Автор: А.М. Норов, Д.А. Пагалешкин, П.С. Федотов (АО «НИУИФ»)
Опубликовано в журнале Химическая техника №12/2017
Совмещение процессов гранулирования и сушки в одном аппарате широко используется в производствах минеральных удобрений, так как это позволяет значительно упростить технологическую схему, снизить потери сырья, уменьшить энергетические и материальные затраты [1].
Для проведения совмещенных процессов гранулирования и сушки можно применять грануляционные башни, аппараты с кипящим (псевдоожиженным) слоем и барабанные аппараты. Последняя группа представлена разработанными еще во времена СССР барабанными грануляторами-сушилками [2–4] и аппаратами, известными под названием «Сферодайзер» [5]. Все они представляют собой вращающиеся барабаны с внутренней подъемно-лопастной насадкой, установленные с наклоном 1…3° к горизонту (рис. 1). Аппарат БГС отличается от «Сферодайзера» внутренней насадкой, и, в первую очередь, наличием обратного шнека, позволяющего возвращать некоторое количество гранулированного материала в головную часть аппарата (внутренний ретур). При вращении барабана лопатки специального профиля, установленные внутри барабана, проходят через слой продукта в нижней части («завал»), захватывая его и затем ссыпая, образуя при этом завесу по всему сечению. На эту завесу с помощью форсунки наносится перерабатываемая пульпа, диспергируемая с помощью сжатого воздуха (или за счет пара, образующегося при работе с трубчатым реактором). В головную часть барабана также подаются топочные газы и внешний ретур.
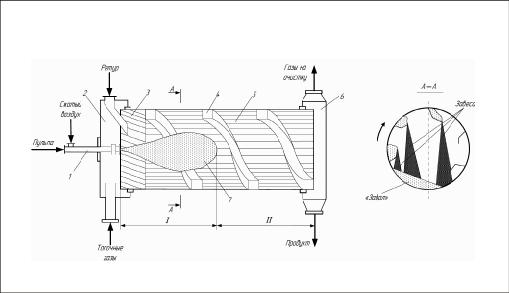
1 – форсунка; 2 – загрузочная камера; 3 – винтовая питающая насадка; 4 – обратный шнек; 5 – подъемно-лопастная насадка; 6 – разгрузочная камера; 7 – факел; I – зона гранулирования; II – зона досушки
Для перемещения внешнего ретура в зону образования завесы головная часть БГС оснащена винтовой насадкой. При нанесении пульпы на частицы завесы происходит образование гранул, которые затем досушиваются. Максимальное количество пульпы, подаваемое на завесу,зависит от предельной влажности гранул, при которой начинается образование агломератов в «завале».
Механизм гранулообразования в БГС можно упрощенно представить состоящим из следующих этапов [1, 6]:
- нагрев частиц ретура, ссыпающегося с лопаток насадки в токе горячего теплоносителя (топочных газов);
- нанесение пленки жидкости на частицы ретура при прохождении их через объем факела распыливаемой пульпы;
- сушка увлажненных гранул в токе нагретых газов после их выхода из факела пульпы.
Протяженность зоны гранулирования в аппаратах БГС определяется глубиной проникновения факела распыла пульпы сквозь завесу ретура в объем барабана.Из-за высокой интенсивности процессов тепло- и массообмена в зоне распыла формирование основной массы гранул и удаление из них большей части влаги практически завершается на первых метрах длины аппарата [1, 7].Окончательная досушка гранул осуществляется далее по длине аппарата при более мягких температурных условиях.
Наличие в аппаратах БГС обратного шнека обеспечивает поступление в зону гранулирования кроме внешнего еще и внутреннего ретура, что способствует образованию более плотной завесы гранул и увеличивает количество центров гранулообразования (по сравнению со «Сферодайзером»). Это в свою очередь позволяет значительно интенсифицировать процесс гранулирования, увеличить производительность аппарата, применять теплоноситель с более высокой температурой, повысить термический КПД системы, увеличить выход товарной фракции, снизить количество внешнего ретура [1].
Существуют технологические схемы, оснащенные аппаратами БГС и не имеющие внешнего ретура. В них крупная фракция после рассева поступает на дробление и затем возвращается на повторный рассев, а мелкая фракция подается в БГС на обратный шнек. Но это решение не является наилучшим как по производительности, так и с точки зрения стабилизации технологии и качества продукта. Опытным путем установлено, что только сочетание внешнего и внутреннего ретура является оптимальным для схем с аппаратом БГС [8, 9].
