Авторы: С.В. Афанасьев (Тольяттинский государственный университет), О.С. Рощенко (ОАО «Тольяттиазот»), С.П. Сергеев (ОАО «ГИАП»).
Опубликовано в журнале Химическая техника №11/2015
В настоящее время считается общепризнанным, что появление фотохимического смога в промышленных городах обусловлено высокой концентрацией в тропосфере формальдегида и оксидов азота.
Для улавливания формальдегида из абгаза, выходящего с верха абсорбционной колонны производства карбамидоформальдегидного концентрата, нами внедрены каталитические реакторы-дожигатели, конструкция одного из которых показана на рис. 1.
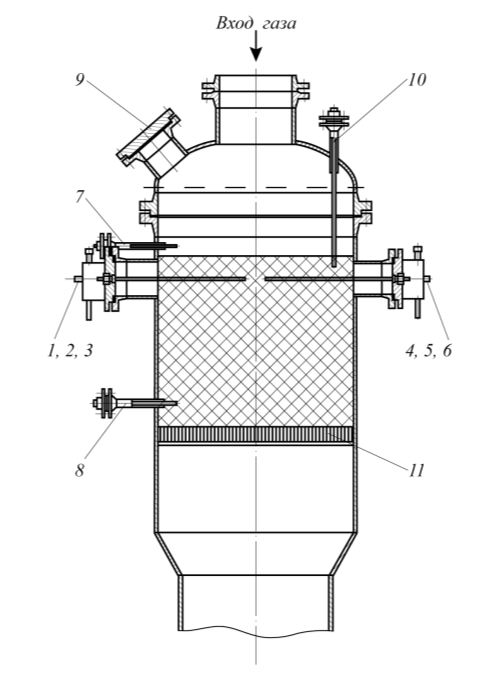
Реактор-дожигатель включает металлический корпус с установленными в нем термодатчиками 7, 8, 10 и закрепленной внутри решеткой 11 с размещенным на ней слоем катализатора, в котором симметрично расположены от двух до шести электроподогревателей 1…6, выведенных на регулятор мощности, а отношение диаметра аппарата к высоте катализаторного слоя равно ~1 (0,6…1,4). Аппарат снабжен люком 9 для загрузки и выгрузки катализатора [1].
Окисление формальдегида протекает на слое платинового катализатора марки PPt-47, насыпанного высотой 800 мм на решетку 11, в котором смонтированы шесть U-образных электроподогревателей, размещенных строго симметрично по сечению аппарата. Перед пуском аппарата в работу с помощью электрических нагревательных элементов температуру в верхнем слое катализатора повышают до 250°С. В этот момент в реактор начинают непрерывно подавать газовую смесь, содержащую оксид углерода, метиловый спирт, формальдегид и диметиловый эфир в количестве 14,6 г/с. За счет теплоты экзотермической реакции происходит прогрев всего катализаторного слоя, и с термодатчиков на регулятор мощности поступает сигнал об отключении электронагревателей. В дальнейшем температура в зоне реакции на уровне 250…260°С поддерживается вследствие протекания химического процесса. В результате каталитического окисления компонентов газовой смеси со степенью конверсии в диоксид углерода и воду на уровне 96% их содержание на выходе из реактора снижается до 0,6 г/с, и данная концентрация загрязнителей уже не представляет угрозы окружающей среде.
С целью сокращения расхода электрической энергии было предложено нейтрализацию формальдегидсодержащего газа проводить в реакторном блоке, включающем контактный аппарат каталитического окисления метанола в формальдегид 4, котел-утилизатор 5, компаблок 7 и реактор-дожигатель 1 полочного или трубчатого типа (рис. 2).
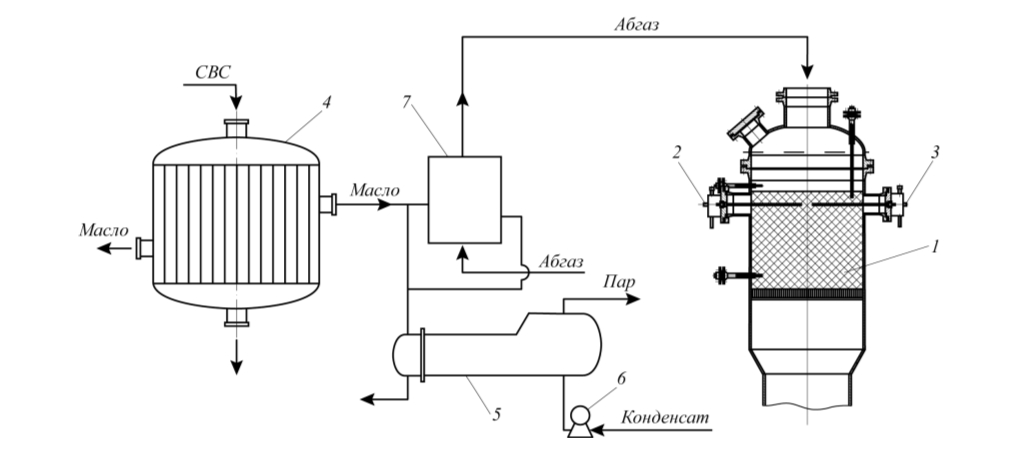
Как и компаблок, котел-утилизатор является теплообменником, и при подаче в него деминерализованной воды с помощью насоса 6 трансформирует теплоту химических реакций, протекающих в аппарате 4, в пар давлением 1,2 МПа.
