КАО «Азот» – одно из крупнейших российских предприятий по производству минеральных удобрений. Завод предприятия находится в г. Кемерово и обладает мощностями для производства более 1,2 млн тонн аммиака, 1,3 млн тонн аммиачной селитры, 1 млн тонн азотной кислоты, 600 тысяч тонн карбамида, 300 тысяч тонн сульфата аммония, 135 тысяч тонн капролактама и 146 тысяч тонн карбамидно-аммиачной смеси в год.
Современные рыночные реалии предполагают увеличение выработки, повышение рентабельности и сокращение издержек производства. Поэтому КАО «Азот» инвестирует в развитие предприятия, внедряет новые технологии и подходы для того, чтобы сделать его более эффективным и конкурентоспособным.
Развитие современного крупнотоннажного технологического производства является сложной технической задачей. От того, насколько точно предприятие сможет определить наиболее сдерживающие участки и выбрать мероприятия по их модернизации, зависит окупаемость инвестиций и дальнейшее развитие бизнеса. Руководство КАО «Азот» понимает, что поиск технологических ограничений, сокращающих эффективность производства и анализ последствий от замены или реконструкции оборудования, не может основываться только на экспертных знаниях производственного персонала, производственных экспериментах или технических предложениях сторонних организаций. Предприятию необходимо иметь собственный объективный источник информации о технологических процессах «как есть» и «как будет». При этом он должен быть точным, чтобы оценить влияние любого изменения на работу системы и минимизировать риск принятия неверного решения. Этот источник – подробная математическая модель технологических процессов предприятия. Она воспроизводит превращения всех материальных потоков в цеху, показывает ограничения и позволяет провести виртуальные испытания новых технических решений.
Для того, чтобы создать такую модель для цеха по производству аммиачной селитры, специалисты КАО «Азот» обратились к экспертам компании «Моделирование и цифровые двойники» (АО «МЦД»).
Математическое моделирование для решения вопросов производства
Математическое моделирование (CAE, Computer-Aided Engineering) является хорошо известной технологией, позволяющей эффективно разрабатывать новую продукцию. Возможность провести всесторонние виртуальные испытания до физического создания прототипа сокращает продолжительность разработки и повышает качество изделия.
Благодаря развитию программ математического моделирования сегодня их используют значительно шире, например, для оптимизации работы действующих предприятий.
Основная особенность таких задач в том, что модель должна точно соответствовать работающему производству. Если соответствия не будет, ее расчетам нельзя доверять.
Это требование создает определенные сложности для разработчика – нужно учитывать большое многообразие процессов, при этом точных данных о том, как они протекают в оборудовании, часто бывает недостаточно. Поэтому создать качественную модель нельзя без участия самого производства, а также людей, которые за него отвечают на предприятии.
Важно и то, что конечное решение должно быть отчуждаемым от разработчика. То есть, модель должна, работая в контуре КАО «Азот», помогать специалистам предприятия оперативно решать текущие производственные задачи, надолго сохраняя актуальность и работоспособность.
Экспертам АО «МЦД» было необходимо разработать модель цеха крупнотоннажного производства селитры, введенного в эксплуатацию в 80-е годы прошлого века и прошедшего множество изменений. Цех работает на максимальной проектной мощности, перевыполняя план производства. Но производственная повестка требует дальнейшего планомерного роста выработки. При этом очевидно, что большое количество оборудования, являясь устаревшим, может сдерживать рост производительности и ограничивать производство. Учитывая долгую историю работы цеха и его многочисленные изменения, нелегко предсказать, как модернизация оборудования повлияет на выработку, сохранится ли устойчивость работы технологических агрегатов. Важно и то, насколько быстро окупятся затраты на модернизацию, хотя она не является единственной задачей цифрового двойника. Он дает долгосрочный эффект, помогая решать проблемы и выбирать эффективные рационализаторские предложения персонала.
«При работе технологического оборудования могут возникать различные нежелательные явления, которые плохо влияют на выработку. Однако проблемы появляются нерегулярно, а воздействующих факторов много. Поэтому разобраться и устранить их причины бывает очень сложно. Проблему позволяет решить технологическое моделирование. Оно дает возможность избежать лишнего риска и потерь для производства. С этой ключевой идеей мы и начали работу с КАО «Азот», который реализует современные подходы в развитии производственной системы в соответствии с принципами бережливого производства», – комментирует Андрей Крылов, директор центра цифровых технологий АО «МЦД».
Сбор исходных данных и подготовка к проекту
Специалисты КАО «Азот» проделали сложную работу в рамках подготовки к созданию цифровой модели. Они собрали большой массив исходных данных, касающийся работы всех элементов технологического комплекса по производству аммиачной селитры. Среди них – ретроспективные данные по аналитическому контролю, исходные данные о конструктивных характеристиках, технологические регламенты цеха и технологические схемы цеха.
