Автор: А.П. Завьялов, В.А. Лукьянов (ОАО «Оргэнергогаз», РГУ НиГ им. И.М. Губкина).
Опубликовано в журнале Химическая техника №2/2014
В настоящее время обеспечение безопасной эксплуатации сосудов и аппаратов, работающих под давлением, основано на проведении технической диагностики указанных конструкций с применением современных методов неразрушающего контроля и средств измерений. При этом многие современные средства диагностики являются достаточно дорогостоящими, затраты на диагностическое обслуживание составляют на современных опасных производственных объектах до 15% общей сметы технического обслуживания и ремонта (ТОиР).
В условиях выработки основного назначенного ресурса оборудования, в массовом количестве вводившегося в эксплуатацию в 1970–1990 гг. прошлого века, значительную часть диагностических работ на эксплуатируемых опасных производственных объектах составляет экспертиза промышленной безопасности сосудов и аппаратов с целью продления срока безопасной эксплуатации.
В общем случае указанные работы включают [1–3]:
- анализ проектной и эксплуатационной документации, корректировку стандартной программы инструментального диагностического обследования;
- комплекс работ по неразрушающему контролю с целью определения технического состояния металлоконструкций, включающий ультразвуковую толщинометрию и дефектоскопию, капиллярную дефектоскопию, визуально-измерительный контроль, твердометрию металла, металлографические исследования и иные методы контроля в зависимости от специфики отрасли;
- гидравлические испытания сосуда с проведением акустико-эмиссионного контроля с целью диагностирования развивающихся дефектов;
- определение остаточного ресурса и оформление заключения экспертизы промышленной безопасности с последующей регистрацией его в органах Ростехнадзора.
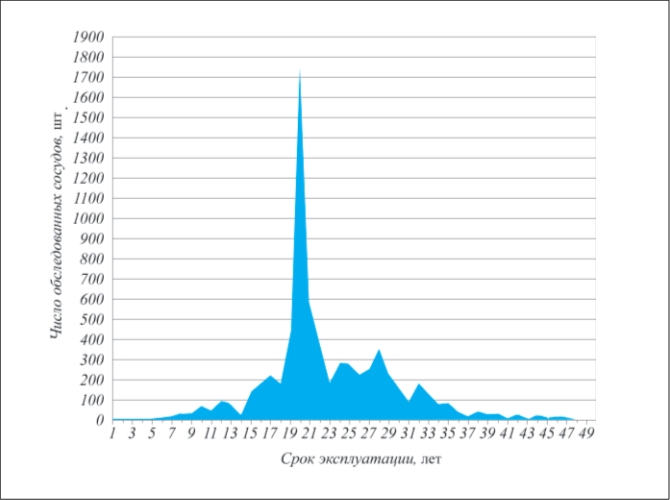
ОАО «Газпром», обследованных ОАО «Оргэнергогаз» в 1999–2013 гг.,
в зависимости от срока эксплуатации
К настоящему моменту ОАО «Оргэнергогаз» накоплен значительный опыт проведения указанных работ (рис. 1), поскольку значительная часть эксплуатируемых сосудов, работающих под давлением, выработала основной назначенный ресурс, а некоторые – и первый, и второй дополнительные назначенные ресурсы.
Таким образом, на некоторых «лидерных» сосудах и аппаратах работы по продлению ресурса проведены 2–3 раза.
На рис. 1 заметно относительно большое число обследованных сосудов со сроком эксплуатации 24; 28 и 32 года, что соответствует периоду исчерпания первого и второго дополнительных сроков эксплуатации.
Анализ результатов работ на указанных сосудах показывает достаточно высокую повторяемость результатов диагностических обследований при втором, третьем и т.д. проведении работ по определению технического состояния (при обеспечении должного качества обследований и сопоставимости результатов). Так, практически не изменяются результаты измерений твердости металла, а результаты измерений толщины стенки сосудов и аппаратов, работающих в малоагрессивных средах, изменяются не более, чем на 0,1…0,2 мм/год, что по сравнению с принятыми припусками на коррозию можно считать незначительными; практически не прослеживается тенденции к развитию небольших дефектов сварных швов, возникших на стадии изготовления и монтажа оборудования.
Кроме того, большинство выявляемых дефектов (рис. 2) возникают на стадии изготовления и монтажа оборудования, а значит, должны быть выявлены при обследовании, проводимом по окончании основного назначенного срока эксплуатации.
