Автор: С.В. Афанасьев (Тольяттинский государственный университет),
О.С. Рощенко (ОАО «Тольяттиазот»), С.П. Сергеев (ОАО «ГИАП»).Опубликовано в журнале Химическая техника №12/2015
Технологические процессы окисления метанола в формальдегид с применением металлооксидных катализаторов широко используются в нашей стране и за рубежом, например при синтезе карбамидоформальдегидного концентрата, используемого в производстве древесно-стружечных и волокнистых плит [1–4]. Принципиальная схема одного из них приведена на рис. 1. Данная схема была разработана в ОАО «Тольяттиазот» и впервые в России реализована на данном предприятии.
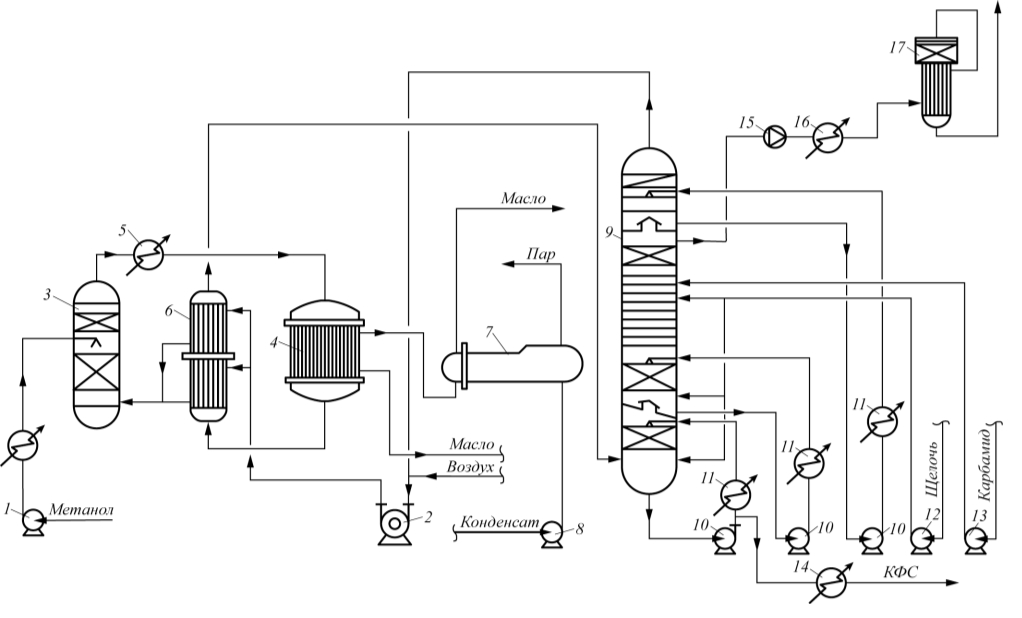
1 – насос метанола; 2 – нагнетатель смеси воздуха с обгазом; 3 – спиртоиспаритель; 4 – реактор; 5 – подогреватель спиртовоздушной смеси; 6 – теплообменник; 7 – парогенератор; 8 – насос конденсата; 9 – абсорбер; 10 – циркуляционный насос абсорбера; 11 –теплообменник; 12 – насос щелочи; 13 – насос карбамидного раствора; 14 – холодильник КФК-80; 15 – вентилятор; 16 – подогреватель газов; 17 – реактор каталитического дожига газов
Основным аппаратом установки является реактор окислительного дегидрирования метанола в формальдегид. В настоящее время наибольшее распространение получили три типа реакторов [2]:
- трубчатые аппараты типа теплообменник, в которых катализатор расположен в трубках малого диаметра, в межтрубном пространстве находится теплоноситель, охлаждающий катализатор и продукты реакции. Процесс в этих реакторах выполняется с внутренним теплоотводом в условиях, близких к изотермическим;
- комбинированные реакторы, в которых вначале расположена трубчатая часть по первому типу реактора, а затем один слой катализатора, в котором происходит доокисление не прореагировавшего в трубчатой части реактора метанола;
- многослойные многополочные многосекционные реакторы с несколькими слоями катализатора, где каждый его слой работает без охлаждения с адиабатическим разогревом продуктов реакции и охлаждением их после каждого слоя. Процесс в этих конструкциях реакторов предусматривает промежуточное охлаждение продуктов реакции.
