Авторы: Р.М. Ахмадуллин, П.М. Трофимов, П.П. Трофимов, Л.И. Мусин, А.Г. Ахмадуллина (ООО НТЦ «Ахмадуллины», Казань);
Г.С. Яицких, К.П. Кулаков, А.В. Краснов, В.Г. Яицких (АО «Инженерно-промышленная нефтехимическая компания», Москва)
Опубликовано на портале «Химическая техника», май 2022
На сегодняшний день одной из основных задач нефтеперерабатывающей отрасли является увеличение глубины переработки нефти, которую традиционно связывают с типичными технологиями вторичных деструктивных процессов переработки нефтяных остатков – мазутов и гудронов. Среди них: глубокая вакуумная перегонка, термокрекинг, замедленное коксование, гидрокрекинг, каталитический крекинг и др. [1–2].
Разумеется, технологии вторичных деструктивных процессов, актуальны и для переработки высоковязких трудноизвлекаемых нефтей по причине повышенной концентрации в них асфальто-смолистых веществ. Поскольку в объеме добычи жидких углеводородов растет доля высоковязких трудноизвлекаемых нефтей, решение вопросов их транспортировки и переработки становится актуальнее [3].
У российских НПЗ (особенно малых и средних по мощности) возникают серьезные опасения за рентабельность своих предприятий в силу ограниченной востребованности в мазуте на внутреннем рынке, а экспорт в начале 2022 г. резко сократился. Таким образом, у нефтепереработчиков возникла серьезная проблема: где найти, как определить эффективность и быстро построить простые технологические процессы, которые позволили бы за короткий срок максимально сократить или исключить мазут из товарной продукции завода, а вместо него производить нефтепродукты с высокой добавленной стоимостью.
Капиталовложения в строительство каждой новой «классической» установки глубокой переработки мазута достигают сотен миллионов евро. Положительная экономика на таких установках достигается при единичной мощности не менее 2…3 млн. т переработки тяжёлых фракций в год.
В то же время в современной России продолжают работать сотни небольших НПЗ, перерабатывающие от 0,1 до 2,0 млн. т нефти в год. Как правило, эти НПЗ расположены в удалённых регионах страны, куда доставка нефтепродуктов обходится дороже их производства на местных предприятиях. Добываемая на региональных месторождениях нефть является дешёвым сырьём для миниНПЗ, которые нередко совмещают с установкой комплексной подготовки нефти (УКПН) к дальнему транспорту в рамках обустройства месторождения.
Заводы малой нефтепереработки включают установки первичной перегонки нефти, иногда (но не всегда) установки гидроочистки, изомеризации и риформинга бензиновых фракций, что позволяет получать из нефти в среднем суммарно до 50–55% бензина и дизельного топлива. Оставшиеся около 45–50% мазута – это дешёвый товар, который реализуется с трудом и не приносит прибыли. Собственники небольших заводов пытаются найти возможности повышения эффективности действующего производства (базовый вариант) за счёт внедрения каких-либо нетрадиционных технических решений, направленных в первую очередь на углубление переработки мазута с целью получения дополнительного количества более дорогих бензиновых и дизельных фракций.
Классические способы вторичной переработки тяжелых нефтяных остатков (термический крекинг, деасфальтизация и коксование) будут обладать ограниченным пределом возможного максимального отбора светлых дистиллятных фракций, т.е. углубления переработки нефти, в силу специфических свойств тяжелых остатков, таких как повышенное содержание смол и асфальтенов, а также высокие показатели коксуемости.
Способы вторичной переработки тяжелых нефтяных остатков вакуумная перегонки и деасфальтизация не дают конечной товарной продукции. Более того, для увеличения глубины переработки и тяжелый вакуумный газойль, и деасфальтизат требуют дальнейшей капиталоемкой каталитической переработки. Гудрон и асфальтит необходимо направлять либо на висбрекинг [4], либо на окисление до битумов [5], либо на замедленное коксование [6]. Применение перечисленных процессов в виде длинных технологических цепочек в схемах малых и средних НПЗ экономически нецелесообразно, так как стоимость такого завода по сравнению с базовым вариантом увеличится в 10–30 раз.
В настоящее время в основном применяется такой способ, как замедленное коксование гудронов, обеспечивающий максимальный выход дистиллятных фракций (до 60–80% от сырья). При этом дистиллятные фракции коксования тяжелых остатков соответствуют характеристикам средних и тяжелых газойлевых фракций. Средние дистилляты после гидроочистки направляют в дизтопливо, а тяжелые газойли направляют на каталитическую переработку. Но применительно к высокосернистым нефтям процесс коксования становится экологически неприемлемым. Производимый в огромных количествах высокосернистый кокс как топливный продукт не находит квалифицированного применения. Подвергать обессериванию такой кокс нерентабельно. Сам процесс замедленного коксования весьма энергоемок, экологически грязен и на малых мощностях нерентабелен. Необходим поиск других технологий.
