Автор: Г.С. Яицких, П.А. Вахрушин, А.В. Краснов (АО «ИПН»), В.Р. Исхаков (Филиал ПАО АНК «БАШНЕФТЬ»).
Опубликовано в журнале Химическая техника №5/2016
Основная доля нефтеперерабатывающих заводов (НПЗ) нашей страны вводилась в эксплуатацию в 60– 80 гг. прошлого столетия. В это время особое внимание уделяли увеличению единичных мощностей установок, а вопросы экономии энергоресурсов и повышения технико-экономических показателей отходили на второй план.
Такой подход вполне себя оправдывал чрезвычайно низкой стоимостью энергоносителей и отсутствием жесткого экологического законодательства.
В настоящее время стоимость строительства и энергоносителей значительно выше и продолжает монотонно увеличиваться, а экологические требования ужесточаются с каждым годом. Эти обстоятельства ставят перед нефтепереработчиками задачу оптимизации технологических схем и режимов переработки с целью увеличения выхода целевого продукта, повышения его качества, снижения эксплуатационных затрат и уменьшения размеров оборудования. Широко распространенным требованием к производственному процессу стало низкое энергопотребление, которое обеспечивает ощутимые преимущества в коммерческой рентабельности и соответствие предприятия экологическим требованиям. Именно поэтому для многих НПЗ, спроектированных и построенных во времена низких цен на энергоносители, работающих далеко не в оптимальном режиме с точки зрения энергопотребления, основной целью является снижение себестоимости продукта путем снижения расхода энергоносителей.
Большинство НПЗ под лозунгом энергосбережения зачастую ограничиваются лишь мероприятиями по экономии электроэнергии путем, например, установки частотных регуляторов для электроприводов насосов и вентиляторов воздушных холодильников, использования экономичных электроосветительных приборов и т.п.
При этом «модную» в настоящее время установку частотных регуляторов для электроприводов вентиляторов воздушных холодильников производят тогда, когда можно вообще обойтись без воздушных холодильников.
Некоторые предприятия рассматривают возможность применения «бросового тепла» (теплота технологических потоков температурой ниже 100…120°С) для производства теплофикационной воды. Эту воду можно использовать для обогрева полов открытых насосных станций, заводских зданий, а также для обогрева резервуаров для хранения нефти, мазута, дизельного топлива и пожарной воды. Однако этот способ утилизации теплоты имеет сезонный характер, и в летний сезон, когда нагрузка на водяные и воздушные холодильники максимальна, полезная утилизация теплоты практически отсутствует. Сейчас мало кто из отечественных нефтепереработчиков понимает, что основной потенциал экономии энергоносителей (до 90%) скрывается в самих технологических процессах, а особенно – в схеме рекуперации. В целом модернизацию, направленную на повышение энергетической эффективности и энергосбережение, следует начинать с реакторной системы, системы разделения и системы теплообмена и лишь потом переходить к интенсификации утилит (внешние энергоресурсы – электрическая энергия, пар и топливо).
Повышение энергетической эффективности должно быть одной из составляющих любых реконструкций, технических перевооружений и модернизаций, проводимых на объекте. Так, изменения указанных систем влияют и на выпуск целевой продукции, и на объемы требуемых энергетических ресурсов. Нельзя отделять технологическую эффективность от энергетической эффективности.
Попытка утилизировать бросовую теплоту – это лишь заход со «стороны потерь», в то время как начинать нужно со «стороны технологического потребления».
Правильное проектирование системы рекуперации теплоты любого технологического процесса позволяет значительно снизить нагрузку на печи, паровые подогреватели, а также водяные и воздушные холодильники, что, в свою очередь, позволяет значительно сэкономить на топливе, электроэнергии, паре и оборотной воде. Снижение потребления этих энергоносителей может составлять 10–20%, а в отдельных случаях и до 40–50% начального энергопотребления.
Экономии на энергоносителях можно достичь в трех основных направлениях:
- оптимизация системы теплообмена;
- вовлечение в рекуперацию максимального числа основных технологических и вспомогательных потоков;
- использование высокоэффективных теплообменных аппаратов.
