Автор: Т.Д. Алеференко, А.Г. Александров, Е.А. Садовский (НПО «ЛЕНКОР-НЕФТЕХИМ»); А.Г. Аненко, А.В. Приходько, Ю.А. Иващенко («ОЗСМ» – филиал ООО «Газпромнефть-СМ»).
Опубликовано в журнале Химическая техника №3/2016
Низколегированная кремний-марганцовистая сталь 09Г2С широко используется для изготовления сосудов и аппаратов в нефтехимии и нефтепереработке. В настоящее время в эксплуатации находится значительное количество технических устройств из этой стали, изготовленных в 60-х–70-х годах прошлого века, для которых время эксплуатации составляет 300…400 и более тысяч часов.
Действовавшие в то время технические условия, например ТУ 157–59, не предусматривали контроль металла методами металлографии или УЗК и не нормировали наличие неметаллических включений. При проведении технического диагностирования такого оборудования методами УЗК обнаруживаются точечные (типа неметаллических включений) и протяженные (типа расслоений) дефекты, в некоторых случаях не допустимые по ныне действующим нормативным требованиям.
При проведении диагностического обследования пропановой колонны К-1 установки 36/1-1, отработавшей на момент проведения исследований более 400 000 ч (введена в эксплуатацию в 1965 г.), методом УЗК (производился дефектоскопом УД2В-П46, прямыми совмещенными и раздельно-совмещенными пьезоэлектрическими преобразователями с частотами 2 и 4 МГц) было обнаружено значительное количество дефектов типа неметаллических включений, на отдельных обечайках объединенных в зоны площадью Sусл > 100 см2, что, согласно ГОСТ 22727–88, недопустимо. В то же время внутри этих зон донный сигнал всегда присутствовал, судя по характеру изменения сигнала дефектоскопа при движении датчика по поверхности металла, дефекты хаотически распределены по глубине и площади. Неразрушающими методами контроля получить дополнительную информацию о степени ослабления конструкции фиксируемыми дефектами и об их физико-химической природе не представлялось возможным. В связи с этим из стенки колонны был вырезан темплет диаметром около 100 мм и проведены испытания механических свойств стали 09Г2С с зафиксированными УЗК неметаллическими включениями и металлографические исследования соответствующих шлифов с целью определения возможности дальнейшей эксплуатации колонны. Диаметр колонны составлял 2800 мм, толщина стенки 63 мм, рабочее давление 4,2 МПа, рабочая температура 85 °С.
Вырезанный темплет был разрезан на слои толщиной 12…15 мм параллельно наружной поверхности аппарата.
Из каждого слоя были изготовлены по два образца для испытаний на ударный изгиб по ГОСТ 9454–78 (вид концентратора U, тип 1) и по три образца на испытания на разрыв по ГОСТ 1497–84 с учетом ГОСТ 10145–81 (тип IV, образец №6).
Испытания на разрыв проводили на испытательной машине Р-5, испытания на ударную вязкость – на копре МК-30. При проведении металлографических исследований фрагментов металла использовали световой металлографический микроскоп «Обсервер» и микротвердомер «Аффри» с пирамидой HV.
При проведении металлографических исследований установлено следующее.
В образцах из всех слоев темплета (образцы пронумерованы от внутренней поверхности к наружной) зафиксирована морфологически одинаковая структура металла, которая представляет собой мелкозернистый феррит (8…9 баллов по шкалам ГОСТ 5639) и структурно-свободный цементит в форме мелких (1…3 мкм) частиц, расположенных на границах зерен (рис. 1).
