Автор: А.Б. Жидков (ООО «Алитер-Акси»).
Опубликовано в журнале Химическая техника №10/2014
Крупные промышленные печи установок производства водорода (печи водородного риформинга) активно эксплуатируются с начала 1960-х годов в нефтеперерабатывающей, нефтехимической отраслях, в химической промышленности (производство аммиака, метанола, минеральных удобрений). За последние десять лет в мире общая мощность установок производства водорода увеличилась более чем в четыре раза.
В России происходит масштабная реконструкция, развитие нефтехимических отраслей, при этом тенденция реконструкции существующих и строительства новых установок производства водорода более актуальна, чем за рубежом. Сегодня установки производства водорода (УПВ), построенные в начале 2000-х годов, требуют проведения ремонтов. На многих нефтеперерабатывающих заводах (НПЗ) строятся новые крупные УПВ.
Одним из наиболее ответственных элементов печи водородного риформинга является выходной коллектор – трубопровод, по которому синтез-газ, состоящий на 75% из водорода, при температуре до 870°С подается в закалочный аппарат на установках нефтепереработки или в конвертер на установках синтеза метанола. Основная проблема эксплуатации коллектора – перегревы наружной поверхности металла с последующей водородной коррозией.
Эти процессы могут развиваться очень быстро, приводя к аварии (разгерметизация) коллектора с тяжелыми последствиями.
Данная статья посвящена факторам, вызывающим риски в работе коллекторов, систематизации знаний по конструкции коллекторов, возможным материальным исполнениям стенок и футеровки коллекторов.
Анализ работы выходного коллектора по технологическому и химическому воздействию на стенки коллектора
Основные реакции получения водорода при использовании в качестве сырья природного газа и водяного пара:
CH4 + H2O = CO + 3H2;
CO + H2O = CO2 + 3H2.
Продуктами реакции являются водород, монои диоксид углерода.
Первые два вещества являются сильными восстановителями, что предъявляет определенные требования к выбору металла для коллектора (водород при контакте с углеродистыми сталями при температуре выше 280°С вызывает водородную коррозию), к защите наружного металлического кожуха, к выбору огнеупорных материалов.
Для оценки скорости потока, перепада давления в коллекторе в рабочем состоянии нами были взяты данные по загрузке трех печей водородного риформинга, работающих на НПЗ в Перми (ООО «ЛУКОЙЛ- ПНОС»), Рязани (ЗАО «РНПК») и Киришах (ООО «КИНЕФ»). Результаты представлены в табл. 1. Линейная скорость движения синтез-газа в сборном коллекторе находится в диапазоне 30…50 м/с. Для сравнения: максимальная скорость движения дымовых газов в дымоходах с использованием дымососов – 15 м/с.
Таблица 1
Технологические характеристики работы коллекторов различных НПЗ
Показатель | ООО «КИНЕФ» | ЗАО «РНПК» | ООО «ЛУКОЙЛ-ПНОС» |
Тип коллектора | Футерованный
с металлической вставкой |
Футерованный | Футерованный
с металлической вставкой |
Внутренний диаметр коллектора «в свету», мм | 565,6 | 565,6 | 565,6 |
Загрузка, % | 100 | 100/110 | 100/75 |
Расход сырья, кг/ч | 96337 | 81250/94590 | 74250/56250 |
Температура продукта, °С | 871 | 845/845 | 880/935 |
Давление продукта, МПа | 2,53 | 2,53/2,53 | 2,11/2,11 |
Линейная скорость продукта, м/с | 40 | 44,29/51,56 | 35,4/26,8 |
Массовая скорость продукта, кг/(м2с) | 106 | 104,1/121,2 | 85/64,4 |
Состав синтез-газа до конвентора СО, % об. |
H2 – 75,5 CO – 11,9 CO2 – 10,1 CH4 – 2,5 |
H2 – 77,96
CO – 9,34 CO2 – 7,15 CH4 – 4,7 O2 – 0,16 N2 – 0,69 |
H2 – 73,5
CO – 14,9 CO2 – 8,7 CH4 – 3,5 N2 – 0,05 |
Плотность синтез-газа до конвентора СО, кг/м3 | 2,671 | 2,351 | 2,398 |
На рис. 1 показаны расчетные перепады давления, возникающие при движении синтез-газа в сборном коллекторе печи ООО «КИНЕФ».
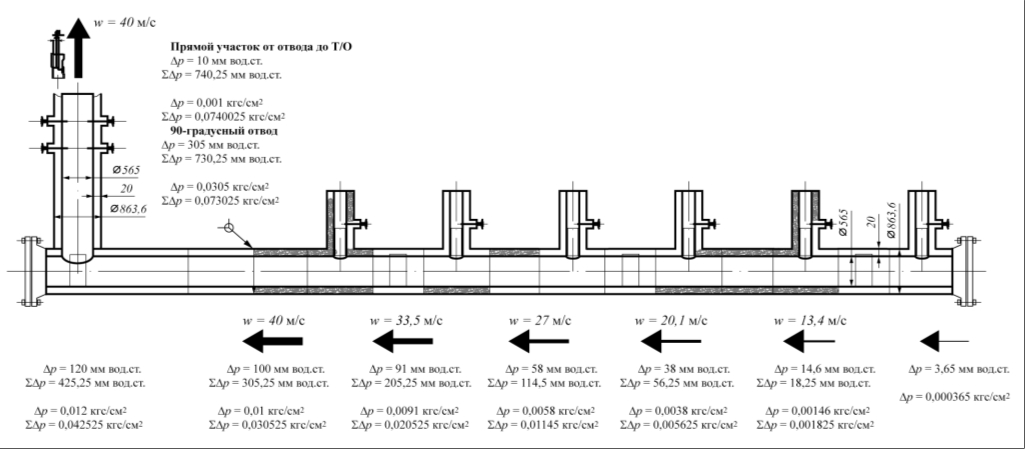
Для удобства значения перепада представлены в мм вод. ст. и в обычных единицах.