Оптимизация системы теплообмена
При разработке системы теплообмена перед технологом стоит задача рекуперации максимального количества теплоты технологических потоков при наименьших капитальных затратах на оборудование. При этом число потоков, которые нужно нагреть или охладить, достаточно велико. Например, на установке первичной перегонки для нагрева нефти обычно используется теплота потоков мазута, газойля, дизельного топлива, циркуляционных орошений и др. В связи с этим стоит непростая задача: какие именно потоки и в какой последовательности соединять между собой рекуперативными теплообменниками. Чаще всего при проектировании руководствуются следующими принципами:
- рекуперировать теплоту потоков, связанных с одним аппаратом (например, нагревать входящее в реактор сырье выходящим их него продуктом или входящее в колонну сырье выходящим из нее кубовым остатком);
- для нагрева потоков с низкой температурой стараться использовать технологические потоки с более низкой начальной температурой, а для нагрева потоков с высокой начальной температурой использовать более горячие потоки;
- подбирать теплообменник или группу теплообменников таким образом, чтобы обеспечить передачу максимально возможного количества теплоты;
- оптимизировать конфигурацию теплообменника (или системы теплообменников) с целью повышения коэффициента теплопередачи и снижения поверхности теплообмена.
Зачастую этих принципов не всегда достаточно для обеспечения максимальной или близкой к максимальной рекуперации теплоты. В связи с этим в западных странах во время энергетического кризиса в середине 1970-х годов появился новый метод оптимизации системы теплообмена, получивший название Пинч-анализ. В последние десятилетия этот метод интенсивно развивался и получил широкое практическое применение на Западе.
Использовать Пинч-анализ можно как при проектировании новых, так и при реконструкции существующих технологических установок, при этом, по практическим данным, капитальные затраты на перевооружение теплообменного ряда в отдельных случаях были сведены всего лишь к переобвязке существующих теплообменников, а капитальные вложения окупались зачастую всего за несколько месяцев [1, 2]. Данный метод позволяет заказчику проводить поэтапную оптимизацию системы теплообмена с пошаговыми изменениями в структуре теплообмена, начиная с переобвязки теплообменных аппаратов, разделения потоков, интенсификации теплообмена и заканчивая увеличением площадей теплообмена с определением приемлемой стоимости и эффективности инвестиций.
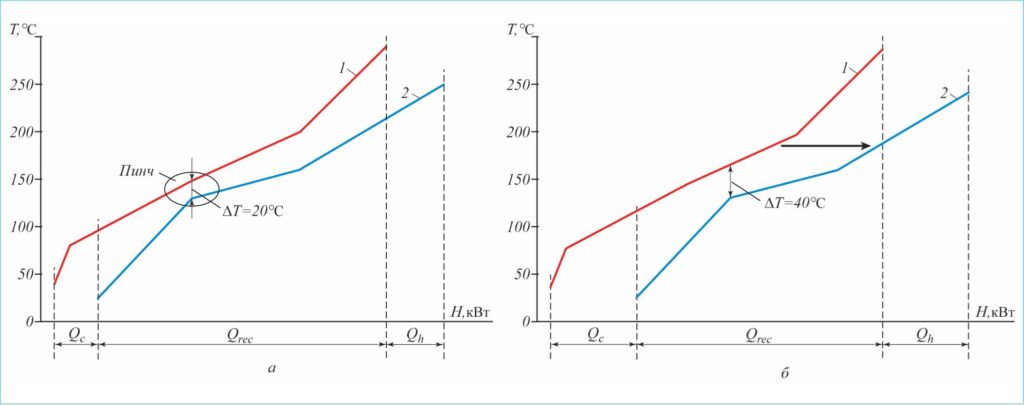
Вкратце расскажем об основных принципах этого метода. Пинч-анализ начинается с составления на основе исходных данных так называемых составных кривых технологических потоков, которые отображаются на температурно-энтальпийной плоскости (рис. 1, а). Потоки, которые необходимо охладить, в Пинч-анализе называют горячими потоками (кривая 1), а потоки, которые необходимо нагреть, – холодными (кривая 2). Минимальное расстояние между составными кривыми вдоль температурной оси – это минимальная разность температур (ΔТmin) между горячим и холодным потоком в теплообменной сети, соответствующей данной диаграмме, а сама область сближения называется пинчем.
