Автор: Б.Л. Красный, Д.А. Серебрянский (НТЦ «Бакор»).
Опубликовано в журнале Химическая техника №12/2016
Научно-технический центр «Бакор» специализируется на выпуске плотной (специальной) и пористой проницаемой керамики, огнеупоров и плавильных тиглей, керамических фильтров и фильтрующих элементов, керамических аэраторов, фильтров для очистки газов. Одним из приоритетных направлений деятельности компании является очистка дымовых и технологических газов промышленных производств. Так, компания имеет возможность производить: аппараты центробежной очистки различных конструкций, циклофильтры, фильтры для очистки высокотемпературных (порядка 600°С) газов.
С появлением новых технологических процессов и увеличением объема производства повышение стоимости электроэнергии стимулирует создание энергосберегающих систем, основанных на применении в качестве источников теплоты и других видов энергии горячие (250…1000°С) отходящие газы промышленных агрегатов. При этом для утилизации теплоты необходима предварительная очистка горячих газов как от пылевидных частиц, так и от паров кислот и других ядовитых и вредных веществ.
Высокотемпературная фильтрация газов может быть использована в следующих технологических процессах:
- сталелитейная промышленность; выплавка алюминия, свинца, серебра и др. металлов (утилизация теплоты при 540…815°С);
- цементная промышленность (утилизация теплоты при охлаждении клинкера);
- каталитический крекинг нефтепродуктов (очистка газов регенерации при 600…800°С);
- газификация древесного угля и торфа (улавливание твердых частиц при 650…870°С);
- очистка нефти (улавливание катализаторов при 760°С);
- производство кремния (улавливание пыли кремнезема при 250…400°С);
- стекольная промышленность (печи окисления при 540°С)
- и многие другие процессы.
В настоящее время проблема фильтрации горячих производственных отходящих газов решается путем использования фильтрующих элементов с температурой до 300°С, которые устанавливаются в различные типы фильтрующих агрегатов последовательно или параллельно с циклонами, скрубберами, пылеосадительными камерами и т.п. Эффективность таких систем достигает 70–99%, однако, стоимость очистки газов достаточно высока ввиду громоздкости оборудования, необходимости охлаждения и разбавления газов до низких температур, большой занимаемой площади. Кроме того, вопрос регенерации вредных газовых включений в отходящих газах как правило, не решается, что приводит к ухудшению экологической обстановки в промышленных регионах.
В НТЦ «Бакор» освоен выпуск керамических патронных газовых фильтров на основе фильтрующих элементов, изготовленных из корунда, а также карбида кремния с наружным диаметром 60 мм и длиной до 1000 мм. Площадь фильтрации такого фильтрующего элемента составляет 0,17 м2 (рис. 1).
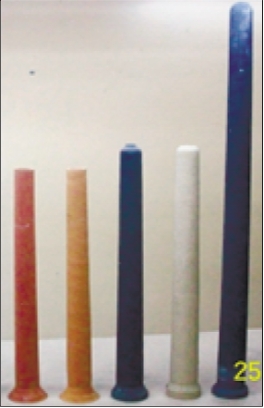
выпускаемые в НТЦ «Бакор»
Сотрудники НТЦ «Бакор» разработали аппарат очистки ФКИ-45 (рис. 2). Объем очищаемых газов единичного аппарата составляет 4 800 м3/ч.