«Исходные технологические данные играют важную роль для математического моделирования. При этом объективных и точных данных на действующих производствах сравнительно мало для выполнения аналитических задач. За годы своей работы специалисты АО «МЦД» наработали определенные подходы для решения этой проблемы, включая обратное проектирование, методы машинного обучения и многое другое. Однако полностью решить ее в одиночку нельзя, поэтому активная позиция производства по поиску и сбору исходных данных является ключевым фактором успеха», – рассказывает Андрей Крылов.
Обследование предприятия и разработка цифровой модели
Работа экспертов АО «МЦД» началась с технического обследования – проверки фактической конфигурации производства на соответствие собранным данным и документации.
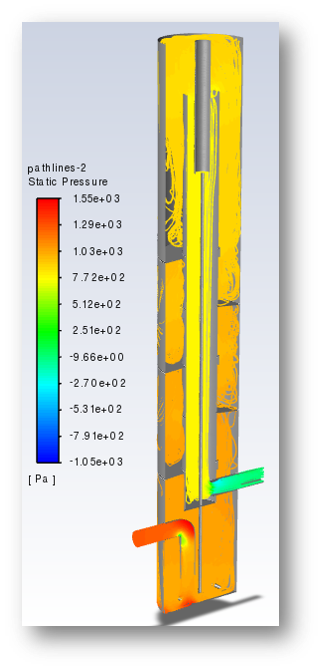
Технологические данные о работе цеха производства селитры включали в себя несколько сотен ключевых параметров комплексного процесса. Готовая цифровая модель состояла в общей сложности из более полутора тысяч индивидуальных элементов – теплообменников, трубопроводов, арматуры, массообменного и динамического оборудования. В реальных условиях эксплуатации режимы работы меняются, оборудование работает по-разному. Со временем происходит постепенное изменение его характеристик из-за износа, коррозии, внешних факторов. Гарантировать корректность и непротиворечивость всего массива данных было невозможно без работы на площадке и технического обследования.
Поездка специалистов АО «МЦД» на объект совпала с технологическим остановом – одна из установок цеха была остановлена на плановый ремонт. Им удалось не только проверить размеры трубопроводов на соответствие технической документации, осмотреть работающие узлы и агрегаты, снять температуру и другие технологические показатели на месте, но и изучить внутреннее устройство остановленных агрегатов – грануляционной башни, скрубберов. Это дало полезную информацию для правильного построения математической модели.
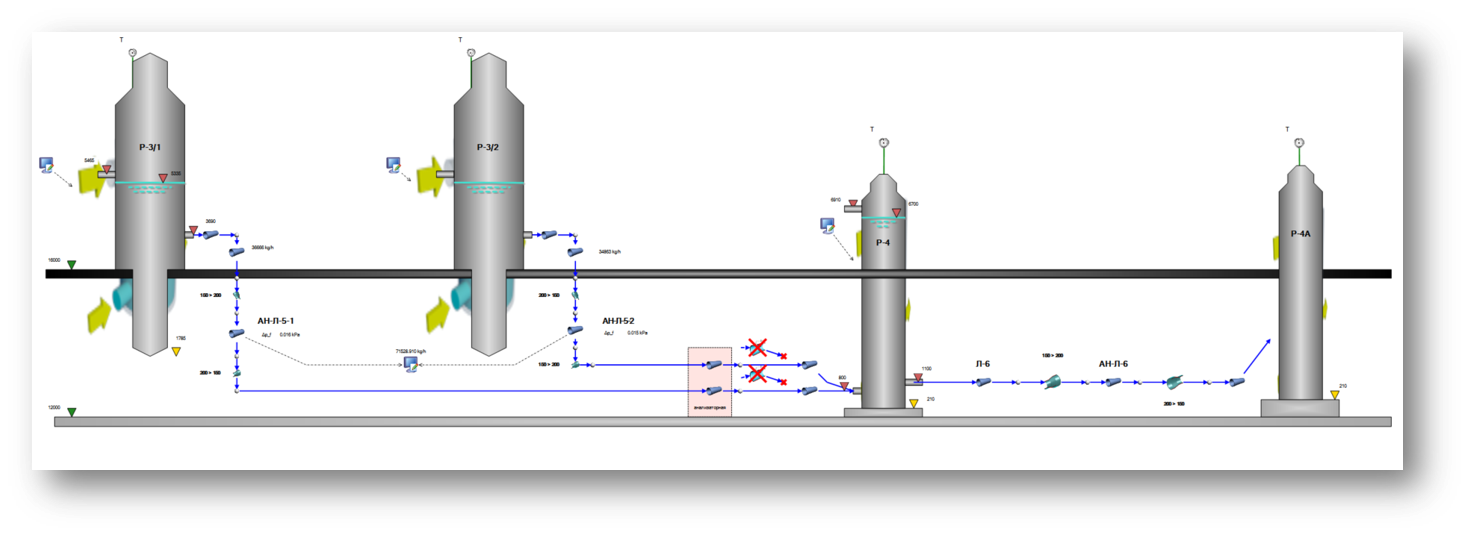
Тем не менее, в процессе построения и верификации модели эксперты АО «МЦД» обнаружили ряд расхождений в технологических данных. Они неизбежно возникают в большинстве проектов по созданию цифровых двойников: определенные несоответствия в технологических данных может не препятствовать работе цеха, но мешают точному моделированию процессов. Поэтому наибольшее время в проекте заняла работа с данными, включавшая выявление явных расхождений и их урегулирование с учетом производственного опыта, соблюдения материального баланса, законов физики и термодинамики. На этом этапе специалисты КАО «Азот» предложили ряд упрощений, который позволял гарантировать соответствие материально-тепловым балансам без ущерба для главной цели. Среди них – меньшая детализация, расширение диапазона допустимых отклонений для тех участков, данные по которым были неоднозначны, а влияние для основных показателей производства незначительно. Таким образом, экспертам АО «МЦД» удалось обеспечить общую сходимость материально-теплового баланса, результатов модели и показаний измерительных приборов реального производства.
