Авторы: В.М. Давыдов, С.Д. Рязанов, Л.С. Алексенцева (ООО НПП «Механик»), Р.В. Жуков (ООО НУЦ «Качество»).
Опубликовано в журнале Химическая техника №4/2015
Компрессорные агрегаты аммиачно-холодильных установок, а также небольшие воздушные компрессоры обычно по линии нагнетания связаны со вспомогательными сосудами (маслоотделители, конденсаторы или ресиверы – обычные цилиндрические сосуды с эллиптическими днищами).
Можно выделить три основных варианта компоновки рассматриваемых установок. Наиболее мощные содержат отдельно стоящие сосуды и компрессоры. В установках меньшей мощности компрессор может быть установлен на высокой раме, внутри которой размещены вспомогательные сосуды. Существуют компоновки аммиачных и воздушных компрессорных агрегатов, в которых корпус ресивера (конденсатора, маслоотделителя) используется в качестве опорной рамы собственно компрессора и двигателя. В двух последних случаях некоторые предприятия, поставляющие, а также эксплуатирующие компрессорные агрегаты, относят емкость к составной части компрессорного агрегата и считают, что действие правил на нее не распространяется.
Такое мнение является глубоким заблуждением.
Во-первых, сосуд, входящий в состав агрегата, по своей конструкции не является частью компрессора, т.е. оба технических устройства могут существовать отдельно, выполняя свои функции. Во-вторых, сосуд по своему назначению и параметрам работы является объектом повышенной опасности как накопитель энергии сжатого газа. В-третьих, кроме всех требований, которые предъявляются «Правилами» к сосудам, работающим под давлением, в данном случае из-за условий работы сосуда необходимы дополнительные требования. Установка механизма с вращающимися инерционными массами на обечайке приводит к появлению в ней циклических напряжений, вызванных вибрацией компрессора и двигателя. При износе или отказе механизма движения компрессора вибрационное воздействие в зоне его крепления значительно увеличивается. В ряде случаев в корпусах маслоотделителей (конденсаторов) наблюдались усталостные трещины, развивающиеся от сварных швов в местах крепления компрессора.
Опыт обследования компрессоров, смонтированных на емкостном оборудовании, показывает, что при техническом диагностировании необходимо руководствоваться программой (методикой), в которой должны быть учтены все особенности работы агрегата. Необходим дополнительный контроль обечайки в местах приварки опор компрессора и двигателя, а также систематический контроль вибрационного состояния компрессора. Кроме того, в тех случаях, когда произведение объема сосуда на его рабочее давление соответствует параметрам, при которых на сосуд распространяются ФНП «Правила промышленной безопасности опасных производственных объектов, на которых используется оборудование, работающее под избыточным давлением» [1], завод-изготовитель должен составлять и прикладывать паспорт установленной формы на сосуд, работающий под давлением. На такой сосуд должны распространяться требования по периодическим освидетельствованиям и другие требования «Правил».
Затронутая проблема трагически проявилась во время аварии на передвижной компрессорной воздушной установке УКП-1/10 в ЗАО «Новомосковский мелькомбинат» в 2008 г.
Установка состояла из двухступенчатого компрессора с электродвигателем мощностью 8 кВт, смонтированного на воздушном ресивере объемом 0,250 м3 и давлением 0,8 МПа.
Совокупность рабочих параметров ресивера распространяла на него правила ПБ 03-576–03. Однако завод-изготовитель составил паспорт на установку в целом. Паспорт на ресивер, как на сосуд, работающий, под давлением, отсутствовал, не было и разрешения на применение агрегата. Соответственно на предприятии, эксплуатирующем установку, не проводили очередные освидетельствования сосуда, отсутствовал журнал проверки исправности действия предохранительных клапанов и, как оказалось, сами проверки клапанов также не проводили. Реле давления из-за его неисправности было отключено. Вентиль на штуцере выхода воздуха из ресивера в момент пуска компрессора был закрыт, давление и температура превысили допустимые значения, реле давления не сработало, предохранительные клапаны не открылись, и произошел взрыв масловоздушной смеси с разрушением ресивера (рис. 1).
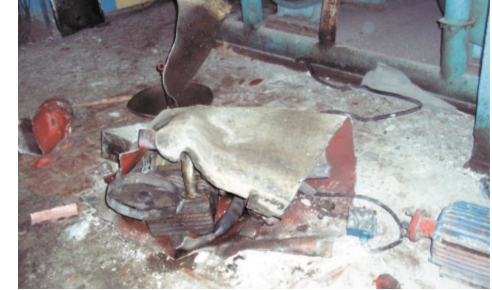
Комиссия, созданная для установления причин аварии, в процессе обследования сделала следующие выводы. Поверхности изломов имели мелкозернистую структуру, исследования не выявили в швах недопустимых дефектов. Отсутствие на краях изломов пластически деформированного металла однозначно говорит о хрупком характере разрушения при мгновенном приложении нагрузки. Приводной конец коленчатого вал компрессора обломился в месте галтельного сопряжения. Макроскопическое исследование срезанного участка вала показало, что он имеет структуру, характерную для хрупкого разрушения. В клапанной коробке со стороны первой ступени, а также на внутренней поверхности трубопровода нагнетания первой ступени наблюдалось большое количество нагара масла. Лакокрасочное покрытие всех трубопроводов обгорело, что свидетельствует о воздействии высокой температуры. Обратный клапан, установленный на трубопроводе нагнетания второй ступени, разрушился.
