Автор: И.П. Клепцов (ООО «ИЛЬМА»).
Опубликовано в журнале Химическая техника №2/2016
Нефтепереработка и нефтехимия – это передовые отрасли, в которых эксплуатируется высоконадежное оборудование, а для герметизации применяются современные уплотнительные материалы. На нефтеперерабатывающих и нефтехимических предприятиях действуют жесткие требования к обеспечению промышленной безопасности. Именно поэтому уникальные высоконадежные уплотнения нашли широкое применение в этих отраслях.
Опишем факторы, которые учитываются ответственными поставщиками промышленных уплотнений при решении вопросов, связанных с герметизацией разъемных соединений основного и вспомогательного оборудования на нефтеперерабатывающих и нефтехимических заводах:
- износ уплотнительных поверхностей. Он может быть связан как с длительным сроком эксплуатации разъемных соединений, так и с низким качеством ранее применяемых уплотнений. В частности, содержание примесей в уплотнениях из терморасширенного графита (ТРГ) зачастую является причиной коррозии фланцев.
Кроме того, графит низкого качества, как правило, прилипает к поверхностям, а при его механическом удалении на фланцах остаются повреждения и неровности, которые не позволяют обеспечить герметичность разъемных соединений. Ответственные поставщики при производстве уплотнений используют высококачественный графит, что позволяет преодолеть данную проблему. Для обеспечения герметизации ответственных узлов используются как мягкие уплотнения (цельные и сегментные), так и комбинированные;
- длительный срок поставки и высокая цена оригинальных уплотнений зарубежного производства. Обладая научно-техническим потенциалом, ответственные поставщики, используя собственные производственные возможности, предлагают решения в рамках программ по импортозамещению. Заказчик в таких случаях получает в сжатые сроки изделие мирового уровня, адаптированное для российского рынка, по меньшей стоимости;
- потребность в постоянном техническом сопровождении. Предлагая заказчикам высокотехнологичную продукцию, ответственные поставщики осуществляют постоянное техническое сопровождение поставок, взаимодействуя с техническими специалистами, отвечающими за бесперебойную работу оборудования.
Приведем примеры технических решений, внедренных на оборудовании нефтеперерабатывающих и нефтехимических заводов в результате тесного сотрудничества заказчиков и разработчиков инновационных уплотнений. В основе подхода лежит использование современных безасбестовых материалов, подобранных с учетом условий эксплуатации, в сочетании с оптимальной конструкцией уплотнения, разработанной для данного узла.
В последние годы на промышленных предприятиях широкое применение нашли уплотнения на основе фольги из ТРГ, армированной гладкой или перфорированной коррозионно-стойкой сталью. Применение графитовых уплотнений, вырубленных их листовых материалов, иногда ограничено размерами и толщиной уплотнительных листов. Тем не менее, при профессиональном подходе техническим специалистам удается найти нестандартные решения для обеспечения надежной герметизации разъемных соединений.
Так, на некоторых нефтеперерабатывающих заводах во фланцевых соединениях входов вакуумных колонн размерами до DN 1200 было предложено использовать не однослойные, а двуслойные прокладки на основе армированного ТРГ.
Для герметизации прямоугольных фланцевых соединений теплообменников были предложены два решения.
В первом случае были спроектированы двуслойные сегментные прокладки. Уплотнения были изготовлены из ламината, состоящего из слоев графита высокой чистоты толщиной 0,5 мм и стальных вкладышей толщиной 0,05 мм, соединенных между собой специальным методом без применения клея. Прокладки можно формировать из сегментов прямо на поверхности фланцевого соединения. В качестве альтернативного решения была разработана цельная прямоугольная прокладка со стальным сердечником и двусторонним пластичным уплотнителем из графита. Оба варианта обеспечивают требуемую герметичность прямоугольных фланцевых соединений.
Для надежной герметизации оборудования, работающего в агрессивных средах, российскими инженерами была разработана уникальная технология покрытия графитовой основы фторопластовой пленкой. Графито-фторопластовые уплотнения, изготовленные по этой запатентованной технологии, обладают пластичностью и упругостью графита, а за счет фторопластового покрытия уплотнения отличаются стойкостью к химическому воздействию и механическим повреждениям.
Так, на линии производства серной кислоты во фланцевые соединения стеклопластиковых трубопроводов обвязки теплообменников были установлены графитофторопластовые прокладки (рис. 1). Внедрение этих уплотнений позволило увеличить межремонтный период работы данных разъемных герметичных соединений до 21 месяца.
