Автор: В.А. Коротков (Нижнетагильский технологический институт – филиал Уральского федерального университета).
Опубликовано в журнале Химическая техника №9/2014
Электрическая дуга, обжатая в той или иной мере газовым потоком, увеличивает температуру, становится более устойчивой и получила название плазменной дуги.
Наличие в промышленности электродуговых аппаратов для резки, сварки, напыления дало повод новаторам в 80-е годы 20-го века приспособить их для поверхностной закалки. Установки микроплазменной и аргонодуговой сварки, плазменного напыления, плазменной сварки и резки модернизировали для закалки деталей шахтного оборудования, бандажей рельсо-правильных машин, прокатных валков, роликов рольгангов и др.[1–4].
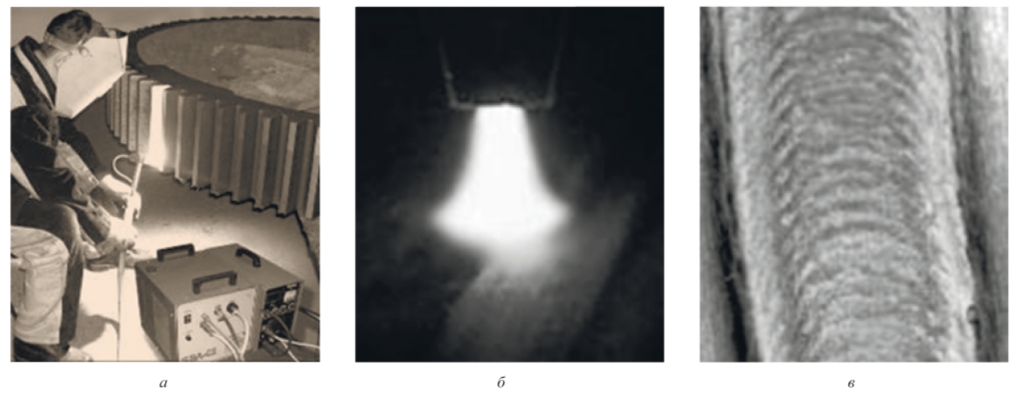
а – установка УДГЗ-200; б – плазменная дуга; в – закаленная полоса с цветами побежалости
Однако плазменной закалке 1980–1990-х годов был присущ существенный недостаток. Она применялась только в автоматическом режиме, когда параметры настройки легко поддерживаются неизменными, ручное же ведение процесса было практически невозможно.
В современный век роботов и «безлюдных» производств разработка ручной технологии может показаться ошибочной. Но ручные технологии, благодаря универсальности, демонстрируют живучесть. В мире основной объем сварки (более 80%) продолжает выполняться электродами или полуавтоматами, т. е. вручную. По аналогии полагали (и этот расчет оправдался), что с разработкой ручного способа плазменной закалки объемы ее применения возрастут, и произойдет это за счет изделий, которые ранее по тем или иным причинам закалить было невозможно или затруднительно.
Проблема ручной плазменной закалки была решена в начале 2000-х годов в ООО «Композит», созданном в 1990 г. при Нижнетагильском филиале УПИ (ныне УрФУ).
