Новая конструкция ячеистой перегородки для печи Claus повышает производительность и характеристики технологического потока
Авторы: ДЖЕФФРИ БОУЛБРУХ (Blasch Precision Ceramics), МОССАЕД И АЛЬ-АВВАД (Saudi Aramco),
МЕНЬ-ХУНЬ ЧЕН (CPC Corporation)
Опубликовано на портале «Химическая техника», май 2019
В зависимости от владельца лицензии на рынке существует несколько архитектур, совместимых с печью Claus и влияющих на ее производительность. Каждая из них имеет свои плюсы и минусы. Вне зависимости от конструкции одним из проблемных мест все еще остается механическая стабильность.
Перед компанией Blasch была поставлена задача разработать ячеистую перегородку, которая была бы простой в установке, механически стабильной при всех возможных условиях, имела бы несколько вариантов открытой поверхности и предусматривала бы возможность установки встроенного люка-лаза. На этом этапе все вопросы сводились к механике; смешивание или управление потоком не рассматривалось. Поставленная задача состояла лишь в создании ячеистой перегородки, которая оставалась бы неповрежденной в течение всего срока службы.
Результатом решения данной задачи стала ячеистая перегородка Blasch HexWall. Блоки были рассчитаны на сухой монтаж и механическое соединение с помощью серии шипов и пазов, поэтому перегородка была стабильной, даже если ее диаметр достигал нескольких метров. Блоки соединялись без использования какого-либо раствора, что позволяло перегородке выдерживать тепловое расширение и сжатие, характерное для работающей реакционной камеры. Блоки были пригодны для повторного использования.
Первоначальная ширина блоков ячеистой перегородки составляла 9 дюймов аналогично ширине ряда кирпичей футеровки. По мере появления более крупных печей разрабатывались дополнительные варианты с блоками большей длины, в которых выдерживалось нормальное соотношение ширины стенки к ее высоте. В самых больших перегородках (> 5 м) использовались блоки шириной 18 дюймов.
Стены возводились либо в щели существующей футеровки, либо устанавливались напрямую на поверхность огнеупорного кирпича с добавлением по ряду кирпичей с каждой стороны для фиксации. Возможность взаимной фиксации блоков дает возможность непосредственного и эффективного расширения. Отверстия в блоках имеют круглую форму, поэтому каждая часть блока, которая не опирается непосредственно на другие блоки, выполнена в форме арки, что, в свою очередь, дает более высокую механическую стабильность по сравнению с прямыми отрезками. За следующие несколько лет по мере подтверждения стабильности и долговечности ячеистой перегородки некоторые операторы, которые ранее реконструировали перегородки в своих печах, стали задавать вопросы относительно того, на что же еще рассчитаны эти перегородки, помимо стабильной работы в течение всего срока службы.
Подробно посоветовавшись с лицензиарами технологических процессов, проектными организациями, конечными пользователями и различными заинтересованными лицами, мы выяснили, что практически все сходятся на том, что время (time), температура (temperature) и турбулентность потока (turbulence) — это переменные, играющие важнейшую роль для составляющих технологического процесса. Это имеет смысл, поскольку эти переменные «три T» кинетики реакции и их влияние на КПД процесса хорошо документировано.
Компания Blasch решила найти способ использования ячеистой перегородки HexWall таким образом, чтобы она оказывала влияние на эти параметры. Мы выбрали турбулентность потока с той мыслью, что если мы сможем улучшить смешиваемость веществ в печи, то это приведет к повышению КПД. Вскоре мы выяснили, что эти переменные взаимосвязаны, что привело нас к необходимости изучения таких факторов, как время нахождения веществ в реакционной камере, распределение времени нахождения веществ, а также выбор конструкции реактора — пробковый поток или перемешиваемый реактор.
Нами был разработана направляющая насадка, которая устанавливалась на выходной стороне существующих блоков таким образом, чтобы перенаправлять поток, исходящий из каждого отдельного блока в сборке, создавая требуемую конфигурацию потоков.
Изначально нами был выбран вихревой поток, поскольку мы считали, что данная конфигурация оптимально использует объем печи и создает такую картину потоков, которая дает максимальный путь движения частицы с очень плотным распределением времени нахождения веществ в камере.
Данный вариант ячеистой перегородки HexWall был назван VectorWall.
В настоящее время по всему миру работают около 24 ячеистых перегородок VectorWall, а также около 100 более ранних версий HexWall. Далее приведены два примера установки перегородки VectorWall, которые демонстрируют разницу в показателях стабильности до и после установки.
Опыт использования ячеистой перегородки VectorWall: механическая часть
Одна из перегородок VectorWall большого диаметра, изготовленных на данный момент, установлена на заводе Berri компании Saudi Aramco.
