Авторы: В.В. Бурлов (ООО «НПО «Нефтехим»), В.К. Крыжановский, Д.А. Панфилов(Санкт-Петербургский Государственный Технологический институт).
Опубликовано в журнале Химическая техника №3/2014
Увеличение ресурса разнообразных трубопроводных устройств продолжает оставаться одной из важнейших материаловедческих и конструкторских проблем. Основной причиной выхода труб из строя является коррозия, вызванная воздействием транспортируемых сред или рабочих тел, которые могут представлять собой разнообразные по физическому состоянию и химическим свойствам продукты. Общее для таких труб состоит лишь в том, что все они начинают разрушаться изнутри и в результате главным образом процессов химической коррозии, действие которой пытаются замедлить применением для изготовления труб дорогостоящих легированных хромоникелевых сталей. Необходимость совершенствования защиты труб различного назначения от коррозии особенно проявляется в оборудовании нефтехимического комплекса [1].
Известно, что полимерные материалы находят широкое применение для антикоррозионной защиты труб.
С этой целью используют как термопластичные, так и термореактивные пластики, в основном в виде внутренних покрытий [2, 3], толстостенных пластмассовых внутренних оболочек [4–6], а также по так называемой чулочной технологии [7]. Все эти приемы имеют ряд существенных недостатков, основные из которых перечислены далее.
Полимерные покрытия склонны к отслаиванию вследствие внутренних напряжений, неминуемо возникающих на границе полимер – металл; вставки из крупнотоннажных термопластов существенно уменьшают живое сечение трубы и вследствие их невысокой теплостойкости (80…100°С) ограничивают температуру транспортируемой среды; при чулочной технологии, как и любой технологии с применением реакционно-способных олигомеров, присутствует длительная фаза гелеобразования реакционно-способного олигомера, приводящая к неконтролируемому стеканию связующего внутри металлической трубы и, соответственно, к неконтролируемой неравнопрочности чулка по его сечению и длине.
Определенным выходом из создавшейся ситуации может служить вариант использования для коррозионной защиты труб, изготовленных промышленным способом, тонкостенных высокопрочных оболочек из высокопрочных полимерных композиционных материалов [8], таких, как стеклоили углепластики, модуль упругости и предел прочности которых существенно выше, чем у конструкционных термои реактопластов [9].
Применение таких оболочек характеризуется рядом привлекательных качеств, дающих преимущество перед существующими техническими решениями:
- надежность коррозионно-стойкой защиты трубы в течение существенно более длительного периода эксплуатации металл-пластиковой трубы;
- более высокая механическая прочность металл-пластиковой трубы благодаря высокопрочной оболочке (как следствие, либо возможность эксплуатации трубы при более высоких рабочих параметрах, либо уменьшение толщины стенки металлической трубы при постоянных эксплуатационных условиях);
- возможность замены высоколегированного металла труб более дешевым низколегированным или черным металлом;
- возможность установки этих оболочек в трубы из любого материала (металл, керамика, композиты).
Отметим, что применение предлагаемых промышленно изготавливаемых оболочек возможно не только на стадии изготовления металл-пластиковых труб, но и при устранении аварийных протечек в действующих магистральных трубопроводах [10].
Процесс установки оболочек в трубы существенно упрощен благодаря способности разработанных густосетчатых термореактивных связующих переходить в определенных условиях в высокоэластическое состояние, деформироваться в этом состоянии, сохранять полученную деформацию и в последующем контролированно восстанавливать форму, близкую к исходной.
Эффект высокоэластического деформирования густосетчатого полимерного связующего достигается созданием в нем топологической структуры, способной к локальным кинематическим перестроениям за счет включения в его пространственную сетку гибких, подвижных фрагментов.
Лучшие результаты были получены при использовании связующих следующего состава [11]:
- эпоксидиановая смола ЭД-20 (ГОСТ 10587);
- олигоэфируретандиоксид марки ППГ-3А (ТУ 38-03–001);
- изометилтетрагидрофталевый ангидрид (ТУ 6-09-3321) (отвердитель);
- 2, 4, 6-трис (диметиламинометил) фенол (ТУ 6-09-6101) (ускоритель).