К процессам термодеструктивного крекирования относятся висбрекинг (лёгкий термический крекинг) [7] и термический крекинг при жёстком технологическом режиме, а также их разновидности. Процесс жёсткого термического крекинга не нашел широкого распространения в нефтепереработке, а применение современных гидро- и каталитических процессов в некоторых случаях сдерживается из-за крайней дороговизны. Тем не менее, висбрекинг распространён в настоящее время значительно шире [8].
Обычный термический крекинг протекает с разрывом связей С–С и образованием свободных радикалов или карбанионов (т.е. разложение и превращения химических соединений при нагревании). Расщепление соединений сопровождается значительным поглощением тепла и традиционно проводится в обогреваемом реакторе либо змеевике, на внутренних стенках которых образуются коксовые отложения вследствие более высокой температуры стенки и более низкой скорости потока вдоль нее, чем в основном объеме, что способствует протеканию в пристенном слое вторичных процессов (полимеризация или поликонденсация). Кроме того, перегрев приводит не только к разрыву связей С–С в середине молекулы, как наиболее ослабленной, но и на ее окраинах, т.е. образование неселективной газовой фазы.
Целесообразным видится обеспечение пребывания тяжелой части сырья в реакционной зоне в мягких условиях, в результате чего происходит легкий крекинг исходных тяжелых углеводородов с образованием целевых среднедистиллятных продуктов и пониженное коксообразование. Таким образом, на достижение этих целей были направлены усовершенствования процессов крекинга: висбрекинг, выносная реакционная камера (сокинг-камера), гидровисбрекинг, термический гидрокрекинг («Дина-крекинг»), каткрекинг, гидрокаткрекинг и добавки-инициаторы [9–10].
Предлагаемая технология термоокислительного крекинга (ТОК) позволяет исключить протекание вторичных процессов и образование коксовых отложений за счет компенсации энергетических затрат на реакции крекинга теплом, выделяющимся при окислении части сырья кислородом воздуха при его подаче непосредственно в реактор при температуре проведения процесса крекинга, в отличие от обычного окислительного крекинга, где гидропероксиды, образующиеся окислением части исходного непрогретого сырья, при нагреве начнут распадаться при температурах существенно ниже температуры крекинга, теряя инициирующее действие. ТОК процесс надежнее в эксплуатации, так как исключается закоксовывание оборудования.
Преимущества технологии ТОК:
- возможность получения из тяжелых нефтяных остатков (ТНО) более лёгких углеводородных фракций;
- сравнительно низкие энергозатраты на крекинг; в процессе ТОК поддерживается баланс между экзотермическими реакциями окисления и эндотермическими реакциями непосредственно самого крекинга;
- высокая технико-экономическая эффективность процесса и малые капиталозатраты на производство, обусловленные простотой процесса, отсутствием избыточного давления и относительно невысокой температурой крекинга;
- отсутствует необходимость подготовки (предварительное удаление серы) сырья крекинга с целью повышения выхода светлых фракций и снижения коксообразования;
- многократное снижение содержания серы в продуктах крекинга, что обусловлено окислением серусодержащих органических соединений до сульфонов и сульфооксидов с последующим их термическим распадом на диоксид серы и углеводороды.
Таким образом, незаменимым процессом для мини НПЗ может стать термоокислительный крекинг. Принципиальная технологическая схема ТОК приведена на рис. 1.
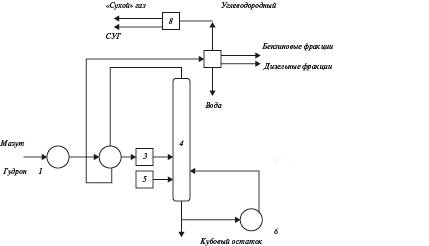
1 – сырьевой насос; 2 – рекуперативные теплообменники; 3 – печь; 4 – реактор; 5 – блок получения кислорода; 6 – насос; 7 – узел ректификации продуктов крекинга; 8 – блок получения СУГ
Сырьё (мазут или гудрон) насосом 1 прокачивается последовательно через
рекуперативный теплообменник 2 и печь 3, где нагревается до температуры 400…500оС, и подаётся в реактор 4. Ниже ввода сырья в реактор
подаётся кислород. Здесь происходят реакции конверсии тяжёлых углеводородов в более лёгкие и одновременно реакции окисления незначительной части углеводородов с выделением тепла. Печь 3 обладает сравнительно небольшой мощностью и необходима для пуска установки. Основной объём тепловой энергии, необходимой для процесса ТОК, выделяется при частичном окислении углеводородного сырья в реакторе 4.
