Автор: А.Л. Прончаков, С.В. Панченко, В.А. Платонов, Ю.Н. Тюрин, М.С. Трещева, С.В. Дьяконов (ОАО «НОРЭ»).
Опубликовано в журнале Химическая техника №1/2015
Специалистами ОАО «НОРЭ» проведено обследование шарового резервуара для хранения жидкого аммиака вместимостью 2000 м3, изготовленного ПО «Уралхиммаш» по типовому проекту ЦНИИПСК им.
Мельникова для одного из предприятий агрохимического комплекса после 31 года эксплуатации.
Монтаж резервуара был осуществлен по месту установки из заводских поставочных блоков. Оболочка шарового резервуара состоит из 24 лепестков, которые по условиям транспортировки после изготовления были разрезаны на две части (нижняя часть на 0,5 м длиннее верхней), и двух крышек, состоящих из трех элементов каждая. Элементы оболочки резервуара изготовлены методом вальцовки. Протяженность монтажных швов шаровой оболочки резервуара составляет 620 м. Материал оболочки – сталь 09Г2С, сварка выполнена с применением присадочной проволоки Св-08ГА и электродов УОНИ 13/55. Толщина стенки оболочки резервуара – 20,0 мм, сварка – двухсторонняя с полным проплавлением. В соответствии с проектом была произведена термообработка угловых и тавровых швов вварки патрубков и горловин в крышки оболочки. Резервуар находится в эксплуатации с 1982 г., с момента пуска и по настоящее время эксплуатируется при давлении до 0,6 МПа и температуре продукта до 13°С.
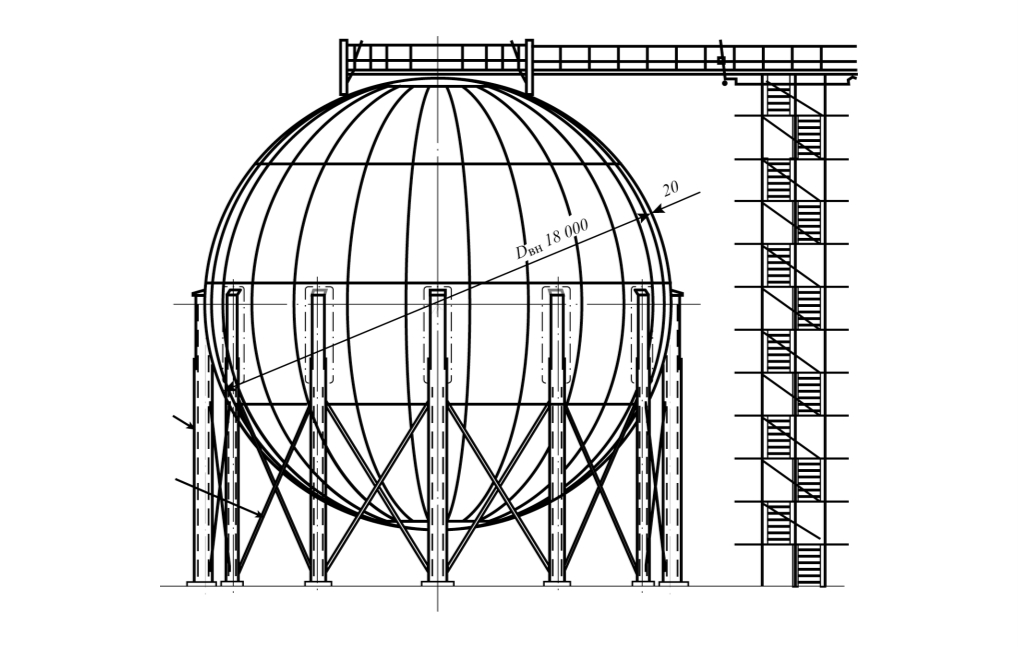
Начиная с 1991 г., в связи с исчерпанием проектного срока службы периодически проводились обследования резервуара.
В 1991 г. специалистами ЦНИИ-ПСК, проводившими первое диагностирование резервуара, были обнаружены многочисленные дефекты в виде трещин и коррозионных раковин различной глубины и протяженности с внутренней стороны оболочки резервуара, связанные с коррозионным растрескиванием в зоне сварных швов.
При последующих обследованиях, проводимых через каждые 4 года, фиксировались дефекты сварных швов, подлежащие устранению с применением сварки. При этом число и степень критичности дефектов с увеличением срока эксплуатации тенденции к росту не проявляли.
После проводимых ремонтов резервуар вновь допускался к эксплуатации. Аварий и нештатных ситуаций за весь срок службы резервуара не наблюдалось.
Настоящее диагностирование было выполнено в рамках экспертизы промышленной безопасности резервуара в связи с окончанием срока действия ранее выданного заключения экспертизы. Объем и методы диагностирования были приняты в соответствии с РД 03-380–00 «Инструкция по обследованию шаровых резервуаров и газгольдеров для хранения сжиженных газов под давлением» [1].