В реакторах первого и второго типов в межтрубном пространстве находится жидкий теплоноситель, снимающий основное количество тепла экзотермических реакций.
В связи с тем, что максимум температуры приходится на среднюю часть контактного аппарата и здесь же находится область максимальной параметрической чувствительности, ввод жидкого теплоносителя выгоднее производить именно в центральную часть межтрубного пространства, а вывод осуществлять снизу и сверху.
Это обстоятельство было учтено авторами патента [5] при разработке усовершенствованной конструкции контактного аппарата окислительного дегидрирования метанола производительностью не менее 25 000 т в год при пересчете на карбамидоформальдегидный концентрат марки КФК-85 (рис. 2).
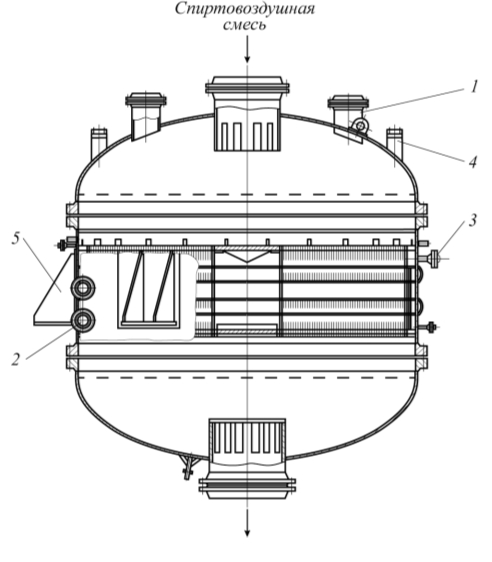
Для достижения требуемых производственных показателей процесса превращения метанола в формальдегид авторами патента [5] предложен принципиально новый аппарат, в котором в трубных досках установлены около 10 000 трубок диаметром 25х2 мм площадью теплообмена 800 м2 [5]. Трубная доска разделена на секторы, в каждом из которых находится по 900 отверстий.
Реакторные трубки заполнены гранулами железомолибденового катализатора марки КН-26С фирмы «Персторп Формокс» в виде полых цилиндров, содержащего 80 % мас. МоО3 и 20 % мас. Fe2O3, верхняя часть – инертной керамической насадкой. В каждом секторе имеется часть незаполненных трубок, которые предназначены для установки термопар. Реактор снабжен штуцерами ввода теплоносителя (симметрично по два в каждую из зон) и двенадцатью штуцерами вывода теплоносителя из центрально расположенной перфорированной трубы аппарата. Для защиты реактора от разрушения при взрыве газовой смеси на верхней крышке установлены предохранительные мембраны с давлением срабатывания 0,41… 0,51 МПа. Жидкий теплоноситель подается в межтрубное пространство четырех зон, расположенных одна над другой, радиально по периферии трубного пучка.
Реактор работает следующим образом. В верхнюю часть контактного аппарата подается подогретая до температуры 190…210°С спиртовоздушная смесь, содержащая 6–8 % об. метанола и 8–11 % об. кислорода. При температуре 220…240°С (условие зажигания катализатора) в верхней зоне трубного пучка начинается процесс образования формальдегида, сопровождающийся большим выделением тепла. Съем тепла осуществляется подачей масла АМТ300У во все четыре зоны реактора.
Проходя через межтрубное пространство к центру аппарата, теплоноситель поступает в котел-утилизатор, где аккумулированное тепло расходуется на производство пара. Состав газовой смеси на выходе из реактора определяется профилем температуры по высоте аппарата, который в свою очередь зависит от содержания метанола и кислорода в спиртовоздушной смеси, нагрузки на аппарат, активности железо-молибденового катализатора, температуры и объема теплоносителя, поступающего в межтрубное пространство.
Для аппарата, выведенного на оптимальный режим работы, конверсия метанола в формальдегид достигает 95%.
