Автор: В.А. Захаров (АО «ВНИИНефтемаш»), О.Ю. Елагина (РГУ нефти и газа им. И.М. Губкина)
Опубликовано в журнале Химическая техника №6/2017
Для теплообменных аппаратов, работающих при высоких давлениях и температурах на взрывопожароопасных производствах, предъявляются особые требования к прочности и плотности соединений труб с трубной решеткой. Приварка труб применяется в сочетании с развальцовкой. Трубы развальцовываются после их приварки, в результате чего исключается возможность попадания смазочного масла с вальцовки на подлежащие сварке поверхности.
Таким образом, конструктивной особенностью пучка секции аппарата воздушного охлаждения является наличие потенциально опасных узлов (ПОУ) конструкции – наиболее нагруженных мест (узлы труба – трубная решетка и особенно узлы нижнего ряда в зонах варки штуцеров). Сочетание различных ПОУ (концентраторов напряжений с потенциально коррозионными зонами) с локальными дефектами поверхности и сварных соединений значительно увеличивают вероятность образования и ускоренного развития эксплуатационных повреждений.
В 2017 г. специалистами АО «ВНИИНефтемаш» и РГУ нефти и газа им. И.М. Губкина проведено диагностическое обследование разгерметизировавшегося пучка секции аппарата воздушного охлаждения. Пропуск обнаружился в узлах труба – трубная решетка при проведении пусковых операций. Наружный диаметр трубок – 25,4 мм, материал – SA-334 Gr 6 ASME. По эксплуатационным условиям и составу среды данный аппарат относится к аппаратам 1 категории по ТР ТС 032/2013 и к аппаратам 1 группы сосудов по ГОСТ Р 52630–2012. Секция прошла гидроиспытания на заводе-изготовителе и после монтажа на месте эксплуатации.
Для исследования причин разгерметизации заказчиком были предоставлены фрагменты вырезанных трубок. Осмотр наружной поверхности трубки на участке крепления в трубной доске показал наличие смолистых отложений и загрязнений на наружной поверхности трубок. Их наличие указывало на тот факт, что подготовка и зачистка наружной поверхности труб под приварку в зоне развальцовки не проводилась, что является нарушением требований п.10 ГОСТ Р 55601–2013. Осмотр торцовой поверхности (корневая часть шва, рис.1) выявил наличие пор на поверхности реза и линейных дефектов, ориентированных по диагональным линиям. Внутренняя поверхность трубок характеризовалась развитием общей неравномерной коррозии в виде коррозионных пятен.
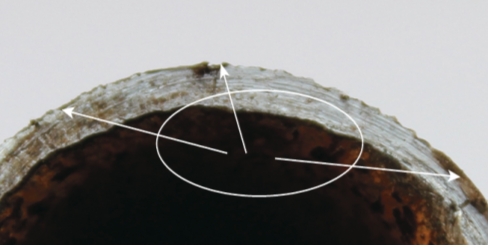
Химический анализ металла трубок, выполненный оптико-эмиссионным методом на спектрометре Foundry Master PRO показал, что металл более близок к стали 17Г1С-У, характеризуется пониженным содержанием углерода и относится к высококачественным рафинированным сталям. Представленные в документации присадочные материалы относятся к низкоуглеродистым сталям с Si–Mn системой легирования и низким содержанием серы (до 0,01%) и фосфора (до 0,015%).
При исследовании торцовой поверхности фрагмента трубки в зоне разрушения выявлена сквозная трещина, пересекающая всю толщину стенки трубы под углом ~75–80° к наружной поверхности. Трещина характеризуется ступенчатой траекторией и малым ветвлением, характерным для формирования трещин в охрупченном металле. Развитие трещины направлено от наружной поверхности к внутренней, на что указывает уменьшение ширины раскрытия трещины по мере продвижения к внутренней части стенки трубки (рис. 2).