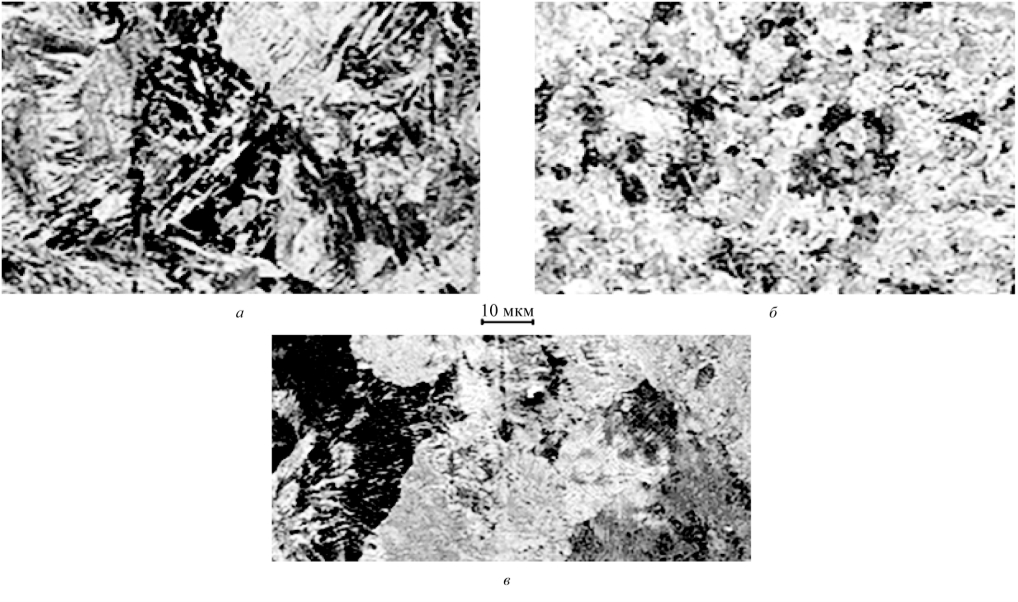
на рельсовой стали 70 (сверху) и полученная в ионном облучении (в) на микроскопе AurigaCrossbeam
Здесь выполнили разработку способа и установки для ручной плазменной закалки УДГЗ-200 [5, 6]. В установке предусмотрена горелка, небольшие размеры которой делают ее удобной для ручного манипулирования, и позволяют добираться до труднодоступных мест, т.е. упрочнять то, что может остаться без упрочнения. При закалке сварщик перемещает дугу по поверхности, на которой остаются имеющие цвета побежалости закаленные полосы шириной 8…16 мм (рис.1). Сварщик следит, чтобы под дугой происходило «вспотевание» поверхности (состояние предшествующее плавлению) при котором гарантируется разогрев, достаточный для закалки, но без грубого ее повреждения в виде оплавления. «Вспотевание» контролировать не труднее, чем плавление при сварке, поэтому работу на установке осваивают сварщики 2, 3 разрядов. При этом дуга оставляет на поверхности закаленные полосы с цветами побежалости без существенного изменения шероховатости в диапазоне Rz10…60.
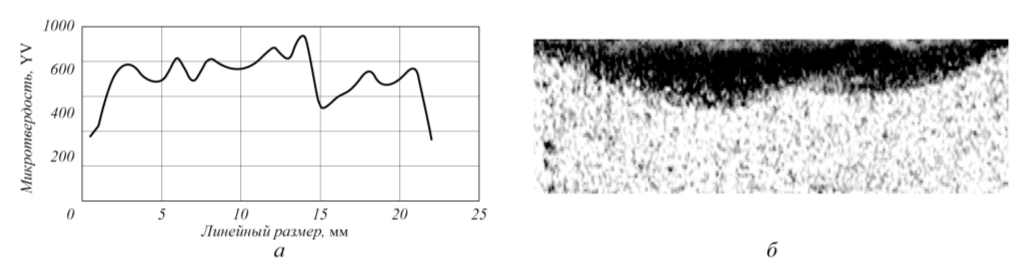
Закалка происходит за счет отвода теплоты в тело детали без подачи воды на место нагрева [7]. Поэтому установка УДГЗ-200 применяется на ремонтных площадках, по месту механообработки и эксплуатации деталей, а не только в термических цехах и специализированных участках. Закалка установкой УДГЗ-200 может быть механизирована, автоматизирована и роботизирована, что делает ее пригодной к применению в современных высокотехнологичных производствах.
Целью настоящей работы является изучение влияния плазменной закалки установкой УДГЗ-200 на структуру и износостойкость различных сталей и деталей машин в лабораторных и производственных условиях.