Особенностью гранулирования и сушки удобрений в БГС является периодическое колебание гранулометрического состава и связанное с этим изменение массовых расходов ретура и готового продукта [10]. Эти процессы оказывают негативное влияние и на свойства удобрений. Для стабилизации процессов гранулирования и сушки,а также для получения качественных показателей продукта необходимо поддерживать определенный расход и качество внешнего ретура [8–14]. Предложен также способ стабилизации и регулирования процесса гранулирования путем изменения гранулометрического состава внешнего ретура [9, 15, 16].
Разработаны конструкции БГС, позволяющие одновременно осуществлять кроме гранулирования и сушки охлаждение и классификацию удобрений [17]. Однако опыт промышленного внедрения этих аппаратов показал, что они слишком сложны и неудобны в эксплуатации, а совмещение в одном аппарате большого числа операций (три или четыре) значительно снижает эффективность и качество проведения каждой из них.
Процесс гранулирования и сушки удобрений зависит от влажности исходной пульпы, степени нейтрализации входящих в ее состав кислот, температуры топочных газов, конфигурации и дисперсности факела распыла пульпы, скорости газового потока и ряда других факторов. Кроме того, на процесс гранулирования и сушки оказывают влияние и конструктивные особенности аппарата БГС (конструкция и размеры внутренней насадки, обратного шнека, угол наклона барабана, скорость вращения и др.) [1, 17].
Сравнивая технологические схемы, оснащенные аппаратами БГС, и традиционные схемы с аммонизаторами-грануляторами (АГ) и сушильными барабанами (СБ), обычно приходят к выводу, что первые имеют следующие преимущества [1, 18, 19]:
- позволяют получать гранулированные удобрения из пульп с высокой влажностью (40% и более);
- содержат меньшее число единиц оборудования, что, в свою очередь, снижает капитальные затраты на их создание, расход электроэнергии, затраты на ремонт,а также повышает их надежность и увеличивает эффективный рабочий фонд времени;
- имеют сравнительно небольшую внешнюю ретурность (в некоторых схемах внешний ретур совсем отсутствует), что позволяет использовать транспортное оборудование меньшей производительности (и соответственно меньшей стоимости) и также снижает энергозатраты.
К недостаткам технологических линий, укомплектованных аппаратами БГС, обычно относят:
- меньшую по сравнению с технологией АГ-СБ производительность;
- относительно узкий ассортимент производимой продукции.
Традиционно считалось, что схемы с аппаратами БГС предназначены для производства гранулированного двойного суперфосфата, аммофоса (МАФ) и некоторых марок NP- иNPK-удобрений, получаемых методом азотнокислотного разложения сырья. Производительность одной технологической нитки составляла от 10 до 25 т/ч в зависимости от вида удобрения, влажности пульпы и диаметра аппарата БГС. Также до определенного времени считалось,что на аппаратах БГС нельзя производить удобрения с высоким мольным отношением NH3:H3PO4 – диаммонийфосфат (ДАФ), а также NPS, NPK и NPKS-удобрения на его основе [1, 19].
В последние годы в АО «НИУИФ» был проведен большой комплекс работ, который позволил в значительной степени изменить представление о возможностях технологических схем, укомплектованных аппаратами БГС. Были разработаны универсальные технологические схемы, которые позволяют производить широкий ассортимент марок удобрений [16, 19].
Для производства фосфорсодержащих удобрений на технологических нитках, оснащенных аппаратами БГС, применяются различные схемы нейтрализации исходной экстракционной фосфорной кислоты (ЭФК), в зависимости от ее концентрации, содержания в ней примесей, ассортимента производимой продукции и других факторов [9, 20, 21]. Рассмотрим наиболее типичные из них.
1. Одностадийная аммонизация
1.1. Одностадийная аммонизация в емкостных аппаратах, оснащенных перемешивающими устройствами, либов скоростных аммонизаторах-испарителях (САИ).Этот способ обычно используется для переработки неконцентрированной (неупаренной) ЭФК. В случае использования более концентрированной (упаренной) фосфорной кислоты требуется разбавление ее абсорбционной жидкостью (или водой) для обеспечения повышенной влажности (~20% и более) и подвижности пульпы, что в свою очередь снижает производительность. На рис. 2 представлена блок-схема одностадийной нейтрализации в емкостном нейтрализаторе.
