Автор: С.В. Афанасьев, Ю.Н. Шевченко, Е.А. Белова (Тольяттинский госуниверситет),
С.П. Сергеев (ОАО “ГИАП”), Г.К. Лавренченко (УА «СИГМА»)Опубликовано в журнале Химическая техника №5/2017
Современные установки синтеза аммиака, как правило, базируются на циркуляционных схемах, т.е. часть азотоводородной смеси непрерывно превращается в колонне синтеза в аммиак, который выводится из установки, а непрореагировавшие компоненты выделяются из реакционной смеси и снова подаются в реактор. В циркуляционных газах растет содержание инертных примесей – аргона, гелия, криптона, ксенона, т.е. инертных газов по отношению к реакции синтеза аммиака, что снижает скорость реакции, а, следовательно, и технико-экономические показатели. В связи с этим часть циркуляционных, так называемых продувочных газов (ПГ), непрерывно выводится из цикла. В таких установках синтеза аммиака оптимальным считается содержание инертных примесей в циркуляционных газах в пределах 9–13 % об. При этом расход ПГ, например, на установке производительностью по аммиаку 1360 т/сут. (паспортная производительность отечественной установки модели АМ-76), может доходить до 8000 м3/ч, т.е. 140 м3/ч ПГ на 1 т аммиака [1–3]. Вместе с ПГ из цикла синтеза аммиака помимо инертных компонентов выводится часть непрореагировавшей азотоводородной смеси.
В результате дросселирования жидкого аммиака из конденсационной колонны в сборник жидкости образуется паровая фаза, содержащая инертные газы, азотоводородную смесь и значительное количество аммиака – танковые газы (ТГ). ТГ направляют в испаритель с целью утилизации аммиака путем его низкотемпературной сепарации. Для поддержания в циркуляционном газе постоянного содержания инертных газов ТГ выводятся из установки. Состав танковых газов указан в табл. 1. Смесь танковых и продувочных газов в большинстве отечественных установок синтеза аммиака используют как топливный газ в печи риформинга, что способствует образованию больших количеств оксидов азота, выбрасываемых в окружающую среду [4].
Системы выделения водорода из сбросных газов (ПГ и ТГ) производства аммиака включены во все усовершенствованные установки зарубежного и немногочисленные отечественного производства. Это наиболее реальный путь сокращения энергосырьевых затрат, позволяющий либо на 2–3 % повысить выход аммиака при том же расходе сырья, либо на 3–7 % сократить потребление сырья при том же выпуске конечного продукта. Вместе с тем сбросные газы являются ценным сырьем для производства редких газов, поскольку в них наряду с водородом, азотом и метаном содержится до 10% аргона и в сотни раз больше криптона и ксенона, чем в воздухе. Свойства этих газов представлены в табл. 2.
В настоящее время существует множество способов переработки водородсодержащих газов, что объясняется различием составов газов и спецификой конкретных производств. По природе разделительного эффекта способы выделения водорода могут быть классифицированы как основанные на фазовых равновесиях: абсорбция (газ–жидкость); адсорбция (газ–твердое тело); низкотемпературная конденсация и ректификация (газ–жидкость); диффузия газов через мембраны. Каждый из указанных способов выделения водорода из водородсодержащих газов имеет характерные преимущества, недостатки и предпочтительные области применения.
Остановимся на мембранном методе разделения газов, получившем широкое распространение в нашей стране и за рубежом.
Таблица 1
Характеристика продувочных и танковых газов агрегатов синтеза аммиака АМ-76
Тип газа | Объемный расход, тыс. м3/ч | Давление, МПа |
Состав, % об. | ||||
NH3 | H2 | N2 | CH4 | Ar | |||
Продувочные | (4…6)/ (7,3…8,4) |
(20…24)/ (28…31) |
(1,5…7)/ (1,15…2,03) |
(58,8…64)/ (60,89…59) |
(15…22)/ (19,66…19,85) |
(8…13)/ (12,7…14,38) |
(4…7,5)/ (5,17…4,93) |
Танковые | (1,5…2,2)/ (1,4…2,4) |
(1,5…1,8)/ (2,1…7,58) |
(8…12)/ (4,54…10,75) |
(44,5…48)/ (39,19…46,77) |
(14,82…15,2)/ (14,34…19,66) |
(26…29)/ (28…31,06) |
(5…7,5)/ (4,46…5,1) |
Примечание. 1. В числителе – данные ОАО «Тольяттиазот», в знаменателе – литературные данные [5]. 2. Содержание редких газов в ПГ, % об.: <0,0001 ксенон; <0,001 криптон; <0,4 гелия. |
Таблица 2
Некоторые физические свойства основных компонентов ПГ и ТГ установок синтеза аммиака
Параметр | Гелий, He | Водород, H2 | Неон, Ne | Азот, N2 | Аргон, Ar | Метан, CH4 | Криптон, Kr | Ксенон, Xe | Аммиак, NH3 |
Температура кипения при атмосферном давлении, К | 4,2 | 20,4 | 27,1 | 77,4 | 87,3 | 111,7 | 119,8 | 165,0 | 239,7 |
Критическая температура, К | 5,2 | 33,18 | 44,4 | 126,2 | 150,8 | 190,77 | 209,39 | 289,75 | 405,6 |
Критическое давление, МПа | 0,23 | 1,3 | 2,65 | 3,4 | 4,9 | 4,63 | 5,49 | 5,82 | 11,3 |
Принцип работы мембранных систем заключается в разной скорости проникновения компонентов газа через вещество мембраны. Движущей силой разделения газов является разница парциальных давлений на различных сторонах мембраны. Важную роль играет и тот факт, что разделяемые газы по скорости проникновения через газоразделительный слой мембраны условно делятся на «быстрые» и «медленные».