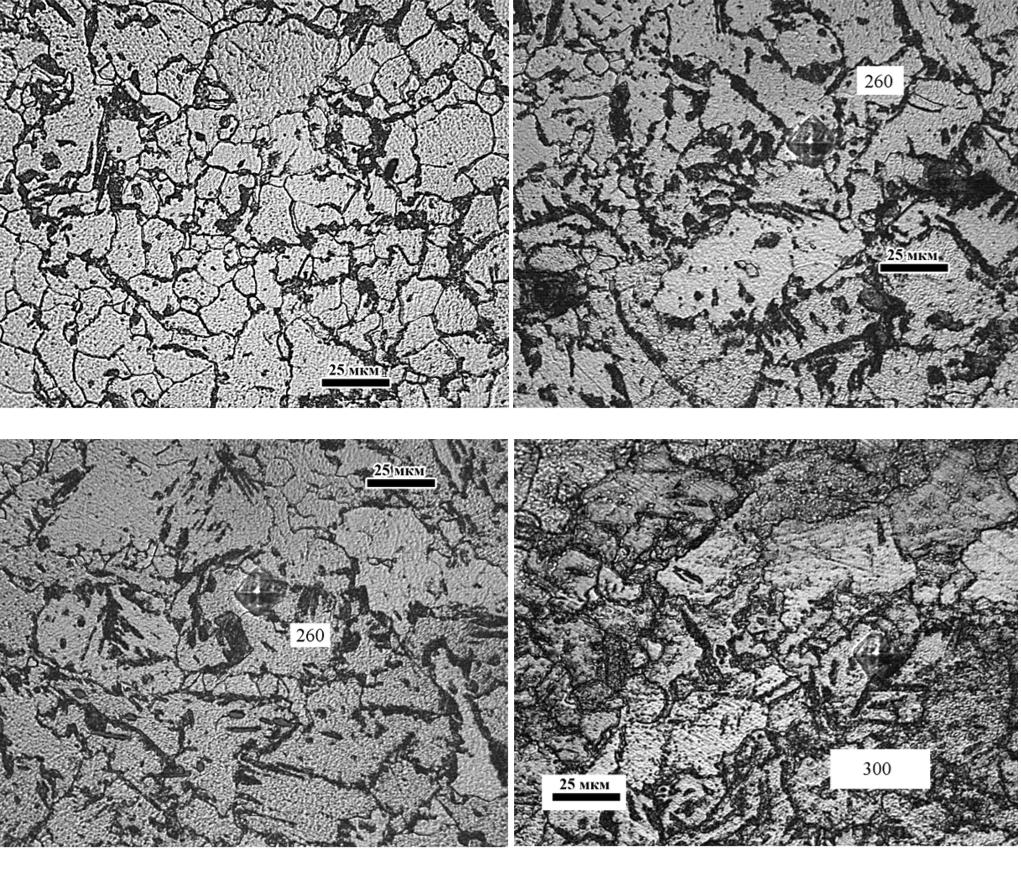
По виду зерен и микротвердости матрицы (260±20 кгс/мм2), которая вычислена по размерам отпечатков призмы HV после индентирования нагрузкой 50 г, металл соответствует малоуглеродистой стали с содержанием углерода до 0,2%. В местах, где индентор микротвердомера попал в объем, расположенный у границы зерна, микротвердость определена в 290±10 кгс/мм2. Полученные данные типичны для малоуглеродистых сталей феррито-перлитного класса. Отсутствие перлитной составляющей в стали не противоречит требованиям ТУ 157–59, по которым она была изготовлена.
Установлено, что в металле содержатся неравномерно распределенные неметаллические включения (рис. 2).