Нефтеперерабатывающий завод, установка SRU200. Данная часть статьи является выдержкой из статьи, написанной Моссаедом Аль-Аввадом, инженером по теплопередаче отдела консультационной службы (CSD) Aramco. Blasch выражает искреннюю благодарность компании Saudi Aramco за предоставленные данные.
Газовый завод Berri компании Saudi Aramco
Текущая огнеупорная система, используемая для внутренней обшивки реакционной печи извлечения серы (SRU) компании Saudi Aramco, выполнена из двух слоев огнеупорных кирпичей в качестве верхнего слоя и литого нижнего слоя со стальными анкерными болтами в качестве опоры для литого слоя огнеупора. Часть данной огнеупорной системы внутреннего пространства включает ячеистую перегородку, встраиваемую в верхний слой огнеупорного материала.
Существующая ячеистая перегородка, которая использовалась на протяжении более 20 лет, часто отказывала в силу неправильной конструкции и методов установки.
Данная статья описывает опыт использования огнеупорной системы с ячеистой перегородкой модифицированной системы и влияние последней на эксплуатацию реакционной печи.1
Описание футеровки
Нормальная рабочая температура печи в установках SRU компании Saudi Aramco составляет 1 800…2 000 °F (980…1 090 °C); тем не менее, материал верхнего слоя футеровки должен выдерживать температуры порядка 2 500…3 000 °F (1 370…1 650 °C), которые возможны при сжигании природного газа на этапе пуска. Рабочий слой футеровки всех реакционных печей установок SRU должен состоять из огнеупора с содержанием не менее 90 % окиси алюминия.
Кирпичная футеровка рабочего слоя более долговечна, чем литая часть или огнеупорная обмазка.
Первоначальная укладка кирпичей может быть несколько дороже и потребовать высококлассного специалиста, но кирпичи обычно служат дольше и менее затратны в обслуживании. Частью внутренней обшивки данной огнеупорной системы является ячеистая перегородка, изготовленная из глиноземных кирпичей, которая устойчива к высокой температуре и способна выдерживать жесткие условия.
Основная функция ячеистой перегородки
Основной функцией ячеистой перегородки является перемешивание газов путем увеличения времени нахождения веществ в результате улучшенного разрушения H2S. В дополнение к этому ячеистая перегородка работает в качестве защиты трубной решетки от теплового излучения и других эффектов технологического процесса.
Существующие традиционные ячеистые перегородки, установленные в реакторах завода Saudi Aramco, изготовлены либо из цилиндрических элементов, которые выдерживают высокие нагрузки благодаря своей форме, либо выложены из кирпичей, соединенных между собой раствором, которые обычно разрушались в результате циклических перепадов температур, разрушения раствора и вибрации.
Модифицированный процесс Клауса
Все установки SRU компании Saudi Aramco работают по модифицированному процессу Клауса, изображенному на рис. 1, где кислый газ сначала обрабатывается в скруббере кислого газа и газожидкостном сепараторе для удаления воды, жидких углеводородов и дигликольамина. Затем кислый газ нагревается до 500 °F (260 °C) в предварительном нагревателе и подается в реакторную печь, где треть газа H2S сжигается в присутствии нагретого воздуха с выделением SO2 . Полученный SO2 взаимодействует с остатком H2S в трех последовательных ступенях в присутствии катализатора, в результате чего получается сера. Каждая ступень имеет дополнительную горелку (подогреватель), конвертер и конденсатор. Жидкая сера из всех конденсаторов собирается и хранится в приямке серы, где из нее удаляются газы, а сама она подается на выход.