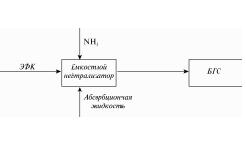
Преимущества:
- возможность переработки неконцентрированной (неупаренной) ЭФК;
- простота технологической схемы;
- удобство управления технологическим процессом.
Недостатки:
- низкая производительность;
- плохие физико-химические свойства удобрений с высоким мольным отношением NH3:H3PO4(МО) 1,7 (ДАФ и NPK-удобрения на его основе) [22].
1.2. Одностадийная нейтрализация в емкостном нейтрализаторе с последующей упаркой пульпы. Этот способ применяется исключительно для переработки неконцентрированной (неупаренной) ЭФК. На рис. 3 представлена блок-схема одностадийной нейтрализации в емкостном нейтрализаторе с последующей упаркой пульпы.
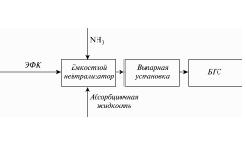
Преимущества:
- возможность переработки неконцентрированной (неупаренной) ЭФК.
Недостатки:
- относительно низкая производительность;
- более сложная схема;
- большее число используемого оборудования;
- нельзя производить удобрения с высоким мольным отношением NH3:H3PO4(МО) – ДАФ и NPK-удобрения на его основе.
1.3. Одностадийная нейтрализация в трубчатом реакторе (ТР). Совместное применение ТР и аппарата БГС позволило создать принципиально новый агрегат ТР-БГС, дающий возможность аммонизировать концентрированную ЭФК под давлением с непосредственным распыливанием пульпы с влажностью 4-8% в зоне гранулирования [23]. Это позволило резко увеличить производительность технологической нитки. Кроме того, вывод пульпы из ТР непосредственно в БГС приводит к значительному (в 1,5 и более раз) снижению расхода природного газа, а при определенных нагрузках и рецикле части подогретого воздуха (например, после охладителя кипящего слоя) возможно достижение автотермического режима сушки. На рис. 4 представлена блок–схема одностадийной нейтрализации в ТР.
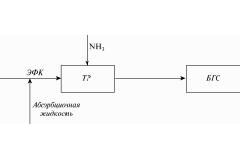
Преимущества:
- высокая производительность;
- простота технологической схемы;
- минимум оборудования;
- удобство управления технологическим процессом;
- снижение энергозатрат, наиболее полное использование тепла химических реакций.
Недостатки:
- необходимость использования концентрированных кислот;
- повышенное отложение шламов в пульпопроводах;
- проблемы с производством удобрений с МО » 1,0 (МАФ и NPK-удобрения на его основе) из-за особенностей гранулирования.
По данным исследований работы агрегата ТР-БГС на пульпе влажностью 4–8%, удовлетворительное гранулирование достигается при МО = 1,20…1,25 или 1,7…1,8. Работа за пределами этого интервала дает избыток мелкой фракции, а внутри – чрезмерное укрупнение и образование комков [23].
2. Двухстадийная нейтрализация
2.1. Двухступенчатая нейтрализация в емкостном нейтрализаторе (либо в аппарате САИ) на первой ступени и в ТР на второй. На первой ступени нейтрализацию проводят до МО, равного 0,7 или 1,4 (для обеспечения максимальной подвижности пульпы при оптимальной влажности), на второй – в ТР до МО, равного 1,0…1,1 или 1,7…1,8 в зависимости от марки производимого удобрения [9, 20, 21, 25]. Выбор конструкции нейтрализатора для первой ступени также определяется ассортиментом выпускаемой продукции. Аппараты САИ, в которых перемешивание зависит от теплового эффекта происходящих в нем реакций [24], целесообразно применять при выпуске одной или максимум двух–трех близких марок удобрений. При более широком ассортименте рекомендуется емкостной реактор с перемешивающим устройством [16]. На рис. 5 представлена блок-схема двухстадийной нейтрализации в емкостном нейтрализаторе и ТР.
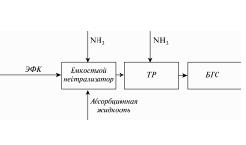
Преимущества:
- возможность использования менее концентрированных кислот, чем при одностадийной нейтрализации в трубчатом реакторе;
- возможность более оперативного и гибкого регулирования гранулометрического и химического состава продукта;
- уменьшение отложения шламов в пульпопроводе от ТР.
Недостатки:
- более сложная технологическая схема;
- большее число используемого оборудования.
