Автор: С.В. Афанасьев (Тольяттинский госуниверситет), С.П. Сергеев (ОАО «ГИАП»), В.А. Волков (ООО «Дельта-пром инновации»).
Опубликовано в журнале Химическая техника №11/2016
Совершенствование технологий и оборудования крупнотоннажного производства диоксида углерода является приоритетным направлением деятельности любого крупного изготовителя аммиака и карбамида. Это вызвано тем, что диоксид углерода находит широкое применение не только на предприятиях крупнотоннажной химии, но и в различных отраслях промышленности, в том числе и в нефтехимии. Росту его потребления способствует создание крупных агрегатов с углекислотной конверсией, например метанольных, в которых диоксид углерода используется в качестве одного из компонентов промышленного синтеза.
По нашему мнению, в качестве перспективного способа переработки жидкого диоксида углерода следует рассматривать и его газоциклическое закачивание в нефтьсодержащие пласты с целью интенсификации нефтедобычи. Это обеспечивает снижение энергетических затрат, исключение риска образования газовых гидратов, повышение нефтеотдачи месторождений с высоковязкой нефтью.
Известно, что после заводнения нефтяных месторождений по обычной технологии или с использованием их улучшенных вариантов (циклическое воздействие, изменение направления потоков жидкости, водогазовое циклическое воздействие), или с повышением вытесняющих свойств воды (ПАВ, полимеры, щелочи), в недрах остаются неизвлекаемыми до 30–70 % начальных запасов нефти, которые оказываются сложно рассредоточенными в заводненном объеме пластов в виде остаточной рассеянной нефти и не охваченных заводнением слоев, линз, пропластков. Остаточную нефть способны вытеснять лишь те рабочие агенты, которые смешиваются с нефтью и водой или имеют сверхнизкое межфазное натяжение на границе раздела фаз. Такие условия возникают при вытеснении высоковязкой нефти диоксидом углерода.
Эти методы относятся к числу наиболее высокопотенциальных, способных снижать до 2–5 %. остаточную нефтенасыщенность призабойной зоны, охваченной рабочим агентом. Главное в применении этих методов – обеспечить высокий охват нефтяной залежи эффективным вытесняющим агентом (диоксидом углерода) и мицеллярным раствором. Применительно к российским нефтедобывающим организациям они имеют принципиальное значение, так как основная часть остаточной нефти на известных разрабатываемых месторождениях остается в виде заводненных запасов, которые труднее извлекать, чем из незаводненных пластов.
При растворении в воде диоксида углерода вязкость ее несколько увеличивается, однако этот прирост незначителен. При массовом содержании в воде 3–5 % СО2 вязкость ее возрастает на 20–30 %. Образующаяся угольная кислота растворяет породы пласта и повышает проницаемость. В случае песчаников она увеличивается на 5–15%, а доломитов – на 6–75 %. В присутствии диоксида углерода снижается набухаемость глинистых частиц. СО2 растворяется в нефти в 4–10 раз лучше, чем в воде, поэтому он может переходить из водного раствора в нефть.
Диоксид углерода в воде способствует разрыву и отмывке пленочной нефти, покрывающей зерна породы, и уменьшает возможность разрыва водной пленки.
Вследствие этого капли нефти при малом межфазном натяжении свободно перемещаются в поровых каналах.
По данным проведенных исследований, СО2 растворяется в нефти значительно лучше метана и его газообразных гомологов, при этом растворимость увеличивается с ростом давления и молекулярной массы нефти.
Контактируя с нефтью, диоксид углерода частично растворяется в ней и одновременно экстрагирует углеводороды, обогащаясь ими. В результате давление, необходимое для смешивающегося вытеснения нефти диоксидом углерода, в 3 раза меньше, чем одним углеводородным газом.
На реализацию прогрессивных методов переработки диоксида углерода направлено и постановление правительства РФ №877-р, согласно которому к 2020 г. запланировано сокращение выбросов парниковых газов до уровня не более 25 % объема указанных выбросов в 1990 г. В соответствии с ним в июне 2017 г. Минприроды России поручено разработать методические указания по количественному определению косвенных энергетических выбросов парниковых газов.
В данной статье рассмотрены технологические аспекты производства и переработки диоксида углерода на примере ОАО «Тольяттиазот».
Особенности выделения СО2 из газовых смесей в процессах абсорбции/десорбции
Для извлечения СО2 из газовой смеси используются процессы абсорбции и десорбции. На производствах СО2, которые сосредоточены на аммиачных заводах, реализуются две классические схемы его выделения из продуктов конверсии природного газа: этаноламинная и с применением раствора поташа. Первый способ, как известно [1], описывается двумя основными химическими реакциями:
2RNH2 + H2О + CО2 ↔ (RNH3)2CО3; (1)
(RNH3)2CО3 + H2О + CО2 ↔ 2RNH3HCО3, (2)
где R – НОСН2СН2.