График составных кривых несет в себе следующую полезную информацию:
- количество теплоты Qrec, которое может быть передано от горячих потоков к холодным, – область перекрытия кривых вдоль оси абсцисс;
- минимальное количество теплоты Qh, которое должно быть передано холодным потокам от внешнего источника теплоты, и минимальное количество теплоты Qс, которое должно быть передано от горячих потоков внешним энергоносителям.
По составным кривым также можно с приемлемой точностью рассчитать минимальную общую площадь поверхности теплообмена, обеспечивающую необходимый перенос теплоты от горячих потоков к холодным. Очевидно, что капитальные затраты на теплообменное оборудование, которые возрастают с увеличением площади поверхности теплообмена, должны окупаться экономией на энергоносителях. Пинч-анализ позволяет определить стоимостной компромисс между экономией на энергоносителях и капитальными вложениями при заданном сроке окупаемости. В Пинч-анализе разработчик имеет право сдвигать кривую холодных потоков вправо или влево вдоль оси абсцисс, тем самым увеличивая или уменьшая ΔТmin, Qh, Qс, Qrec (рис. 1, б). При движении вправо Qh и Qс увеличиваются, тем самым повышаются затраты на внешние энергоносители. В свою очередь при этом уменьшается Qrec и увеличивается ΔТmin, что снижает минимальную общую площадь поверхности теплообмена, а, следовательно, и стоимость оборудования. Рассчитав капитальные вложения и затраты на энергоносители для нескольких положений составной кривой холодных потоков, можно построить кривые зависимости этих затрат (рис. 2), а также кривую зависимости суммарных затрат от ΔТmin и определить ΔТopt, при которой суммарные затраты будут минимальны. Таким образом, проектировщик определяет для себя целевые значения количества потребляемых энергоносителей и общей площади поверхности теплообмена.
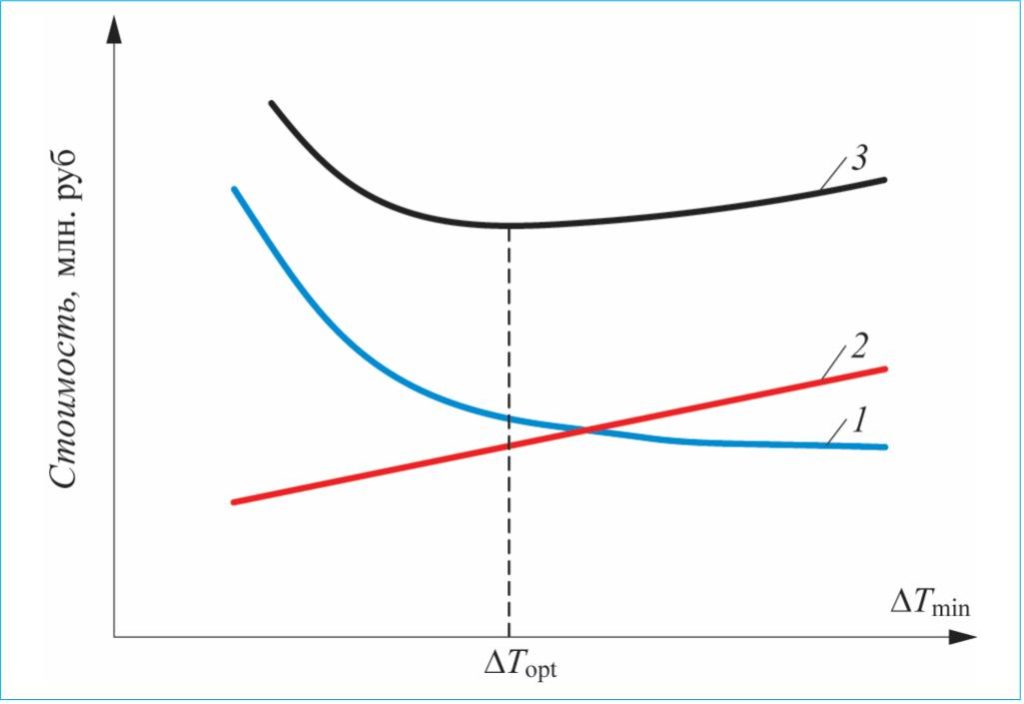
1 – капитальные затраты; 2 – стоимость энергоносителей;
3 – общая приведенная стоимость
После этого можно начинать размещать теплообменное оборудование, руководствуясь правилами Пинч-анализа, основные из которых следующие:
- запрещается переносить тепловую энергию от горячих потоков к холодным через пинч;
- запрещается подводить теплоту от внешних энергоносителей к холодным потокам ниже пинча;
- запрещается отводить теплоту горячих потоков к внешним энергоносителям выше пинча.