2.2. Двухстадийная нейтрализация с промежуточной упаркой «кислых» пульп.Данная технология [1, 26] предусматривает на первой стадии нейтрализацию ЭФК до МО = 0,5…0,8 (так называемая «кислая» пульпа) в емкостном нейтрализаторе (либо в аппарате САИ), затем упарку полученной «кислой» пульпы и донейтрализацию в ТР. В случае производства ДАФ и NPK-удобрений на его основе можно получать на первой ступени и затем упаривать нейтральную пульпу с МО 1,0. На рис. 6 представлена блок-схема двухстадийной нейтрализации с промежуточной упаркой «кислых» пульп.
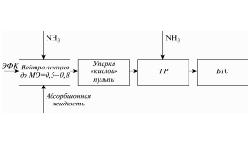
Эта технология обычно применяется для переработки ЭФК с повышенным содержанием примесей соединений магния, железа и алюминия, которая плохо поддается концентрированию из-за повышенной вязкости.
Преимущества:
- более высокая производительность, чем при одностадийной нейтрализации в емкостном нейтрализаторе или САИ;
- возможность переработки ЭФК с повышенным содержанием соединений магния, железа и алюминия;
Недостатки:
- более сложная схема;
- большее число используемого оборудования.
Как уже отмечалось, выбор той или иной схемы нейтрализации во многом определяется концентрацией исходной ЭФК и маркой производимых удобрений. Так, для производства ДАФ при использовании фосфорной кислоты с содержанием Р2О5 менее 36% целесообразны варианты 1.1, 1.2 и 2.2. При содержании Р2О5 от 36 до 42%рекомендуется применять схему по варианту 2.1, а для более концентрированной кислоты (43% Р2О5 и более) – по варианту 1.3 [9, 20, 21, 25]. Специалистами АО «НИУИФ» была разработана универсальная гибкая схема нейтрализации (рис. 7), позволяющая вести аммонизацию ЭФК по одностадийному либо по двухстадийному способу в зависимости от ее концентрации.
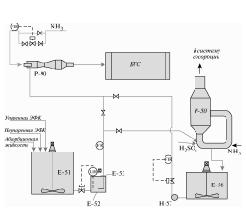
Е-51 – бак фосфорной кислоты; Е-52, Е-53 – расходный бак с насосом; Р-50 – аппарат САИ; Е-56 – бак пульпы; Р-90 – трубчатый реактор
3. Нейтрализация с «раскислением» (смешением «щелочной» пульпы с МО = 1,4 и упаренной ЭФК с содержанием Р2О5 не менее 52%)
По данному способу неконцентрированная фосфорная кислота нейтрализуется аммиаком в емкостном нейтрализаторе или в аппарате САИ до МО = 1,4 с последующим взаимодействием полученной пульпы с упаренной ЭФК с образованием моноаммоний фосфата (МО = 1,0…1,1).При этом концентрированная фосфорная кислота может вводиться разными способами: предварительно наноситься на поверхность ретура, распыливаться на завесу ретура одновременно с пульпой или подаваться в ТР перед БГС [20, 21, 27, 28]. Опытным путем установлено, что наиболее оптимальным является вариант с ТР как более производительный и обеспечивающий наилучшее качество продукта. Нейтрализация по этому варианту также идет с выделением тепла, так как тепловой эффект образования моноаммоний фосфата из фосфорной кислоты в ~2 раза больше, чем диаммонийфосфата из моноаммоний фосфата. Этот способ применим также для производства некоторых марок NPS-удобрений, в этом случае для снижения МО может использоваться и серная кислота.На рис. 8 представлена блок-схема двухстадийной нейтрализации с «раскислением» (со смешиванием пульпы с МО 1,4 и упаренной ЭФК).
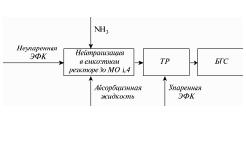
Внедрение данного способа на одном из российских заводов позволило при получении МАФ достичь производительности 60 т/ч, и это не является пределом.
Преимущества:
- относительно высокая производительность при выпуске МАФ и некоторых марок NPS-удобрений;
- ТР не требует ввода аммиака, и при его установке не возникает вопросов по категорированию помещений.
Недостатки:
- позволяет производить только марки удобрений с МО = 1,0…1,1;
- требуется наличие части ЭФК в упаренном виде;
- при распыливании ЭФК и пульпы на завесу ретура получается МАФ более низкого качества, склонный к слеживаемости.
Специалистами АО «НИУИФ» разработана гибкая технологическая схема получения широкого ассортимента комплексных фосфорсодержащих удобрений (рис. 9) [19].