Аппарат каталитического дегидрирования метанола в формальдегид 4, входящий в реакторный блок, является стальным теплоизолированным аппаратом диаметром 4 000 мм, в котором в трубных досках установлены 10 800 трубок длиной 1 100 мм и диаметром 25×2 мм. Суммарная площадь теплообмена – 803 м2. Трубная доска разделена на секторы, в каждом из которых находится по 900 отверстий. Реакторные трубки на 75% длины заполнены гранулами железо-молибденового катализатора торговой марки КН-26С. Гранулы – полые цилиндры, содержащие 80% мас. МоО3 и 20% мас. Fe2O3; верхняя часть трубок заполнена инертной керамической насадкой. В межтрубном пространстве циркулирует масло (высокотемпературный теплоноситель АМТ-300У), которое снимает теплоту экзотермической реакции при подаче в аппарат спиртовоздушной смеси (СВС).
Котел-утилизатор трубчатого типа 5 имеет длину 4 145 мм и диаметр 1 000 мм, а компаблок 6 – площадь поверхности теплообмена 4,88 м2 и габаритные размеры 666×666×613 мм.
Предложенный реакторный блок работает следующим образом. С помощью электрических нагревательных элементов 2, 3 температуру слоя катализатора в реакторе 1 повышают до 250°С. При выведенном на производственный режим аппарате 4 в компаблок начинают непрерывно подавать газовую смесь, содержащую оксид углерода, метиловый спирт, формальдегид и диметиловый эфир в количестве 14,6 г/с следующего состава, мас. %:
N2 89,81…89,95;
О2 6,05…6,18;
Н2О 1,70… 1.80;
СН3ОН 0,10…0,14;
СО 1,41…1,57;
СН3ОСН3 0,56…0,68;
СН2О 0,02…0,04
При достижении нужной температуры газовой смеси в компаблоке (250…260°С) электрообогрев в реакторе 1 отключают. Необходимый для нормального течения реакции температурный режим в дальнейшем поддерживается подогревом абгаза теплоносителем марки АМТ-300У от реактора 4 и теплотой экзотермических реакций в катализаторном слое.
В результате каталитического окисления компонентов газовой смеси со степенью конверсии в диоксид углерода и воду на уровне не менее 96% содержание загрязнителей на выходе из реактора-дожигателя снижается до 0,5 г/с.
Таким образом, по сравнению с известными техническими решениями предложенная конструкция реакторного блока отличается простотой исполнения и более эффективна при каталитической очистке абгаза, выходящего из узла абсорбции формальдегида.
С целью очистки дымовых газов аммиачного производства от оксидов азота был разработан оригинальный способ, схема которого представлена на рис. 3.
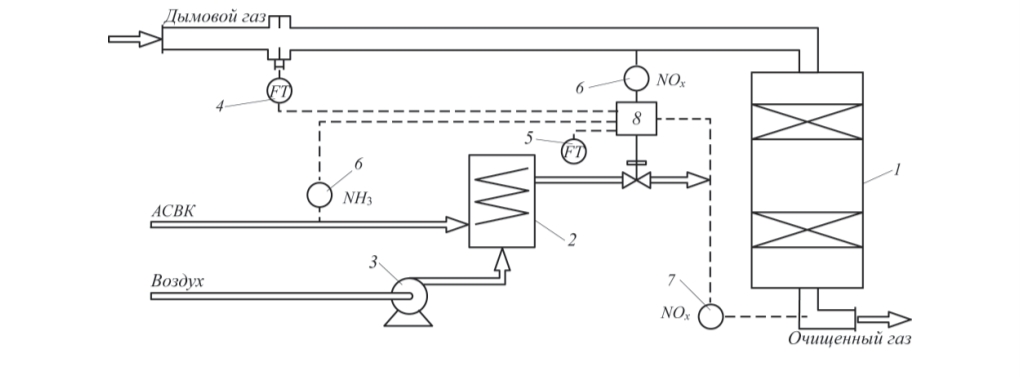
1 – реактор; 2 – теплообменник; 3 – воздуходувка; 4 – датчик расхода дымового газа; 5 – датчик расхода АСВК;
6 – газоанализатор содержания аммиака; 7 – газоанализатор содержания оксидов азота; 8 – блок управления
Поток очищаемых газов смешивается с воздухом и аммиаксодержащим восстановительным компонентом (АСВК), в качестве которого используют танковые газы производства аммиака, а селективное каталитическое восстановление осуществляют в реакторе при температуре 250…450°С на катализаторе блочного типа.