Соотношение ЭД-20/ППГ-3А изменялось в интервалах от 1,0/0,1 до 1,0/1,0.
Для намотки оболочек в качестве волокнистых наполнителей использовались стеклоровинг марки РБН 10840 (ТУ 648-00204984-22) и углеровинг Урал-4 (ТУ 21-25-234).
Оболочки получали методом мокрой намотки ровинга на оправки диаметром 80 и 220 мм длиной до 2 500 мм на намоточном станке в условиях промышленного производства ФГУП «Прометей» (Санкт- Петербург). Были изготовлены оболочки диаметром 80 мм с толщиной стенки 1,5 мм и диаметром 220 мм со стенкой толщиной 1,8 мм. Установку оболочек в стальные трубы выполняли в условиях технологической лаборатории кафедры химической технологии пластмасс СПбГТИ(ТУ), рис. 1.
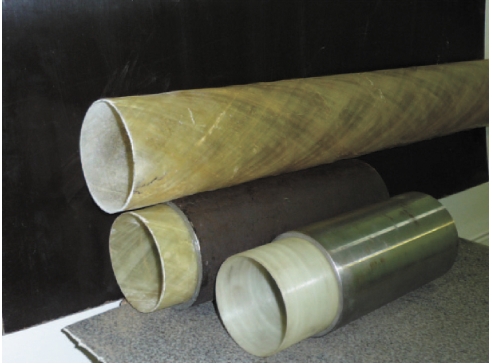
Анализ особенностей исследованных стеклои углепластиков свидетельствует: температуре пропитки 60°С ниже, чем у стеклоровинга (табл. 1). Это можно объяснить меньшей адгезией углеволокна к эпоксидным составам, чем у стеклоровинга, даже при отсутствии операций его предварительной обработки (отжиг замасливателя);
- с увеличением содержания модификатора растут значения относительного удлинения в статических условиях нагружения и ударной вязкости при динамических нагрузках, при этом собственно прочность стеклои углепластиков уменьшается;
- введение модификатора до 20% снижает прочность на 4–6%. При дальнейшем увеличении содержания ППГ-3А в ЭД-20 до 50% прочность при растяжении уменьшается на 12–17%.
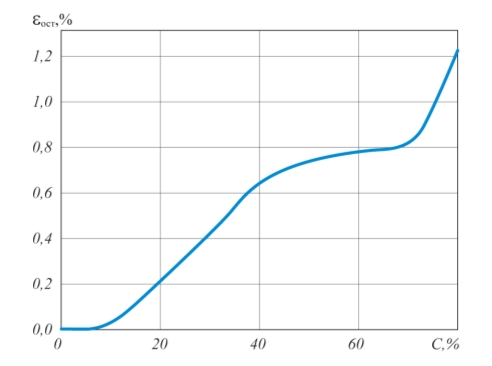
С учетом полноты восстановления высокоэластической деформации (ВЭД) разработанных пластиков (рис. 2) было установлено, что предельное содержание структурного модификатора в ЭД-20, применяемой для деформируемых оболочек, не должно превышать по объему 20%.
Испытания оболочек из стеклои углепластиков с оптимальным составом связующего показали, что система ЭД-20 + ППГ-3А + стеклоровинг допускает ВЭД с последующим ее «замораживанием» и затем полном восстановлением до 14–18% первоначального диаметра оболочки. В то же время оболочки из углепластика разрушались уже при деформировании на 8–10% (табл. 2).
Таблица 1
Влияние эластификатора на свойства стекло- и углепластиков, полученных контактным формованием (отвердитель изо-МГТФА)
Содержание ППГ-3А в связующем, % | Содержание связующего, % | Предел прочности при растяжении, МПа | Относительное удлинение при 20°С, % | Ударная вязкость, кДж/м2 |
Стеклопластик | ||||
0 | 37 | 248 | 0,6 | 108 |
10 | 36 | 239 | 0,9 | 113 |
20 | 38 | 232 | 1,1 | 120 |
30 | 36 | 223 | 1,4 | 125 |
40 | 36 | 218 | 2,0 | 127 |
50 | 37 | 206 | 3,2 | 129 |
Углепластик | ||||
0 | 48 | 452 | 0,3 | 68 |
10 | 49 | 448 | 0,7 | 76 |
20 | 48 | 436 | 1,4 | 82 |
30 | 47 | 430 | 1,8 | 87 |
40 | 48 | 426 | 2,1 | 92 |
50 | 49 | 398 | 4,2 | 95 |
Оболочки из стеклоровинга, полученные спирально-перекрестной намоткой под углом ϕ = ±30°, характеризуются не только способностью к термодеформированию до 18%, но и к практически полному восстановлению исходного размера при «распрямлении замороженной» ВЭД.