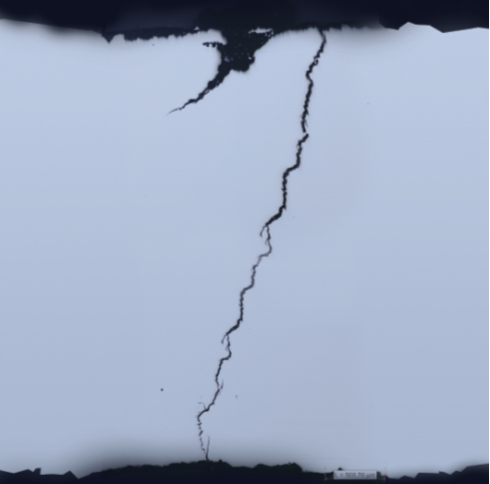
При травлении шлифа выявлена существенная разница в реакции металла в зонах, прилегающих к трещине, на реактив. Это указывает на изменение химического состава стали в приповерхностном слое трещины в процессе ее роста (рис. 3).
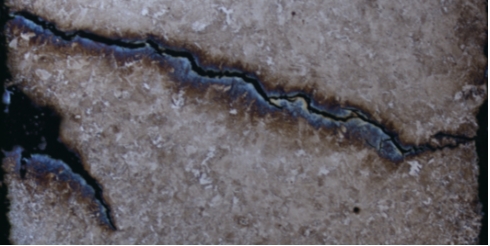
Как правило, образование горячих трещин сопровождается интенсивным окислением вновь сформированной поверхности в области высоких температур и, как следствие, выгоранием углерода и легирующих элементов. При повторном окислении (травлении) эти участки протравливаются с другой интенсивностью. Оценка изменения степени травления металла показывает, что часть длины трещины, примыкающей к наружной поверхности, характеризуется большей реакцией на реактив, а на участке выхода трещины на внутреннюю поверхность трубы степень протравленности снижается. Видимо, на этом участке изменения химического состава металла в зоне роста трещины не происходило.
Оценка химического состава смолистых отложений, обнаруженных на наружной поверхности трубки в зоне крепления и приварки к трубной доске, была выполнена методом рентгено-флуоресцентного анализа на спектрометре ALR Perform X 4200. Параллельно, для определения базовых интенсивностей спектральных линий различных элементов исследовалась наружная поверхность трубы на участке снятого оребрения, предварительно подвергнутая обезжириванию. Сопоставление интенсивности спектральных линий двух фрагментов выявило резкое возрастание концентрации серы на участке смолистых отложений (рис. 4). Содержание серы в отложениях на поверхности посадки трубки в трубную доску более чем в 130 раз превышало ее концентрацию на очищенной поверхности. Попадание серы в зону сварки могло привести к повышению склонности металла к образованию горячих трещин и формированию сульфидных неметаллических включений, способствующих последующему разрушению.
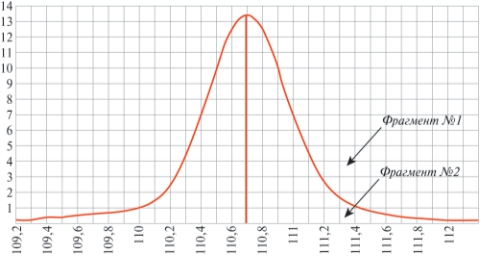
Исследование металла торца трубки на наличие неметаллических включений выявило их значительное количество по сечению стенки. Значительная часть этих включений представляет собой скопление частиц темного цвета округлой формы, неравномерно выделившихся по сечению стенки трубы на участке сварного шва. Кроме того, в металле зафиксированы включения серого цвета неправильной формы, расположенные по границам зерен (рис. 5).
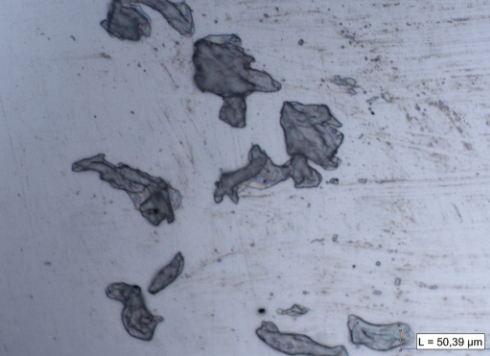
сварного шва трубы. ´500
В низкоуглеродистой стали сферидизация структуры неметаллических включений, как правило, происходит в результате связывания серы в сульфиды марганца (например, МnS). Металл трубки и рекомендованные для применения сварочные материалы характеризуются высокой степенью чистоты по сере и значительным содержанием марганца. Между тем, при отсутствии внешних факторов выделения в виде сульфидов в металле сварного шва должны были отсутствовать. Их формирование, зафиксированное при металлографических исследованиях, показывает, что в процессе сварки сера попала в сварной шов в результате наличия внешних загрязнителей и при плавлении из-за наличия марганца сформировала дезориентированные сульфиды.