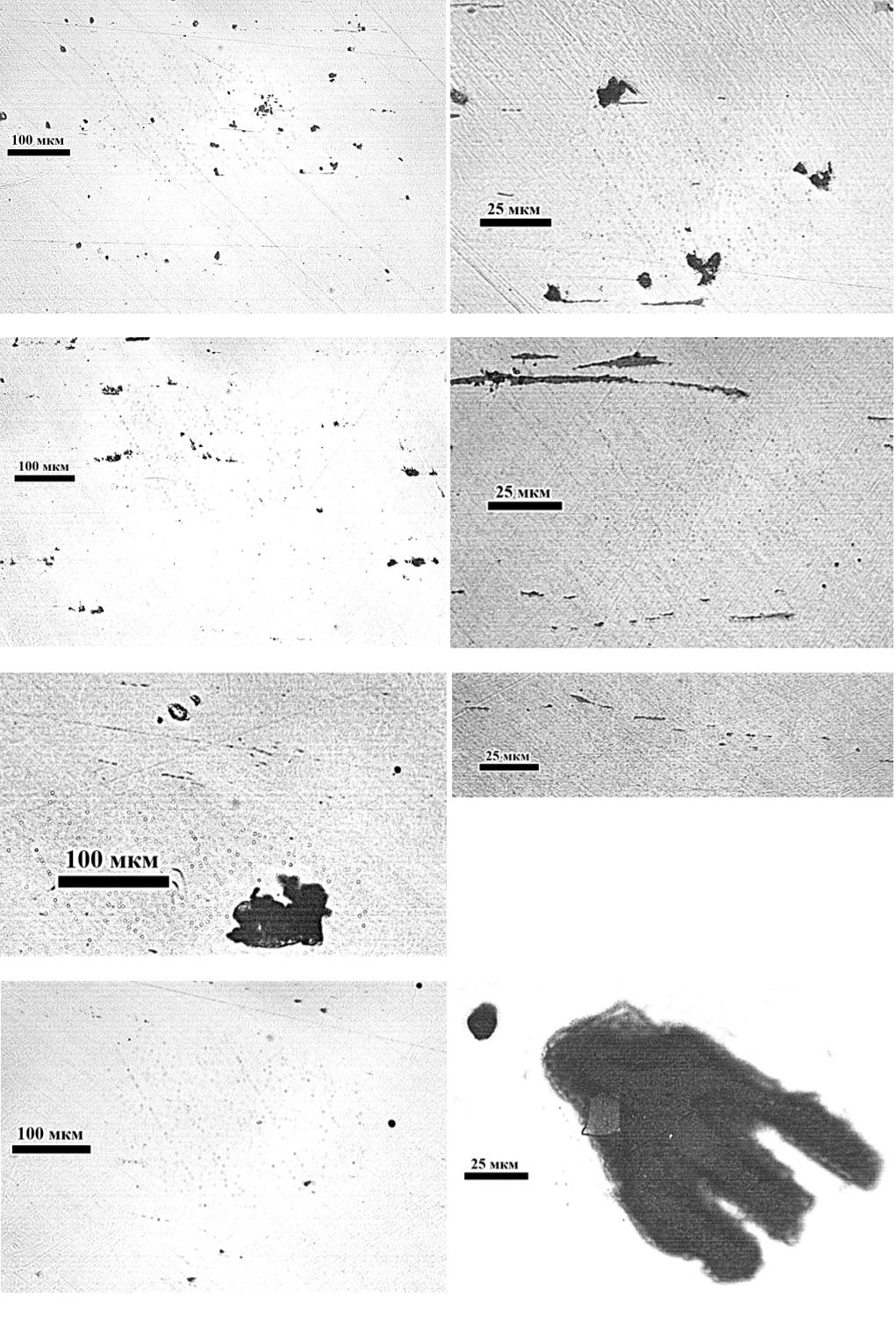
При этом зафиксированы участки размером до 1×2 мм, где присутствуют крупные (до 100 мкм) включения. По шкалам ГОСТ 1778 металлургическое качество металла отвечает следующим оценкам:
- в пробах №1 и №2 содержатся преимущественно оксиды (3 балла) и сульфиды (2 балла);
- в пробе №3 обнаружены редкие крупные оксиды (4 балла) и сульфиды (3 балла);
- в пробе №4 доминируют оксиды (5 балла) и недеформируемые силикаты размером до 20 мкм, окруженные в ряде случаев сульфидной оболочкой.
Приведенные оценки свидетельствуют о невысоком металлургическом качестве металла. Микротрещины или другие опасные дефекты эксплуатационной природы не обнаружены.
Результаты исследования механических свойств металла приведены в табл. 1 и 2.