Таблица 2
Результаты испытаний оболочек из стекло- и углепластика с разным углом намотки j при их деформировании в стеклообразном (Т = 20°С) и в высокоэластическом состоянии
Вид намотки | Наружный диаметр, мм | Толщина стенки, мм | Температура деформации, °С | eВЭ, % | Диаметр после инверсии ВЭД, мм |
Стеклопластик | |||||
Поперечная | 150 | 1,4 | 90 | Образец разрушается | |
Спирально- перекрестная, j = ±45° |
150 | 1,5 | 20 | Образец разрушается | |
150 | 1,5 | 90 | 14 | 150 | |
150 | 2,0 | 90 | 15 | 152 | |
Спирально- перекрестная, j = ±30° |
150 | 1,5 | 20 | Образец разрушается | |
150 | 1,5 | 90 | 18 | 152 | |
150 | 2,0 | 90 | 16 | 153 | |
Углепластик | |||||
Поперечная | 150 | 1,5 | 90 | Образец разрушается | |
Спирально- перекрестная, j = ±45° |
150 |
1,5 |
90 |
Образец разрушается |
Таблица 3
Свойства стеклопластиков, полученных различными методами формования
Свойства | Без модификатора | С модификатором (20% ППГ-3А) | ||||
Прессование | Намотка | Прессование | Намотка | |||
Спиральная
j = ±30° |
Поперечная | Спиральная
j = ±30° |
Поперечная | |||
Плотность, кг/м3 | 1750 | 1620 | 1680 | 1780 | 1645 | 1710 |
Разрушающее напряжение, МПа: при растяжении
при изгибе |
294
318 |
590/342
– |
386/178
– |
210
487 |
680/450
– |
578/280
575/362 |
Относительное удлинение при растяжении, (Т = 20°С), % | – | 1,8 | 0,5 | – | 2,5 | 1 |
Модуль упругости при растяжении, ГПа | – | 22/14 | 28/18 | – | 45/32 | 58/31 |
Ударная вязкость, кДж/м2 | 104 | 253/262 | 264/235 | 98 | 348/326 | 408/392 |
Водопоглощение, % | 0,05 | 0,5 | 0,5 | 0,05 | 0,5 | 0,5 |
Примечания. 1. Значения в числителе соответствуют продольному направлению армирования, в знаменателе – поперечному. 2. Для прессованных стеклопластиков коэффициент наполнения составляет 70–75%, для намотанных – 64–70%. |
Из стеклопластиков, полученных намоткой на серийном оборудовании (спиральная с углом намотки ϕ = ±30°, поперечная), а также прессованием, лучшие результаты (табл. 3) по прочности, деформативности в высокоэластическом состоянии и по восстановлению ВЭД отмечены для оболочек, изготовленных спирально-перекрестной намоткой стеклоровинга по мокрой технологии с углом намотки ϕ = ±30° [12].
Исследование влияния содержания модификатора на химическую стойкость перспективного эпоксидного связующего для стеклопластиков показало, что лучшими показателями по водопоглощению, маслостойкости и бензостойкости характеризуются составы с содержанием структурного модификатора до 30%, т.е. эпоксиолигоэфиры с наиболее плотной сеткой (табл. 4). Химическая стойкость стеклопластиков, полученных различными способами (табл. 5) свидетельствует о том, что сособ намотки не снижает антикоррозионные свойства полимерных композиционных материалов по сравнению с широко распространенным способом прессования стеклопластиков, главная особенность которого заключается в использовании высокого давления, способствующего достижению предельной плотности пластика (см. табл. 3).