Структура и твердость закаленного слоя
При плазменной закалке установкой УДГЗ-200 поверхность разогревается до температур близких к температуре плавления материала детали. Поэтому структурные превращения в закаленном слое аналогичны превращениям в зоне термического влияния при сварке [8]. Непосредственно под поверхностью, где температура нагрева особенно велика, происходит укрупнение зерна; ниже лежит участок мелкого зерна (рис. 2)1.
Между закаленным слоем и основным металлом находится переходный участок к основному металлу, в котором присутствуют фрагменты повышенной твердости.
Закаленные полосы в поперечном сечении представляют собой сегменты высотой 0,5…2,0 мм в зависимости от режима закалки. Их укладывают с перекрытием, чтобы не иметь незакаленных промежутков.
В местах перекрытия полос происходит двойная закалка с некоторым увеличением твердости. Последующая закаленная полоса оказывает на предыдущую полосу отпускное воздействие, сопровождающееся снижением твердости в меньшей (на легированных сталях) или большей (на углеродистых сталях) мере (рис. 3). Твердость поверхности с плазменной закалкой у различных сталей (измерения выполнены ультразвуковым переносным прибором УЗИТ-3), HRC:
Сталь 65Г | Сталь 40Х | Сталь 20ГЛ | |
На полосе | 52…57 | 49…54 | 34…39 |
На стыках полос | 40…45 | 37…42 | 23…28 |
Износостойкость слоя плазменной закалки
На машине трения МИ-1М в пять этапов (по 5 мин каждый) с нагрузкой 200 Н на первых четырех этапах и полуторной нагрузкой на пятом этапе при 240 об/мин по схеме диск–колодка без смазки испытывалась износостойкость различных сталей с плазменной закалкой.
Результаты приведены в табл. 1 и на рис. 4, 5.
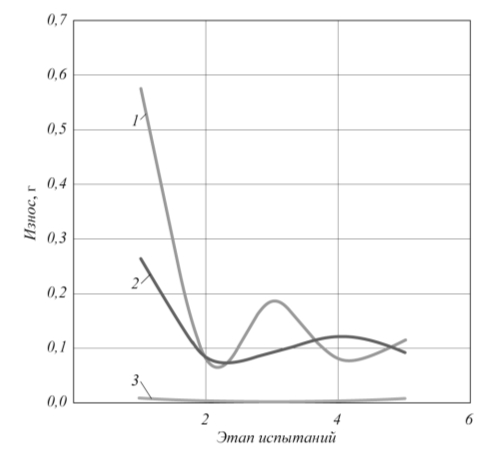
из стали 30ХГСА после различной обработки:
1 – нормализация (HB 240); 2 – объемная закалка
с отпуском (HB 400); 3 – плазменная закалка (HB 500)
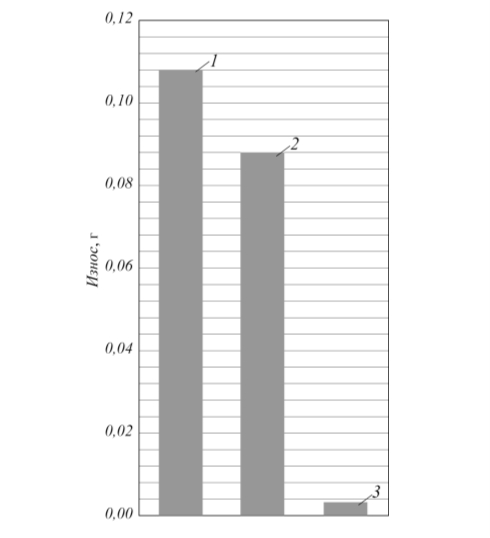
из стали 30ХГСА на 2–4 этапах устоявшегося изнашивания при сухом трении после различной обработки:
1 – нормализация (HB 240); 2 – объемная закалка с отпуском (HB 400); 3 – плазменная закалка (HB 500)
Из табл. 1 видно, что плазменная закалка снизила износ колодки из рельсовой высокоуглеродистой стали 70 в 121 раз; при этом неупрочненный диск из колесной стали 65Г не только не снизил износостойкости, но увеличил ее в 2,1 раза. Феноменальное увеличение стойкости в результате плазменной закалки объясняется сменой механизма изнашивания. Поверхности трения без упрочнения имели возможность «схватываться», т. е. образовывать выступами микронеровностей точечные сварные соединения, которые создают абразивный фактор и ускоряют изнашивание. Исключение явлений схватывания при упрочнении закалкой изменило характер изнашивания, который приобрел характер усталостного диспергирования, что многократно уменьшило износ.