Уравнения (1) и (2) представляют собой упрощенную модель поглощения углекислого газа этаноламинами, конечными продуктами которого являются карбонаты и бикарбонаты этаноламмония.
При температуре 35…45 °С эти реакции идут вправо (абсорбция), а при температуре 105 °С и выше – справа налево (десорбция).
Детальное рассмотрение механизма взаимодействия СО2 с этаноламинами позволяет установить, что при сравнительно небольших степенях карбонизации (α < 0,5 моль СО2 на моль производного моноэтаноламина) реакция протекает с образованием замещенной карбаминовой кислоты:
CО2 + RNH2 ↔ RNHCOO– +H+. (3)
При этом в водном растворе мгновенно устанавливается кислотно-основное равновесие:
RNH2 + H+ ↔ RNH3 +. (4)
Конечным продуктом реакций (3) и (4) становится карбамат следующего строения:
RNH2COO– + RNH3 + ↔ RNHCOORNH3. (5)
Суммарную реакцию взаимодействия СО2 с молекулой этаноламина по карбаматному механизму можно записать в виде:
(1 + γ)RNH2 + СО2 ↔ (1 – γ)RNHCOOH + + γRNHCOO– + γRNH3 +, (6)
где γ — степень диссоциации карбаминовой кислоты.
Существенным недостатком моноэтаноламинного способа очистки газовых смесей от СО2 является образование значительных количеств смолистых веществ из-за циклизации моноэтаноламина в производные оксазолидона-2 и далее в продукты их превращения.
Благодаря предпринятым нами усилиям, были найдены эффективные методы переработки данных отходов в наполнитель для лакокрасочных материалов, поверхностно-активные вещества, ускоритель твердения полиизоцианатных композиций. На многие разработки получены патенты РФ [2–4].
Особый интерес представляет аминный модификатор карбамидоформальдегидных смол, синтезируемый из кубового остатка моноэтаноламинной очистки производства аммиака. Он производится ОАО «Тольяттиазот» по ТУ 2423-017-00206492–2002. Модификатор является смесью производных оксазолидона-2 и соединений с общей формулой R-CH2CH2OH, взятых в определенном соотношении [5].
С целью повышения эффективности выделения диоксида углерода из газовых смесей, на большинстве предприятий по производству минеральных удобрений проводится замена моноэтаноламина на метилдиэтаноламин. При этом из технологической схемы исключается смоловыделитель, сокращаются расходные нормы сырья и энергоносителей на выпуск продукции.
Второй распространенный способ очистки аммиака от диоксида углерода связан с использованием водного раствора поташа, преимущественно на агрегатах типа Кемико. Он описывается следующей кинетической моделью:
К2СО3 + Н2О + СО2 ↔ 2КНСО3. (7)
При температуре 45…55 °С реакция (7) идет вправо, т.е. наблюдается абсорбция СО2; при температуре 102°С и выше – влево (десорбция).
Параллельно с данной реакцией протекает электролитическая диссоциация К2СО3 и КНСО3, описываемая уравнениями (8) и (9):
К2СО3 + Н2О ↔ 2К+ + НСО3– + ОН–; (8)
КНСО3 + Н2О ↔ К+ + Н2СО3 + ОН–. (9)
Первая ступень гидролиза характеризуется существованием равновесия между ионами СО3 2– и НСО3–, а вторая – между ионами НСО3– и молекулами Н2СО3.
Для повышения эффективности процессов абсорбции и десорбции в раствор поташа для его активации добавляются диэтаноламин и ингибитор коррозии V2О5.
Указанные компоненты в водном растворе имеют следующее содержание,%: 24–30 К2СО3; 2,0–3,5 диэтаноламина; не менее 0,4 % V2О5 (раствор «Бенфилд»).
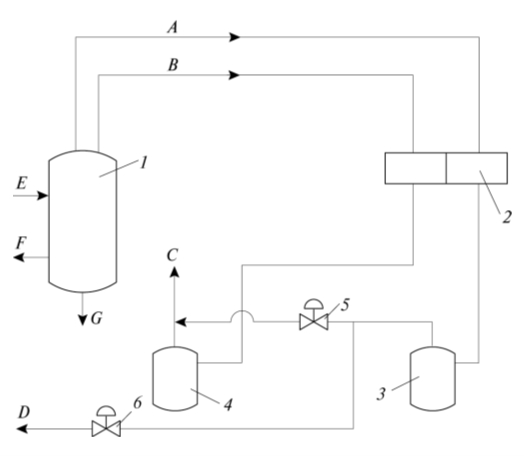
1 – регенератор (десорбер); 2 – воздушный холодильник;
3, 4 – сепараторы; 5, 6 – задвижки; А – «чистый» СО2;
B – «грязный» СО2; С – «грязный» СО2 в атмосферу;
D – «чистый» СО2 к потребителю; E – вход насыщенного диоксидом углерода раствора; F, G – выходы бедного
и полубедного растворов
На рис. 1 приведена принципиальная технологическая схема регенерации раствора «Бенфилд» с целью извлечения из него диоксида углерода.