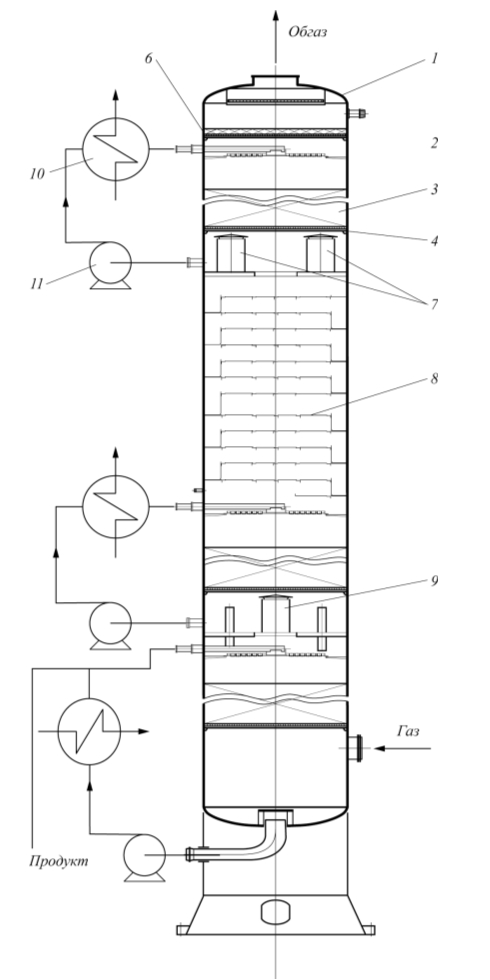
6 – каплеотбойник; 7, 9 – камеры для уровнемеров;
8 – тарельчатая зона; 10 – пластинчатый теплообменник;
11 – циркуляционный насос
На рис. 3 показан общий вид абсорбционной колонны улучшенного типа, рассчитанной на выпуск 25 000 т/год карбамидоформальдегидного концентрата марки КФК-85.
Она представляет собой стальной теплоизолированный аппарат диаметром 2 600 мм и высотой 36 740 мм.
Внутри аппарата расположены три тарелки, предназначенные для распределения потоков жидкой фазы, поступающих на насадочные секции. В качестве насадки использованы кольца Палля из нержавеющей стали, насыпанные в несколько слоев на решетки, приваренные к корпусу. Между насадочными секциями находятся камеры с уровнемерами, предназначенные для поддержания необходимого уровня жидкой фазы по высоте массообменного аппарата [6].
В колонне имеется тарельчатая зона, состоящая из двенадцати тарелок, на которые подается раствор карбамида концентрацией 50–64% мас. и 6–10% -ного водного раствора щелочного агента.
Поддержание необходимой температуры жидкой фазы в насадочных секциях достигается путем циркуляции жидкой фазы через пластинчатые теплообменники 10 с помощью насосов 11.
Реакторы рассмотренных конструкций успешно эксплуатируются в ОАО «Тольяттиазот». Они могут найти применение при синтезе безметанольного формалина в производстве изопрена и других отраслях промышленности. К их достоинствам относятся пониженный расход метанола на единицу производимой продукции, более длительный срок эксплуатации железомолибденового и платинового катализаторов, ничтожно малое влияние на окружающую среду [7].
В случае необходимости они могут быть также использованы и для организации производства безметанольного концентрированного формалина повышенной мощности.
Список литературы
- Патент на изобретение RU №2142964 России, МПК: С 08 G 12/12.Способ получения карбамидоформальдегидного концентрата.
- Махлай В.Н., Афанасьев С.В. Химия и технология карбамидоформальдегидного концентрата. Монография. Самара: Изд-во СНЦ РАН, 2007. 234 с.
- Патент на изобретение RU №2196147 России, МПК: С 08 G 12/12.Способ получения карбамидоформальдегидного концентрата.
- Афанасьев С.В., Трифонов К.И. Физико-химические процессы в техносфере. Учебник. Самара: Изд-во Сам. научн. центра РАН, 2014 195 с.
- Патент на полезную модель RU №40012 России, МПК: B 01 J 8/08. Реактор.
- Патент на полезную модель RU №66224 России: МПК В 01 J 8/08. Колонна абсорбции.
- Афанасьев С.В., Махлай С.В. Карбамидоформальдегидный концентрат. Технология. Переработка. Самара: Изд-во Сам. научн. центра РАН, 2014. 298 с.