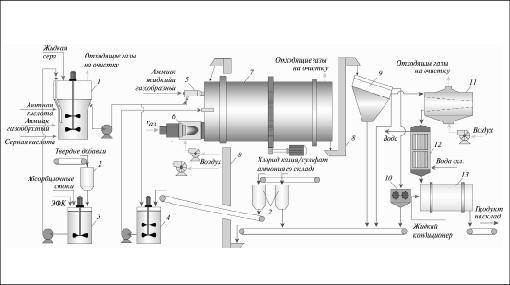
1 – преднейтрализатор; 2 – бункеры; 3 – сборник кислоты; 4 – бак смешения пульпы с хлористым калием; 5 – трубчатый реактор; 6 – топочно-горелочное устройство; 7 – БГС; 8 – элеваторы; 9 – грохот; 10 – дробилка; 11 – холодильник «кипящего слоя»; 12 – охладитель Solex; 13 – барабан-кондиционер
Данная схема позволяет выпускать различные виды удобрений: NP – МАФ 15:52, ДАФ 18:46; NPS – 16:20:0: 12(S), 20:20:0:14(S), 19:38:0:7(S), 14:34:0:8(S) и др.; NPK – 10:26:26, 9:25:25, 8:24:24, 13:19:19, 15:15:15, 16:16:16, 10:15:15, в том числе с микроэлементами и др.; NPS+S с элементной серой – 12:40:0:5+5(S), 13:33:0:7,5+7,5(S) [29]. Все получаемые удобрения имеют хорошие физико-химические свойства.
На рис. 10 представлена еще одна гибкая технологическая схема, позволяющая производить: PK – 0:24:24, 0:20:30 и др.; РКS – 0:20:20:5(S); NPK – 5:15:30, 4:16:34, 4:30:10, 4:30:15, в том числе с микроэлементами и др.; NPKS – 1:20:20:5(S), 4:20:20:5(S), 2:20:18:5(S):0,2(В) и др. [30–32].
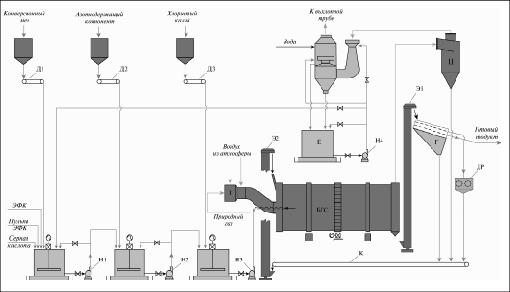
Б1–3 – бункеры, Д1–3 –дозаторы, Р1-3 – реакторы, Н1–4 –насосы, К – конвейер, Э1–2 – элеваторы, Е – сборник абсорбционной жидкости, АПС – абсорбер пенный скоростной, АВ – абсорбер вентури, Ц – циклон, Г – грохот, ДР – дробилка, Т – топка
Разработана и запатентована перспективная, не имеющая аналогов гибкая схема АГ-БГС, сочетающая преимущества обоих способов [33].В настоящее время ведутся работы по внедрению ее на одном из российских предприятий.
Таким образом, универсальные, компактные и экономичные схемы, оснащенные БГС, совмещающие в одном аппарате процессы гранулирования и сушки, на наш взгляд, имеют хорошую перспективу и могут быть альтернативой традиционным схемам АГ-СБ.
Список литературы
1. Кононов А.В., Стерлин В.Н., Евдокимова Л.И.Основы технологии комплексных удобрений. М.: Химия, 1988. 320 с.
2. А.с. СССР№216639.
3. А.с. СССР№554881. Устройство для гранулирования материалов
4. Классен П.В., Гришаев И.Г.Основы техники гранулирования. М.: Химия, 1982. 272 с.
5. Пат. Бельгии№727276. Dry-granulated ammonium salts.
6. Лыков М.В.Труды НИУИФ, 1980. Вып. 237. С. 3–5.
7. Шахова Н.А., Пронин А.И., Гришаев И.Г.//Химическаяпромышленность. 1973. №12. С. 905–907.
8. Норов А.М., И.Г. Гришаев, Малявин А.С. и др.Технология гранулированного диаммонийфосфата из неконцентрированной экстракционной фосфорной кислоты//Химическая технология. 2011. №10. Т. 12. С. 589–593.