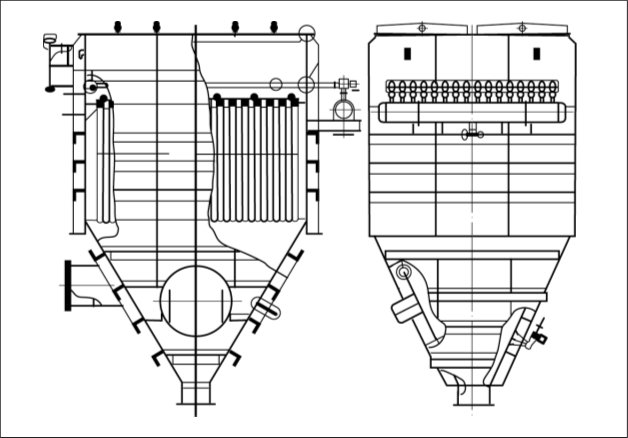
Аппараты очистки компонуются в модули необходимой производительности
Условия эксплуатации фильтра
Температура газа на входе в фильтр, °С | До 600 |
Остаточное давление газа внутри корпуса, Па | До 5 000 |
Максимальная газовая нагрузка на фильтровальную поверхность, м3/(м2·мин) | Не более 1,8 |
Массовая концентрация улавливаемых веществ в газе, г/м3: | |
на входе в фильтр | Не более 1,5 |
на выходе из фильтра (предполагаемая) | Не более 0,001 |
Очистку газов температурой до 130°С и с высокой начальной концентрацией пыли целесообразно проводить в аппарате комплексной очистки газов – циклофильтре.
Данный аппарат сочетает в себе преимущества циклона и рукавного фильтра (рис. 3).
Первая ступень – центробежная, в сепарационном канале, из которого уловленная пыль сразу отводится в отдельный бункер-пылесборник. Такая предварительная очистка позволяет уменьшить начальную запыленность газового потока, поступающего на фильтровальные рукава. Далее поток поступает на вторую ступень очистки.
Вторая ступень – центробежная, в цилиндрической камере, в которой расположены фильтровальные рукава. Далее поток поступает на третью ступень очистки.
Третья ступень – в фильтровальных рукавах, позволяющих улавливать мелкодисперсные частицы пыли.
Фильтровальные рукава оборудованы системой импульсной регенерации.
При фильтрации взрывоопасной пыли фильтр оснащается устройством для отвода взрывной волны или системой подавления взрыва. Благодаря большой устойчивости к воздействию резкого изменения давления фильтр можно устанавливать в помещениях с взрывным клапаном в соответствии с новым европейским стандартом EN14491.
Фильтр представляет собой простую модульную систему, состоящую из взаимозаменяемых частей, поэтому легко конфигурируется. Фильтр имеет два входных патрубка для входа запыленного потока и один патрубок для выхода очищенного потока. Два входных патрубка для входа запыленного потока позволяют иметь в циклофильтре четырехпозиционную систему регулирования скорости потока в первой ступени очистки (центробежной), поддерживая ее высокую эффективность при изменении расхода запыленного потока. Фильтр может применяться для отделения сухих и слабо слипающихся частиц пыли.
Циклофильтр обладает следующими преимуществами:
- производительность – 500…80 000 м3/ч;
- встроенная динамическая предочистка;
- возможность изготовления во взрывобезопасном исполнении;
- пригоден для мелкодисперсной и абразивной пыли;
- может применяться при высоких концентрациях твердых частиц;
- эффективная импульсная система регенерации;
- быстросъемные каркасы для упрощения замены фильтровальных рукавов;
- компактный дизайн.
Центробежный фильтр предназначен для очистки газовоздушных потоков от золы и пыли температурой до 350°С и концентрацией твердых частиц до 1000 г/м3.
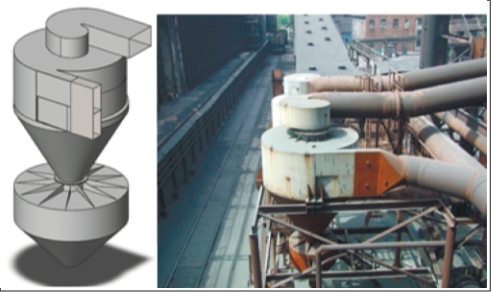
Центробежный фильтр (рис. 4) применяется в следующих случаях:
- в системах аспирации узлов пересыпок сыпучих материалов;
- в системах газоочистки сушильных барабанов, дробилок, зачистных станков и др.;
- в системах аспирации литейных дворов, цементных мельниц, холодильников клинкера;
- в золоочистке твердотопливных котлов.