Были выполнены визуальный и измерительный контроль металлоконструкций резервуара, контроль величины осадки фундамента, измерения отклонений от проектного положения опорных стоек оболочки резервуара, измерения толщины и твердости металла оболочки. Все измеренные величины и параметры находились в пределах, допустимых действующими нормами и проектом.
Таким образом, нагрузки на оболочку резервуара соответствуют проектным.
В качестве метода, определяющего объем и содержание дефектоскопического контроля, был применен метод акустической эмиссии.
Акустико-эмиссионный контроль (АЭК) выполнялся при пневматическом нагружении оболочки газообразным аммиаком, подаваемым с испарителя склада аммиака. Такой способ нагружения был выбран для обеспечения возможности быстрого набора испытательного давления и отсутствия возможных помех от нагружающего оборудования. АЭК проведен с использованием 32-х канального диагностического комплекса «Эксперт-2014» (производство НПО «Алькор», г. Дзержинск).
При акустико-эмиссионном контроле были зафиксированы источники акустической эмиссии 2-го класса (активные) от дефектов, представляющих собой раковины в наплавленном металле с внутренней стороны оболочки, появление которых было связано с поверхностным растрескиванием и выкрашиванием металла. Была выполнена плавная выборка мест локализации раковин с последующим дефектоскопическим контролем методом цветной дефектоскопии. Заварка выборок не проводилась в связи с тем, что остаточная толщина стенки в местах выборок превышала расчетную.
По результатам проведенного ремонта работоспособность была восстановлена на приемлемом уровне.
Следующим этапом диагностирования является установление срока дальнейшей безопасной эксплуатации шарового резервуара, которая определяется наиболее значимыми повреждающими факторами, действующими на его конструкцию.
В нашем случае фактором, определяющим долговечность резервуара, является повреждение сварных швов коррозионным растрескиванием.
Согласно приложению к ГОСТ 9.901.1–89 «Металлы и сплавы. Общие требования к методам испытаний на коррозионное растрескивание» [2], в котором даются определения терминов, применяемых в стандарте, коррозионное растрескивание – поражение металла, вызванное одновременным воздействием коррозионной среды и номинально статическим растягивающим напряжением, в результате которого обычно образуются трещины.
Опасность коррозионного растрескивания заключается в том, что коррозия не приводит к существенному уносу металла и появлению явных коррозионных поражений, сохраняя видимость неповрежденного металла. При этом образующиеся дефекты имеют наиболее опасный характер хрупкой трещины.
Проблема коррозионного растрескивания сварных швов шаровых резервуаров для хранения аммиака активно обсуждалась, начиная с 70-х годов ХХ века. Так, в 1978 г., по результатам специального совещания в ГИАП, производителей шаровых резервуаров обязали проводить термическую обработку узлов вварки патрубков, в которых концентрация напряжений является наибольшей за счет резкого изменения формы нагруженного сечения. Однако проблема коррозионного растрескивания стыковых сварных швов таким образом не была решена.
Случаи образования трещин в сварных швах оболочек шаровых резервуаров для жидкого аммиака продолжались регистрироваться регулярно, в том числе и до выработки нормативного срока службы (12 лет).
Шаровые резервуары традиционно рассчитываются по предельным нагрузкам, тогда как расчет на прочность большей части емкостной химической аппаратуры проводится по допускаемым напряжениям.
Расчет по предельным нагрузкам, безусловно, позволил снизить металлоемкость изготовления, массу и соответственно стоимость шаровых резервуаров. Для сред, не оказывающих коррозионного воздействия на металл, такой подход вполне оправдан. Однако в случае резервуаров для жидкого аммиака снижение запаса прочности сыграло негативную роль.
Эмпирическим путем установлено, что интенсивное развитие коррозионного растрескивания в среде жидкого аммиака происходит в том случае, если растягивающие напряжения составляют ~30–50% фактического предела текучести материала. Таким образом, для исключения возможности коррозионного растрескивания в среде жидкого аммиака толщина стенки должна в 2–3 раза превышать необходимую по условию прочности.
Увеличенный запас прочности, который имеют горизонтальные резервуары или, например, транспортные цистерны для перевозки жидкого аммиака позволяет полностью избежать коррозионного растрескивания либо свести к минимуму вероятность его возникновения. На предприятиях агрохимического комплекса имеется более чем сорокалетний опыт использования горизонтальных резервуаров для жидкого аммиака вместимостью 100 м3 без возникновения явлений коррозионного растрескивания.
Такая существенная разница между расчетной и минимально необходимой толщиной стенки связана с наличием локальных напряжений, возникающих в конструктивных узлах оболочки шарового резервуара. Увеличение локальных напряжений в сварной оболочке определяется многими факторами. Среди основных следует назвать: наличие значительных остаточных напряжений после сварки в наплавленном металле и околошовной зоне; наличие дефектов сварных швов типа подрезов, непроваров, цепочек пор и т.п.; наличие дефектов формы сварных узлов типа смещения кромок или угловатости швов, объемные напряжения в оболочке из-за большого числа сварных соединений и общего отклонения от идеальной сферической формы; наличие циклической нагрузки; температура хранимого аммиака (в изотермических резервуарах, работающих при температуре около –33°С явлений коррозионного растрескивания не наблюдается).