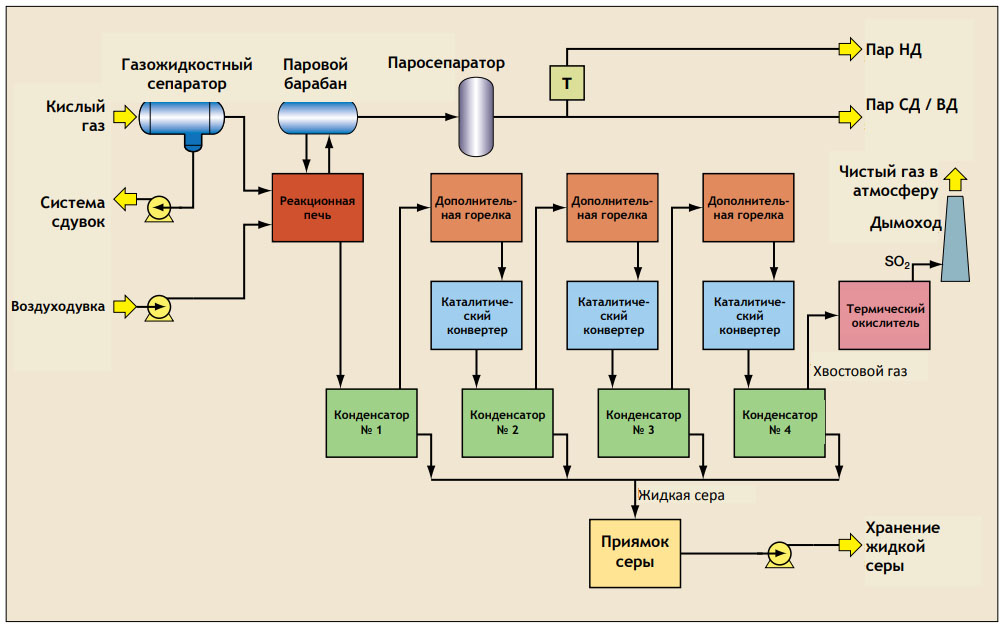
Непрореагировавший H2S и другие серусодержащие компоненты хвостового газа, выходящего из последнего конденсатора, окисляются до SO2 в тепловом окислителе.
Реакции в модифицированном процессе Клауса:
3 H2S + 3/2O2 → H2O + SO2 + 2H2S
2 H2S + SO2 → 2H2O + 3/x Sx
где x = 1, 2, 3…
В варианте модифицированного процесса Клауса, где используется рассеченный поток, треть кислого газа проходит через реакционную печь и теплообменник отвода тепла, а оставшаяся часть смешивается с газами, выходящими из теплообменника отвода тепла непосредственно перед первым конвертером.
Горячий технологический воздух поступает из воздухоподогревателя с температурой 700 °F (370 °C) и под манометрическим давлением 9 футов/кв. дюйм и встречается с потоком кислого газа у форсунки горелки. Воздух подается в количестве, достаточном для сжигания трети всего H2S кислого газа без избытка кислорода.
Количество воздуха, необходимое для сохранения соотношения H2S/SO2 в размере 2:1, поддерживается на постоянном уровне. Соотношение 2:1 для H2S/SO2 должно поддерживаться по всему объему камеры сгорания.
Если соотношение Н2S/SO2 в реакционной печи больше, чем 2:1, то содержание SO2 в газе будет постепенно снижаться по мере продвижения смеси, а H2S будет в избытке. Если соотношение H2S/SO2 в реакционной печи меньше, чем 2:1, то количество оставшегося SO2 в хвостовом газе будет больше, чем количество H2S.
Во время первичного пуска завода для прогрева реакционной печи используется топливный газ, поскольку холодный кислый газ горит плохо. При работе основной горелки на топливном газе поддерживается стехиометрический состав воздушно-газовой смеси.
Слишком высокое содержание газа или субстехиометрический состав горючей смеси приведет к отложению сажи на катализаторе, а слишком высокое содержание воздуха или надстехиометрический состав приведет к снижению температуры в слое конвертера при наличии серы из-за ее окисления.
Добавление топливного газа обычно используется для прогрева агрегата до подачи кислого газа, а также для прочистки конвертерных слоев до запланированного останова. Линии горячего технологического воздуха и кислого газа оборудованы системой вдувания пара под манометрическим давлением 75 фунтов/кв. дюйм. Пар вдувается для поддержания стабильного факела и для поддержания температуры факела ниже 2 400 °F (1 315 °C).
Результаты исследования
Существующие традиционные ячеистые перегородки, установленные в реакторах завода Saudi Aramco, изготовлены либо из цилиндрических элементов, которые выдерживают высокие нагрузки благодаря своей форме, либо выложены из кирпичей, соединенных между собой раствором. Проведенное исследование позволило выявить, что существующая ячеистая перегородка имеет явный конструктивный недостаток и требует модернизации. Основная причина отказа перегородки была обусловлена перепадами температуры в процессе пуска и останова. Перенос жидкости в камеру сгорания ослабляет кирпичную систему и приводит к ее разрушению. В дополнение к этому эксплуатация установки с превышением расчетных параметров приводит к разрушению традиционной ячеистой перегородки, так как она не способна выдержать сильную вибрацию, вызываемую расходом, превышающим расчетное значение.
На рис. 2 и 3 показаны повреждения ячеистых перегородок обоих конструкций.
В процессе дополнительного расследования было выявлено, что с учетом отсутствия сильных изменений внутреннего сгорания состава газа и внешних атмосферных условий преждевременный отказ существующей огнеупорной системы был связан с различными факторами, включая конструктивные факторы, качество кирпичей, монтажа и т. д.