При ее реализации газы десорбции выводятся из регенератора двумя потоками в виде «чистой» и «грязной» фракций. «Чистая» фракция, составляющая около 85 % общего количества СО2, отбирается ниже точки ввода насыщенного раствора в регенератор с температурой не более 100°С и с избыточным давлением выше 0,4 кгс/см2. Она охлаждается в воздушном холодильнике до температуры ниже 57°С и после отделения влаги в сепарирующем устройстве поступает через электрозадвижку к потребителю. Содержание горючих компонентов в диоксиде углерода не превышает 0,2% об. В «грязной» фракции СО2 концентрация водорода около 5% об.
После прохождения сепаратора эта фракция выводится за пределы технологической установки.
Важнейшим аппаратом установки регенерации раствора «Бенфилд» является регенератор (десорбер), представленный на рис. 2 [6].
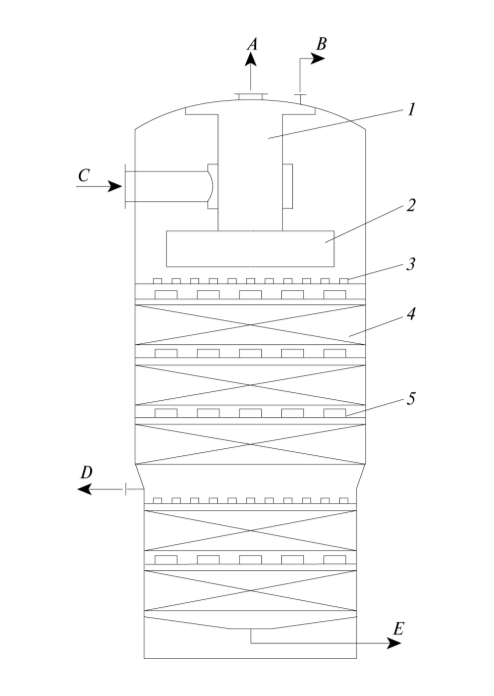
1 – труба для отбора «чистой»фракции СО2;
2 – сепарирующее устройство; 3 – распределительное устройство; 4 – насадка с кольцами Палля;
5 – колпачковая тарелка; А – «чистый» СО2; B – «грязный» СО2; С – вход насыщенного СО2 раствора; D – выход полубедного раствора; Е – выход бедного раствора
По сравнению с известными колонными устройствами в его конструкции имеются некоторые изменения.
Регенератор представляет собой вертикальный сварной аппарат высотой 70 м и включает центрально размещенную трубу 1 для отбора чистой фракции СО2, оригинальное сепарирующее устройство 2, несколько распределительных элементов 3, пять насадочных секций 4, заполненных кольцами Палля и разделенных колпачковыми тарелками 5.
В нижнюю часть аппарата загружают два слоя колец Палля размером 38×38 мм суммарным объемом 168,8 м3, а в верхнюю – три слоя колец размером 51×51 мм общим объемом около 460 м3. Конструкция регенератора обеспечивает высокую эффективность массообменных процессов при десорбции диоксида углерода из раствора «Бенфилд». Она, как видно из рис. 2, также позволяет проводить одновременный отбор как «чистой» (в нижней части трубы), так и «грязной» (из верхней секции) фракций СО2.
Объем производства диоксида углерода различной степени чистоты в ОАО «Тольяттиазот»:
Производство «грязного» диоксида углерода
Агрегат | Объем выпуска |
№1 | 46 532 кг/ч (372 263 т/год) |
№2 | 44 152 кг/ч (353 213 т/год) |
№3 | 39 013 кг/ч (312 108 т/год) |
№4 | 41 334 кг/ч (330 672 т/год) |
Итого | 1 368 000 т/год |
Производство «чистого» диоксида углерода
Агрегат | Объем выпуска |
№5 | 35501 кг/ч (284 008т/год) |
№6 | 41 605 кг/ч (332 842 т/год) |
№7 | 34 995кг/ч (279 946 т/год) |
Итого | 1 200 000 т/год |
Баланс потребления СО2 можно проиллюстрировать следующими данными. «Грязный» СО2 используется в установке получения жидкого диоксида углерода. Линия работает периодически и потребляет в течение года около 150 000 т. Кроме того, загрязненный водородом диоксид углерода применяется в производстве метанола при нехватке чистой фракции в количестве 18…20 т/ч в расчете на один агрегат производительностью 400 000 т/год.