Таблица 1
Влияние плазменной закалки на износостойкость рельсовой стали
Колодка (Сталь 70) | Диск (Сталь 65Г) | ||||||
Обработка | Твердость, HV | Износ, г | Коэффициент износостойкости | Обработка | Твердость, HV | Износ, г | Коэффициент износостойкости |
Без закалки | 280 | 1,50740 | 1,0 | Без закалки | 314 | 2,1246 | 1,0 |
С плазменной закалкой | 877 | 0,01242 | 121,0 | С плазменной закалкой | 314 | 1,0208 | 2,1 |
Износ – суммарный за 20 мин испытаний средний по 5 парам. |
На рис. 4 видно, что объемная и плазменная закалка дисков из стали 30ХГСА существенно снизили износ на первом этапе приработки. При этом износ на этапах 1–4 устоявшегося изнашивания у дисков с плазменной закалкой оказался примерно в 30 раз меньше, чем у нормализованных и дисков с объемной закалкой и отпуском (см. рис. 5).
В целом по результатам проведенных испытаний можно заключить, что плазменная закалка существенно увеличивает износостойкость по сравнению с нормализацией и объемной закалкой с отпуском.
Таблица 2
Износ рельсов на линии по производству колесных осей
Период эксплуатации | Наличие плазменной закалки | Выпуск осей, тыс. шт | Износ, мм | Стойкость, тыс.шт.осей/мм износа |
03.2005 – 06.2007 (28 мес) | Нет | 198, 3 | 3,2 | 62 |
07.2007 – 12.2013 (78 мес) | Да | 474,0 | 1,1 | 431 |
Производственные наблюдения
На линии по производству железнодорожных колесных осей из рельсов Р18 смонтирован путь 14,5 м.
Грубая кованая поверхность осей ускоряет изнашивание рельсов, уменьшение высоты которых (износ) за 28 месяцев составило ~3,2 мм из 5,0 мм допускаемых. Для замедления изнашивания, без прерывания производства осей, выполнили закалку рельсов установкой УДГЗ-200, увеличившую твердость от HRC 20 до HRC 50. Из табл. 2 видно, что стойкость рельсов в результате закалки возросла почти в 7 раз. Поскольку износ рельсов (3,2+1,1 = = 4,3 мм) еще не достиг критического (5,0 мм), а закаленный слой (~1 мм) почти износился, запланирована еще одна закалка, которая, как и первая, будет проведена без демонтажа рельсов.
Проводились наблюдения за крановыми рельсами КР-100, упрочненными плазменной закалкой, установленными в одну нитку с незакаленными рельсами на грузоподъемном кране. Твердость рельсов в состоянии поставки составляла НВ180, после плазменной закалки – НВ550. После 14 мес. эксплуатации незакаленные рельсы получили износ не менее 2 мм, тогда как об износе закаленных свидетельствовала лишь «потертость» поверхности, а не уменьшение размера.