Выполнение этих и других принципов Пинч-анализа позволяет оптимизировать систему теплообмена при проектировании новой или реконструкции существующей технологической установки нефтегазопереработки, химии и нефтехимии, а результатом этой оптимизации, как уже было сказано, может стать экономия до 40–50% затрат на энергоносители.
Именно на стадии проектирования как нового строительства, так и реконструкций и технических перевооружений необходимо в обязательном порядке проводить оптимизацию системы теплообмена при заданных сроках окупаемости самого проекта. Это позволит не ухудшать показатели экономической эффективности проекта и при этом снизить затраты на последующую эксплуатацию. Именно на стадии проектирования это можно сделать гораздо дешевле и правильнее, иначе есть риск получить неэффективную установку и израсходовать средства на закупку бесполезных с точки зрения энергоэффективности воздушных и водяных холодильников, в то время как данные капитальные затраты можно было бы потратить на повышение эффективности теплообмена.
Вовлечение в рекуперацию максимального числа потоков
Зачастую при проектировании для рекуперации теплоты на технологических установках по тем или иным причинам используют не все технологические, а уж тем более вспомогательные потоки. Например, при проектировании системы теплообмена на установке первичной перегонки нефти очень часто в теплообмен с нефтью не вовлекают керосиновую фракцию и паровые потоки верхов колонн. Обосновывается данное решение тем, что пространство теплообменного аппарата, занятое нефтью, находится под более высоким давлением, чем пространство дистиллята, вследствие чего при нарушении герметичности нефть, попадая в поток дистиллята, необратимо «портит» продукт. Однако рекуперация теплоты паров верха колонны, имеющих значительный потенциал по тепловой энергии и температуре, весьма выгодна и широко используется в мировой практике проектирования систем конденсации установок, тем более что уже существуют технические решения, практически исключающие попадание сырья в продуктовые потоки.
Другой пример применения новых потоков с целью энергосбережения – использование теплоты конденсата, образовавшегося из пара высокого давления, для получения пара низкого давления и последующего применения его в технологии или на объектах общезаводского хозяйства, а также использование конденсата пара низкого давления на общезаводские нужды.
Кроме того, возможна выработка электроэнергии с использованием потенциала технологических потоков с высоким давлением при их дросселировании.
Использование высокоэффективных теплообменных аппаратов
В качестве основных теплообменных аппаратов в блоках теплообмена установок широко используют теплообменники кожухотрубчатого типа, значительно реже пластинчатые теплообменники. Однако следует заметить, что пластинчатые теплообменники обладают преимуществами перед кожухотрубчатыми и лучше подходят для целей рекуперации теплоты по ряду причин.
Во-первых, это возможность работы при низкой разности температур горячего и холодного потока (ΔТmin), которая является движущей силой процесса теплопередачи. Величина ΔТ оказывает существенное влияние на площадь теплообменной поверхности и, следовательно, на стоимость теплообменной системы. Увеличение ΔТ, с одной стороны, приводит к снижению площади теплообмена, а с другой – снижает доступную для рекуперации теплоту. При уменьшении ΔТ, наоборот, происходит рост требуемой площади теплообменной поверхности (а вместе с ней и стоимости теплообменной системы), но при этом увеличивается количество рекуперируемой теплоты. В связи с этим для различных типов теплообменных аппаратов установлены свои оптимальные значения ΔТ. При применении кожухотрубчатых аппаратов не следует устанавливать ΔТ менее 10°С, для пластинчатых аппаратов ΔТ может доходить до 5°С.
Во-вторых, кроме возможности работы при низких температурных напорах, пластинчатые аппараты отличаются строгим противоточным движением потоков теплоносителей, тогда как даже в одноходовых кожухотрубчатых аппаратах из-за наличия в кожухе поперечных перегородок присутствуют поперечные течения, что также снижает эффективность теплообмена.
Другими преимуществами пластинчатых аппаратов являются более высокие коэффициенты теплопередачи, пониженная восприимчивость к загрязнениям, высокие скорости потоков, высокая удельная площадь поверхности на единицу объема.
