Автор: А.М. Добротворский, А.В. Копыльцов, Д.А. Легостаев, А.В. Макаров, А.Г. Саватеев (ЗАО «НПО «Ленкор»).
Опубликовано в журнале Химическая техника №1/2015
Переход к рыночной экономике и включение Российской Федерации в международную систему разделения труда, осуществленные за последнее двадцатилетие, дали определенный положительный эффект, связанный, прежде всего, с реализацией преимуществ, которые были обусловлены высокими ценами на углеводороды. За счет этого, в частности, осуществляются новое строительство, реконструкция и модернизация предприятий нефтеперерабатывающей и нефтехимической промышленности РФ.
Не секрет, что в основу такой модернизации отрасли были заложены закупки зарубежных технологий и оборудования в масштабах, которые в силу политических и экономических причин были недоступны ранее. Этот процесс, очевидно, имеет и негативную сторону. В значительной степени затормозилось развитие отечественного химического машиностроения, снизилось качество его продукции и конкурентоспособность не только на внешнем рынке, но и на внутреннем. Существенный, а в ряде случаев невосполнимый ущерб был нанесен отечественной прикладной науке. Россия быстрыми темпами начала терять технологическую независимость во многих отраслях народного хозяйства, включая стратегические отрасли.
Это обстоятельство было хорошо понятно многим специалистам. Об опасности дальнейшего движения в этом направлении сообщалось и в печати [1, 2].
С особой остротой проблема хотя бы частичного восстановления технологической независимости нашего государства встает сегодня в условиях, вероятнее всего, долгосрочных экономических санкций со стороны западных партнеров.
Эти вопросы вынесены на общегосударственный уровень. Они стали повесткой дня заседания Государственного Совета 18 сентября 2014 г.
На заседании Госсовета в выступлении Министра экономического развития А.В. Улюкаева были указаны критические направления импортозамещения: электронно-компонентная база, наукоемкое станкостроение, инструментальная промышленность, оборудование для нефтегазового комплекса, промышленность катализаторов для химии и нефтехимии.
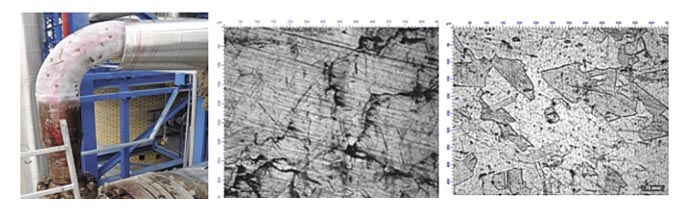
Если мы обеспечим эти позиции, значит, мы сбережем огромные объемы национального внутреннего продукта [3]. По крайне мере, три из обозначенных направлений имеют прямое отношение и к нефтепереработке и нефтехимии. Непосредственно к этой теме относятся вопросы замещения закупаемого по импорту оборудования.
Переходя к обсуждению этого вопроса, следует сразу отметить, что отечественное химическое машиностроение по целому ряду позиций сегодня просто не способно решить проблему замещения импортного оборудования. Остановимся на проблемах, которые возникают в секторе потенциальных возможностей отечественных производителей
Прежде всего, подчеркнем, что проблема замещения зарубежных поставок на отечественную продукцию, актуальна не только в связи с сокращением доступа к ней, но в целом ряде случаев из-за снижения качества импортного оборудования и комплектующих. Химическое машиностроение СССР, несмотря на определенное технологическое отставание, повышенную материалоемкость производства и др., в целом обеспечивало достаточно высокую надежность изготавливаемого оборудования. Об этом говорит опыт его диагностики. Такие ответственные аппараты, как реакторы, кожухотрубчатые теплообменники, сосуды давления, отработали на предприятиях отечественной нефтепереработки и нефтехимии три-четыре и более проектных срока эксплуатации. При этом нам не известно ни одного случая катастрофического разрушения реакторов или теплообменников, подобного тому, который произошел на Tesoro Refinery (Анакортис, штатВашингтон США) в 2010 г. [4, 5].
Сегодня мы неоднократно сталкиваемся с низким качеством поставок зарубежного оборудования.
Приведем несколько примеров. За последние несколько лет года наша организация трижды столкнулась с преждевременным выходом из строя труб, изготовленных из высоколегированных сталей и сплавов и поставленных на предприятия отрасли компанией TUBACEX: трубы печей пиролиза установки (ЗАО «Сибур-Химпром»), трубы трубчатого реактора синтеза изопрена (Нижнекамский НХЗ), отвод продуктовой линии установки гидроочистки дизельного топлива (Омский НПЗ).