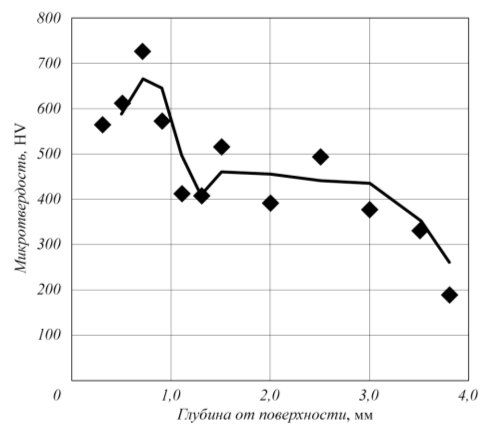
– статистическая обработка результатов
Исследовалась возможность упрочнения крановых колес плазменной закалкой в ходе восстановления наплавкой. Для их наплавки обычно применяется проволока Нп-30ХГСА, которой был наплавлен опытный образец, после чего механически обработан и закален установкойУДГЗ-200. Исследование его поперечного сечения показало (рис. 6), что наплавленный слой составляет ~3мм и имеет микротвердость ~HV450. В результате плазменной закалки на глубине до ~1мм он увеличил твердость до ~ HV650. Наплавленные колеса, упрочненные плазменной закалкой (рис. 7) не уступают в износостойкости новым колесам из стали 65Г с термическим упрочнением на твердость ~НВ350.
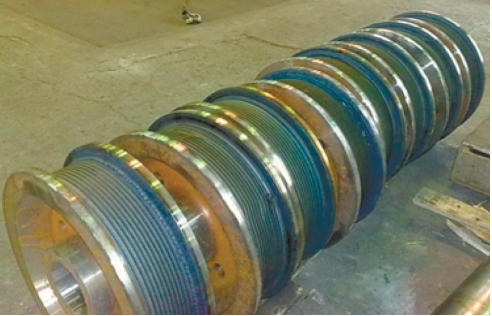
Размеры закалочной горелки установки УДГЗ-200 позволяют закаливать зубья шестерен с модулем m ≥ 6.
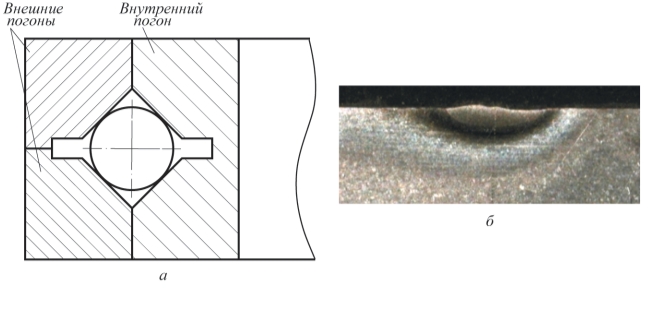
Закалка производится по боковым поверхностям зуба. Впадины между зубьями не закаливаются, так как туда нет доступа плазменной дуге. При закалке ТВЧ это является недостатком, вызывающим поломки зубьев при эксплуатации. Но плазменная закалка боковых поверхностей к поломкам не приводит, так как производится последовательно, тогда как закалка ТВЧ – одновременно по всему профилю, что приводит к появлению больших остаточных напряжений. Закалка установкой УДГЗ-200 зубчатых колес (сталь 35Л число зубьев z = 90, модуль m = 24) сталеразливочного крана грузоподъемностью 225 т (см. рис. 1, а) увеличила срок службы в 2,8 раза. Подобный результат получен при плазменной закалке зубчатого венца (сталь 35ГЛ) рудоусреднительной машины. Из-за больших размеров венца (диаметр ~6 м), закалка производилась на шихтовом дворе под открытым небом, что составляет еще одно преимущество установки УДГЗ-200. Шестерни (m = 10, z = 16) из конструкционной стали 40Х в «улучшенном» состоянии (закалка с высоким отпуском) в открытой передаче укладчика в агломерационном производстве изнашивались в течение одной недели. Плазменная закалка увеличила твердость с НВ250 до НВ520, а наработку – до 4 недель, т.е. в 4 раза. При этом изнашивается только закаленный слой (~1мм), что позволяет повторять закалку прямо на укладчике (важная особенность работы установкой УДГЗ-200) и увеличить срок службы шестерней до 8 раз. «Погоны» (рис. 8) представляют собой обоймы (кольца) крупногабаритных опорных шариковых подшипников диаметром 608…2354 мм из стали 20Х13. Эта сталь имеет повышенную склонность к оплавлению поверхности, поэтому была предусмотрена шлифовка после закалки. Припуск на шлифовку выбирали с учетом того, что возможная глубина оплавления составляет 0,3 мм при глубине закаленного слоя 1,3 мм. Для закалки на плите размещали несколько «погонов» (рис. 9). Закалку производили короткими участками с переходом от одного «погона» к другому, чем удалось полностью предотвратить их деформирование. Закаленные погоны (~HRC50) выдержали стендовые испытания и были приняты заказчиком.