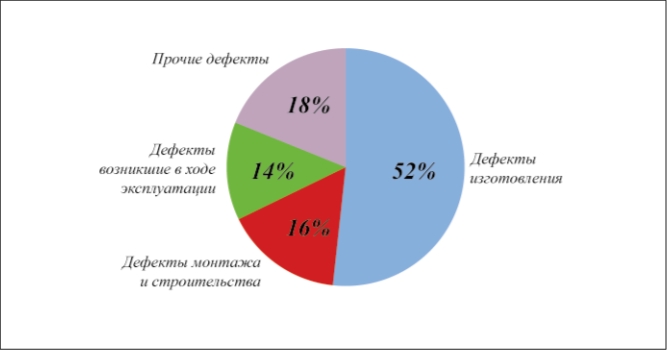
обслуживания сосудов, работающих под давлением
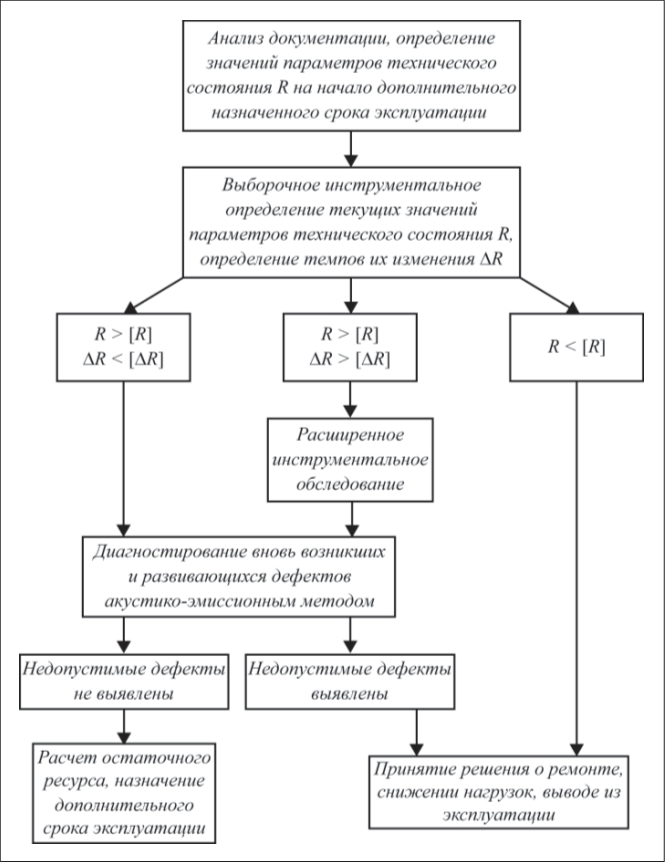
эксплуатации сосудов и аппаратов, работающих под давлением
Это обстоятельство создает возможности для оптимизации программы диагностического обследования при повторном продлении срока безопасной эксплуатации оборудования, поскольку основной задачей становится выявление дефектов, развившихся в течение дополнительного срока эксплуатации (20…24 или 20…28 лет), для чего вполне пригоден метод акустической эмиссии.
При определении технического состояния оборудования в этом случае предлагается в значительной степени использовать результаты диагностирования, полученные при первичном продлении срока безопасной эксплуатации, оптимизировав объемы инструментального обследования.
Таким образом, задачи, решаемые при проведении работ по неразрушающему контролю при повторном техническом диагностировании, сведутся к следующим:
- выборочной проверке результатов первичного диагностирования и определению скорости изменения параметров, характеризующих техническое состояние конструкции;
- диагностированию возможного возникновения и развития эксплуатационных дефектов методом акустической эмиссии [4].
Предлагаемая схема принятия решения о продлении срока безопасной эксплуатации сосуда или аппарата представлена на рис. 3.
Фактически речь идет о переходе от системы разовых, практически не связанных друг с другом мероприятий по продлению срока безопасной эксплуатации к полноценной ресурсосберегающей системе управления жизненным циклом оборудования.
Экономическая целесообразность
Расчеты показывают, что предлагаемая схема повторного продления срока безопасной эксплуатации сосудов и аппаратов, работающих под давлением, позволит значительно снизить затраты на проведение экспертизы промышленной безопасности.
Анализ сметной документации на проведение работ по продлению ресурса показывает, что их стоимость складывается из трех частей:
- стоимости работ по анализу проектной и исполнительной документации, расчету остаточного срока эксплуатации, анализу и оформлению результатов, так назваемых «камеральных» работ – 30–35% общей стоимости;
- стоимости работ по неразрушающему контролю – 40–45% общей стоимости;
- стоимости работ по проведению гидравлических испытаний и акустико-эмиссионного контроля – 20–30% общей стоимости.
При выполнении выборочного инструментального обследования вместо сплошного объем работ по неразрушающему контролю может быть снижен в 3–4 раза, что приведет к уменьшению общей стоимости экспертизы промышленной безопасности на 25–30%.
С учетом того, что часть эксплуатируемого оборудования будет подвергаться расширенному инструментальному обследованию, и возможного возникновения дополнительных затрат на организацию управления жизненным циклом оборудования (о которых будет сказано далее), можно предположить, что общее снижение затрат на обследование парка оборудования может составить 20–25%. Для крупных производственных комплексов это означает десятки миллионов рублей.
Особенности внедрения
Внедрение указанной методологии продления срока безопасной эксплуатации оборудования потребует решения ряда прикладных инженерных задач, которые не были актуальными при использовании современной методологии. 1. Необходима корректировка нормативно-технической документации, определяющей порядок продления срока безопасной эксплуатации сосудов и аппаратов, работающих под давлением. Применяемая в настоящее время нормативная документация устанавливает, как правило, только предельные значения параметров, определяющих техническое состояние оборудования, и никак не регламентирует скорость изменения этих параметров при нормальной эксплуатации оборудования. Указанное обстоятельство является также причиной того, что в соответствии с существующими нормативными документами срок, на который продлевается эксплуатация, как правило, не рассчитывается, а назначается исходя из субъективных критериев (4, 8 лет и т.д.).