Крупным потребителем «чистого» СО2 является производство карбамида, на долю которого приходится около 640 000 т/год. Еще около 300 000 т/год расходуется на проведение углекислотной конверсии на двух агрегатах производства метанола.
На сегодняшний день в резерве предприятия имеется более миллиона тонн диоксида углерода, который может быть использован для газоциклического закачивания в нефтедобывающие скважины. Технология процесса разработана авторами данной статьи и проходит процедуру патентования.
Производство жидкого низкотемпературного СО2
В настоящее время предложены энергосберегающие способы сжижения диоксида углерода, один из которых описан авторами [7].
В ОАО «Тольяттиазот» освоено получение жидкого низкотемпературного СО2, которое осуществляется в следующей последовательности.
Диоксид углерода из заводского коллектора поступает в сепаратор для выделения кислого конденсата из исходного газа. Далее он направляется на всасывание в двухкорпусный четырехступенчатый центробежный компрессор, где сжимается до давления 35 кгс/см2.
После компримирования, пройдя через еще один сепаратор, диоксид углерода подается в систему осушки.
Она состоит из двух адсорберов, заполненных двумя слоями силикагеля марок КСКГ и КСМГ. Контроль влажности осушенного газа осуществляется прибором типа «Байкал-2В».Адсорберы работают поочередно в автоматическом или полуавтоматическом режимах согласно программе по двум циклам: адсорбция и регенерация.
Осушенный газообразный СО2 температурой 5…10°С и температурой точки росы не выше –38°С поступает в первый конденсатор. Конденсация диоксида углерода осуществляется в трубном пространстве аппарата при температуре от –5 до –20 °С за счет охлаждения СО2 фреоном, поступающим в межтрубное пространство.
Жидкий диоксид углерода из конденсатора с температурой от 0 до –15°С и под давлением 30…35 кгс/см2 сливается в емкость на хранение.
Несконденсированный газообразный диоксид углерода подается в установку каталитической очистки для получения СО2 повышенного качества, используемого для специальных нужд. Сначала газ проходит угольный фильтр, где очищается от органических примесей и направляется в реактор окисления окиси углерода и водорода до диоксида углерода и воды на рутениево-палладиевом катализаторе. Окисление протекает согласно экзотермическим реакциям
2CO + O2 ↔ 2CO2 + Q1; (10)
2H2 + O2 ↔ 2H2O + Q2. (11)
Температура в зоне каталитической реакции поддерживается на уровне 220…240°С. Для ускорения процесса окисления газ перед реактором подогревается в теплообменнике до температуры 120°С. Выходящий из аппарата очищенный диоксид углерода охлаждается, проходит сепаратор и направляется на осушку в силикагелевые адсорберы. Осушенный газообразный CO2 конденсируется при давлении 28…35 кгс/см2 в интервале температур от –5 до –20°С за счет испарения жидкого фреона, подаваемого в межтрубное пространство конденсатора из холодильной установки. Жидкий CO2 собирается в сборник, а остаточные и продувочные газы сбрасываются в атмосферу.
Таким образом, на примере крупного химического предприятия, ориентированного на выпуск минеральных удобрений, рассмотрены вопросы производства и переработки диоксида углерода. Показано, что наращивание мощностей по выпуску диоксида углерода должно сопровождаться решением двух вопросов: организация производств по глубокой переработке CO2 и по его использованию на нефтедобывающих предприятиях.
Список литературы
- Афанасьев С.В., Капитонов М.С., Лисовская Л.В. Совершенствование техно логии и оборудования крупнотоннажного производства диоксида углерода//Технические газы. 2007. №3. С.51–55.
- Афанасьев С.В., Лавренченко Г.К., Копытов А.В., Рощенко О.С. Повышение эффективности подачи диоксида углерода на синтез карбамида//Технические газы. 2011. №2. С. 27–31.
- Афанасьев С.В., Махлай С.В. Карбамидоформальдегидный концентрат. Технология. Переработка. Самара. Изд-во Самарского научн. центра РАН, 2012. 298 с.
- Патент на изобретение RU №2296000, МПК В 01 D 53/56, B 01 D 53/86, B 01 J 23/16. Способ очистки дымовых газов от оксидов азота.
- Патент на изобретение RU №2376537. МПК F25J 1/02. Способ ожижения диоксида углерода.
- Патент на полезную модель RU №117311 МПК B01D 53/14. Регенератор диоксида углерода.
- Лавренченко Г.К., Копытин А.В., Афанасьев С.В. и др. Совершенствование производства жидкого низкотемпературного диоксида углерода в циклах среднего давления//Технические газы. Научно 2013. №2. С. 60–62.