Способность разработанного связующего к инверсии ВЭД позволила разработать принципиально новую технологию как установки оболочки внутрь стальной (или из иного материала) трубы, так и неразъемного соединения единичных оболочек (труб) конечной (стандартной) длины в бесконечную плеть.
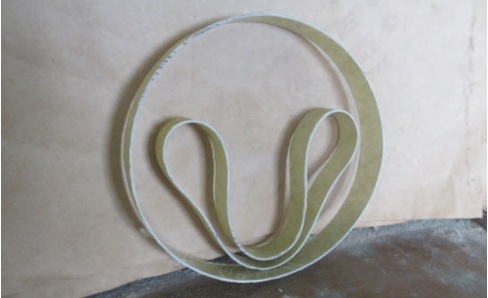
Известно, что процесс футеровки трубы из любого материала футеровочной оболочкой с плотным прилеганием к ее внутренней поверхности, т.е. когда наружный диаметр композитной оболочки совпадает с внутренним диаметром трубы, весьма затруднен трением скольжения оболочки о стенки трубы. Особенно этот процесс затруднен в случае ремонта уже побывавших в эксплуатации труб. Способность разработанных оболочек к деформированию с последующей инверсией, восстановлением формы устраняет эти трудности. Установлено, что предлагаемые оболочки допускают продольное складывание, фиксацию этого складывания и последующее восстановление оболочки к исходной конфигурации [12]. Из рис. 3 видно, что кольцевому сечению цилиндрической оболочки технологическим продольным смятием может быть придана, например, форма своеобразной гантели с резким уменьшением геометрической площади и критического поперечного размера. Применительно к реальной технологии эта способность оболочек обусловливает следующую последовательность операций (рис. 4): а – оболочка 1 с исходным контуром; б – монтажное продольное смятие оболочки 1 в условиях термодеформирования связующего с фиксацией полученной конфигурации сечения (гантель) 2; в – установка термодеформированной оболочки 2 в трубу 3; г – нагрев оболочки 2, приводящий к ее расправлению и плотному прилеганию к внутренней поверхности трубы 3.
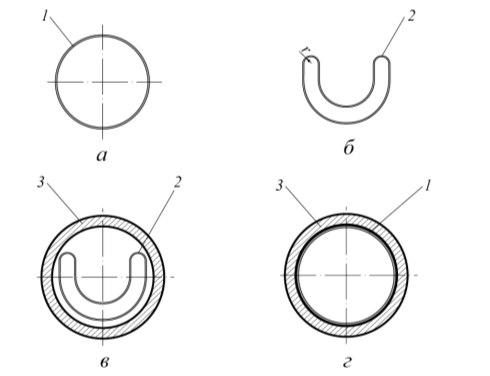
Таблица 4
Химическая стойкость ЭД-20, модифицированной ППГ-3А и отвержденной изо-МТГФА
Соотношение ППГ-3А : ЭД-20 | Водопогощение за 24 ч, при 20°С, % | Маслостойкость, % | Бензостойкость, % |
1 : 4 | 0,04 | 0,05 | 1,9 |
3 : 7 | 0,07 | 0,06 | 2,8 |
1 : 1 | 0,13 | 0,15 | 3,7 |
7 : 3 | 0,32 | 0,28 | 5,6 |
Таблица 5
Химическая стойкость стеклопластиков
Вид переработки | Содержание модификатора, % | Изменение массы после выдерживания в среде, % | |
10%-ный NaOH | Концентрированная H2SO4 | ||
Прессование | 20 | +0,24 | +0,41 |
Намотка | 20 | –0,04 | +0,14 |
Прессование | 50 | +0,06 | +0,32 |
Намотка | 50 | –0,05 | +0,21 |
Температура испытаний 50°С; время экспозиции 7 сут. |
Нагрев оболочки может производиться подачей внутрь нее горячего воздуха. Расправление смятой оболочки происходит самопроизвольно или под давлением воздуха до 0,1 МПа.
Окончательный результат операции футеровки стальной трубы деформируемой оболочкой, выполненной в лабораторных условиях современной вузовской кафедры представлен на рис. 5.