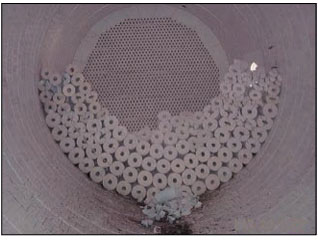
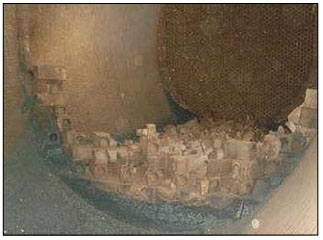
Результаты исследования и рекомендации
Компания Saudi Aramco испытывала проблемы с эксплуатацией традиционных ячеистых перегородок в связи с постоянными неисправностями, коротким сроком службы, длительным простоем на ремонт, а также высокими затратами на ремонт.
Рекомендуется использовать систему взаимозацепляющихся керамических блоков (VectorWall, см. рис. 4).
Благодаря особой конструкции модифицированная система шестигранной формы увеличивает мощность и снижает затраты
на эксплуатацию и техническое обслуживание реакционных камер средней и высокой температуры, которые, например, используются в установках Клауса для восстановления серы. Это достигается изменением пути движения реакционной смеси, что создает перемешивающийся поток в камере, тем самым оптимизируя использование доступного объема камеры.
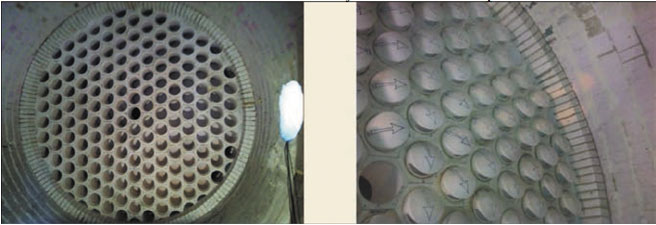
Опыт использования ячеистой перегородки VectorWall: технологическая часть
Корпорация CPC — нефтеперерабатывающий завод Таоюань
Корпорация CPC, Тайвань (CPC), — крупнейшее энергетическое предприятие Китайской Народной Республики, имеющее около 15 000 сотрудников и множество работающих установок на острове.
Будучи государственным предприятием, компания отвечает за разработку и поставку нефти и природного газа, а также является основным предприятием нефтехимической отрасли Тайваня [1]. CPC Тайвань владеет и управляет тремя НПЗ, расположенными в Гаосюне, Далине и Таоюане соответственно. Суммарная мощность этих НПЗ составляет 720 000 баррелей в день [3] Гаосюнский НПЗ, старейший из трех перечисленных заводов, является большим интегрированным нефтеперерабатывающим и нефтехимическим комплексом, включающим сложные производственные процессы и полный спектр оснащения. Его мощность составляет 220 000 баррелей сырой нефти в день.
Далинский НПЗ, отделившийся от Гаосюнского НПЗ в 1996 году, имеет четыре морские нефтедобывающие установки, а также несколько больших и малых доков для загрузки и отгрузки сырой нефти и нефтепродуктов. Максимальная мощность завода — 300 000 баррелей в день.
Таоюаньский НПЗ был основан в 1976 году и спустя несколько модернизаций и добавление второй дистилляционной установки достиг мощности 200 000 баррелей сырой нефти в день [3].
Компания CPC имеет 15 установок по восстановлению серы. Реакционная печь F6301, часть процесса Клауса по восстановлению серы, является основной частью установки по извлечению серы № 3 Таоуюаньского НПЗ. Она была разработана для переработки кислого газа от установки HDS (гидродесульфуризации) данного НПЗ. Кислый газ поступает из двух источников — установки регенерации аминов (ARU), «чистый кислый газ», содержащий в основном сероводород, и десорбера кислой воды (SWS), «грязный чистый газ» с примерно одинаковым содержанием аммиака, сероводорода и водяных паров [5].
На рис. 5 приведена технологическая схема реакционной печи F6301. Это реактор с огнеупорной футеровкой, внутренним диаметром 2,1 м и длиной около 9 м. Стандартная кирпичная ячеистая перегородка разделяла печь на две зоны.
