А.М., Соколов В.Л., Ульянов П.Г и др. Перспективы применения современных физических методов для оценки состояния конструкционных материалов оборудования нефтеперерабатывающих производств//Актуальные задачи нефтехии и нефтепереработки. СПб.: НПО «Профессионал», 2010.С. 119–131.
- Балутов А.В., Добротворский А.М. Нормативные требования к техническим устройствам, поставляемым на опасные производственные объекты//Химическая техника. 2011. №4. С. 35–37.
- Добротворский А.М., Корнилов В.В., Балутов А.В. и др. ЗАО «НПО «Ленкор»: десятилетие работы в области экспертизы промышленной безопасности технических устройств ООО «Сибур-Нефтехим»//Энергетическая стратегия. 2011. Сентябрь. С. 128–131.
- Добротворский А.М., Шевякова Е.П., Масликова Е.И. и др. Современные методы выявления причин отказов нефтеперерабатывающего и нефтехимического оборудования//Химическая техника. 2013. №12. С. 10–15.
- Добротворский А.М. Диагностика оборудования НПЗ: современное состояние и перспективы//Технополис XXI, 2014. Вып. 30. С. XVIII–XX.
- Добротворский А.M., Масликова Е.И., Андреева В.Д. Влияние эксплуатационных факторов на структуру материала змеевиков технологических печей// Заводская лаборатория. Диагностика материалов. 2014. (принята к печати)
- Постановление Правительства РФ от 16.02.2008 №87 (ред. от 26.03.2014). О составе разделов проектной документации и требованиях к их содержанию.
- СНиП 11-01–95. Инструкция о порядке разработки, согласования, утверждения и составе проектной документации на строительство предприятий, зданий и сооружений.
- ВУПП–88. Ведомственные указания по противопожарному проектированию предприятий, зданий и сооружений нефтеперерабатывающей и нефтехимической промышленности.
- ВНТП 81–85. Ведомственные нормы технологического проектирования. Нормы технологического проектирования предприятий по переработке нефти и производству продуктов органического синтеза.
- Инструкция по проектированию паровой защиты технологических печей на предприятиях нефтеперерабатывающей и нефтехимической промышленности.
- Alvino A., Lega D, Giacobbe F., MazzocchiV., Rinaldi A. Damage characterization in two reformer heater tubes after nearly 10 years of service at different operative and maintenance conditions//Eng. Fail.Anal., 2010. Vol. 17, No. 7–8. Р. 1526–1541.
- Quickel G., Jaske C., Rollins B., BeaversJ. Failure Analysis and Remaining Life Assessment of Methanol Reformer Tubes//J Fail. Anal. and Preven. 2009. Vol. 9. Р. 511–516.
- Tawancy H.M. Degradation of mechanical strength of pyrolysis furnace tubes by high-temperature carburization in a petrochemical plant//Eng. Fail. Anal., 2009.Vol16. No. 7. Р. 2171–2178.