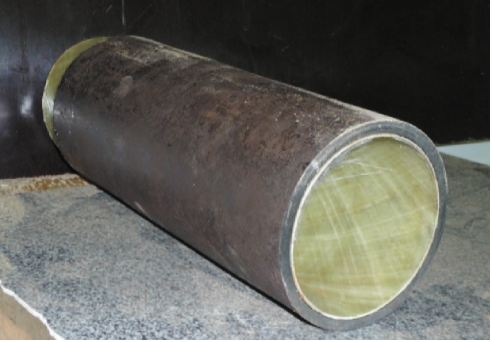
Технология соединения единичных оболочек в бесконечную плеть осуществляется следующим образом (рис. 6): конец одной их соединяемых оболочек 1, называемой первой, нагревают до температуры перехода в высокоэластическое состояние (100 ± 10°С), а затем радиально расширяют его с помощью конического расширителя 2, перемещаемого по геометрической оси оболочки внутрь нее. В этом положении конец первой оболочки приобретает форму конического раструба, которая сохраняется в результате охлаждения (замораживания) до температуры ниже рабочей и временно остается в растянутом состоянии. Далее в этот временный раструб вводят до упора цилиндрический конец второй оболочки 3. Для увеличения прочности соединения на этот участок второй оболочки наносится слой адгезива 4 холодного отверждения. Расположение соединенных к этому моменту оболочек показано на рис 6, в. После этого участок соединения нагревают ИК-нагревателем или иным способом до температуры выше температуры размягчения. Это приводит к инверсии ВЭД первой оболочки, в результате чего она плотно облегает конец второй оболочки, образуя соединение, показанное на рис. 6, г.
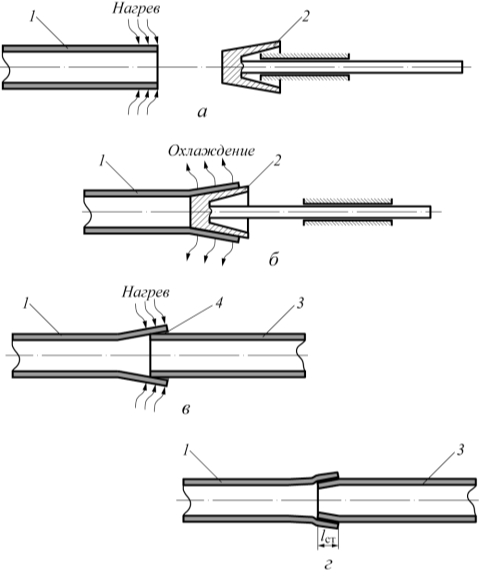
Известно, что для достижения максимальной прочности любого клеевого соединения необходимо, чтобы толщина адгезива была минимальной [13].
Это условие выполняется, если для соединения труб используют технологию инверсируемого раструба. В процессе инверсии временного раструба осуществляется самоцентровка труб, устраняются непроклеенные участки, а излишки клея выдавливаются. В результате формируется клеевой слой, обеспечивающий требуемые прочностные характеристики. Для успешного практического осуществления изложенной идеи следует учесть ряд обстоятельств. Температурно-временной режим усадки раструба и отверждения клея должен быть синхронизирован таким образом, чтобы сначала происходил процесс инверсии раструба, а после его завершения – процесс отверждения клея.
В качестве адгезива для соединения труб по изложенной технологии была разработана эластичная композиция (εр = 80–120%), комплекс свойств которой удовлетворяет поставленной задаче. В данном случае использовалось разработанное связующее с традиционным аминным отвердителем – полиэтиленполиамином в стехиометрическом соотношении. Жизнеспособность композиции при 20°С составляет 120 мин, при 50°С – 60 мин, а время отверждения при 20°С – 24 ч, при 80°С – 30 мин.
Определялась и адгезионная прочность при сдвиге в системах стеклопластик-металл в зависимости от содержания ППГ-3А при различном времени отверждения. Установлено, что при содержании модификатора 20–30% адгезионная прочность возрастает при любой продолжительности отверждения в 2,5 раза.
Проверка полученных соединений на прочность при растяжении показала, что в условиях правильной конструкции клеевой шов и материал труб равнопрочны.