В отличие от известных методов очистки дымовых газов от оксидов азота предусмотрено их смешение с воздухом и АСВК, в качестве которого взяты танковые газы производства аммиака следующего состава, об. %:
NH3 20…30
CH4 18…24
H2 25…35
Ar 3,8…4,8
N2 остальное, а селективное каталитическое восстановление оксидов азота дымовых газов проводят в реакторе при температуре 250…350°С на вольфрамо-ванадиевом оксидном катализаторе [3–5].
Эффективность удаления NOх на данном катализаторе может достигать 90% и более с проскоком аммиака ниже 50 ppm, в то время как некаталитические методы характеризуются гораздо меньшей степенью очистки, а проскок аммиака с трудом может быть отрегулирован на приемлемом уровне.
Важно отметить, что в случае предлагаемого способа очистки наряду с аммиаком оксиды азота взаимодействуют и с другими компонентами восстановительной системы, в частности с водородом и метаном.
При этом протекают каталитические химические реакции, конечными продуктами которых являются азот, вода и двуокись углерода: 4NO + 4NH3 + O2 → 4N2 + 6H2O; 6NO2 + 8NH3 → 7N2 + 12H2O;
CH4 + 4NO → CO2 + 2H2O + 2N2;
CH4 + 2NO2 → CO2 + 2H2O + N2; 2H2 + 2NO → 2H2O + N2; 4H2 + 2NO2 → 4H2O + N2.
Также найдено, что при полном окислении аммиака, метана и водорода потенциальный рост температуры в зоне реакции составляет 5…10°С.
В соответствии с приведенной схемой дымовые газы с трубчатых печей, содержащие О2 – 6,2…8,2 об. %;
H2O – 10,0…13,0 об. %; NOх – 200…700 мг/м3; СО2 – 4,9…6,9 об. %; СО – 70…150 мг/м3; SO2 – 4,9…11,3 мг/м3;
N2 – остальное и имеющие температуру 290…300°С, смешиваются с воздухом и подогретым до этой же температуры АСВК вышеуказанного состава и направляются в реактор селективного каталитического восстановления.
Выбранная температура является оптимальной, так как при ее снижении возможно образование смеси нитрита и нитрата аммония, а в случае более высокой – снизится селективность работы катализатора.
Необходимое массовое соотношение между оксидами азота в дымовых газах и аммиаком в АСВК регулируется датчиками расхода, а также газоанализаторами содержания аммиака и оксидов азота, выведенных на блок управления установки. Объем реакторного блока и масса катализатора рассчитываются, исходя из количества очищаемых дымовых газов. Расход воздуха преимущественно зависит от содержания монооксида азота в дымовых газах и достигается с помощью воздуходувки.
К достоинствам предлагаемого способа следует отнести то, что степень очистки нитрозных газов регулируется скоростью их подачи в зону реакции и отношением объема дымовых газов к АСВК.
Таким образом, в результате проведенного исследования предложены высокоэффективные каталитические способы нейтрализации смогообразующих газов – формальдегида и оксидов азота от стационарных источников. Внедрение данной технологии на промышленных предприятиях г. Тольятти позитивно отразится на экологической обстановке в регионе.
Список литературы
- Афанасьев С.В., Рощенко О.С., Калинин С.А. Каталитические способы снижения выбросов формальдегида для предотвращения фотохимического смога//Сб. докладов 16 междунар. науч.-практ. конф. «Древесные плиты: теория и практика». СПб.: СПбЛТА, 2013.
- Патент на полезную модель RU №128836. МПК В 01J 8/08. Реакторный блок.
- Справочник азотчика. Изд. 2-е переработанное. М.: Химия,1986.
- Патент на изобретение RU №2296000 России, МПК В 01 D 53/56, В 01 D 53/86, В 01 J 23/16. Способ очистки дымовых газов от оксидов азота.
- Афанасьев С.В., Трифонов К.И. Физико-химические процессы в техносфере. Учебник/Самара. Изд-во Сам. научн. центра РАН, 2014. 195 с.