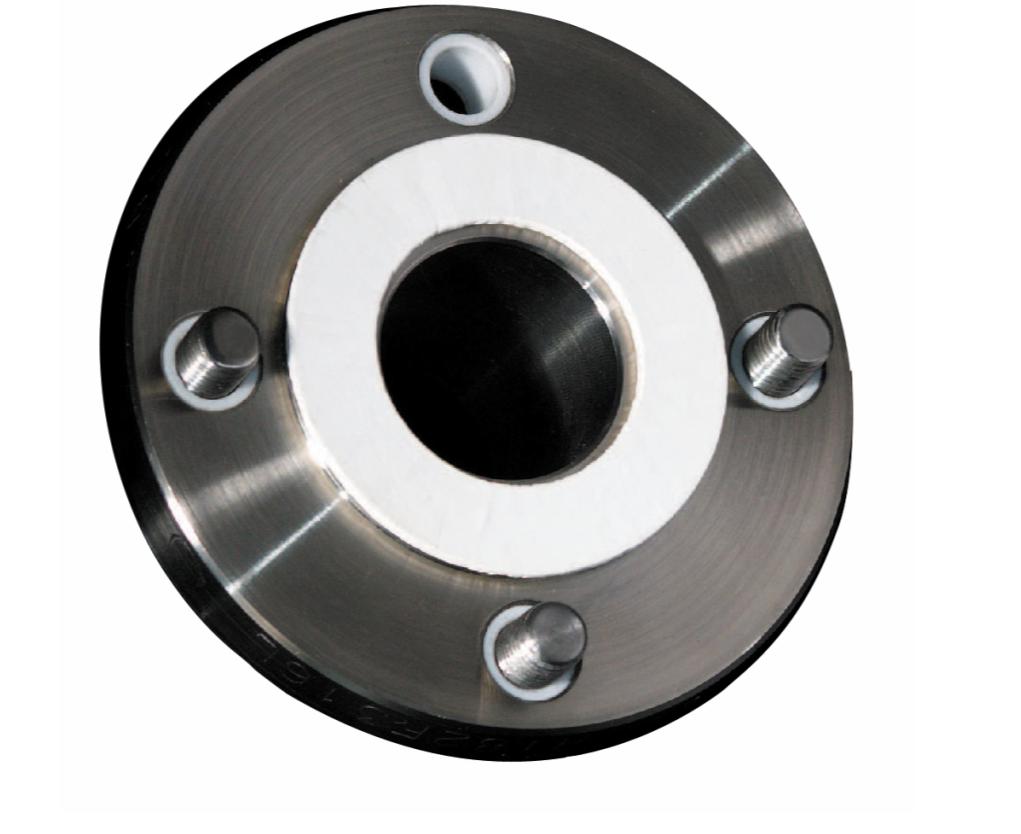
На линии производства водорода для решения проблемы герметизации крышек трубопроводной арматуры (задвижки, клапаны, вентили) было предложено уникальное техническое решение. После доработки конструкции крышек уплотнительные металлические кольца были заменены комплектами, состоящими из двух фланцевых прокладок из армированного ТРГ и графито-фторопластовой сальниковой набивки. В результате была достигнута требуемая герметичность уплотняемого узла, сократилось время на установку уплотнений, увеличился срок службы уплотнительных поверхностей за счет отсутствия коррозии.
Для надежной герметизации неподвижных разъемных соединений ответственного оборудования широко применяются комбинированные уплотнения с металлическим сердечником и пластичным уплотнителем. При этом уплотнение можно использовать многократно при условии замены мягкого уплотнителя. Так, для герметизации фланцевых соединений теплообменного оборудования успешно применяют прокладки, состоящие из стального цельного сердечника с пазом и уплотнителя из неармированного графита (рис. 2). Стальной сердечник используется многократно, при ремонте в паз укладывается новый уплотнитель, изготовленный из фланцевой графитовой ленты.
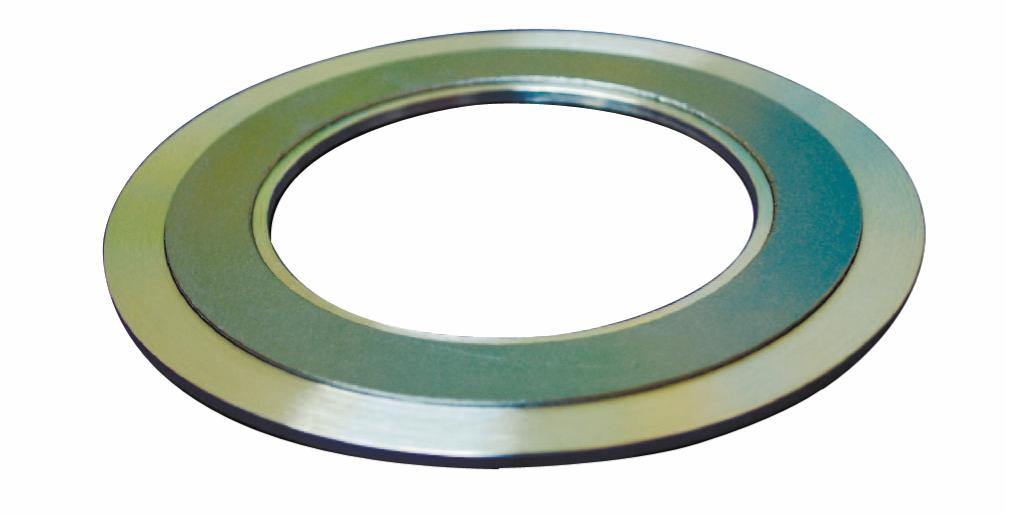
На одной из установок получения элементарной серы взамен металлических прокладок овального сечения были установлены плоские стальные прокладки с металлическим зубчатым сердечником и уплотнителем из графитовой фольги чистотой 99,85%. Прокладки также используются повторно после замены мягкого графитового уплотнителя.