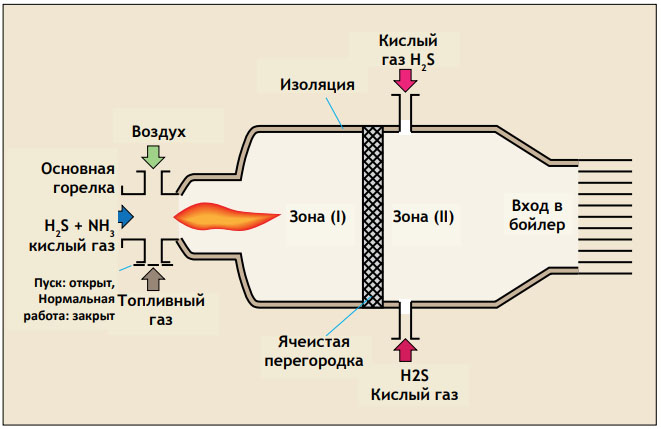
Кислый газ от HDS подавался как в горелку, так и непосредственно в поток, выходящий из ячеистой перегородки. Сероводород и аммиак кислого газа преобразовывались в элементарную серу, SO2 и N2 соответственно в печи до выхода из бойлера отвода тепла. Элементарная сера, осажденная на трубках охладителя, удалялась через выход жидкости. Остаток H2S и образованный в печи SO2. реагировали ниже по течению в каталитическом реакторе, образуя дополнительное количество элементарной серы.
Изначально печь была оснащена традиционной 9-дюймовой кирпичной ячеистой перегородкой. До модификации печь сильно вибрировала и шумела, особенно при высокой загрузке. Инженеры подозревали, что это вызывалось нестабильностью поврежденной ячеистой перегородки. Следовательно, эксплуатация печи при высокой температуре была невозможна, особенно в первой зоне.
В дополнение к этому в оборудовании на выходе печи были обнаружены отложения бисульфата/сульфата аммония, что связано с недостаточным разложением аммиака в печи.
Модернизация
В свете обозначенных выше проблем CPC в мае 2012 года приняла решение произвести реконструкцию печи. Реконструкция включала установку нового огнеупорного слоя по всей поверхности печи и замену ячеистой перегородки на перегородку VectorWall производства Blasch.
На рис. 6 приведена фотография, сделанная в процессе установки перегородки VectorWall. Она была установлена на огнеупорный слой с помощью кирпичей с высоким содержанием глинозема в качестве фундамента, залитых плотным огнеупорным раствором.
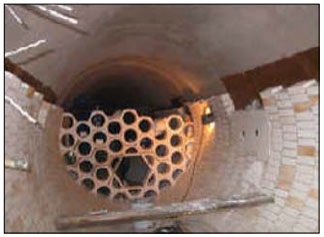
Результаты
На рис. 7 приводится сравнение температур в печи до и после реконструкции. Как видно, температура в зоне I после реконструкции увеличилась до ~1 400 °C. Тем не менее, температура в зоне II снизилась на ~200 °С — до уровня ниже 1 000 °С.
Более высокая температура в зоне I была полезна не только для конверсии серводорода, но и для распада аммиака в кислом газе.
Инженеры считают, что после реконструкции количество аммиака, окисляющегося до N2, в зоне I увеличилось, поэтому содержание аммиака в газе, поступающем в зону II для окисления, было ниже. Следовательно, температура в зоне II снизилась.
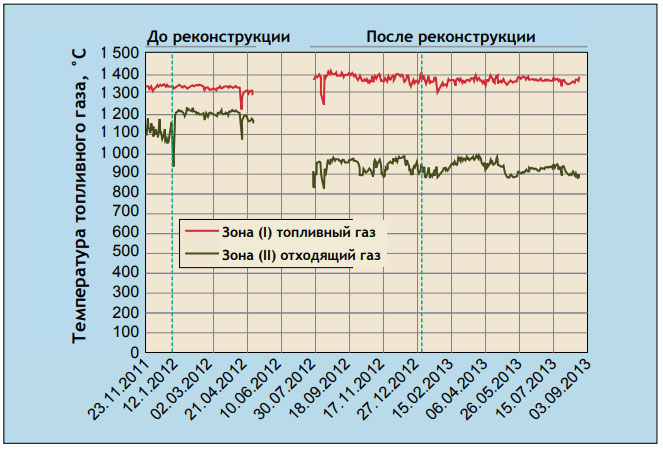
На рис. 8 приведено сравнение скорости обработки грязного кислого газа. Количество обработанного кислого газа увеличилось на ~30 % до 2000 м3/ч. В дополнение к этому вибрация печи прекратилась.
На рис. 9 приводится выработка серы. После реконструкции среднее количество вырабатываемой серы увеличилось со среднего уровня 105 т/день до 120 т/день. Это может быть связано с увеличением количества кислого газа, перерабатываемого в печи.