Монтажная длина стыка lст (см. рис. 6, г) определяется по уравнению lст = π2δ(d + 2δ)[σр]/[τср] = 10δ(d + 2δ)[σр]/[τср], м, где δ – толщина стенки соединяемых труб; d – внутренний диаметр соединяемых труб; [σр] – допускаемое напряжение растяжения для соединяемых труб; [τср] – допускаемое напряжение среза для адгезионного шва.
Экспериментально установлено, что соединение инверсионным раструбом легко воспринимает операцию технологического смятия, например V-образную, сохраняя придаваемую ему конфигурацию сколь угодно долго при температуре ниже температуры размягчения и возвращаясь к цилиндрической форме при последующем общем нагреве расправляемой трубы.
Преимущества предлагаемой технологии соединения труб при помощи инверсируемого раструба по сравнению с традиционно применяемыми – высокая надежность изделий, увеличенный их ресурс, простота изготовления, минимальный объем подготовительных работ.
Технология ВЭД армированных оболочек может быть расширена за область ее инверсии и использована для производства изделий, конфигурация которых не позволяет получать их методом намотки. Это относится к намоточным изделиям с изменяемой по знаку кривизной сечения – волнистой, звездообразной, с продольными углублениями, гантелеобразной формы с любым соотношением радиусов кривизны поверхностей.
Основным условием сохранения деформированными оболочками приданной им формы является температура эксплуатации, которая должна быть ниже температуры размягчения связующего.
Таким образом, намоточные изделия с температурой размягчения связующего 140°С и температурой хрупкости –70°С (интервал, вполне достигаемый на базе отечественных эпоксидных смол и модификаторов) могут в деформированном состоянии эксплуатироваться в интервале температур –60…+130°С.
Увеличение верхнего температурного предела эксплуатации до температур, превышающих 130°С может быть достигнуто также с использованием технологии двухстадийного отверждения.
В целом промышленное использование разработанной на отечественных компонентах и реализуемой на типовом оборудовании технологии термодеформируемых оболочек представляется и своевременным, и целесообразным.
Список литературы
- Бурлов В.В., Алцыбеева А.И., Парпуц И.В. Защита от коррозии оборудования НПЗ. СПб.: Химиздат, 2005.
- Швейцер Ф.А. Коррозия пластмасс и резин. Пер. с англ./Под ред. Резниченко С.В., Морозова Ю.Л. СПб.: Научные основы и технологии, 2010.
- Патент РФ №2220995. Способ защиты и восстановления прокорродировавших металлических поверхностей.
- Патент РФ №22113394. Стеклопластиковая труба.
- Удовенко В.Е., Сафонова И.П., Гусева Н.Б. Полиэтиленовые трубопроводы. М.: Полимергаз, 2003.
- Орлов В.А. Стратегия восстановления водопроводных и водоотводящих сетей. М.: Изд-во ассоциации строительных вузов, 2001.
- Патент РФ №2037733. Способ покрытия внутренней поверхности трубопровода.
- Патент РФ №2248496. Способ защиты внутренней поверхности трубопровода.
- Крыжановский В.К., Бурлов В.В. Технические свойства полимерных материалов. Уч.-справ. пособие. СПб.: Профессия, 2007.
- Крыжановский В.К. Бурлов В.В. Применение эффекта регулирования высокоэластической деформативности густосетчатых полимеров в технологии композиционных оболочек для нефтегазового комплекса//Тез. докл. VIII междунар. НТК. Уфа: 2002.
- Крыжановский В.К., Семенова А.Д. Тонкослойные стеклопластики на модифицированном эпоксидном связующем с регулируемыми термоинверсионными свойствами. Изв. СПбГТИ (ТУ). 2012. №13 (39).
- Паниматченко А.Д., Бурлов В.В., Крыжановский В.К. Технология производства высококачественных тонкостенных стеклопластиковых оболочек и их применение//Сб. мат-лов конф. «Качество полимерных материалов и изделий: инновации, сертификация, контроль». СПб.: 2003.
- Патент РФ №2266455. Способ неразъемного соединения стеклопластиковых труб.