Основные преимущества центробежного фильтра:
- способность достижения санитарных норм на выбросы твердых частиц в атмосферу;
- отсутствие сменных фильтрующих элементов;
- простота конструкции и надежность в эксплуатации.
Эффективность улавливания в зависимости от числа каналов в центробежном фильтре при улавливании пыли, начиная с медианного диаметра 5 мкм, приближенно можно определить по нижеприведенным данным:
Число каналов в центробежном фильтре | Коэффициент улавливания, % |
1 | 50 |
2 | 67 |
3 | 80 |
4 | 89 |
5 | 94 |
6 | 97 |
7 | 98 |
8 | 99 |
Адекватность приведенных данных многократно подтверждена промышленными испытаниями центробежных фильтров в различных отраслях промышленности.
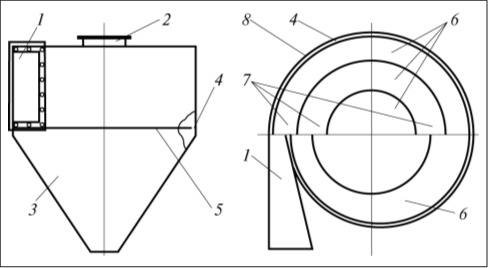
в четырехканальном исполнении:
1 – входной патрубок; 2 – выходной патрубок;
3 – конический бункер; 4 – кольцевая щель;
5 – днище головки; 6 – криволинейные каналы;
7 – рециркуляционные щели; 8 – сепарационная камера
Центробежный фильтр работает следующим образом (рис. 5): запыленный газовый поток по тангенциальному входному патрубку 1 поступает в сепарационную камеру 8. Вследствие движения по криволинейной траектории твердые частицы концентрируются на периферии каждого из каналов 6 и выводятся из них через зазоры 7 в предыдущий по ходу движения потока каналы. Из первого и второго по ходу потока каналов 6 пыль, вместе с частью газа поступает через кольцевую щель 4 в цилиндрический бункер-пылесборник 3, где большая масса частиц оседает, а продолжающие витать наиболее легкие (мелкие) фракции возвращаются через щели 7 в зону активной сепарации (каналы) и снова сепарируются. В результате организации внутренних (циркулирующих) потоков в системе каналов образуется динамический газопылевой слой, который и является фильтром для вновь поступающих на очистку газа частиц.
Интенсивный абразивный износ циклонов на многих предприятиях является технической проблемой, возникающей при их эксплуатации. Примером может быть очистка циркуляционных потоков в установках сухого тушения кокса (УСТК). Циркулирующий в УСТК охлаждающий инертный газ представляет собой продукт взаимодействия находящегося в газоходах УСТК воздуха с раскаленным коксом.
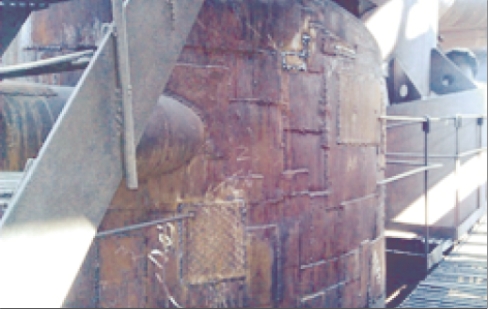
Время абразивного износа стенки циклонных пылеуловителей можно приблизительно оценить по зависимости
где τ – время износа стенки пылеуловителя, с; g – ускорение силы тяжести, м/с2; h – глубина износа, м; С – запыленность газового потока, кг/м3; θг – скорость газового потока, м/с; Ка – коэффициент абразивности, м2/кг; Е – вероятность удара частиц пыли о стенку, доли.
Как видно, время износа зависит от скорости газопылевого потока в третьей степени, концентрации частиц и вероятности удара частиц о стенку. Снижения абразивного износа с увеличением эффективности улавливания твердых частиц в циклонных пылеуловителях можно достичь благодаря организации отвода концентрированной части потока в области входного патрубка в отдельный изолированный бункер.
Аппарат, в котором реализован данный принцип, – циклонный пылеуловитель (см. рис. 3).
