Авторы: Е.И. Копалиди (ПАО «ЛУКОЙЛ»), С.А. Лапкин, В.Р. Ржевкин, А.Б. Самохвалов (ООО «ДИАПАК»).
Опубликовано в журнале Химическая техника №2/2016
В настоящее время планирование обследования оборудования на основе оценки рисков находит все большее применение в нефтеперерабатывающей и нефтехимической отраслях. Анализ рисков играет большую роль в процессе оптимизации работы служб технического надзора и в переводе технологических установок на увеличенный межремонтный пробег [1].
Краткая характеристика программного комплекса PCMS
PCMS является специализированным программным обеспечением, предназначенным для хранения информации и выполнения расчетов, связанных с надежностью оборудования [2, 3]. В базе данных PCMS хранятся «электронные паспорта» оборудования, включая сведения о конструктивных элементах, материальном исполнении, условиях работы, химическом составе технологических сред, результатах толщинометрии, об истории визуальных и инструментальных обследований и ремонтов.
На основе этой информации PCMS определяет действующие механизмы повреждения конструкционных материалов, вероятности аварии (отказа), величину последствий расчетного сценария аварии и, соответственно, величину риска. Риск определяется как на текущий момент, так и на будущий (прогнозируемый) период времени. Учитывая эти данные, PCMS предоставляет рекомендации по срокам, методам и объемам обследований оборудования. Специалист, работающий с системой, осуществляет осознанное планирование инспекций оборудования с целью минимизации риска и экономии средств.
Расчеты рисков (RBI) соответствуют стандартам API 571 и API 581.
Помимо методики RBI, предназначенной для статического оборудования (сосуды давления, трубопроводы, резервуары), в PCMS есть модуль RCM, с помощью которого можно оценивать также и динамическое (вращающееся) оборудование.
Ключевые структурные модули PCMS
Модуль контроля коррозии является средством для записи, хранения и анализа информации о коррозионном состоянии оборудования.
Модуль:
- анализирует коррозионное состояние оборудования с целью предотвращения незапланированных остановок и аварий;
- документирует изменения толщин стенок;
- вычисляет минимально допустимую толщину стенки компонентов оборудования различных геометрических форм (калькулятор Тмин) на базе стандартов ANSI, ASME, API, EN и ГОСТ;
- дает оценки общей и локальной коррозии;
- указывает проблемные области, чтобы сузить круг проведения обследований;
- вычисляет сроки будущих обследований на основе многоуровневого анализа;
- устанавливает, вычисляет и документирует сроки вывода из эксплуатации.
Модуль позволяет выявить проблемные области и места мониторинга состояния (в частности, места замеров толщин), которые наиболее близки к пределу отбраковки.