Во всех случаях одной из главных причин разрушения труб явилось недостаточное качество их изготовления. Так, разрушение отвода произошло из-за неоднородности металла в зоне высокой концентрации неметаллических включений, в которой развивалось водородное растрескивание (рис. 1).
Два других примера связаны с разрушением труб подогревателя варочного щелока на лесохимическом комплексе ОАО «Монди СЛПК» (г. Сыктывкар) и на НПЗ ООО «ЛУКОЙЛ-Нижгороднефтеоргсинтез».
В обоих случаях фирмы-изготовители настаивали на том, что причиной растрескивания явилось наличие хлоридов в сырье или в воде, использованной для гидроиспытаний.
На наш взгляд, этот довод, основанный на требованиях инструкции по эксплуатации аппаратов, содержащей практически не выполнимые и не поддающиеся контролю требования к содержанию хлоридов, не является обоснованным. Главной причиной разрушения, по нашему мнению, являлся высокий уровень остаточных напряжений холоднодеформированных труб, не снятых термообработкой, а также недостатки конструкции аппаратов. Большое число отказов наблюдается также на пластинчатых теплообменниках [6]. Обладая высокой эффективностью, конструкция этих аппаратов ограничивает объем их входного контроля, технической диагностики, снижает или полностью исключает их ремонтопригодность.
Наконец, укажем на проблемы эксплуатации футерованных коллекторов реакционных печей в составе установок получения водорода (УПВ) – парового риформинга. Из-за нарушения целостности футеровки наблюдаются значительные перегревы стенок коллекторов, как правило, выполненных из углеродистых сталей (рис. 2). При контакте с горячим синтез-газом, содержащим 75% об. водорода, создается угроза быстрого развития водородной коррозии стали, что наблюдалось на УПВ ООО «КИНЕФ» (рис. 3). Таким образом, следует признать, что выбор материального исполнения коллекторов был недостаточно обоснован.

Большое число таких примеров было приведено в докладе генерального директора ООО «КИНЕФ» В.Е. Сомова на семинаре-совещании Ростехнадзора с участием членов секции по безопасности объектов нефтегазового комплекса НТСРостехнадзора, проведенного в г. Кириши 23–25 апреля 2014 г. [7].
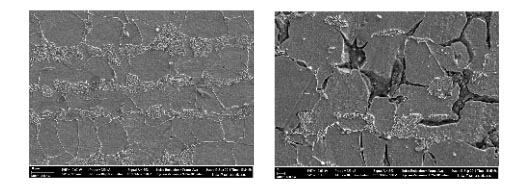
по результатам растровой электронной микроскопии: а – в объеме стенки;
б – на внутренней стороне трубы в зоне перегрева
с характерными признаками водородной коррозии
Безусловно, качество изготовления продукции отечественного химического машиностроения также является важнейшей проблемой импортозамещения. В нашей практике мы сталкиваемся со случаями несоответствия поставляемой продукции даже собственным техническим условиям изготовителя. Так, значительные отклонения от требований технических условий были выявлены по целому ряду параметров (предел текучести, предел прочности, размер зерна) большой партии центробежно-литых труб, поставленных в ООО «КИНЕФ». При этом данные, содержавшиеся в сертификатах на трубы, не соответствовали фактическим характеристикам металла. На низкое качество трубной продукции было указано на заседании секции по безопасности объектов нефтегазового комплекса НТС
Ростехнадзора 28.10.14. В связи с этим в НК «Роснефть» с целью обеспечения необходимого качества закупаемых труб создана служба, специалисты которой работают на трубных заводах, где осуществляют пооперационный, начиная с заготовок, контроль качества изготовления изделий.
Значительный объем брака выявляется в сварных соединениях сосудов и аппаратов, поставляемых отечественными производителями.
В качестве примера можно привести брак сварных соединений, в том числе протяженные трещины, реакторов адиабатического гидрирования, поставленных в ОАО «Сибур-Нефтехим». По результатам 100%-ного радиографического контроля было принято решение о демонтаже уже смонтированных аппаратов и возврате их для выполнения ремонтных работ. Другим примером является значительное превышение допусков по уводу кромок продольных швов и смещению кромок кольцевых швов на обечайках реакторов гидроочистки дизельного топлива, подготовленных к поставке в ЗАО «РНПК».
Устранение выявленных дефектов потребовало длительного времени и привело к дополнительным издержкам как завода-изготовителя, так и заказчика оборудования.