Выбор оптимальных рабочих параметров установок по выделению водорода, базирующихся на указанном принципе, зависит от состава перерабатываемого газа и материала мембраны (носителя и нанесенного на него газоразделительного слоя).
Верхняя температура исходного водородсодержащего газа, поступающего в мембранный блок, ограничена максимально допустимой рабочей температурой мембраны. Так, для наиболее часто применяемого материала мембраны – ацетата целлюлозы – максимально допустимая рабочая температура составляет 60°С. Нижний уровень ограничен температурой точки росы отходящего потока.
Также необходимо учитывать, что при высокой концентрации легко проникающего компонента в исходном газе в процессе разделения из-за эффекта дросселирования может значительно понижаться температура как пермеата, так и ретанта (пермеат – компонент или группа компонентов исходного газа, проникающего через газоразделительный слой мембраны; ретант – остаточный газ, не проникающий через мембрану). В связи с этим разделение таких газов проводят не в одном, а в нескольких последовательно расположенных мембранных аппаратах, при этом между аппаратами предусматривают установку теплообменников для подогрева разделяемой газовой смеси.
Давление как исходного, так и продуктового и сбросного потоков оказывает существенное влияние на коэффициент извлечения водорода и чистоту конечного продукта. Указанный коэффициент определяется как отношение количества продуктового водорода к количеству водорода, содержащегося в исходном газе [1].
С понижением давления пермеата увеличивается чистота продуктового водорода. В действительности рабочее давление вырабатываемого Н2 выбирается в зависимости от способа дальнейшего его использования.
В настоящее время в ОАО «Тольяттиазот» эксплуатируются семь агрегатов аммиака, один из которых, как правило, поочередно останавливается для планового обслуживания. Продувочные газы по общему коллектору поступают на вход двух параллельно работающих мембранных установок (рис. 1).
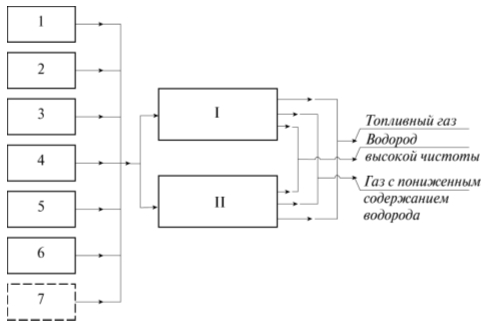
на аммиачном производстве ОАО «Тольяттиазот»:
1…7 – агрегаты синтеза аммиака;I, II – мембранные установки
Установки поставлены фирмой «Монсанто», проектная мощность каждой из них составляет 4000 нм3/ч в пересчете на чистый водород. Продуктами, выдаваемыми данными мембранными установками, являются водород высокой чистоты (97–98 % об.) давлением 2,6…2,8 МПа и газ с пониженным содержанием водорода (87–89 % об.) давлением 2,6…2,8 МПа. Кроме того, в процессе разделения продувочных газов в мембранных установках образуется остаточная газовая смесь, обедненная водородом (топливный газ), которая после снижения давления до 1,0… 1,2 МПа возвращается в агрегаты аммиака для сжигания в горелках трубчатых печей парового риформинга.
По реализованному проекту водород высокой чистоты и газ с пониженным содержанием водорода подаются в ОАО «КуйбышевАзот» на производство капролактама либо используются на собственные нужды в производствах аммиака ОАО «Тольяттиазот», поступая на всасывание компрессоров синтез-газа агрегатов 1 – 7 (рис. 2) для получения дополнительного количества аммиака.