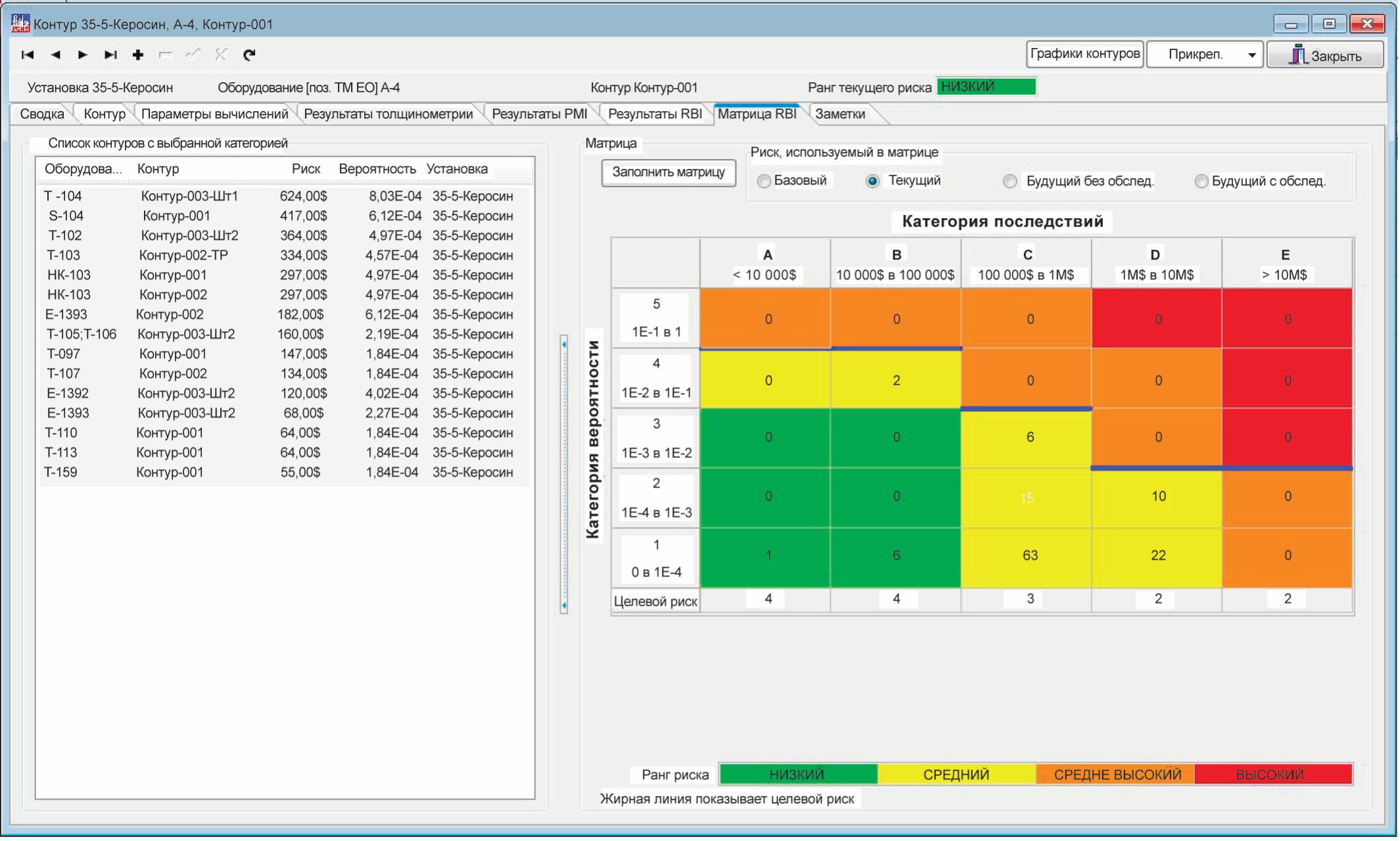
Модуль оценки рисков (RBI). Основная цель RBI – гарантировать безопасность и надежность оборудования в условиях увеличенного пробега установок. Подход RBI фокусирует внимание на оборудовании и механизмах изнашивания, представляющих наибольший риск для эксплуатации. Путем оценки рисков и способов их снижения подход RBI реализует взаимосвязь между механизмами, которые приводят к отказам оборудования, и планированием обследований, которые приводят к снижению риска.
Модуль RBI обеспечивает:
- автоматическое определение действующих механизмов повреждения;
- расчет величины последствий расчетного сценария аварии, включая экономические последствия, последствия для жизни и здоровья людей, экологические последствия;
- расчет вероятности отказа по каждому действующему механизму и по их совокупности, как на сегодняшний день, так и на прогнозируемый период времени, учитывая эффективность ранее выполненных и планируемых в будущем обследований.
На основе расчетов оборудование (коррозионные контуры) распределяется в матрице рисков, пример которой показан на рис. 1.
Механизмы повреждения, учитываемые PCMS, разделены на 4 группы:
- внутренняя потеря толщины;
- внешняя потеря толщины;
- растрескивание, вызванное агрессивной средой;
- металлургическое и механическое разрушение.
Повреждения, рассматриваемые в PCMS, соответствуют основным видам повреждения, имеющим место на нефтеперерабатывающих и нефтехимических заводах.
Модуль RBI предоставляет специалистам решать такие задачи, как:
- установить приоритет обследований на базе рисков;
- определить соответствующий план обследований, основанный на традиционных методиках, или на данных анализа риска;
- сфокусировать усилия персонала на объектах наибольшего риска, согласно данным RBI;
- уменьшить время простоя благодаря снижениям объемов обследований объектов меньшего риска.
Модуль обследований обеспечивает организованный подход к сбору данных, оценке, документированию и планированию визуальных и инструментальных обследований. Модуль содержит архив данных всех обследований любой единицы оборудования, включая прикрепленные документы и рекомендации. Основные функции модуля следующие:
- отслеживает и сохраняет историю обследований вместе с вносимыми изменениями в конструкцию и заменами оборудования завода;
- создает стандартизованные листы проверок и полную отчетность;
- отслеживает заявки/выполнение ремонтов, рекомендаций и генерирует напоминания о необходимости обследований и обслуживаний;
- вычисляет даты следующих обследований на базе заложенных в систему правил;
- составляет расписания (планы) обследований, используя результаты толщинометрии, результаты оценки риска (RBI) и требования нормативных документов.