При переходе на систему управления жизненным циклом оборудования необходимо нормативно установить предельные значения скорости изменения параметров технического состояния, превышение которых будет служить основанием для проведения расширенного инструментального обследования данной единицы оборудования.
Следствием корректировки нормативной документации станет переход к объективному инженерному расчету величины назначаемого дополнительного ресурса, что на практике в большинстве случаев будет означать его увеличение (это позволит получить дополнительный экономический эффект).
Указанная корректировка нормативной документации потребует выполнения комплекса научно-исследовательских работ по оценке надежности и эксплуатационных характеристик применяемых в промышленности серийных образцов оборудования. 2. Внедрение указанной методологии потребует принципиально нового подхода к качеству диагностических работ. При традиционном подходе заказчика – эксплуатирующую организацию интересует в основном конечный результат работ – зарегистрированное в Ростехнадзоре заключение экспертизы промышленной безопасности. Диагностическое обследование имеет в целом вспомогательную роль, его результаты используются, в основном, экспертом при формировании окончательных выводов.
При внедрении предлагаемой методологии предъявляются повышенные требования к качеству диагностических работ, поскольку для ее реализации необходимо обеспечить сравнимость результатов с предыдущими и последующими обследованиями [5].
Это означает следующее:
- единство методологической базы предыдущих и последующих измерений;
- применение наиболее современного, точного, а значит, и дорогостоящего оборудования неразрушающего контроля и диагностики с целью обеспечить минимально возможные погрешности измерений;
- привлечение к работам высококвалифицированных специалистов, неукоснительное соблюдение технологии диагностических работ, с целью минимизации влияния «человеческого» фактора и случайных ошибок.
Перечисленные требования позволяют предположить, что внедрение технологии управления жизненным циклом будет под силу только крупным инжиниринговым фирмам, имеющим значительный опыт выполнения диагностических работ, располагающим высококвалифицированными специалистами и современным оборудованием, а также научно-техническим потенциалом. 3. При внедрении предлагаемой методологии актуальным становится оказание комплекса инжиниринговых услуг по управлению жизненным циклом оборудования, включающих следующие:
- конкретизацию методики диагностического обследования применительно к конкретным типам оборудования, эксплуатируемым на опасном производственном объекте;
- выполнение прикладных исследований надежности элементов конкретных типов оборудования, обоснование предельных значений параметров технического состояния;
- координацию практических работ по диагностике и экспертизе промышленной безопасности;
- разработку и ведение базы данных технического состояния парка оборудования;
- статистическую и аналитическую обработку результатов диагностики;
- формирование единой методологической базы диагностических работ;
- подготовку и аттестацию кадров.
Таким образом, на основании изложенного можно сделать следующие выводы.
Накопленный опыт свидетельствует о целесообразности перехода от системы разовых, практически не связанных друг с другом, мероприятий по продлению срока безопасной эксплуатации к системе управления жизненным циклом оборудования с целью оптимизации и общего снижения затрат на экспертизу промышленной безопасности.
Переход на предлагаемую систему управления жизненным циклом может привести к общему снижению затрат на проведение экспертизы промышленной безопасности парка оборудования на 20–25%.
Переход к системе управления жизненным циклом оборудования потребует проведения комплекса научно-исследовательских работ по исследованию надежности оборудования, корректировки нормативной документации, формированию новых требований к проведению практических диагностических работ и оказанию инжиниринговых услуг.
Список литературы
- ПБ 03-576–03. Правила устройства и безопасной эксплуатации сосудов, работающих под давлением. М.: ПИО ОБТ, 2003.
- РД 03-421–01. Методические указания по проведению диагностирования технического состояния и определения срока службы сосудов и аппаратов. Утв. Приказом Госгортехнадзора России от 06 сентября 2001 г., №39.
- СТО Газпром 2-2.3-491–2010. Техническое диагностирование сосудов, работающих под давлением на объектах ОАО «Газпром. М.: ОАО «Газпром», 2010. 161 с.
- Нагинаев К.Е., Лапшин М.Б., Нагинаев Е.Н. и др. Новый подход к экспертизе промышленной безопасности технологического оборудования//Диагностика оборудования и трубопроводов компрессорных станций: Мат-лы XXVIII тематического семинара (г. Геленджик, 12–16 октября 2009 г.): В 2 т. Т.2. М.: ООО «Газпром экспо», 2010. С. 37–46.
- Кудрявцев А.Ю. Особенности организации и проведения диагностических работ технологического оборудования, проектируемого ДОАО ЦКБН ОАО «Газпром»//Диагностика оборудования и трубопроводов компрессорных станций. Мат-лы XXVIII тематического семинара (г. Геленджик, 12–16 октября 2009 г.): В 2 т. Т.2. М.: ООО «Газпром экспо», 2010. С. 46–53.