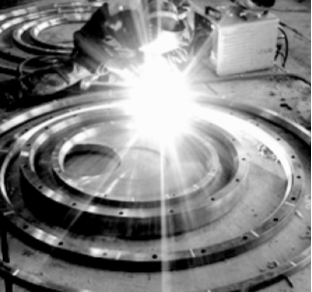
Таким образом, значительным событием в развитие закалки стала разработка установки УДГЗ-200. Это единственная, выпускающаяся серийно, специализированная установка для поверхностной плазменной закалки. Она сделала возможным проводить закалку вручную, что существенно расширило область ее применения. Теперь стало можно закаливать многое из того, что ранее было недоступно.
Установка УДГЗ-200 прошла сертификацию, и к концу 2013 г. было произведено более 50 установок, которые поставлены на предприятия России, Украины, Казахстана, Киргизии. В 2008 г. установка отмечена серебряной медалью на Женевском салоне изобретений и инноваций.
Закалка установкой УДГЗ-200 происходит без подачи воды; теплота, выделяющаяся в процессе закалки, отводится в тело детали. Поэтому данную технологию можно применять не только в термических цехах, но и на ремонтных площадках, по месту обработки и эксплуатации деталей, что многократно сокращает капитальные вложения при ее внедрении в производство. Работу на ней осваивают сварщики 2–3 разрядов.
Закалка установкой УДГЗ-200, оставляя на поверхности цвета побежалости, не приводит к существенному ухудшению шероховатости в диапазоне Rz 10…60 и к возникновению деформаций. Благодаря этому многие закаленные детали идут в эксплуатацию без финишной шлифовки. Это сокращает процесс изготовления, снижает себестоимость.
Твердый (HRC45…65) слой закалки (до 2 мм) многократно увеличивает срок службы крановых рельс и колес, зубчатых и шлицевых соединений, канатных блоков, различных штампов и проч.
Список литературы
- Кобяков О С., Гинзбург Е.Г. Использование микроплазменного нагрева в процессе упрочняющей технологии//Автоматическая сварка. 1985. №5.
- Лещинский Л.К., Пирч И.И., Самотугин С.С. и др. Структура и свойства наплавленного металла углеродистых сталей, упрочненных плазменной струей//Сварочное производство, 1985. №11.
- Сафонов Е.Н., Журавлев В.И. Поверхностное упрочнение железоуглеродистых сплавов дуговой закалкой//Сварочное производство. 1997. №10.
- Бердников А.А., Демин В.С., Серебрякова Е.Л. и др.Упрочнение чугунных валков методом плазменной закалки//Сталь, 1995. №1.
- Патент РФ 2313581. Способ ручной плазменной закалки
- Korotkov V.A., Shekurov A.V. Investigations into plasma quenching//Welding International. 2008. Vol. 22. №7.
- Korotkov V.A., Anan’ev S.P., Shekurov A.V. Investigation of the effect of the cooling rate on the quality of the surface layer in plasma quenching//Welding International. 2013. Т. 27. №5.
- Коновалов А.В., Куркин А.С., Макаров Э.Л.и др.Теория сварочных процессов/Под ред. В.М. Неровного. М.: Изд-воМГТУ им. Н.Э. Баумана, 2007.