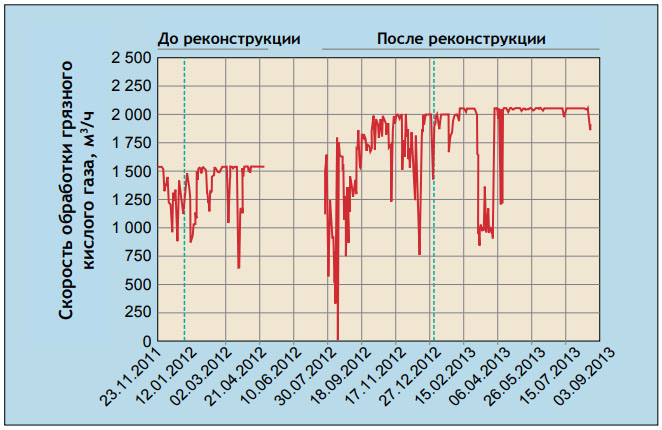
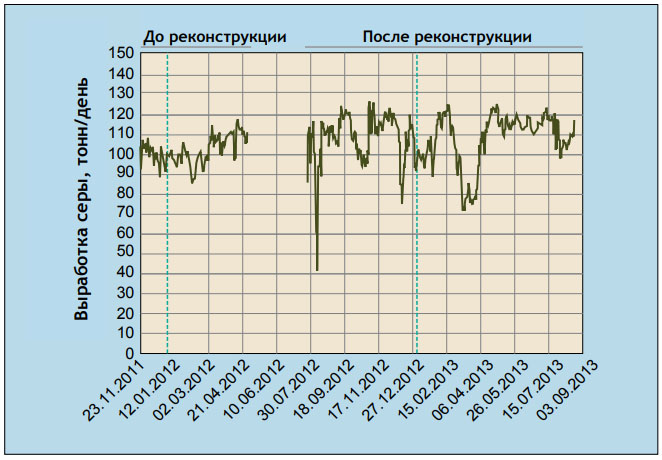
Совместное соглашение по производству серной кислоты
После того как Blasch впервые представила эту технологию, к нам обратилась компания DuPont Clean Technologies для изучения возможности применения технологии VectorWall в производстве серной кислоты с целью разработки печи более эффективной и компактной конструкции с применением данной технологии.
Компания DuPont уже использует перегородки HexWall производства Blasch на двух собственных заводах. Первая из них — на заводе по сжиганию серы в городе Ричмонд, штат Вирджиния, расположенном на реке Джеймс. Две перегородки были установлены в 2007 году. Диаметр обечайки печи составлял 10 футов. Обе перегородки имели толщину 9 дюймов.
Первая перегородка была сделана в форме ограничительного кольца, вторая — в форме стандартной ячеистой перегородки — форма, которую мы увидим снова в установках Клауса. Первая перегородка располагалась всего лишь в 8 футах и 5 дюймах от горелки, а вторая — на расстоянии 21 фут 5 дюймов.
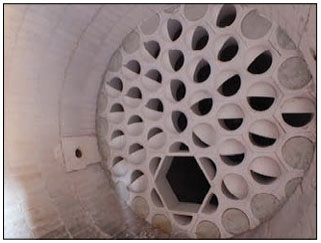
На рис. 11 показаны фотографии перегородок, сделанные во время осмотра в 2012 году, спустя около пяти лет после установки. Они все еще используются.
Кроме того, в 2007 году две перегородки HexWall были установлены в городе Эль Пасо, штат Техас, на заводе, расположенном в районе Бордерленд (рис. 12).
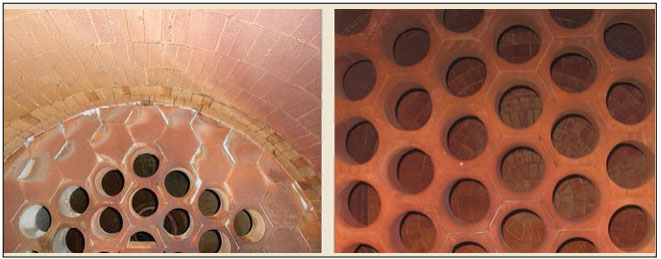
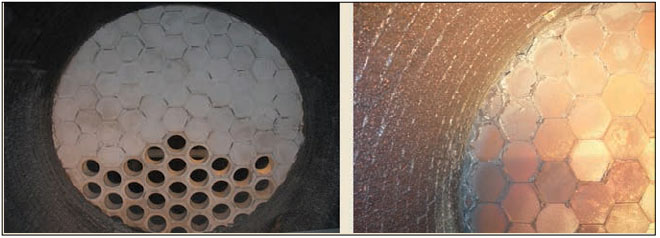
Это был завод по регенерации отработанной кислоты (SAR), и каждая печь имела три кирпичные перегородки. Первые перегородки (для подруслового потока) были заменены перегородками HexWall, поскольку в это время компания DuPont пока еще не изучала перегородку VectorWall и ее возможности.