Наибольшие проблемы изготовителей возникают при выполнении сварных соединений сосудов и аппаратов, изготавливаемых из биметаллического листа. Прежде всего, следует указать на недостаточное качество биметаллических листов, изготовленных взрывом. Дефекты изготовления вплоть до образования трещин вдоль всей образующей как по основному металлу, так и вдоль сварных швов выявляются уже на стадии вальцовки листа, а также после сварки обечаек.
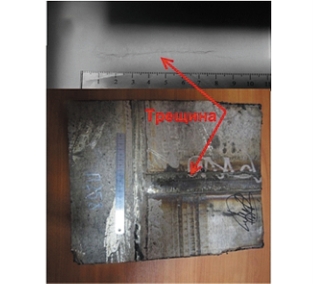
отпарной колонны, выявленная
при рентгенографическом контроле
К сожалению, дефекты сварных соединений сосудов часто выявляются при входном контроле уже поставленного оборудования. На рис. 4–6 приведены результаты контроля отпарной колонны блока отпарки сульфидных стоков установки «Элементарная сера» (рис. 4, 5) и вакуумной колонны установки первичной переработки нефти (рис. 6). Металлографическое исследование вырезок металла в местах наиболее опасных трещин сварных швов, выявленных радиографическим контролем, не только подтвердили его результаты, но также показали наличие большого числа разнонаправленных трещин, что может привести к их быстрому развитию при контакте с коррозионно-активными компонентами технологических сред.
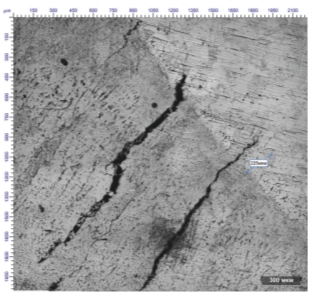
а – общий вид; б – микротрещины в зоне сварного шва
Объективные причины снижения качества продукции отечественного химического машиностроения связаны с отставанием в области модернизации технологии производства, технического оснащения предприятий как основными средствами производства, так и средствами пооперационного контроля, недостаточным числом квалифицированных специалистов. Еще одной причиной является вынужденное снижение цен на продукцию в условиях наиболее недобросовестной конкуренции. Преодоление указанных трудностей является основной задачей, стоящей на пути решения проблемы импортозамещения.
В этой связи нельзя допускать, чтобы машиностроительные предприятия использовали при изготовлении оборудования устаревшие
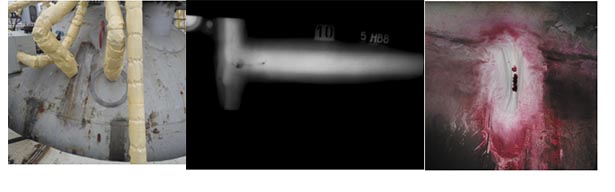
и капиллярного (в) контроля
Технические условия, не соответствующие требованиям действующих нормативных документов; чтобы оборудование изготавливалось с использованием морально и физически устаревших станков, приспособлений, средств контроля качества.
Следует также исключить возможность поставки оборудования, не отвечающего требованиям Технических регламентов таможенного Союза, что в свою очередь обеспечит его надежность и безопасность в период назначенного срока эксплуатации.
Список литературы
- Добротворский А.М. Симбиоз государства, науки и техники/Технополис XXI. 2011. Вып. 1 (23). С. XII–XII.
- Добротворский А.М. Наука страдает от разрыва связей с производством// Деловая карта России. Региональное приложение к газете «Экономика и время». 2013. С. 31.
- Заседание Государственного Совета 18.10.14 г. http://state.kremlin.ru/state_ council/46636
- Naphtha Hydrotreater E-6600E Failure. Anacortes Refinery, Washington//TOP Investigation Team Report. 2011. 52 p.
- Catastrophic rupture of heat exchanger (seven fatalities) Tesoro Anacortes refinery Anacortes,Washington April 2, 2010//Report 2010-08-i-wa, May 2014. Р. 1–160.
- Бурлов В.В., Парпуц Т.П. Оценка работоспособности пластинчатых теплообменников на основании опыта эксплуатации на нефтеперерабатывающих и нефтехимических предприятиях//Химическая техника. 2011. №3. С. 7–11.
- Haдзop – строгое сoблюдeниe дeйствyющего законодательства//Бeзoпаснoсть тpyда в прoмышлeннoсти. 2014. №5. С. 5–14.