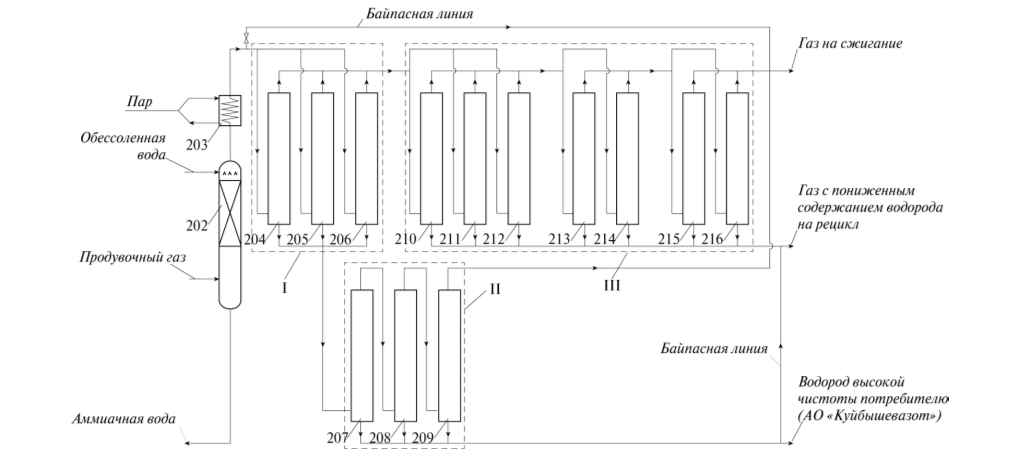
202 – скруббер;203 – подогреватель; 204…216 – мембранные картриджи «Prism»;
I, II, III– соответственно первая, вторая и третья ступени извлечения водорода
Давление в общем коллекторе продувочных газов поддерживается на уровне 23…27 МПа, однако его максимальное значение для применяемых мембранных картриджей типа «Prism» ограничено на уровне 14 МПа. По указанной причине перед подачей продувочных газов на выделение водорода его давление снижают до 10,5…14,0 МПа.
Выделение водорода из ПГ в мембранных установках ОАО «Тольяттиазот», укомплектованных мембранными картриджами типа «Prism», осуществляется следующим образом.
Поток подготовленного газа поступает в три группы картриджей, образующих трехступенчатую систему извлечения водорода (см. рис. 2).
Пермеат, прошедший через пористые стенки половолоконных мембран первой ступени картриджей 204, 205 и 206, имеет давление 5,4…6,4 МПа и содержит 93–94% об. водорода. Он собирается в общий коллектор и поступает во вторую ступень картриджей «Prism». Вторая ступень состоит из трех картриджей 207, 208 и 209, соединенных последовательно. В этих картриджах пермеат обогащается водородом и с концентрацией не менее 97% об. под давлением 2,6…2,8 МПа выводится из установки. Поток газа, не проникший через стенки половолоконных мембран (ретант) в картриджах первой ступени 204, 205 и 206, направляется в картриджи третьей ступени 210 – 216. Третья ступень состоит из семи картриджей, которые составляют три последовательно соединенные группы. Выходящий из третьей ступени пермеат под давлением 2,6…2,8 МПа содержит не менее 87% об. водорода и подается на рециркуляцию.
Ретант из третьей ступени после снижения давления до 1,0…1,2 МПа соединяется с ретантом второй ступени, после чего смешанный поток направляется в топливную систему аммиачных агрегатов.
В результате длительной эксплуатации мембранных установок установлено, что коэффициент извлечения и максимально достижимая чистота продуктового водорода близки соответствующим значениям, получаемым в криогенных установках. В качестве исходного сырья может быть использован газ с низкой концентрацией водорода. Однако изменение состава исходного газа в процессе эксплуатации мембранной установки без корректировки ее схемы (числа мембранных картриджей в каждой ступени) может привести к значительному снижению коэффициента извлечения водорода, его чистоты и, соответственно, ухудшению энергетических характеристик.
Для более полного извлечения водорода из сбросных газов и сокращения воздействия отходящих газов агрегатов аммиака на окружающую среду мембранные установки должны быть дополнены криогенными. Это позволит дополнительно извлекать водород и инертные газы и улучшить экономику производства.
Список литературы
1. Головко Г.А. Установки для производства инертных газов. Л.: Машиностроение, 1974. 384 с.
2. Пат. на полезную модель RU №87504. МПК F25J. Установка переработки продувочных и танковых газов.
3. Афанасьев С.В., Рощенко О.С., Лавренченко Г.К., Копытин А.В. Энергосберегающие технологии переработки продувочных газов производства аммиака//Вектор науки Тольяттинского государственного университета. 2012. №1(19). С. 17–19.
4. Афанасьев С.В., Трифонов К.И. Физико-химические процессы в техносфере. Учебник. Самара. Изд-во Самарского научн. центра РАН, 2014. 148 c.
5. Справочник азотчика/Под общ. Ред. Е.Я. Мельникова. М.: Химия, 1986. 512 с.