Автор: С.А. Селиванов (ООО «КИНЕФ»).
Опубликовано в журнале Химическая техника №11/2016
В декабре 2013 г. в ООО «КИНЕФ» завершено строительство крупнейшего в Европе комплекса глубокой переработки нефти на базе гидрокрекинга вакуумного газойля. На комплексе эксплуатируется большое количество насосно-компрессорного оборудования разных производителей.
Основные виды оборудования и арматуры, применяемого на комплексе ГПН:
Оборудование | Всего | Импорт | Россия |
Печное оборудование | 15 | 15/100% | 0 |
Аппаратура колонная и емкостного типа, включая реакторы и котлы | 640 | 446/70 | 194/30% |
Аппаратура теплообменная | 326 | 283/87% | 43/13 |
Аппараты воздушного охлаждения | 46 | 45/98% | 1/2% |
Насосно-компрессорное оборудование и приводы АВО | 657 | 651/99% | 6/1% |
Компрессоры | 32 | 32/100% | 0 |
Вентиляционные установки | 455 | 301/66% | 154/34% |
Арматура запорная | 46972 | 28184/60% | 18788/40% |
Регулирующие клапаны и отсекатели | 1744 | 1744/100% | 0 |
Арматура предохранительная ППК | 1087 | 797/73% | 290/27% |
В период комплексного опробования, испытания и пуска оборудования возникало множество технических задач. В предлагаемой вниманию читателей статье рассказывается опыте эксплуатации и импортозамещения поршневых и центробежных компрессоров установки гидрокрекинга.
Компрессор поз. С-2003 подпиточного водорода 6-цилиндровый трехступенчатый оппозитный производен фирмой Thomassen С.S. по лицензии компании Mitsui E.S.
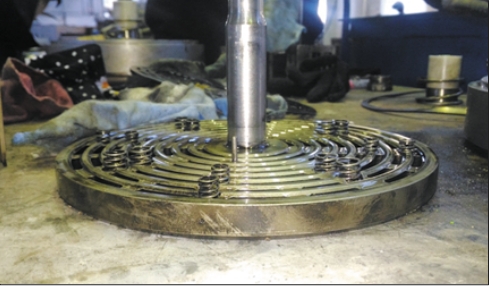
С 2014 г. зафиксировано не менее 16 выходов из строя компрессоров этой позиции по причине разрушения пластин клапанов нагнетания первой ступени. Компрессор был укомплектован пластинчатыми клапанами известной зарубежной компании, сценарий развития разрушения всегда один и тот же – повышение температуры стакана разрушаемого клапана (преимущественно самого дальнего от коленвала) с одновременной просадкой давления и расхода от первой ступени. На второй и третей ступенях с данными клапанами были лишь единичные несистемные случаи выхода из строя. При разборке клапанов первой ступени было выявлено разрушение пластин на периферии, что и вызывало перепуск газа.
В качестве основных причин данных разрушений рассматривались:
- разрушение пластин на этапе технологического режима с 50%-ной загрузкой компрессора, когда в работе находятся клапаны, ближние к коленвалу, а дальние испытывают на себе хаотичное движение газа. Данное предположение частично подтвердилось, так как наблюдался рост температуры дальних клапанов практически сразу после повышения загрузки до 100%. Было решено повысить загрузку до 100% сразу после пуска компрессора с байпасированием излишнего количества газа на прием, но пластины продолжали разрушаться;
- залипание пластин из за большого количества подаваемого масла в цилиндр (основная версия производителя). Эта версия не подтвердилась, несмотря на действительно большой расход масла от лубрикатора (~ 15 л/сутки): снижение подачи масла на цилиндры первой ступени не исправили ситуацию; поставщик клапанов предложил за отдельную плату произвести анализ работы и настройку системы смазки, но было решено отказаться от этой услуги;
- основная версия неправильный подбор клапанов первой ступени из-за ошибки в расчетах – подтвердилась после выполнения проверочного расчета АО «Ленниихиммаш», по результатам которого выявлена излишняя жесткость пружин демпферных пластин, что вызывало излом по краям основной пластины. На совещаниях с поставщиком клапанов выяснилось, что при проектировании компрессора компания Мitsui Е.S. запрашивала комплектующие у производителей (в том числе и компанию-поставщика) по опросному листу, предоставленному заказчиком. В большинстве случаев указываются стандартные или близкие к ним «бюджетные» комплектующие, если в опросном листе не указаны особые (не стандартные) требования к эксплуатации оборудования. Обычно в опросных листах указываются идеальные, расчетные условия эксплуатации оборудования, которые в процессе пуска и эксплуатации зачастую не соответствуют реальным условиям.
