Автор: Д.С. Шелестов (ОАО «Волгограднефтемаш»).
Опубликовано в журнале Химическая техника №12/2016
ОАО «Волгограднефтемаш» – предприятие с полным технологическим циклом изготовления оборудования.
Наличие собственных конструкторских и технологических служб позволяет оперативно осуществлять технические проработки и подготовку производства к выполнению заказов любой сложности. Предприятием накоплен опыт совместной работы с ведущими российскими и межднародными инжиниринговыми компаниями по производству оборудования, оно имеет аттестацию по ASME.
ОАО «Волгограднефтемаш» специализируется на выпуске различного оборудования для нефтегазохимического комплекса: нефтеаппаратуры (колонны, реакторы, блочное оборудование, коксовые камеры, сепараторы, теплообменники, устройства приема и запуска ВТУ и др.); трубопроводной арматуры (шаровые краны, клапаны обратные осесимметричные, затворы обратные); центробежных насосов (температура перекачиваемой рабочей среды от –80 до +420С).
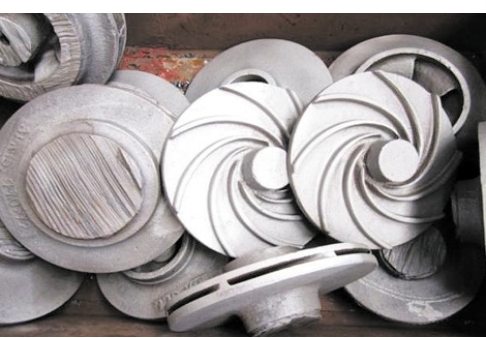
Одним из основных приоритетов предприятия является обеспечение необходимой надежности выпускаемого оборудования.
Наличие собственной аттестованной лаборатории позволяет проводить практически все виды разрушающего и неразрушающего контроля, требуемые при изготовлении продукции. Лаборатория имеет самое современное оборудование для определения химического состава и механических свойств материалов, проведения металлографических исследований и других видов различного контроля.
Специалисты по неразрушающим методам контроля имеют аттестацию по 2-му и 3-му уровням как по отечественным нормам, так и по нормам американского кода ASME. Возможности лаборатории позволяют производить рентгенографический контроль, гамма-контроль, ультразвуковую дефектоскопию, ультразвуковую толщинометрию, контроль проникающими жидкостями, контроль магнитопорошковым методом, акустическую эмиссию и контроль с помощью гелиевого течеискателя.
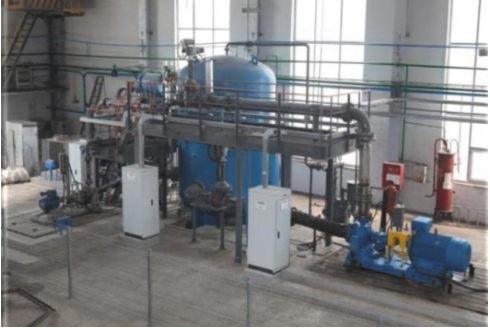
Новые мероприятия, внедряемые в ОАО «Волгограднефтемаш», для повышения надежности выпускаемого оборудования
1. Среди новых методов контроля, внедряемых в ОАО «Волгограднефтемаш», следует отметить ультразвуковой дифракционно-временной метод НК (Time of Flight Diffraction – ToFD) для контроля сварных соединений. Метод основан на приеме как продольных, так и поперечных волн, дифрагированных на вершинах дефекта. Главная информационная характеристика – время прихода сигнала. Время прохождения волны является мерой оценки высоты несплошности, что позволяет измерить дефект.
Размер несплошности всегда определяется временем прохождения дифракционных сигналов.
Дифракция волн – явление, которое можно рассматривать как отклонение от законов геометрической оптики при распространении волн. Для объяснения этого явления необходимо воспользоваться принципом Гюйгенса, в соответствии с которым каждую частицу среды, приходящую в колебание вследствие распространения первичной падающей волны, можно рассматривать как точечный источник, излучающий вторичную элементарную сферическую волну.
Для излучения и приема волны с каждой стороны сварного шва используются два наклонных датчика продольной волны. ToFD обнаруживает образ дефекта по сигналам, дифрагированным с его краев. Для большинства случаев достаточно контроля всей толщины за один проход. Для объектов большой толщины требуется несколько проходов.
Метод ToFD является более чувствительным к дефектам плоскостного типа трещин, чем метод радиографического контроля. Так, сравнение результатов контроля качества сварных швов методами ToFD и радиографии показало, что выходящая на поверхность трещина в сварном соединении толщиной 50 мм не была обнаружена с помощью радиографического метода. Кроме того, контроль с помощью ToFD обеспечивает возможность измерений глубины залегания дефекта, а также получение информации о его высоте.