В металле сварного шва также была выявлена значительная степень пористости. Размеры пор в среднем составляют 1…20 мкм, однако размер отдельных пор достигает 70…80 мкм.
Для оценки механических свойств сварного соединения были выполнены замеры твердости в различных участках (см. таблицу).
Результаты измерения твердости в сечении сварного шва, ориентированном вдоль оси трубки
Зона сварного соединения
|
Номер замера | Расстояние от торца образца, мм |
Твердость, HV5 |
Сварной шов | 1 |
0,75
|
298 |
2 | 1,25 | 284 | |
3 | 1,75 | 257 | |
4 | 2,25 | 224 | |
ЗТВ | 5 | 2,75 | 181 |
6 | 3,25 | 158 | |
7 | 3,75 | 154 | |
Основной металл | 8 | 4,25 | 145 |
9 | 5,25 | 138 | |
10 | 6,25 | 141 | |
11 | 7,25 | 141 | |
12 | 8,25 | 134 |
Как видно из полученных данных, металл сварного шва характеризуется повышенным уровнем твердости. По мере продвижения к основному металлу значения твердости снижаются практически вдвое.
Сварной шов характеризуется формированием преимущественно мартенситной структуры, неоднородной по содержанию легирующих элементов. На отдельных участках присутствуют фрагменты бейнитной структуры и зерна доэвтектоидного феррита. Наличие мартенсита в структуре сварного шва и на линии сплавления, а также повышенный уровень твердости металла этих участков сварного соединения способствовали формированию трещин и разрушению.
Таким образом, разгерметизация теплообменной секции произошла в потенциально опасной зоне трубного пучка – труба – трубная решетка – из-за некачественно выполненного сварного соединения и отсутствия развальцовки. На наружной поверхности металла трубки, на участке ее крепления в трубной доске выявлено значительное содержание серы. При сварке сера попала в сварное соединение с образованием сульфидов и пор. Анализ химического состава металла и присадочных материалов показал, что они отличаются высокой степенью чистоты по сере и не могли стать источником загрязнений. Кроме того, металл сварного шва и линии сплавления характеризуется мартенситной структурой и повышенной твердостью, в 2 раза превышающей твердость основного металла. В комплексе эти факторы привели к образованию трещин, выявленных при исследовании. Можно предположить, что зарождение трещины произошло сразу после сварки, на что указывает изменение травимости металла на участке трещины, выходящем на наружную поверхность трубки. Как правило, появление такого рода дефектов связано с нарушениями технологии изготовления на этапах выполнения контрольных и сварочных операций. При пусковых операциях приложение эксплуатационных нагрузок провело к развитию трещины по направлению от наружной поверхности к внутренней.
Следует также отметить следующее:
- в соответствии с требованиями ГОСТ ISO13706–2011 для аппаратов, эксплуатирующихся на взрывопожароопасных производствах, приварку труб в трубном пучке необходимо сочетать с развальцовкой в отверстиях с двумя канавками для повышенной прочности и плотности соединений труб с трубной решеткой;
- в соответствии с требованиями ФНП «Общие правила взрывобезопасности для взрывопожароопасных химических, нефтехимических и нефтеперерабатывающих производств» при закупках сложного и дорогостоящего оборудования необходимо осуществлять квалифицированный входной и операционный контроль с применением наиболее эффективных средств технической диагностики, качество сварных соединений таких труднодоступных узлов, как труба – трубная решетка рекомендуется проверять вихретоковым контролем динамическим преобразователем роторного типа [3].
Список литературы:
1. ГОСТ Р 55601–2013. Аппараты теплообменные и аппараты воздушного охлаждения. Крепление труб в трубных решетках. Общие технические требования.
2. ГОСТ ISO 13706–2011. Аппараты с воздушным охлаждением. Общие технические требования.
3. Захаров В.А., Борисенко В.В. Диагностика изношенности оборудования с использованием магнитных и акустических характеристик металла//Химическая техника. 2016. №12. С.25–27.