Продукты ТОК выводятся из верхней части реактора 4, отдают часть тепла в рекуперативном теплообменнике 2 и направляются в узел ректификации 7, где разделяются на товарные фракции.
Дизельные фракции реализуются в виде следующих товарных продуктов: – компонент судового маловязкого топлива;
- печное топливо;
- компонент дизельного топлива по ГОСТ 305–2013;
- сырьё установки гидроочистки дизельного топлива (если она имеется в составе НПЗ) для получения товарного топлива кондиций Евро-5.
Бензиновые фракции могут использоваться следующим образом:
- в качестве компонента автомобильных бензинов;
- в качестве сырья для установок гидроочистки, изомеризации и риформинга, если таковые имеются в составе НПЗ; в этом случае возможно увеличение объёмов производства автобензинов кондиций Евро-5;
- в качестве сырья пиролиза для производства полимеров на смежных предприятиях.
Газ из узла ректификации может быть использован в качестве топливного газа для технологических установок НПЗ. В случае переработки на установке ТОК более 400…500 тыс. т сырья в год экономически целесообразно доукомплектовать установку узлом получения товарного сжиженного углеводородного газа (СУГ) 8 (см. рис. 1). Сегодня СУГ является высоколиквидным и дорогостоящим товарным продуктом, реализация которого приносит дополнительную прибыль заводу. За последний год его цена выросла в 2 раза и в конце лета 2021 года превысила цену высокооктанового бензина Евро-5. В зависимости от конъюнктуры рынка и логистических возможностей СУГ может найти применение:
- в качестве моторного топлива для автотранспорта, в том числе и для автотракторной техники, обслуживающей НПЗ;
- в качестве топлива для бытовых нужд в местных населённых пунктах;
- в качестве сырья для газохимических производств.
Необходимость строительства узла получения СУГ определяется на стадии разработки технико-экономического обоснования (ТЭО) целесообразности строительства установки ТОК.
Вышеуказанные фракции из блока ТОК могут смешиваться с прямогонными фракциями из атмосферной трубчатки и далее направляться на реализацию (вариант 1).
Если есть вероятность догрузить установку атмосферной трубчатки существующего НПЗ, то можно значительно уменьшить капиталовложения в установку ТОК, исключив из её схемы узел ректификации продуктов крекинга.
Принципиальная технологическая схема такого варианта представлена на рис. 2.
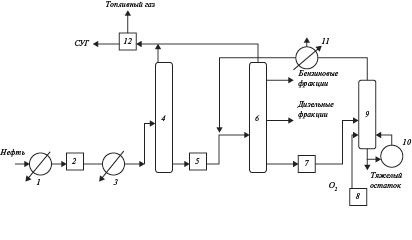
1, 3 11 – рекуперативные теплообменники; 2 – блок ЭЛОУ; 4 – отбензинивающая колонна; 5, 7 – печи; 6 – основная атмосферная колонна; 8 – блок получения кислорода; 9 – реактор; 10 – насос; 12 – блок получения СУГ
Мазут из кубовой части атмосферной колонны 6 догревается в печи 7 до температуры 400…500оС и подаётся в реактор 9. Ниже ввода сырья в реактор подаётся кислород (концентрация 97–98%). Здесь протекают реакции конверсии тяжёлых углеводородов в более лёгкие и одновременно реакции окисления незначительной части углеводородов с выделением тепла. Продукты ТОК выводятся из верхней части реактора 9, отдают часть тепла в рекуперативном теплообменнике 11 и направляются в колонну ректификации 6, где смешиваются с отбензиненной нефтью и разделяются на товарные фракции.
Необходимо отметить, что такая схема возможна только в тех случаях, когда имеется возможность догрузить колонну 6 дополнительным потоком углеводородов из реактора 9 (вариант 2). Потребуется выполнить расчёт колонны на новые условия работы, возможна замена внутренних контактных устройств. Также потребуется перерасчёт всего оборудования установки с вероятной заменой некоторой его части. Но в любом случае это будет значительно дешевле, чем строить новый узел ректификации 7 (см. рис. 1).
Если расчёты покажут невозможность (по тем или иным причинам) догрузки колонны 6 продуктами ТОК, то можно снизить общий объём переработки нефти на НПЗ, например, на 20% (вариант 3). При этом валовый объём товарной продукции завода (в рублях) не уменьшится, а затраты на закупку нефти снизятся на 20%, что значительно повысит экономические показатели деятельности предприятия в целом.