Механическая стабильность первой (подрусловой) перегородки в печи разложения очень часто является проблемой, поэтому в случае изготовления из кирпича они проектируются на толщину 18 дюймов. Эти печи имели скромный диаметр 12 футов, а ширина используемых перегородок HexWall была всего лишь 9 дюймов, и располагались они на расстоянии 17 футов от горелки.
Совсем недавно для печи LA SAR на новом заводе в Бернсайде компанией Blasch были изготовлены все три новые перегородки в формате HexWall. Эта печь — самая большая из изготовленных для DuPont, ее размер составлял почти 19,5 фута. Первая перегородка была шириной 18 дюймов, остальные две — по 13,5 дюймов.
С этого момента Blasch начала отливать заглушки для блоков отдельно, а не целым блоком, что было удачным решением для больших перегородок с конструктивной точки зрения.
На момент этой установки DuPont еще не устанавливала готовую перегородку VectorWall в печи, но после долгого моделирования в Вилмингтоне, штат Делавэр, разработала конструкцию, которая сегодня продвигается на рынке.
Интересно, что установка SAR завода в Бордерленде столкнулась с проблемой образования оксидов азота (NOx). В 2012 было разработано проприетарное решение на основе VectorWall, которое было установлено в оба каскада так, чтобы они работали вместе с существующими перегородками, что решило эту проблему.
Конфигурация печи и производительность перегородки VectorWall
Итак, какие выводы мы сделали из этого? Очень сложно подобрать оборудование и программы, способные создать реалистичную, точную, учитывающую множество физических факторов (теплота, масса, расход и кинетика потока) модель реактора, а также специалистов, способных ее создать, запустить и проанализировать результаты.
Blasch определенно смогла выделить для себя несколько тенденций из этих установок и продолжает относительно простое моделирование холодным потоком, использованное в процессе разработки VectorWall с некоторыми доработками.
Простейшая конфигурация печи — это прямоточная печь (рис. 13). Оба реагента поступают в печь одновременно и реагируют аналогично. Максимальная эффективность в данном случае достигается путем создания такого потока, который дает самое плотное распределение времени нахождения веществ вокруг оптимального значения для данного конкретного процесса.
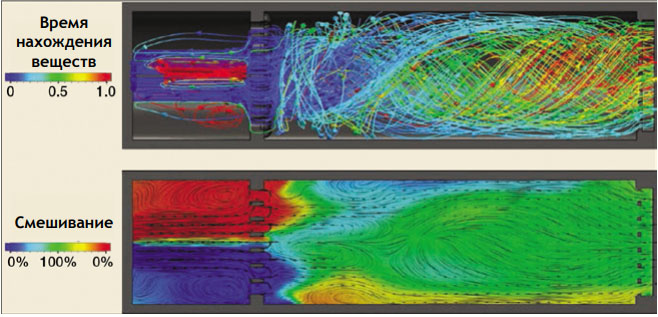
Эта конфигурация работает эффективно при пробковом режиме потока, и при постоянном времени пребывания с длинной спиральной траекторией движения частиц она наиболее эффективна, если учесть, что моделируемая печь имеет достаточную длину для моделируемого процесса.
К сожалению, реальные условия расходятся с такой моделью. В реальности очень часто приходится иметь дело с гораздо более сложными взаимодействиями, и оптимальным решением здесь чаще всего будет компромисс.
В случае с процессом Клауса приходится иметь дело с поглотительным газом кислой воды, содержащим аммиак, и если его не разложить как можно раньше и быстрее, то он создаст много проблем на выходе.
В данном случае предпочтительнее всего создать несколько зон со своими характеристиками. Например, в случае с SWS необходимо создать более высокие температуры в зоне 1 для ускорения разложения аммиака, а также обеспечить хорошее перемешивание частично прореагировавших газов с кислым газом в этой зоне.
В зоне 2 предпочтительны более низкие температуры для предотвращения образования NOx, а также возврат к более тесному распределению времени пребывания веществ рядом с оптимальным значением.
В случае ограничительного кольца, как показано на рисунке, часть потока отражается обратно, что создает перемешивание обратных потоков с прямыми, но значительная часть потока все же проходит через центр кольца. Вброс остатков кислого газа в поток в этой точке (или даже ближе к трубной решетке) создает серьезную проблему регулировки времени пребывания веществ в реакционной зоне. Многие также используют традиционную ячеистую решетку перед трубной решеткой для ее защиты от столкновения с сильным потоком.