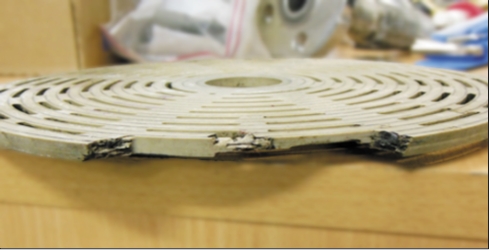
Для подтверждения этой версии потребовался своего рода эксперимент – установка проектных клапанов с удаленным одним из двух рядов пружин. Время наработки таких клапанов увеличилась в разы, не наблюдалось явного повышения температуры клапанов, но в связи с падением расхода была произведена ревизия этих клапанов. При вскрытии вновь были обнаружены поломки пластин.
Одновременно с ведением статистики выходов и анализом собранных данных специалисты «КИНЕФ» изучали российский рынок производителей клапанов и имеют опыт работы с отечественными компаниями.
Для пробного пробега на первую ступень одного из компрессоров были установлены кольцевые клапаны российского производителя. После 2400 ч пробега из-за резкого скачка температуры компрессор был выведен в ремонт. При ревизии был обнаружен неравномерный износ толкателей, колец со стороны действия толкателей и поломку второго по диаметру кольца на одном из клапанов.
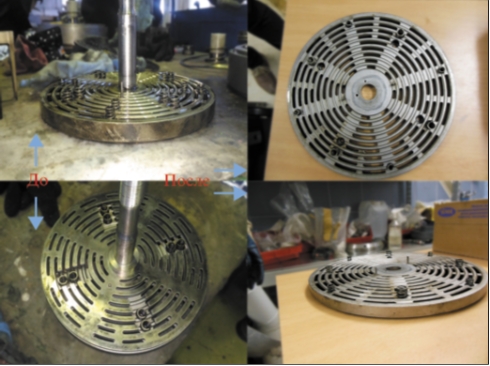
Разрушения частей клапанов, вероятнее всего, возникли из за неправильно выбранного более жесткого материала толкателей. Производитель предложил провести опытный пробег кольцевых клапанов с бесконтактными магнитными толкателями, которыми был полностью укомплектован один из компрессоров (включая вторую и третью ступени). Наработка на таких клапанах составила лишь 12 ч, компрессор был аварийно остановлен по блокировке перепада давления на ступенях. При разборке клапанов выявлено разрушение магнитных элементов толкателей.
Причиной разрушения послужил увеличенный зазор между толкателем и стенками отверстия ограничителя подъема, вследствие чего магнитное напыление выкрашивалось и заново спекалось на магнитах ответных частей толкателей, но уже со сменой полярности. Предложение производителя клапанов применить такие же кольцевые клапаны, но с продуманным подбором материалов для толкателей. Эти клапаны в данный момент работают на всех ступенях одного из компрессоров без каких-либо замечаний, наработка в настоящее время составила около 700 ч, при этом компрессор имеет максимальный расход газа и низкие параметры вибрации.
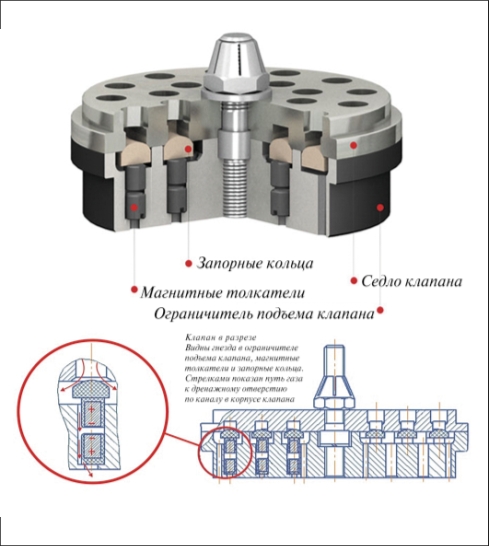
В настоящее время клапанами еще одного отечественного производителя укомплектованы цилиндры первой ступени на двух компрессорах. В одном случае – модульными кольцевыми клапанами (мапеты). Наработка клапанов на настоящее время составила более 4000 ч, и по результатам плановой ревизии не требуют замены каких-либо деталей. Во втором случае было предложено выполнить опытный пробег пластинчатых клапанов.
