Автор: А.В. Шаповалов (ООО «Прюфтехник»).
Опубликовано в журнале Химическая техника №12/2016
Компания PRUFTECHNIK – мировой лидер в производстве приборов для лазерной центровки, вибродиагностики и балансировки машинного оборудования. ООО «Прюфтехник» является дочерней структурой немецкой компании PRUFTECHNIK на территории России и стран СНГ.
Незапланированные простои оборудования существенно сказываются на производительности предприятия и конечном результате. Значительную статью расходов составляет техническое обслуживание оборудования современного производства. Вместе с тем есть реальная возможность оптимизировать эти затраты и поддерживать в порядке все системы производства, обслуживая оборудование в соответствии с его текущим техническом состоянием. Это позволяет контролировать состояние машин, качество производства, а также поддерживать производственный процесс на оптимальном уровне.
Мониторинг технического состояния означает, что каждая машина регулярно подвергается проверке на «состояние здоровья» с помощью вибродиагностики. Решающее значение при этом имеют используемые измерительные приборы: как переносные виброанализаторы, так и стационарные системы мониторинга.
Стационарная система вибромониторинга применяется в качестве современного инструмента не только для повышения безопасности и надежности оборудования, но и для сокращения эксплуатационных затрат на находящееся под мониторингом оборудование. Так, на одном из предприятий затраты на техническое обслуживание составляли 51 800 евро за 5 мес. В результате внедрения стационарной системы мониторинга компрессоров ожидалось снижение этих затрат до 19 500 евро, т.е. в 2,6 раза. Однако реальная сумма затрат на техническое обслуживание составила 9 500 евро – в 5,4 раза меньше. Другими словами, на техническое обслуживание было затрачено всего 18% запланированной суммы.
Это наглядно показывает, что правильный расчет и внедрение серьезной программы по мониторингу состояния являются ключевыми факторами успеха. Кроме того, качество выполняемых ремонтных работ, профессиональное обучение и тренинг ремонтного персонала, четкая отчетность и другие дополнительные меры позволят выйти за пределы ожидаемых результатов.
Еще один резерв кроется в снижении затрат от внеплановых остановок оборудования, находящегося под мониторингом (рис. 1). Снизилась частота незапланированных работ, кроме того значительно уменьшилась и продолжительность незапланированных остановок.
В зависимости от типа компрессора могут быть применимы различные методы диагностики: по спектрам, временным сигналам, орбитам и ударным импульсам.
При этом в большинстве случаев необходим комплексный подход с применением нескольких методов.
Значительная часть компрессоров сейчас оснащается системами аварийного выключения. В силу маркетинговой политики у «основоположников» – производителей систем аварийного выключения – дополнительные модули диагностики имеют значительную стоимость. Некоторые производители систем защиты, например Bently Nevada, изначально обеспечивают возможность подключения сторонних приборов для периодической диагностики оборудования, например виброанализаторы VIBXPERTII (рис. 2, а); или стационарные системы вибромониторинга и диагностики, такие как VIBNODE, VIBROWEB или VIBGUARD (рис. 2, б). Таким образом, система защиты дополняется полноценным мониторингом и диагностикой без установки дополнительных датчиков.
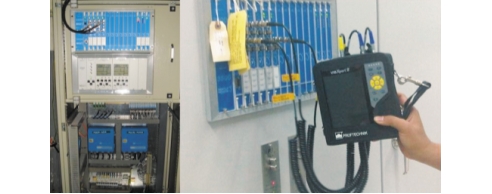
Данный метод подключения позволяет, кроме того, использовать и метод построения орбит траектории вращения вала в движении и траектории движения центра вала на разгоне/выбеге, используемые для диагностики подшипников скольжения (рис. 3).
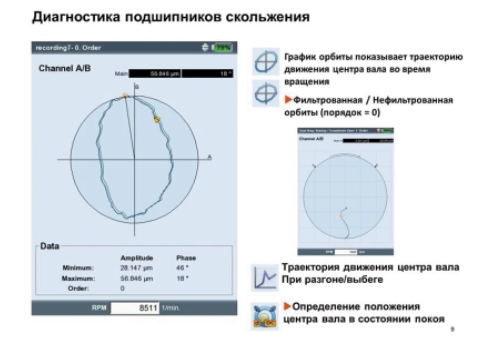
В случае подшипников качения незаменимым является контроль их состояния методом ударных импульсов. Благодаря уникальной запатентованной конструкции датчиков вибрации (акселерометров) TANDEM-Piezo® производства компании PRUFTECHNIK имеется возможность оценки состояния оборудования сразу по двум методам: измерению общего уровня вибрации в диапазоне частот от 0,5 Гц до 20 кГц и измерению ударного импульса на резонансе 36 кГц. Ударные импульсы возникают в подшипниках качения (высокочастотные сигналы указывают на степень повреждения подшипника задолго до его выхода из строя). Данный метод заслуживает более подробного описания.