Перегородка VectorWall, по описанным выше причинам, дает смешивание обратных потоков с прямыми, но поток, идущий через центр, затем закручивается, что дает хорошее перемешивание и удлиняет путь частиц, а также переводит поток в пробковый режим и предотвращает формирование точек высокой температуры на трубной решетке (рис. 14).
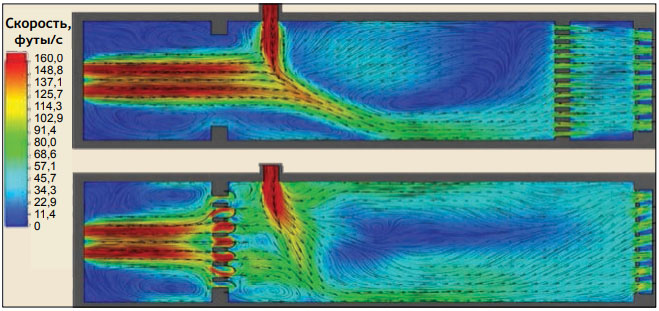
Направляющие ячейки (Vector Tiles) также отражают тепловое излучение обратно в зону 1.
С результатами можно ознакомиться в разделе данных, предоставленных компанией CPC.
С точки зрения времени пребывания веществ в реакционной зоне VectorWall и получающееся в результате этого завихрение переводят поток в пробковый режим быстрее, чем ограничительное кольцо, что, как видимо, дает возможность части потока, вдуваемой за ограничительным кольцом, выйти за пределы печи гораздо раньше заявленного минимального времени пребывания (рис. 15). Заявлено, что сильное улучшение характеристик, наблюдаемое на практике, связано с более тесным распределением времени пребывания и склонности перегородки сводить количество непрореагировавшего вещества, выходящего из печи, к минимуму.
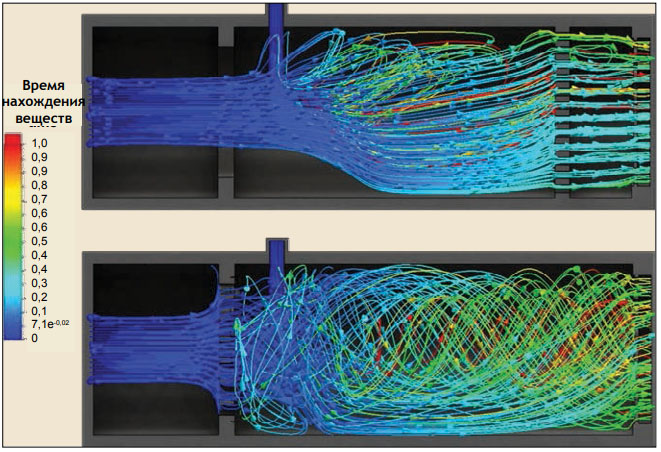
В настоящее время компания Blasch все еще работает с сильно упрощенным моделированием холодного потока и никак не учитывает конкретные конфигурации горелок, температурные эффекты и кинетику реакции.
Практически полученные данные продолжают свидетельствовать об эффективности этого упрощенного моделирования, а мы продолжаем поиск сотрудничества с лицензиарами, с компаниями, производящими горелки, и с университетами.
Наша задача состоит в том, чтобы наиболее подробно изучить влияние перегородки VectorWall на стадию сжигания в процессе Клауса с тем, чтобы помочь операторам воспользоваться теми преимуществами, которые дает данная технология, а также определить другие процессы, основанные на сжигании, которым перегородка VectorWall была бы полезной.
Список литературы
- Моссаед И Аль-Аввад, инженер-теплотехник, Saudi Aramco, Королевство Саудовская Аравия.
- www.cpc.com.tw/english/content/index. asp?pno=24.
- cpc.com.tw/english/content/ index01.asp?sno=715&pno=64.
- cpc.com.tw/english/content/ index01.asp?sno=715&pno=64.
- Мень-Хунь Чен, проектный менеджер, корпорация CPC, Тайвань.
- Schmidt L D, The Engineering of Chemical Reactions, 1998, New York: Oxford University Press
Джеффри Боулбрух — главный менеджер по рынку, Blasch Precision Ceramics, ответственный за продажи на химическом / нефтехимическом рынках. Имеет степень бакалавра технических наук Военной Академии США, город Вест Пойнт, а также магистра делового администрирования Колледжа Марист, Поукипзи, штат Нью-Йорк.
Мень-Хунь Чен — руководитель технической службы исследовательского центра нефтепереработки и производства корпорации CPC. Он специализируется на проектировании и анализе технологических нагревателей, имеет степень магистра кораблестроения Национального тайваньского университета.