Автор: М.В. Никишин (НПО «ГАКС-АРМСЕРВИС»)
Опубликовано в журнале Химическая техника №5/2017
В сфере обслуживания и ремонта трубопроводной арматуры рыночная экономика получила в наследство, как показали новые экономические отношения, неэффективную систему обслуживания арматуры в плановом порядке. Из отрицательных моментов наиболее очевидными являются следующие:
- необходимость обязательной разборки арматуры для ее осмотра даже в том случае, если видимых отказов нет;
- вероятность некачественной сборки после ревизии вследствие отсутствия достаточного количества квалифицированного персонала (человеческий фактор);
- необходимость обязательного наличия складского запаса деталей для возможной замены после ревизии;
- увеличение трудоемкости работ по обслуживанию со всеми вытекающими экономическими последствиями.
В настоящее время все чаще внедряется метод обслуживания арматуры «по техническому состоянию», который позволяет избавиться от влияния перечисленных выше факторов на стоимость ремонта, одновременно повысив его качество. Это является общемировой тенденцией в эксплуатации ответственных инженерных сооружений, так как можно будет привлекать к ремонтным работам квалифицированных специалистов благодаря сокращению объема работ, в том числе и за счет сокращения объемов испытаний.
Вместе с тем в этом случае повышается важность получения достоверной информации о техническом состоянии трубопроводной арматуры, что обусловливает применение современных средств диагностики.
Существует и вторая положительная сторона ремонта арматуры «по техническому состоянию» – это возможность максимального использования ресурса эксплуатируемой арматуры.
Комплекс мероприятий для решения этой задачи получил название «Управление старением оборудования». Результатом применения этой стратегии кроме продления ресурса арматуры (по разным оценкам до 20%) также должно стать повышение качества ремон-та и обеспечение безаварийной работы трубопроводного оборудования.
Внедрение стратегии управления старением оборудования предполагает использование современных средств контроля и методик диагностирования. В настоящее время существует немалое количество средств диагностики.
Остановимся на некоторых из них.
Метод акустической эмиссии
Данная технология является методом «прослушивания» оборудования при помощи звуковых вибраций, получаемых от датчиков вибраций с пьезоэлектрическим зарядом, которые превращают звуковые волны из механических колебаний в электрические сигналы.
Работа по этому методу достаточно проста и, как правило, полностью автоматизирована благодаря существующим сегодня высокотехнологичным программным продуктам. Данные автоматически сопоставляются с таковыми, полученными ранее, с целью выявления тенденции изнашивания клапана.
Ультразвуковая диагностика
Ультразвуковая диагностика позволяет определить положение и уровень стабильности диска. Для получения необходимой информации о клапанном диске используются рефлектоскоп для улавливания изменений потока и соответствующие передатчики. Данный метод характеризуется как метод зрительного наблюдения
в силу своей возможности отслеживать движение диска. Ультразвуковая диагностика предоставляет наиболее точные, количественно выраженные данные, получаемые при тестировании запорной арматуры.
в силу своей возможности отслеживать движение диска. Ультразвуковая диагностика предоставляет наиболее точные, количественно выраженные данные, получаемые при тестировании запорной арматуры.
Метод генерирования вихревых потоков
Данный метод также используется для осуществления зрительного наблюдения. В этой технологии генерируется электрическое поле, проникающее в не содержащие железо материалы. Помехи в поле позволяют определить вибрирующий клапанный диск.
Метод генерирования вихревых потоков рекомендован к использованию для диагностики клапанов из нержавеющей стали, работающих в условиях высокого давления, а также клапанов быстрого хода.
В таблице приведены основные преимущества и недостатки каждой технологии. Не одно из существующих средств диагностики не дает комплексного представления о реальном состоянии арматуры для определения вида ремонта. Получение полной картины о работе арматуры возможно при условии комбинирования технологий в зависимости от условий тестирования, что диктует необходимость создания универсального прибора.
Предпочтительным является прямой приборный контроль параметров герметичности. При невозможности его осуществления из-за неприспособленности арматуры к прямому диагностированию (отсутствие в конструкции специальных узлов для подключения средств технической диагностики) применяется косвенный метод контроля, например, по отсутствию перепада температур металла, по акустическим шумам и т.д. Кроме того, предпочтительно получение измеренного, а не расчетного диагностического параметра.
Средства технической диагностики подразделяются на стационарные и мобильные. Предпочтение должно отдаваться мобильным аппаратным средствам, что является обязательным условием для диагностирования арматуры, находящейся на трубопроводе.
Мобильные средства технического диагностирования предполагают их периодическое подключение по штатной схеме пневмогидравлических испытаний к диагностируемой арматуре.