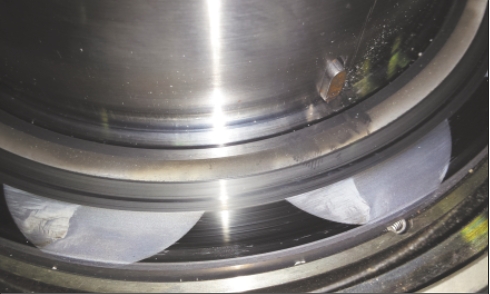
Из-за ненадежной работы проектных пластинчатых клапанов были сомнения в правильности такого решения, тем не менее, пробег на данный момент составил около 1500 ч, компрессор находится в резерве.
Таким образом, на двух из трех компрессоров данной технологической позиции установлены клапаны на цилиндрах первой ступени одного российского производителя и один компрессор полностью укомплектован клапанами другого производителя. Говорить об удачном решении данной технической задачи пока преждевременно в связи с относительно небольшой наработкой предложенных клапанов, но направление для решения выбрано верное. Считаем опыт импортозамещения в данной области удачным.
Центробежные компрессоры фирмы Thermodyn с приводом от паровой турбины Nuovo Pignone (поз. С-2001, 2) предназначены для циркуляции водородсодержащего газа в реакторных блоках второй ступени первой и второй линии и компенсации потерь давления, накопившихся при прохождении газа через контуры высокого давления реакторных блоков.
Основная проблема при эксплуатации данных компрессоров – ненадежная работа СГДУ. В период с сентября 2014 г. по февраль 2015 г. насчитывается четыре выхода компрессора из строя, связанных с утечками ГДУ.
Компрессоры были укомплектованы СГДУ зарубежного производства. Основные причины выходов из строя:
- попадание грязного газа на пары из полости компрессора из-за отсутствия перепада давления на начальных этапах пуска компрессора. Приводом служит паровая турбина, которая имеет свою программу прогрева и разгона, в эти периоды перепад в полости газ–газ практически отсутствует;
- наличие влаги в буферном газе. Фильтры на проектной стойке СГДУ не имеют коалесцирующего эффекта, а обогрев трубопровода буферного газа от фильтров до СГДУ не обеспечивается смонтированным кабелем.
В связи с этим совместно с одной из российских компаний – производителей СГДУ в 2015 г. были разработаны следующие мероприятия по модернизации проектной панели подготовки буферного газа:
- смонтирована дополнительная стойка для буферного газа с каплеотделителем, коалесцентными фильтрами (степень очистки – 10 и 1 мкм). Для вторичного азота установлены коалесцентные фильтры со степенью очистки 1 мкм;
- подведены трубопроводы азота и водорода для выбора этих газов в качестве буферного на разных режимах работы компрессора с целью обеспечения необходимого перепада давления;
- забор буферного газа из компрессора производится не от 3-го колеса как раньше, а от выкидной линии компрессора;
- удалены ограничительные шайбы и смонтированы вентильные блоки с приборами КИП для контроля и возможности регулирования перепада полости газ–газ;
- смонтированы СГДУ российского производителя.
Эти мероприятия позволили проработать компрессорам безаварийно в течение года, однако результаты ревизии данных уплотнений после ~8000 ч работы показали присутствие мелкодисперсной пыли, которая влияет на нормальную работу уплотнения. После проведения регламентных работ в 2016 г. были смонтированы уплотнения также этой фирмы. На одном из компрессоров спустя 1500 ч работы возросла утечка, были выполнены ремонтные работы по замене двух СГДУ уплотнениями зарубежного производителя. В настоящее время работа уплотнений стабильна, утечка сохраняется на минимальном уровне. При ревизии вышедшего из строя уплотнения также выявлено присутствие мелкодисперсной пыли, из-за которой потеряло подвижность подпружиненное кольцо. Для справки: стоимость СГДУ зарубежного производителя в 4 раза выше стоимости СГДУ отечественного производителя, а ревизия зарубежных уплотнений на заводе-изготовителе составляет 20% стоимости нового уплотнения.
Следующим важным этапом в повышении надежности работы центробежных компрессоров запланирован монтаж подогревателя буферного газа, который гарантированно исключит конденсацию влаги при дросселировании на парах СГДУ, кроме того, необходимо выяснить причины загрязнения уплотнений, несмотря на установку дополнительных фильтров, и получить возможность контролировать перепад давления между буферным и перекачиваемым газом.