Увеличение толщины стенки и металлоемкости шарового резервуара сводит на нет все экономические преимущества его использования, поэтому наилучшим способом борьбы с развитием коррозионного растрескивания следует считать меры, направленные на уменьшение локальных и внутренних напряжений в металле.
Наиболее эффективным способом снятия остаточных напряжений является термообработка.
Термообработка стыковых сварных швов оболочки рассматриваемого шарового резервуара, как заводских, так и монтажных, не проводилась, поскольку на момент изготовления (1982 г.) в нормативных документах не было соответствующих требований.
Действующими на сегодняшний день техническими условиями на изготовление шаровых резервуаров ТУ 3615-018-00217320–2006 «Резервуары шаровые. Технические условия» [3] для сред, вызывающих коррозионное растрескивание, предусмотрена термическая обработка сварных соединений. При этомГОСТ Р 52630–2012 [4] жидкий аммиак отнесен с средам, вызывающим коррозионное растрескивание.
Наиболее эффективно снимает остаточные напряжения термообработка в режиме высокого отпуска.
Предпочтительной является объемная термообработка смонтированного резервуара, которая позволяет нивелировать не только местные, но и объемные напряжения в оболочке.
Имеется опыт внепечной термической обработки оболочки шарового резервуара, осуществленный специалистами ОАО «ВНИИПТхимнефтеаппаратуры» (г. Волгоград).
Способ внепечной термической обработки заключался в нагреве внутреннего объема изделия, предварительно теплоизолированного с наружной поверхности продуктами сгорания жидкого топлива в процессе работы специальных теплогенераторных устройств. Объемная термообработка была выполнена на вновь смонтированном шаровом резервуаре вместимостью 3000 м3.
При определенных условиях в процессе проведения ремонта возможно проведение такого способа термообработки на уже действующих резервуарах.
Другой способ уменьшения локальных напряжений предложен специалистами ЦНИИПСК им. Мельникова (Москва). Способ сводится к снятию выступа усиления сварных швов с внутренней стороны оболочки резервуара заподлицо с основным металлом. Помимо уменьшения концентрации напряжений из-за местного отклонения формы и наличия уже существующих микроскопических повреждений поверхностного слоя металла, снятие усиления позволяет облегчить проведение ультразвукового контроля сварных швов [5]. Снятие усиления сварных швов резервуара частично было выполнено при проведении первого технического диагностирования в 1991 г., что позволило существенно сократить число вновь образующихся дефектов и значительно увеличить ресурс резервуара.
Третий способ уменьшения сварочных напряжений в поверхностном слое наплавленного металла сварных швов, предложенный специалистами Института электросварки им. Е.О. Патона НАН Украины, заключается в выполнении наружного (облицовочного) слоя сварного шва аустенитно-мартенситным присадочным материалом (типа Х10Н10) с низкой температурой фазового перехода. При сварке проволокой отмеченного состава процесс межфазного перехода аустенита в мартенсит приводит к расширению металла шва на конечной стадии охлаждения и, как следствие, к возникновению благоприятных остаточных напряжений сжатия в зоне сварного соединения [6].
Последний способ не был апробирован для сварки именно шаровых резервуаров для аммиака, но может быть использован при проведении восстановительного ремонта участков сварных швов с трещинами, так как жидкий аммиак не вызывает электрохимического растворения стали в разнородных сварных соединениях.
Поскольку ни один из предлагаемых способов не мог быть реализован, продление срока дальнейшей эксплуатации было осуществлено в соответствии с уже сложившейся практикой. Межремонтный пробег резервуара в среднем составляет 4 года. За это время дефекты, образующиеся в наплавленном металле, достигают размеров, позволяющих надежно выявлять их с применением методов неразрушающего контроля и рекомендовать их к проведению ремонта. В то же время ни один из выявленных за весь период эксплуатации дефектов не привел к появлению течи или другой критической неисправности резервуара.
Список литературы
- РД 03-380–00. Инструкция по обследованию шаровых резервуаров и газгольдеров для сжиженных газов под давлением.
- ГОСТ 9.901.1–89. Металлы и сплавы. Общие требования к методам испытаний на коррозионное растрескивание.
- ТУ 3615-018-00217320–2006. Резервуары шаровые. Технические условия.
- ГОСТ Р 52630–2012. Сосуды и аппараты стальные сварные. Общие технические условия.
- Баско Е.М. Ресурс эксплуатации шаровых резервуаров вместимостью 2000 м3 для жидкого аммиака//Монтажные и специальные работы в строительстве. 2007. №12.
- Ковальчук В.С., Кныш В.В., Позняков В.Д., Касаткин С.Б. Способ повышения циклической долговечности и ресурса сварных стальных конструкций//Автоматическая сварка. 2007. №3.