Технология | Преимущества | Недостатки |
Ультразвуковая | Дает численную характеристику положения диска и уровня стабильности диска; может быть использована отдельно для получения заключения о состоянии клапана | Область применения ограничена жидкими носителями и по температуре (до 120°С). При более высокой температуре необходим волновод, искажающий показания; требуется повышенный уровень квалификации оператора |
Акустическая | Результаты дают возможность спрогнозировать дальнейший износ; простая система установки и получения данных | Невозможно использование отдельно от других технологий для получения полной картины состояния клапана |
Вихревые токи | Простая система установки; можно использовать при любом носителе; дает возможность наблюдения за полным циклом хода клапана; данные воспроизводятся с характеристикой определенного хода клапана; оптимальный метод диагностики клапанов с быстрым ходом |
Применение ограничено сортами нержавеющей стали |
НПО «ГАКС-АРМСЕРВИС» предлагает мобильную диагностическую систему «СЕЙТРОНИК СИР МД-10-2», предназначенную для оценки технического состояния трубопроводной арматуры в условиях эксплуатации, без демонтажа с трубопровода, и последующего принятия решения о целесообразности проведения ремонта по техническому состоянию. Данная система может быть использована для диагностики технического состояния клиновых, параллельных, двухдисковых задвижек, кранов шаровых DN до 2000 мм, ру до 150 МПа, при наличии дренажных отверстий в корпусе или пробок
в крышке арматуры. В основу процесса диагностирования положен способ испытания арматуры на герметичность воздухом давлением рисп = (0,6 ± 0,1) МПа в соответствии с ГОСТ 33257–2015 «Арматура трубопроводная. Методы контроля и испытаний» и ГОСТ 9544–2015 «Арматура трубопроводная. Нормы герметичности затвора».
в крышке арматуры. В основу процесса диагностирования положен способ испытания арматуры на герметичность воздухом давлением рисп = (0,6 ± 0,1) МПа в соответствии с ГОСТ 33257–2015 «Арматура трубопроводная. Методы контроля и испытаний» и ГОСТ 9544–2015 «Арматура трубопроводная. Нормы герметичности затвора».
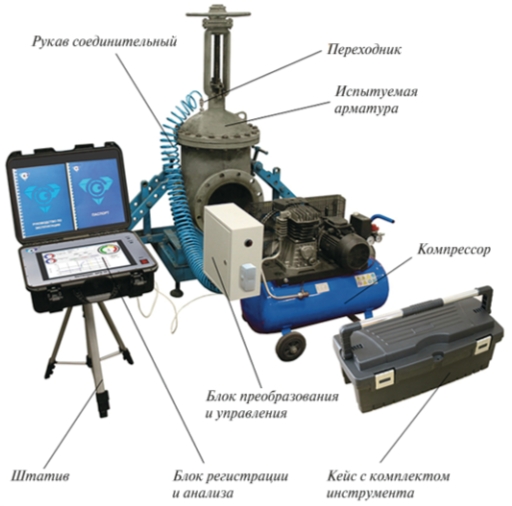
«СЕЙТРОНИК СИР МД-10-2»
Система может применяться для диагностических испытаний трубопроводной арматуры без изъятия из трубопровода в нефтегазодобывающей и нефтехимической отраслях промышленности, транспортно-трубопроводных системах; атомной энергетике и др.
Технические данные испытаний
DN, мм | PN, МПА | Давление испытания, МПа | Испытательная среда | Продолжительность испытаний, с |
300 | 0,6 | 0,6 | Воздух | 580 |
Испытания на утечки
Максимально достигнутое давление при испытаниях, МПа | 0,6 | % падения давления |
Время выдержки под давлением, с | 180 | 73 |
Время контроля герметичности, с | 340 | |
Давление по истечению времени контроля, МПа | 0,38 | |
Скорость падения давления за счет утечки после изготовления, МПа/с | 0 | |
Скорость падения давления за счет утечки после эксплуатации, МПа/с | 0,00041 |
Сравнительные диаграммы нормативных, исходных текущих данных диагностических испытаний
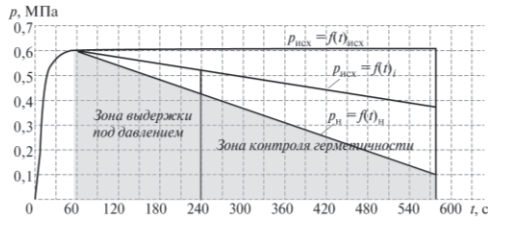
Процесс диагностического тестирования с применением диагностической системы «СЕЙТРОНИК СИР МД-10-2» состоит из следующих этапов:
Первичного тестирования изготовленного изделия с последующим документированием и занесением данных в паспорт («ЭТАП 1»);
Текущего тестирования герметичности после установки арматуры на трубопровод в соответствие со сроками их проведения, установленными принятым регламентом («ЭТАП 2»).
Сравнительного анализа данных первичного, текущего и допустимого значений герметичности для выработки окончательного решения по началу ведения ремонта («ЭТАП 3»).
Каждый этап оформляется протоколом, в котором указываются дата испытаний, заказчик, тип изделия, изготовитель, используемое для испытаний оборудование и другие необходимые сведения, а также технические данные испытаний и диаграмма диагностических испытаний. Пример графического анализа диагностических испытаний приведен на рис. 2.
Очевидно, что приобретение арматуры со встроенными системами диагностирования или приобретение переносных средств диагностики для эксплуатирующих организаций является сознательным вложением существенных денежных средств. Современное направление развития диагностики состояния арматуры настоятельно диктует сделать правильный выбор между двумя вариантами:
1. Минимизация первоначальных вложений в арматуру и последующие высокие эксплуатационные расходы, связанные с ремонтом.
2. Максимальные вложения при приобретении арматуры с возможностью диагностирования и минимальные расходы при эксплуатации.