Наиболее существенные преимущества метода ToFD:
- возможность достижения более высокой точности при проведении измерений (как правило, ± 1 мм, при повторном обследовании ± 0,3 мм);
- независимость обнаружения дефекта от его углового положения;
- измерение параметров дефекта основано на времени прохождения пути дифракционных сигналов и не зависит от амплитуды сигнала;
- высокая производительность контроля, так как сканирование проводится вдоль одной линии с контролем всего объема шва;
- документирование и хранение результатов контроля;
- 100%-ная воспроизводимость результатов контроля;
- измерение величины эрозии металла внутренней поверхности;
- альтернатива радиационному методу НК.
- возможность применения во время эксплуатации. 2. На собственном литейном производстве предприятия для обеспечения качества литых заготовок внедрена линия литья по газифицируемым моделям. Она состоит из двух комплексов, один из которых предназначен для производства моделей отливок из пенополистирола, а другой – для получения литых заготовок.
В стадии внедрения находится также линия ХТС (получения стержневой оснастки с помощью холодно-твердеющих смесей).
Проверка качества литых заготовок деталей корпусной группы насосного оборудования осуществляется на участке для испытаний на герметичность с использованием гелия, что позволяет на ранних стадиях производства выявить дефекты литья.
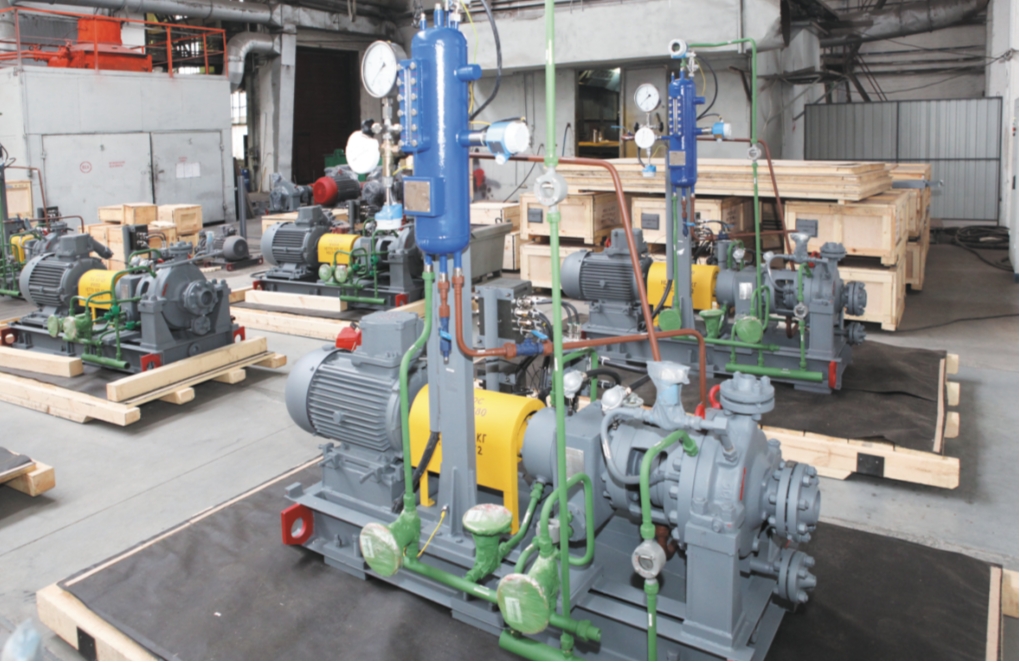
Отделами главного конструктора и главного металлурга осваиваются новые литейные марки стали аустенитно-ферритного класса (дуплексные). 3. Каждый насосный агрегат проходит обкатку на стенде СИД 00.00.00. На стенде можно проводить испытания с учетом всех требований промышленной безопасности, используется диагностическое оборудование, аналогичное применяемому оборудованию, установленному на насосных станциях и установках нефтеперерабатывающих комплексов. В комплект стенда входит операторная с системой управления испытаниями и диагностики насосного оборудования.
В настоящее время стенд модернизируется для внедрения системы подключения электродвигателей с напряжением 6000 В, что позволит проводить испытания насосных агрегатов большой мощности на рабочей частоте вращения ротора насоса. 4. Для минимизации отказов в процессе эксплуатации на площадке у заказчика насосы изготавливаются с полной обвязкой КИП до соединительных коробок, что позволяет осуществлять их ремонт по фактическому состоянию. Это дает возможность увеличить время эксплуатации между текущими ремонтам и существенно повысить надежность оборудования.