Устранение «узких мест» и отработка сценариев технического перевооружения
После того, как цифровая модель была готова и верифицирована, проект перешел в новую фазу аналитики результатов и отработки на модели производственных задач.
В первую очередь нужно было определить с помощью модели, какие части технологической схемы могут ограничивать выработку продукта. Эти части – так называемые «узкие места» – были заложены в первоначальном проекте и не ограничивали производительность цеха при обычной работе. Но если увеличивать подачу сырья и повышать выработку продукта, то они не справятся с увеличившейся нагрузкой: трубопроводы и арматура дадут повышенное гидравлическое сопротивление, теплообменные аппараты не обеспечат нужную теплопередачу, вентиляторы и насосы не смогут дать нужную подачу потоков. Нагрузка на узлы отличается при разных технологических режимах, а поиск «узких мест» требует провести серию расчетов и сравнить их результаты.
Когда «узкие места» определены, нужно реконструировать оборудование таким образом, чтобы надежно снять ограничение. Если, например, просто увеличить диаметр трубопровода или заменить теплообменник, это, скорее всего, не решит проблему, а перенесет «узкое место» в другой элемент схемы. Модель помогла экспертам АО «МЦД» подобрать комплекс нужных изменений, снимая ограничения во всем диапазоне режимов работы агрегатов.
Далее специалистам было необходимо определить, как с минимальными затратами модернизировать производство, чтобы выйти на значительно большую производительность при снижении себестоимости продукции.
Технологическая модель не способна сама по себе ответить на этот вопрос, поэтому эксперты АО «МЦД» дополнительно разработали экономическую модель производства. Она позволила рассчитать срок окупаемости изменений и расставить все мероприятия в порядке его увеличения. Поскольку КАО «Азот» рассматривает проекты модернизации со сроком окупаемости не более трех лет, то связанные технологическая и экономическая модель, а также опыт экспертов позволили исключить неэффективные или слишком дорогие технические перевооружения, и составить «шорт-лист».
Результаты и перспективы проекта
Крупнотоннажное производство КАО «Азот» работает и развивается уже не одно десятилетие. Устойчивое развитие – это долгосрочный процесс, поэтому разовая проработка производственных задач не достаточна. Именно поэтому главный результат совместной работы КАО «Азот» и АО «МЦД» – внедрение цифрового двойника в производственные процессы предприятия.
Руководство КАО «Азот» активно вовлекает производственный персонал в процесс генерации новых идей, стимулирует повышение технологических компетенций. Предложения от персонала производства аммиачной селитры должны оперативно анализироваться на цифровом двойнике цеха. Эксперты КАО «Азот», благодаря цифровому двойнику, могут проанализировать десятки предложений в год, проверяя эффекты, находя оптимальные решения, выявляя потенциальные риски. Таким образом, цифровой двойник работает на повышение качества продукции, сокращения издержек, совершенствования рабочих процессов.
«Создание цифрового двойника одного из крупнотоннажных агрегатов «Азота» – результат высококлассной командной работы специалистов группы моделирования технологических процессов дирекции по развитию бизнес-системы «Азота» и экспертов АО «МЦД». Для крупнейшего за Уралом химического предприятия это уверенный шаг вперед к новым производственным достижениям. Без результативного поиска и качественного устранения потерь – ключевых задач бережливого производства – мы не смогли бы обойтись. Цифровизация позволяет решать их с минимальными затратами и рисками. Логично, что в «Трансформацию бизнес-системы «Азота» вошел ряд проектов, предполагающих кибернетический подход к системному анализу работы агрегатов и протеканию сложных химических процессов. Следующий шаг – их оптимизация. Стратегическая цель, которую ставит перед нами руководство компании – создание эффективного, динамично развивающегося и безопасного производства. Цифровые решения нам в этом помогут», – комментирует Николай Денисов, директор по развитию бизнес-системы КАО «Азот».