В качестве примера можно оценить прогнозируемые показатели для трёх вариантов применения установки ТОК на НПЗ, перерабатывающем 1 млн. т нефти типа URALS в год. Прогнозируемые объёмы производства дополнительных объёмов товарных нефтепродуктов представлены в таблице.
Сравнительные технико-экономические показатели вариантов НПЗ
Для расчётов экономических показателей стоимость приобретаемой нефти, реализуемых нефтепродуктов принята как среднестатистическая на второй квартал 2022 г. Капиталовложения по вариантам приняты по аналогам проектных работ, выполненных ранее АО «ИПН» с учётом коэффициента инфляции 2022 г.
Как видно из таблицы, реконструкция НПЗ по любому из трёх описанных вариантов значительно повышает экономику предприятия.
АО «ИПН» обладает большим положительным опытом реконструкции построенных ранее технологических установок ЭЛОУ-АТ, ЭЛОУ-АВТ (см. референц-лист на WWW.TRUBOPROVOD.RU).
Совместно с лицензиаром процесса ООО «НТЦ «Ахмадуллины» АО «ИПН» готово выполнить ТЭО для конкретного НПЗ. В рамках ТЭО будет проведена следующая работа:
- на пилотной установке будет определена конверсия конкретного образца сырья заказчика с целью расчета материального баланса будущей установки, а также определены свойства получаемых дополнительных нефтепродуктов;
- разработаны базовые проектные решения (исходные данные для проектирования), в рамках которых создается технологическая схема модернизируемого НПЗ и определяется конкретное технологическое оборудование и т.д.;
- рассчитаны прогнозируемые основные технико-экономические показатели по конкретному объекту с учётом текущих и перспективных цен на сырьё, товарные продукты, оборудование, строймонтажные работы и т.д.
На основании разработанного ТЭО заказчик принимает решение о строительстве установки ТОК или реконструкции существующего НПЗ.
Совместно с лицензиаром процесса ООО «НТЦ «Ахмадуллины» АО «ИПН» выполняет проектную и рабочую документацию для строительства установки ТОК, оказывает техническое сопровождение государственных экспертиз, осуществляет авторский надзор за строительством.
Список литературы
- G. Alonso-Ramírez, F. Sánchez-Minero, Jorge Ramírez, Rogelio Cuevas-Garcia & N. Moreno-Montiel. Analysis of the thermal hydrocracking of heavy fuel oil //Petroleum Science and Technology. DOI: 10.1080/10916466.2018.1428627.
- Курочкин А.К., Хазеев Р.Р. Экспериментальный поиск перспективной технологии глубокой переработки ашальчинской сверхвязкой нефти//Сфера. Нефть. Газ. 2015. №2. С. 52–72.
- Макаревич В.Н., Искрицкая Н.И., Богословский С.А. Ресурсный потенциал месторождений тяжелых нефтей европейской части Российской Федерации // Нефтегазовая геология. Теория и практика. 2012. Т. 7. №3. http://www.ngtp.ru/rub/6/43_2012.pdf
- Agustín García Barneto, José Ariza Carmona, María José Franco Garrido. Thermogravimetric assessment of thermal degradation in asphaltenes//Thermochimica Acta, Vol. 627–629. 2016. https://doi.org/10.1016/j.tca.2016.02.004.
- A. Gamarra & E. A. Ossa. Thermo-oxidative aging of bitumen//International Journal of Pavement Engineering, DOI: 10.1080/10298436.2016.1199876.
- Шакирзянова Г.И., Сладовская О.Ю., Сладовский А.Г., Зимнякова А.С., Нигметзянов Н.С. Замедленное коксование как эффективная технология углубления переработки нефти//Вестник технологического университета. 2017. Т. 20. №14.
- Chen N.Y., and E.J.Y. Scott. Low-Temperature Visbreaking Of Heavy Crude Oils. J Can Pet Technol 26 (1987): No Pagination Specified. doi: https://doi.org/10.2118/87-03-01.
- J.G. Speight: A technology of the past and the future//Scientia Iranica. Vol. 19. Issue 3. 2012. P. 569–573. https://doi.org/10.1016/j.scient.2011.12.014.
- Галиев Д.И., Емельянычева Е.А. Перспективные решения для установок висбрекинга нефтяных остатков //Вестник технологического университета. 2015. Т. 18. №8.
- Jasvinder Singh, Surendra Kumar, Madhukar O. Garg. Kinetic modelling of thermal cracking of petroleum residues//A critique. Fuel Processing Technology 94 (2012) 131–144.