Автор: А. Ю. Паньшин (ОАО «НИИК»)
Опубликовано в журнале Химическая техника №7/2017
Одним из основных направлений деятельности ОАО «НИИК» при проведении реконструкций и проектировании новых химических производств является разработка и поставка основного технологического оборудования. Многолетний опыт ОАО «НИИК» в области проектирования, изготовления и монтажа оборудования и аппаратуры для строящихся и действующих производств карбамида позволяет специалистам института производить комплексную оценку качества изготовления оборудования с учетом специфических требований производств карбамида с момента разработки и согласования технической документации до монтажа готового аппарата на площадке заказчика.
В процессе проведения технического сопровождения изготовления оборудования на машиностроительных предприятиях России и Европы специалисты ОАО «НИИК» периодически сталкиваются с различными сложностями и проблемами, которые возникают из-за недопонимания конструкции, отсутствия опыта и соответствующих технических возможностей производителя. К сожалению, некоторые производители не готовы своевременно признавать свои ошибки, что приводит к вынужденному ремонту уже изготовленного нового оборудования.
Примеры основных ошибок при изготовлении оборудования производств карбамида
В связи со сложными и агрессивными условиями эксплуатации к оборудованию производств карбамида предъявляются повышенные требования к качеству применяемых материалов и изготовления. Рассмотрим несколько наиболее показательных примеров допущенных ошибок при изготовлении:
Конденсатор (РФ, 2008 г). Несоответствие используемой технологии обварки труб в трубные доски, а также низкая квалификация персонала привели к многочисленным (более 50% общего количества) сквозным прожогам внутренней поверхности теплообменных труб (рис. 1).
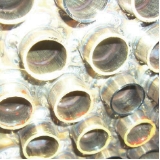
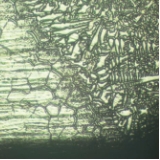
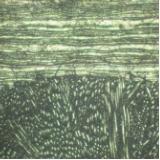
с прожогом (б) и без прожога (в)
Исправление данных дефектов привело к укорочению теплообменной части аппарата и существенному срыву сроков поставки конденсатора. Конденсатор высокого давления (Австрия, 2014 г). После выполнения швов обварки труб в трубную доску были выявлены многочисленные дефекты (20–25% труб) (рис. 2):
- оплавление торцов теплообменных труб;
- выходы наплавленного металла с образованием подрезов и рисок на внутренней поверхности труб;
- частично выполненный путем ручной дуговой наплавки ремонт оплавлений торцов;
- следы механических зачисток на внутренней поверхности и торцах теплообменных трубок, повлекшие за собой уменьшение вылета теплообменных труб по сравнению с проектным;
- некоторые теплообменные трубки были приварены вручную (manual GTAW) к трубной доске;
- несоответствие размера катета сварных швов требованиям проекта.
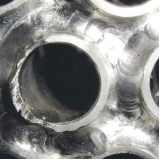
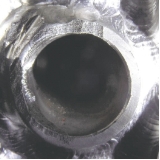
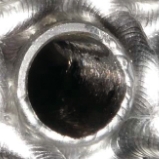
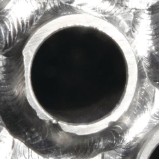
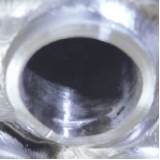
а – механическая зачистка торца, швы выполнены manual GTAW; б – механическая зачистка торца; в – наплавленный торец со следами зачистки внутренней поверхности трубы;
г – сквозное оплавление торца с выходом на внутреннюю поверхность трубы; д – выход наплавленного металла на внутреннюю поверхность трубы
Все это свидетельствует об отклонениях от согласованной рабочей документации и нарушениях технологии сварки, предъявленной представителю ОАО «НИИК» в период инспекционной поездки на начальной стадии обварки теплообменных труб, и о проведении изготовителем без согласования ремонтных работ по исправлению данных дефектов. Примененная технология ремонта и проведенные на основании ее ремонтные работы не привели к окончательному устранению обнаруженных дефектов, что обусловит пониженную коррозионную стойкость узла обварки теплообменной трубы в условиях узла синтеза производства карбамида.
В 2016 г. после ~1 года эксплуатации был выявлен пропуск рабочей среды в штуцер контроля футеровки камеры высокого давления конденсатора, что свидетельствовало о разрушении защитной антикоррозионной футеровки камеры аппарата. После вскрытия аппарата была выявлена сквозная трещина длиной 10 мм по верхней границе сплавления сварного шва приварки горизонтальной разделительной перегородки камеры к футеровке и поверхностные дефекты сварных швов (рис. 3). По всей вероятности, трещина явилась следствием недобросовестного контроля изготовителем сварных швов футеровки и межфутеровочного зазора. В результате был выполнен аварийный ремонт конденсатора.