Предохранительные клапаны первой и второй ступеней в месте резьбового крепления сорваны с бобышек.
Практика эксплуатации воздушных компрессоров показывает, что при длительной эксплуатации появляется опасность воспламенения и взрыва накапливающегося в цилиндре и нагнетательных трубопроводах нагара масла [2]. Это возможно при условии повышения температуры нагнетания относительно паспортных значений. В данном случае это могло возникнуть при работе установки с практически закрытым вентилем на выходе воздуха из ресивера. Термодинамический расчет компрессора показал, что температура нагнетания, при которой возможно самовоспламенение нагара масла (190°С), возникнет в цилиндре первой ступени компрессора при конечном давлении 1,4 МПа. При этом электродвигатель обладал достаточной мощностью для того, чтобы компрессор создавал такое давление.
Расчет температурных напряжений в обечайке ресивера при давлении 1,4 МПа и фактической толщине стенки и анализ снижения механических свойств металла при его нагреве до 200°С показал, что прочность сосуда обеспечивается. При давлении 1,4 МПа без воздействия иных факторов ресивер не мог разрушиться, так как предел текучести в обечайке сосуда достигается при давлении не менее 2,6 МПа.
Таким образом, можно сделать вывод, что разрушение ресивера воздуха произошло по причине самовоспламенения нагара масла в цилиндре или трубопроводе первой ступени компрессора и последующего взрыва масляного тумана в ресивере.
Следует отметить, что при обследованиях подобных машин достаточно часто наблюдается повышенная вибрация, которая через опоры непосредственно передается на сосуд, работающий под давлением. Большие инерционные силы, а также низкая жесткость системы компрессор– обечайка приводят к циклическим деформациям сосуда в области приварки опор и способствуют возникновению в этих местах усталостных трещин. Низкая культура обслуживания на ряде предприятий, связанная с эксплуатацией компрессорных установок при повышенном уровне вибрации, способствует созданию аварийных ситуаций. Так, при проведении экспертизы промышленной безопасности в ОАО ПКП «Меридиан» была обнаружена усталостная трещина на обечайке сепаратора в месте приварки опоры рамы винтового компрессора. После проведенного ремонта и положительных результатов неразрушающего контроля сосуд был допущен к дальнейшей эксплуатации.
В аммиачно-холодильном цехе продовольственной базы (г. Красногорск) находятся в эксплуатации поршневые компрессоры, также смонтированные на сепараторах. Уровень вибрации таких машинных агрегатов (даже при удовлетворительном техническом состоянии) достаточно высок по сравнению с уровнем вибрации винтовых агрегатов. Из-за несвоевременного проведения ремонтных работ эксплуатация этих агрегатов с повышенным уровнем вибрации приводит к образованию трещин на сосудах в зонах приварки опор под компрессором (рис. 2).
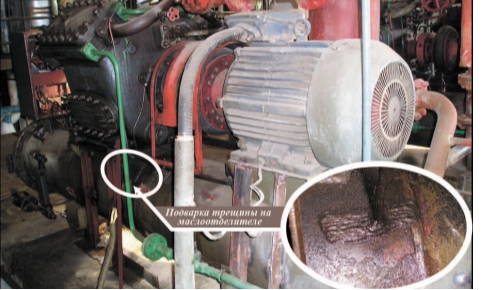
Следует также отметить, что вследствие низкой жесткости системы компрессор–обечайка, как уже указывалось, нагрузка на подшипники двигателя и компрессора со стороны муфты многократно возрастает, что приводит к ускорению их изнашивания и более быстрому выходу их из строя.
Практика взаимоотношений экспертных организаций с владельцами агрегатов показывает, что зачастую последние заказывают экспертизу собственно компрессора, отказываясь оплачивать работы по техническому диагностированию сопутствующего сосуда и составлению паспорта.
По нашему мнению, предприятия, поставляющие подобное оборудование, должны обязательно составлять паспорт установленного образца на сосуд. Кроме того, необходимо внести в инструкцию по эксплуатации и техническому обслуживанию требования по обслуживанию и освидетельствованию сосуда. В объем такого освидетельствования должен быть включен неразрушающий контроль мест крепления компрессора к сосуду, а также виброконтроль агрегата. В инструкции должны быть приведены нормы вибрации с указанием предельно допустимого уровня.
Назначение предельных значений параметров вибрации необходимо увязывать с усталостными процессами не только в узлах компрессора, но и с характером циклических напряжений в обечайке сосуда, под опорами компрессорного агрегата.
При этом должны учитываться конструктивные особенности компрессора и сосуда.
Список литературы
- ФНП «Правила промышленной безопасности опасных производственных объектов, на которых используется оборудование, работающее под избыточным давлением».
- Тихомиров А.А. Обеспечение безопасности при эксплуатации оборудования компрессорных станций с воздушными поршневыми компрессорами//Безопасность труда в промышленности. 2003. №6.