В целом, заводы, эксплуатирующие пластинчатые теплообменники, положительно отзываются о данном типе аппаратов, есть только единичные сообщения о возникновении протечек на горячих потоках. Хорошим решением может быть совместная установка кожухотрубчатых теплообменников для рекуперации теплоты технологических потоков с высоким температурным напором (ΔТ > 10°C) и пластинчатых теплообменников для рекуперации теплоты потоков с низким напором (ΔТ < 10°C).
Все большую популярность набирают сварные пластинчатые теплообменики – компаблоки. Компаблок – это сварной компактный пластинчатый теплообменник, в котором отсутствуют прокладки между пластинами.
Благодаря усовершенствованной конструкции компаблок может работать в агрессивных средах при высоком давлении и в широком диапазоне температур. Компаблок благодаря малому размеру легко может вписаться практически в любую тепловую систему. Их применение можно рекомендовать в различных процессах конденсации и ребойлерах.
На тяжелых и вязких продуктах практическим лидером являются спиральные теплообменные аппараты.
На газосырьевых и газопродуктовых средах гидрогенизационных процессов высокую эффективность показывают теплообменные аппараты типа Packinox.
В настоящее время решениями задач по снижению энергопотребления на российских НПЗ занимаются такие зарубежные компании, как KBC, Aspen Technology и др. Они проводят энерготехнологический аудит предприятия, который включает:
- сбор необходимых исходных данных (изучение проектной документации, режимов работы установки, проведение обследований и т.д.);
- моделирование работы установки с использованием собственного программного обеспечения;
- оценку потенциала системы в отношении снижения энергопотребления;
- разработку технических решений по снижению расхода энергоносителей;
- определение основных экономических показателей (стоимость, срок окупаемости) предлагаемых мероприятий по реализации этих технических решений.
Очевидно, что стоимость этих работ, выполненных иностранной компанией, будет предельно высокой, особенно при сложившейся ситуации в мире.
АО «ИПН» – одна из немногих отечественных проектных организаций, которая готова провести энерготехнологический аудит на технологических установках нефтеи газоперерабатывающих, химических и нефтехимических предприятий, а также провести аудит завода в целом. Компания выполнила и практически реализовала ряд проектов по реконструкции технологических установок, в результате которых значительно повышена энергоэффективность производственных процессов.
Среди них следующие:
- установка АТ-2 на Краснодарском НПЗ;
- установки СПГК и 22/4 на Афипском НПЗ;
- установка 22/4 на Московском НПЗ и др.
К тому же необходимо отметить, что специалистами АО «ИПН» разработаны и запатентованы технические решения по выработке электроэнергии с использованием низкопотенциальной теплоты технологических потоков [3]; по использованию теплоты конденсации паров нефтепродуктов, отходящих с верха колонн установки первичной перегонки для нагрева сырой нефти [4].
Нужно сказать, что сейчас не все отечественные предприятия понимают, что больший экономический эффект заключается не в поиске наиболее дешевых товаров (технологические аппараты, приборы КиП и т.д.) и услуг (инжиниринг, проектирование) путем проведения закупок на основе тендеров, а в поиске толкового исполнителя, который сможет своими идеями добиться значительного увеличения прибыли для заказчика.
Необходимо в обязательном порядке включать в состав технического задания на планируемое новое строительство и реконструкцию требования по повышению энергетической эффективности, начиная с оптимизации систем теплообмена. В Европе данная практика уже нашла свое отражение в нормативной документации Евросоюза по повышению энергетической эффективности. Российская Федерация в данном направлении должна брать на вооружение уже имеющиеся подходы и принципы, обеспечивающие снижение себестоимости продукции.
Список литературы
- Смит Р., Клемеш Й., Товажнянский Л.Л., Капустенко П.А., Ульев Л.М. Основы интеграции тепловых процессов. Харьков: НТУ «ХПИ», 2000.
- Жулаев С.В. Пинч-анализ и оптимизация промышленных объектов//«Нефтегазовое дело». 2012. №2.
- Пат. RU 141991: МПК F 01 K 17/02 (2006.01). Устройство утилизации тепла потоков нефтепродуктов.
- Пат. RU 2014 122080: МПК C 10 G 7/00 (2006.01). Установка первичной перегонки нефти (варианты).