Дополнительные модули включают:
- заявки на работы (обследования, ремонты);
- связь с информационной системой управления ресурсами предприятия SAP;
- связь с AutoCAD (создание автоматически обновляемых электронных коррозионных карт);
- вспомогательные модули, такие как «импорт/экспорт», генерирование отчетов, задание прав пользователей, аудит и др.
Внедрения PCMS
В 2010 г. в компании «ЛУКОЙЛ» началось внедрение системы управления рисками и надежностью оборудования (проект «СУРНО») в «ЛУКОЙЛ-ННОС». В качестве программного обеспечения был выбран успешно применяемый во всем мире программный комплекс PCMS («Plant Conditions Management System») разработки компании MISTRAS (США), локализованный и адаптированный к российским условиям. После удачного внедрения пилотного проекта на «ЛУКОЙЛ-ННОС», в 2011 г. на уровне компании было принято решение о тиражировании этого продукта для других предприятий.
В настоящее время программное обеспечение PCMS в ПАО «ЛУКОЙЛ» используют восемь предприятий компании: ООО «ЛУКОЙЛ-Нижегороднефтеоргсинтез» (ННОС), ООО «ЛУКОЙЛ-Пермнефтепереработка», ООО «ЛУКОЙЛ- Ухтанефтепереработка» (УНП), ООО «Саратоворгсинтез», ООО «Ставролен», ООО «ЛУКОЙЛ-Коробковский ГПЗ», ООО «ЛУКОЙЛ-Волгограднефтепереработка» (ВНП) и «ЛУКОЙЛ-НЕФТОХИМ Бургас».
В настоящее время существуют планы расширения использования PCMS, в частности планируется начать внедрение на НПЗ «Petrotel» (Румыния) в 2016 г.
Если говорить о мировом опыте, то PCMS используется не только на НПЗ, НХП и ГПЗ, но и на других предприятиях нефтехимического и газового комплекса.
Хотя основная область применения PCMS – это перерабатывающие заводы, за рубежом PCMS применяется также на нефтедобывающих предприятиях.
Объемы внедрения и охват по оборудованию
В настоящее время в базу данных PCMS в среднем введено более 70% всего оборудования НПЗ, НХП и ГПЗ, где осуществилось внедрение системы СУРНО.
Внедрение PCMS на заводах ЛУКОЙЛ и ГАЗПРОМНЕФТЬ
Завод | Установки | Оборудование |
«ПЕРМЬНЕФТЕОРГСИНТЕЗ» | 30 | 5 133 |
«НИЖЕГОРОДНЕФТЕОРГСИНТЕЗ» | 24 | 3 880 |
«ВОЛГОГРАДНЕФТЕПЕРЕРАБОТКА» | 21 | 3 500 |
«УХТАНЕФТЕПЕРЕРАБОТКА» | 6 | 1 129 |
Коробковский ГПЗ | 4 | 369 |
«САРАТОВОРГСИНТЕЗ» | 2 | 337 |
«СТАВРОЛЕН» | 1 | 106 |
«ГАЗПРОМНЕФТЬ-МНПЗ» | 5 | 2 303 |
Самый большой процент охвата оборудования – в ООО «ЛУКОЙЛ-ПЕРМЬНЕФТЕОРГСИНТЕЗ». Программа внедрения СУРНО реализуется на всех предприятиях с разной скоростью, так как они различаются объемами переработки сырья и, соответственно, числом единиц оборудования. Небольшие заводы уже закончили внедрение СУРНО, охватив большую часть оборудования, остальные, например, ЛУКОЙЛ-ННОС, ЛУКОЙЛ-ВНП, ЛУКОЙЛ-ПНОС движутся равномерно в этом направлении.
Опыт, полученный на ранних стадиях внедрения PCMS в компании, был использован в полном объеме при расширении проекта на другие заводы, что позволило сократить сроки внедрения пилотных проектов и улучшить качество анализа в рамках СУРНО.
Технологические установки, вводимые в базу данных PCMS, включают установки первичной переработки нефти, установки каталитического риформинга и гидроочистки, абсорбционно-газофракционирующие установки, установки каталитического крекинга и коксования, установки производства водорода и др. В первую очередь PCMS применяется, как правило, для установок, относящихся к производству моторных топлив, как наиболее востребованных продуктов на мировом рынке. С другой стороны, оборудование для производства масел обычно не участвует в анализе RBI, поскольку оно не подвергается значительным коррозионным процессам (конечно, за некоторым исключением) и поэтому возникающие в связи с этим проблемы не имеют существенного масштаба, требующего применения PCMS для расчета возможных рисков.