Таблица 1
Результаты испытаний на статическое растяжение по ГОСТ 1497–84
Номер слоя |
Предел текучести
s0,2, Н/мм2 |
Временное сопротив- ление sв, Н/мм2 | Относи- тельное удлинение
d, % |
Относи- тельное сужение
y,% |
1 | 236 | 499 | 29,0 | 73,0 |
1 | 252 | 494 | 31,0 | 73,0 |
1 | 256 | 501 | 33,7 | 74,5 |
2 | 280 | 506 | 32,7 | 65,5 |
2 | 292 | 505 | 34,7 | 64,0 |
2 | 275 | 501 | 30,0 | 67,5 |
3 | 275 | 505 | 30,3 | 64,0 |
3 | 277 | 508 | 35,0 | 64,0 |
3 | 278 | 510 | 30,0 | 65,5 |
4 | 274 | 495 | 35,0 | 65,0 |
4 | 296 | 494 | 30,0 | 66,0 |
4 | 294 | 494 | 30,3 | 65,5 |
Разброс значений | 60 (20%) | 16 (3%) | 6 | |
Требования по ГОСТ 5520–79 | >275 | 440…640 | >22 | |
Примечания. 1. Температура испытания 20 °С.
2. Номер слоя 1 соответствует внутренней поверхности стенки колонны, номер 4 – наружной поверхности. |
Полученные значения механических свойств образцов в основном соответствуют требованиям нормативных документов. Однако для нескольких образцов (4 из 12) σ0,2 меньше нормативного минимального значения 275 Н/мм2 (236, 252, 256 и 274 Н/мм2). В то же время среднее измеренное значение превышает установленный ГОСТ 5520–79 минимальный уровень.
Таблица 2
Результаты испытаний на ударный изгиб
Номер слоя |
Глубина концент- ратора h, см | Высота рабочего сечения Н1, см | Площадь попе- речного сечения S0, см2 | Работа удара К, Дж (кгс×м) | Ударная вязкость КС,
Дж/см2 (кгс×м/см2) |
1 | 0,2 | 0,8 | 0,8 | 55 (5,6) | 69 (7,0) |
1 | 0,2 | 0,8 | 0,8 | 54 (5,5) | 68 (6,9) |
2 | 0,2 | 0,8 | 0,8 | 67 (6,8) | 83 (8,5) |
2 | 0,2 | 0,8 | 0,8 | 105 (10,7) | 132 (13,4) |
3 | 0,2 | 0,8 | 0,8 | 100 (10,2) | 125 (12,8) |
3 | 0,2 | 0,8 | 0,8 | 71 (7,2) | 88 (9,0) |
4 | 0,2 | 0,8 | 0,8 | 80 (8,2) | 101 (10,3) |
4 | 0,2 | 0,8 | 0,8 | 82 (8,4) | 103 (10,5) |
Разброс значений | 64 (48 %) | ||||
Требования по ГОСТ 5520–79, Дж/см2 | ³ 60 | ||||
Условия испытаний: температура испытания 12 °С; максимальная энергия удара маятника при испытании 300 Дж; скорость маятника в момент удара 5±0,5 м/с; ширина образца 10 мм, высота образца 10 мм. |
Обращает на себя внимание большой разброс полученных значений предела текучести и ударной вязкости (соответственно 20 и 48%) при относительно малом разбросе значений временного сопротивления (3%).
Это соответствует существующим представлениям о том, что рост концентрации мелких неметаллических включений должен приводить к падению пластичности и прочности металла. Неравномерность распределения неметаллических включений обусловливает полученный разброс механических свойств.
На основании минимальных измеренных значений σ0,2 произведена оценка допускаемого напряжения и рассчитана отбраковочная толщина стенки колонны.
Полученное значение значительно меньше фактической толщины, что свидетельствует о достаточном запасе по прочности обследованной колонны.
На основании изложенного можно заключить, что невысокое металлургическое качество исследованного металла (наличие неметаллических включений металлургического происхождение вплоть до 5 балла по ГОСТ 1778–70) сопровождается некоторым ослаблением металла обследованной колонны, что количественно отражается в измеренных значениях σ0,2, но не препятствует дальнейшей эксплуатации оборудования, что подтверждается результатами поверочного прочностного расчета.
Авторы выражают благодарность Центру коллективного пользования при ФГУП ЦНИИ КМ «Прометей» за помощь в проведении исследований.