Ударные импульсы, наблюдаемые на «звуковых частотах», вызываются в первую очередь взаимодействием вращающихся компонентов подшипника качения, а также фрикционными процессами, происходящими в нем.
При этом они не включают вибрацию всех остальных компонентов машины с их значительной массой. Наверняка многие знакомы с процессом «прослушивания» роликового подшипника с помощью отвертки и хорошо представляют себе характерный дребезжащий звук или жужжащий «шум перекатывания элементов качения».
Основным определяемым параметром в данном случае является вибрационное ускорение и его кратковременные повышения. Соответствующие параметры фиксируются в линейном частотном диапазоне датчиков ускорения, ширина которого должна быть как можно больше – до 10 или 20 кГц. Для того чтобы отделить вибрацию самой машины, рекомендуемый нижний частотный предел должен составлять 1 кГц или меньше. Исходя из практики, оптимальным является диапазон, превышающий десятикратное значение частоты вращения.
Данные измерения могут быть произведены с частотой до 40 кГц, что при условии совпадения с резонансными частотами датчика вибрации в данной области позволит получить большую помехоустойчивость и соответственно лучшую достоверность данных.
Пиковые значения (максимальное значение в случае ударного импульса) представляют собой характеристические значения, которые, если говорить проще, образуются в результате ударов элементов качения по кольцу (внутреннему или наружному) подшипника качения при прохождении через локальный дефект. Помимо характеристик состояния определяются эффективные значения (фоновое значение в случае ударного импульса), которые отражают шум, производимый гладкой или неровной поверхностью кольца подшипника. Главная цель измерения указанных характеристик заключается в определении степени повреждений кольца подшипника в зависимости от ее выраженности.
Значительным преимуществом данного метода является возможность определения соотношения между логарифмическими характеристиками состояния в децибелах, с одной стороны, и диаметром вала и скоростью вращения подшипника – с другой. Это дает возможность сравнения различных подшипников между собой и определения общих предельных значений. Таким образом, оказывается решена главная проблема, связанная с проведением измерений на подшипниках качения – определение предельных значений.
Тем не менее, достаточно достоверные данные можно получить только на основании кривой тренда, определяемой на протяжении достаточно длительного периода, в то время как единичные измерения могут быть использованы исключительно для предварительной оценки.
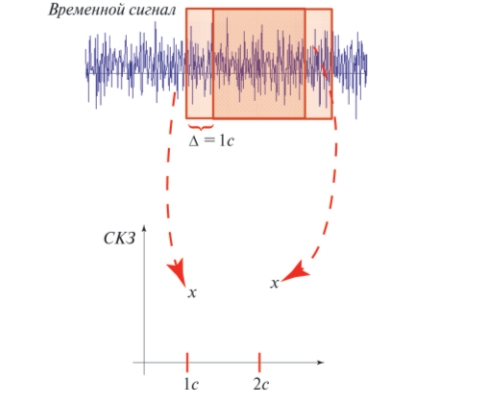
В завершение следует сказать и о новой разработке компании PRUFTECHNIK – стационарной системе VIBGUARD c 20-ю синхронными каналами. Данная система отлично подходит для диагностики компрессоров, совмещая в себе все перечисленные методы – временной сигнал, спектр, орбиты и ударный импульс. Интервал измерений VIBGUARD составляет 1 с, таким образом, ни одно событие не будет пропущено (рис. 4). Применение трехосевых датчиков (рис. 5) вибрации с VIBGUARD позволяет существенно сократить затраты и время на монтаж, а также уменьшить число кабелей. При этом немаловаж-ной является возможность мгновенной передачи полученных значений и тревог в АСУТП по протоколу Modbus для дальнейшего принятия решений.
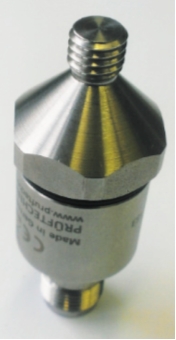
Система VIBGUARD может быть использована также в качестве мобильной системы диагностики – она выполнена в переносном кейсе со встроенным дисплеем и промышленным компьютером. Такая система незаменима для временной диагностики проблемного агрегата.