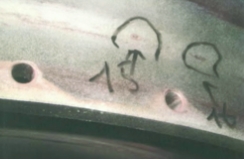
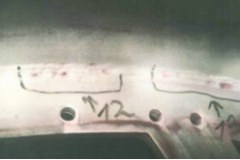
Конденсатор высокого давления (Франция, 2015–2017 гг.). На начальной стадии согласования рабочей документации выяснилось, что изготовитель не знаком с конструкцией аппарата, в связи с чем предложил конструктивные технические решения исходя из своих производственных возможностей. Наиболее спорным решением была замена футеровки камер высокого давления плакировкой, выполняемой с помощью сварки взрывом. Это решение не предусматривало наличие контрольной системы за состоянием плакировки в процессе эксплуатации, что может привести к катастрофическим разрушениям аппарата. После многочисленных обсуждений
и переговоров изготовитель согласился заменить плакированные камеры высокого давления футерованными с наличием контрольной системы, но при изготовлении футерованных камер высокого давления изготовитель настоял на применении своей «уникальной» технологии изготовления, не обладая при этом опытом производства футерованных аппаратов. Результатом применения данной «уникальной» технологии стало несоответствие наружного профиля поверхности футеровки профилю внутренней поверхности камер, зазор между футеровкой и камерами достигал 20…25 мм. Изготовитель принял решение выполнить ремонт путем наплавки внутренней поверхности камер для устранения зазоров с футеровкой (рис. 4). Из-за сложности выполнения наплавки на труднодоступную криволинейную поверхность большой площади производителю не удалось полностью устранить зазоры. Вследствие этого производитель решил теоретически обосновать наличие зазоров, выполнив прочностной расчет и получив необходимый для себя результат. Но, как известно, теоретический расчет не может достаточно точно смоделировать условия эксплуатации, можно лишь однозначно утверждать, что выполненный ремонт и допущенные отклонения с несоответствиями от проверенной временем конструкции аппарата приведут к снижению его эксплуатационной надежности.
и переговоров изготовитель согласился заменить плакированные камеры высокого давления футерованными с наличием контрольной системы, но при изготовлении футерованных камер высокого давления изготовитель настоял на применении своей «уникальной» технологии изготовления, не обладая при этом опытом производства футерованных аппаратов. Результатом применения данной «уникальной» технологии стало несоответствие наружного профиля поверхности футеровки профилю внутренней поверхности камер, зазор между футеровкой и камерами достигал 20…25 мм. Изготовитель принял решение выполнить ремонт путем наплавки внутренней поверхности камер для устранения зазоров с футеровкой (рис. 4). Из-за сложности выполнения наплавки на труднодоступную криволинейную поверхность большой площади производителю не удалось полностью устранить зазоры. Вследствие этого производитель решил теоретически обосновать наличие зазоров, выполнив прочностной расчет и получив необходимый для себя результат. Но, как известно, теоретический расчет не может достаточно точно смоделировать условия эксплуатации, можно лишь однозначно утверждать, что выполненный ремонт и допущенные отклонения с несоответствиями от проверенной временем конструкции аппарата приведут к снижению его эксплуатационной надежности.
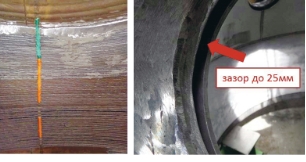
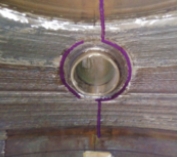
После проведенного гидроиспытания трубной части аппарата был произведен осмотр камер высокого давления, в результате чего было установлено следующее (рис. 5):
- на поверхности футеровки наблюдаются следы многочисленных зачисток, на сварных швах футеровки выполнены многочисленные ремонтные подварки;
- внутренний профиль футеровки имеет неровности: волнистости, выступы, повторяющие профиль внутренней поверхности наплавленного несущего корпуса.
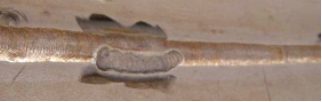
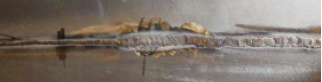
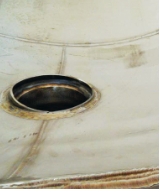
Представленные примеры демонстрируют следующее:
- заказчику необходимо очень тщательно выбирать изготовителя оборудования. Техническая оснащенность производственной площадки, компетентность и квалификация персонала, опыт в конструировании и изготовлении сложного технологического оборудования для производств карбамида напрямую влияет на качество изготавливаемого оборудования и его эксплуатационные характеристики;
- техническое сопровождение и выполнение технического надзора за изготовлением оборудования со стороны заказчика или разработчика технического проекта является необходимым условием для соблюдения всех требований технического проекта и качественного изготовления сложного и уникального оборудования производств карбамида.