9. Норов А.М.Разработка технологии диаммонийфосфата из неконцентрированной экстракционной фосфорной кислоты с использованием барабанного гранулятора-сушилки. Дис. … канд. техн. наук. М.: ОАО «НИУИФ», 2014. 130 с.
10. Гришаев И.Г. Гранулообразование в газожидкостной струе, затопленной в потоке падающего материала//Химическая промышленность. 1999. №11. С. 720–724.
11. Норов А.М., Малявин А.С., Овчинникова К.Н. и др.Разработка норм оптимального технологического режима производства гранулированного диаммонийфосфата из неконцентрированной фосфорной кислоты//Химическая технология. 2012. №11. Т. 13. С. 641–647.
12. Гришаев И.Г., Норов А.М., Соколов В.В., Малявин А.С.Исследование влияния режимов гранулирования на качество диаммонийфосфата//Тезисы докладов на ХIХ Менделеевском съезде по общей и прикладной химии. Волгоград: ВолгГТУ, 2011. Т. 3. С. 14.
13. Гришаев И.Г., Норов А.М.Производительность барабанного гранулятора-сушилки и качество фосфатов аммония//Химическое и нефтегазовое машиностроение. 2011. №5. С. 22–23.
14. Гришаев И.Г.Разработка конструкции барабанных грануляторов-сушилок для производства минеральных удобрений//Труды НИУИФ. М., 2009. C. 154–158.
15. Пат. РФ №RU2545328. Способ регулирования процесса гранулирования фосфорсодержащих удобрений.
16. Норов А.М., Малявин А.С., Цикин М.Н.Модернизация | и развитие производства комплексных фосфорсодержащих удобрений//В сб.: Современные тенденции в производстве и применении фосфорсодержащих удобрений и неорганических кислот. Материалы Международной научно-практической конференции 26 мая 2015 года//М.: АО «НИУИФ», 2015. 129 с.
17. Классен П.В., Гришаев И.Г., Шомин И.П.Гранулирование. М.: Химия, 1991. 240 с.
18. Технология фосфорных и комплексных удобрений/Под ред. С.Д. Эвенчика и А.А. Бродского. М.: Химия, 1987. 464 с.
19. Норов А.М.Развитие производств фосфорсодержащих минеральных удобрений и создание гибких технологий//Химическая техника. №2. 2017. С. 30–32.
20. Давыденко В.В., Норов А.М., Гришаев И.Г. и др. Опыт технического перевооружения производства удобрительных фосфатов аммония на ООО «Балаковские минеральные удобрения»//Бюллетень «Мир серы, N, P и К». 2011. Вып. 2. С. 4–11.
21. Черненко Ю.Д., Норов А.М., Гришаев И.Г.и др. Возможности интенсификации производства комплексных фосфорсодержащих удобрений//Химическая техника. №10. 2011. С. 10–15.
22. Норов А.М., Овчинникова К.Н., Малявин А.С.и др. Влияние концентрации ЭФК и содержания в ней примесей фтора и магния на физические свойства фосфатов аммония//Химическая технология. Т. 13, №10. 2012. С. 577–586.
23. Гришаев И.Г., Гриневич В.А. Особенности получения диам-монийфосфата по схеме с барабанным гранулятором-сушилкой//Труды НИУИФ. М., 2009. С. 100–103.
24. Гришаев И.Г., Назирова Л.З., Федюшкин Б.Ф.Способы аммонизации в технологии минеральных удобрений. М.:НИИТЭХИМ, 1988.
25. Пат. ЕАПВ№016144. Способ получения гранулированного диаммонийфосфата.
26. Пат. ЕАПВ№020676. Способ получения гранулированного аммофоса.
27. Гришаев И.Г., Норов А.М., Малявин А.С.Создание и внедрение реакторов в производстве фосфатов аммония//Труды НИУИФ. М., 2009. С. 330–335.
28. Пат. РФ№RU2370477. Способ получения гранулированного аммофоса.
29. Пат. РФ№RU2561444. Способ получения серосодержащего сложного удобрения.
30. Пат. РФ№RU2514306. Способ получения фосфорно-калийного гранулированного удобрения.
31. Пат. РФ№RU2551541. Способ получения комплексного удобрения.
32. Норов А.М., Овчинникова К.Н., Малявин А.С., Пагалешкин Д.А., Федотов П.С., Петропавловский И.А.Разработка технологии фосфорно-калийных удобрений с использованием карбонатов калия и кальция//Химическая технология. 2014. №2.С. 75–79.
33. Пат. РФ№RU2455228. Способ получения гранулированных фосфатов аммония.