Внедрение PCMS в 2015 г. не снижает свои темпы по сравнению с предыдущими годами и наращивает свои объемы в сторону увеличения количества оборудования, охваченного анализом рисков.
Организация процесса внедрения и эксплуатации PCMS
Центральным органом, курирующим внедрение PCMS, в корпорации «ЛУКОЙЛ» является «Блок нефтепереработка, нефтехимия и газопереработка». Указанный блок выполняет организационные и надзорные функции. В состав блока входят специалисты технологического, механического и экономического профиля. Благодаря централизованной координации заводы придерживаются одинакового подхода к организации внедрения и дальнейшего применения PCMS.
В процесс внедрения PCMS непосредственно на заводах вовлечены специалисты преимущественно отделов технического надзора или диагностирования (специалисты по сосудам и аппаратам, трубопроводам, печам, резервуарам). Внедрение PCMS на отдельных заводах выполняют специалисты отдела технического надзора и отдела технического диагностирования по направлению деятельности: группы (сектора) сосудов и аппаратов, трубопроводов, резервуаров, печей и т.д. Численность персонала, задействованного во внедрении, зависит от штата отдела и варьируется в пределах 3…12 человек.
Указанные специалисты подчиняются руководителю группы и непосредственно Начальнику ОТН или ОТД.
Таким образом, внедрение PCMS осуществляют те же специалисты, которые используют его в дальнейшем в своей повседневной деятельности. После завершения внедрения, анализ рисков в PCMS становится неотъемлемой частью работы отделов технического надзора или диагностирования. PCMS также используется начальниками и механиками установок и производств.
Специалисты, работающие с PCMS, для получения исходной информации взаимодействуют с производствами, техническими отделами, исследовательскими отделами и лабораториями контроля качества сырья и получаемой продукции. Результаты вычислений и планирования отправляются на производства. В целом результаты работы PCMS в форме отчетов и сводок используют собственно ОТН и ОТД, а также начальники, механики производств, установок.
В рамках компании налажен межзаводской обмен опытом по внедрению и использованию PCMS. Заводы делятся друг с другом информацией о возможности использования PCMS на различных периферийных устройствах, разрабатывают лучшие практики использования PCMS, а также обмениваются опытом внедрения.
Сбор и анализ исходной информации. Для заполнения и обновления базы PCMS в качестве источников информации используются технологические регламенты, паспорта оборудования, коррозионные карты, результаты лабораторного химического анализа технологических сред, отчеты по обследованиям, экспертные заключения и т.п.
Учитывается статистика по отказам, авариям, ремонтам. Наряду с заполнением базы PCMS идет работа по созданию электронных коррозионных карт в AutoCAD, связанных с PCMS.
Наиболее сложным является сбор данных по технологическим средам, в особенности определение содержания в них коррозионных агентов.
Для определения эффективности обследований в отношении различных механизмов повреждения используются рекомендации API-581.
Построение коррозионных контуров. Коррозионный контур является основной расчетной единицей при проведении RBI-анализа. Коррозионный контур представляет часть аппарата или трубопровода, которая характеризуется одинаковым материальным исполнением, условиями работы, составом технологической среды и условиями проведения обследований. В рамках контура действуют одинаковые расчетные механизмы повреждения и для него устанавливается определенная величина последствий при расчетном сценарии аварии.
Разделение на коррозионные контуры – это ответственный этап RBI-анализа, и к нему применяются общие методические подходы. Количество и границы коррозионных контуров должны быть выбраны оптимальным образом, чтобы, с одной стороны, не повышать сложность анализа, а с другой – учесть особенности конструкции и эксплуатации аппарата или трубопровода. В аппаратах зачастую выделяются нижняя и верхняя части, различающиеся химическим и фазовым составом сред (типичный пример: в нижней части – жидкость, в верхней – газ). Однако построение коррозионных контуров должно быть индивидуальным, зависящим от сложности аппарата, параметров его эксплуатации и свойств технологической среды и материального исполнения. Перед выполнением разделения на контуры анализируется все указанные факторы.
Вычисление отбраковочных толщин и оценка толщинометрии. Модуль вычислений отбраковочных толщин в PCMS дает возможность оценить приблизительно остаточный ресурс основных несущих элементов оборудования и заблаговременно подготовить соответствующие мероприятия в нужное время и в нужном месте. Толщинометрия тесно связана с оценкой рисков и RBI-анализом.