Технические службы нескольких заводов столкнулись с проблемой, когда традиционно применяемые в соединениях типа RTJ кольца АРМКО не обеспечивали требуемую герметичность из-за наличия дефектов на уплотнительных поверхностях. Для решения этой проблемы было предложено использовать комбинированную прокладку овального или восьмиугольного сечения, состоящую из металлического сердечника и сменных пластичных уплотнителей. Сменные части могут быть выполнены в виде графитовых ленточных уплотнителей (рис. 3), нанесенных на кольцевые канавки, контактирующие с уплотнительной поверхностью канавки фланца, или в виде двух металлических накладок (рис. 4), повторяющих профиль основного сердечника. При этом твердость сменных уплотнителей ниже, чем твердость основной части прокладки. При сжатии прокладки пластичные сменные элементы вдавливаются в уплотняемую поверхность канавок фланцев, а основная часть прокладки пластически не деформируется. При проведении ремонтных работ металлический сердечник можно использовать повторно, а сменные элементы заменять.
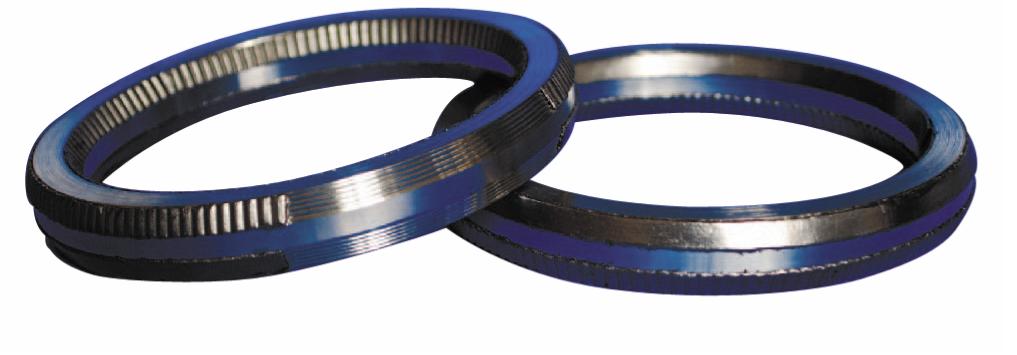
Данная инновация позволяет существенно повысить экономическую эффективность использования металлических прокладок овального и восьмиугольного сечения.
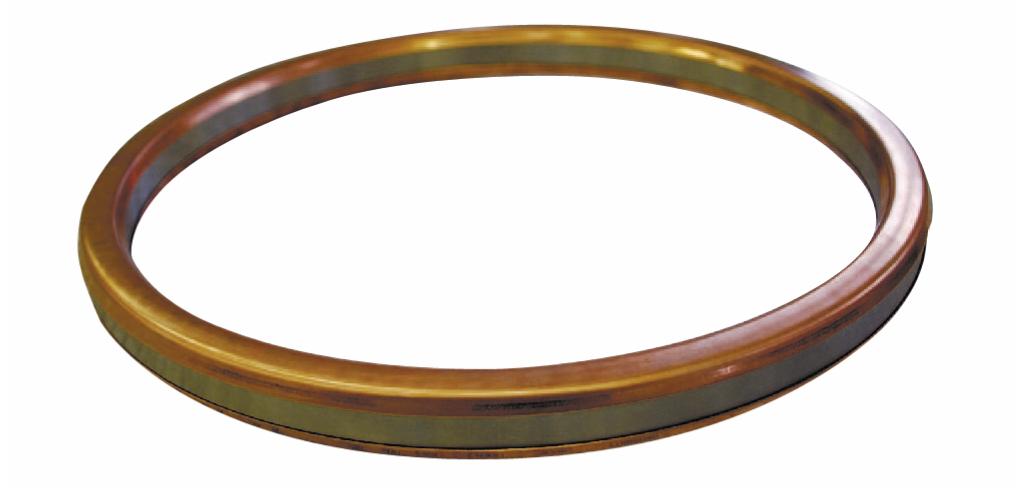
Металлографитовая прокладка, выполненная по описанной технологии, была успешно испытана на установке гидрокрекинга на одном из нефтеперерабатывающих заводов. В настоящее время испытания этого уплотнения проходят в одном из ведущих научно-исследовательских институтов химического и нефтяного машиностроения, после чего опытные партии уплотнений будут переданы на заводы для проведения производственных испытаний.
Важно отметить, что во всех перечисленных случаях технические специалисты нашли оригинальные решения для обеспечения надежной герметизации проблемных узлов, в которых другие уплотнения не работали. Как показывает практика, применение современных высокоэффективных уплотнений позволяет обеспечить существенную экономию ресурсов за счет повышения надежности уплотняемых узлов и увеличения ресурса их работы.