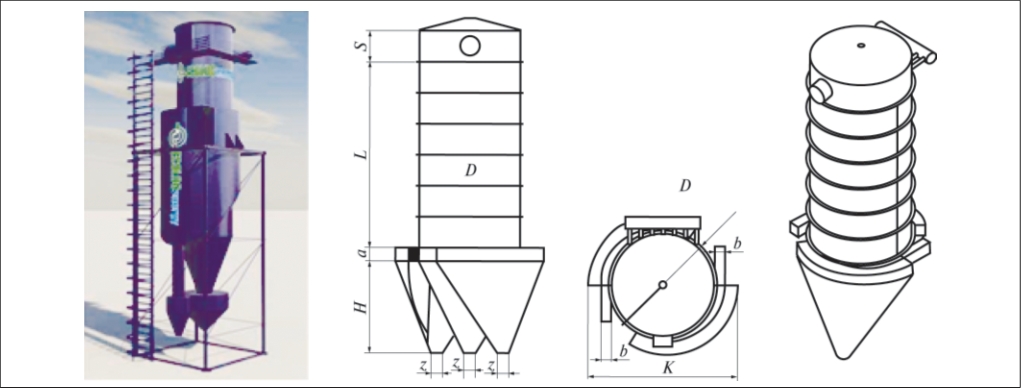
Циклонный пылеуловитель (рис. 7) состоит из входного патрубка 1, внутреннего корпуса 2 и внешнего корпуса 4, жалюзийного элемента 3, внутреннего бункера-накопителя 6 с шлюзовым затвором для выгрузки уловленной пыли или золы (на рисунке не показан), наружного бункера-накопителя 5 с шлюзовым затвором для выгрузки уловленной пыли или золы (на рисунке не показан), выходного патрубка 7.
Пылеуловитель работает следующим образом: запыленный газовый поток попадает по входному патрубку 1 во внутренний корпус аппарата 2. За счет центробежных сил тяжелые фракции пыли или золы концентрируются у стенки внутреннего корпуса в первой трети и через щелевые окна жалюзийного элемента 3, высота которого равна высоте входного патрубка 1, отводятся в кольцевое пространство, образующееся между внутренним 2 и внешним 4 корпусами аппарата. Таким образом, крупнодисперсной фракция под действием силы тяжести оседает во внешнем бункере-накопителе 5. Более мелкая фракция пыли или золы сепарируется во внутреннем корпусе циклонного пылеуловителя 2 и оседает во внутреннем бункере-накопителе 6, герметично изолированного от бункера-накопителя 5. Очищенный газовый поток отводится через выходной патрубок 7. Внешний корпус 4 циклонного пылеуловителя по конструкции может быть применим при модернизации любого типа циклонного пылеуловителя с изолированным отводом уловленной пыли через шлюзовой затвор.
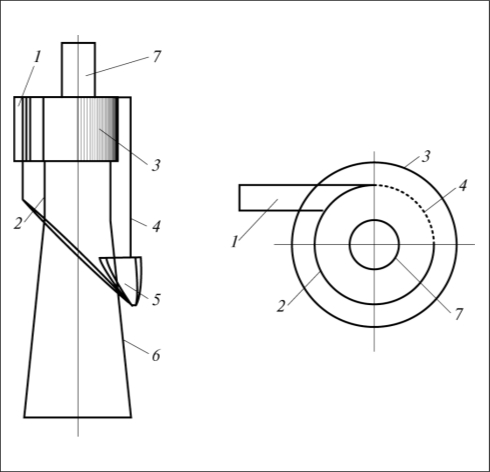
Модернизация любого циклонного аппарата позволяет в 2–4 раза уменьшить выбросы твердых частиц пыли с циклонного пылеуловителя без увеличения энергозатрат на очистку и позволит снизить абразивный износ корпуса аппарата.
Таким образом, ЗАО «НТЦ Бакор» при решении задач по очистке газов предлагает комплексный подход, в который входят предварительное обследование источника твердых частиц, разработка технического решения, изготовление и поставка очистного оборудования, пусконаладка, сервисное обслуживание.