По оценке специалистов, модуль толщинометрии весьма удобен и позволяет быстро построить план толщинометрии в первую очередь тех местах, где это критично.
Анализ толщинометрии средствами PCMS помогает выявить некорректно введенные данные и участки с наибольшей скоростью коррозии. В числе прочего PCMS имеет интерфейс для массовой загрузки данных и автоматических толщиномеров (толщиномеры «с памятью»).
Результаты анализа RBI
По результатам RBI-анализа на предприятиях ЛУКОЙЛ, где осуществлено внедрение PCMS, отмечаются следующие наиболее распространенные механизмы повреждения:
- высокотемпературная Н2/Н2S коррозия;
- низкотемпературная сероводородная коррозия;
- наводороживание (блистеринг);
- коррозионное растрескивание под напряжением;
- коррозия в бисульфите аммония;
- коррозия в хлориде аммония;
- водородное охрупчивание.
Набор механизмов повреждения, заложенный в PCMS, достаточно полно соответствует механизмам, фактически присутствующим на заводах. Корректировка механизмов повреждения «вручную» выполняется не часто, в основном принимаются результаты, автоматически вычисляемые программой. В некоторых случаях, однако, специалисты корректируют данные по механизмам повреждения, выполняя добавление, удаление механизмов, переопределение тяжести повреждения.
Для критичного оборудования анализ RBI выполняется особенно тщательно. К категории критичного оборудование относится по ряду критериев, одним из которых выступают тяжелые последствия его отказа и большая вероятность возникновения этого отказа, соответственно. Доля критичного оборудования невелика, обычно RBIанализ выявляет всего лишь несколько критичных единиц на одну установку.
Общие результаты внедрения PCMS
Специалистами ПАО «ЛУКОЙЛ» совместно с ООО «ДИА-ПАК» проделана большая работа по внедрению систем управления надежностью оборудования на основе оценки рисков с использованием программного обеспечения PCMS. Внедрение PCMS, как правило, встречает поддержку специалистов заводов.
Общие результаты внедрения положительные. PCMS помогает управлять рисками, повышать надежность оборудования и экономить средства, выделяемые на контроль технического состояния. Более полную количественную оценку пользы от внедрения PCMS можно будет дать после наработки определенного периода эксплуатации в среде PCMS, как правило, затрагивающего минимум два-три межремонтных цикла со времени внедрения, чтобы иметь возможность в достаточной степени оценить ее качества в деле повышения надежности оборудования и рационального распределения денежных ресурсов для контроля технического состояния. Тем не менее, уже сейчас можно утверждать, что система управления рисками и надежностью оборудования на основе программного комплекса PCMS является одним из важных инструментов, позволяющих найти пути снижения аварийности и увеличения межремонтного пробега технологических установок.
Преимущества и смысл применения RBI
Промышленность сталкивается со все более жесткими правилами по безопасности, защите окружающей среды, и механической целостности оборудования. RBI является решающим фактором управления эксплуатационным риском с помощью эффективной технологии и наилучшего планирования обследований и обслуживаний.
Подход RBI дает наивысшую выгоду среди других методологий обследований:
- RBI существенно снижает затраты на обслуживание и в то же время увеличивает надежность завода;
- смещает усилия по излишним обследованиям некритичного оборудования в сторону критичного оборудования с более высоким базовым риском;
- минимизирует затраты на обслуживания, благодаря рациональным обследованиям;
- увеличивает объем обследований в процессе эксплуатации и снижает длительность остановок и их стоимость;
- определяет слабые места установок и некачественно проведенные обследования-обслуживания;
- помогает создать стратегию замены оборудования;
- увеличивает интервал остановок в случае, если соответствующие власти понимают и принимают методологию RBI;
- определяет механизмы повреждения.
- RBI позволяет создать подробные планы обследований с указанием рекомендаций по технологиям обследований.
Список литературы
- Золотарев И.Л., Ржевкин В.Р., Самохвалов А.Б., Копалиди Е.И. Количественные процедуры планирования обследований промышленного оборудования на базе оценки рисков//Химическая техника. 2015. №3.
- Ржевкин В.Р., Самохвалов А.Б., Шемякин В.В. PCMS – программное обеспечение для управления состоянием оборудования завода на основе оценки рисков//В мире НК. 2012. №1 (55).
- Risk-Based Inspection Technology. API Recommended Practice 581. Second Edition, September 2008.