Из представленных данных можно видеть, что общий перепад по всей длине сборного коллектора – 740 мм вод. ст. или 0,074 кгс/см2. Основная часть перепада приходится на поворотный участок коллектора к теплообменнику. Отметим, что максимальный перепад давления в дымоходах печей длиной до 150 м при использовании дымососов – не более 100 мм вод. ст. Таким образом, в коллекторе возникает перепад давления по длине, который при наличии достаточно больших, сквозных трещин в футеровке будет приводить к движению синтез-газа через трещины в футеровке, приводя к перегреву наружных стен коллектора.
Второй фактор воздействия, с которым необходимо считаться, – восстановительная среда, обусловленная наличием водорода и монооксида углерода (СО). Монооксид углерода восстанавливает окись железа (Fe2O3) до металлического железа (реакция Будуара [1]). Реакция начинается при температуре выше 510°С, водород ускоряет эту реакцию. В процессе реакции Будуара оксид железа в несколько этапов через карбидные фазы проходит ряд фазовых превращений. Побочным продуктом реакции является углерод (кокс). Если содержание окиси железа в футеровке достаточно велико, то эти процессы могут привести к механическому разрушению футеровки. Оксид кремния также неустойчив в среде водорода и может переходить в газовую фазу при температуре выше 1000°С по следующей реакции:
SiO2 тв + H2 газ = SiO газ + H2O газ.
Эта реакция при температуре ниже 1000°С идет очень медленно и становится заметной только при высоких температурах. Однако многие производители рекомендуют для футеровки выходных коллекторов использовать бетоны с минимальным содержанием окиси кремния.
Классификация выходных коллекторов печей производства водорода
В литературе не предлагается системный взгляд на различные типы коллекторов, поэтому целесообразно предложить следующую классификацию выходных коллекторов печей водородного риформинга по назначению в печи:
- субколлекторы;
- сборные (приемные) коллекторы;
- трансферные коллекторы.
Субколлекторы расположены под печью и служат для сбора синтезгаза из реакционных труб (рис. 2).
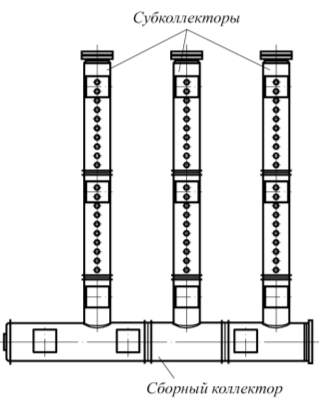
Сборные (приемные) коллекторы (рис. 2) служат для сбора синтез-газа от субколлекторов и передачи его либо в трансферный коллектор, либо в закалочный аппарат (котелутилизатор для выработки пара и охлаждения синтез-газа).
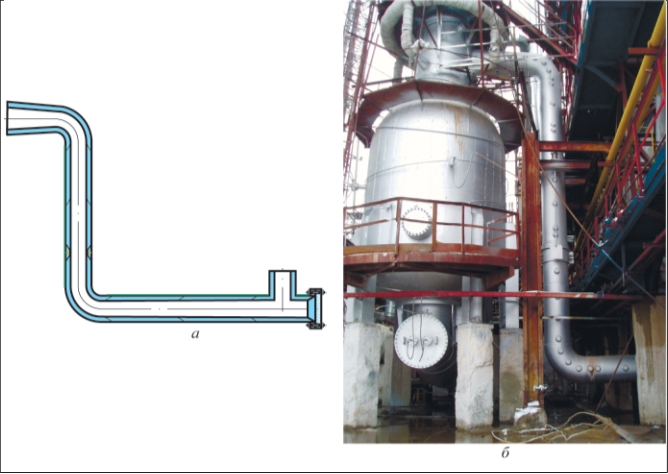
Трансферные коллекторы (рис. 3) служат для передачи синтез-газа в конвертер, реактор и другое оборудование, находящееся на некотором отдалении от печи. Как правило, они имеют сложную форму и протяженность 26…30 м.
Классификация коллекторов по конструкции футеровки
Можно предложить следующую классификацию коллекторов:
- коллекторы без футеровки;
- коллекторы футерованные с внутренней оболочкой из проката с высоким содержанием никеля (например, инколой 800Н или жаростойкая сталь ХН32Т);
- коллекторы футерованные без внутренней металлической оболочки.
Коллекторы без футеровки были использованы в первых печах данного типа. Коллектор выполняется из того же материала, что и реакционные трубы (центробежное литье либо инколой 800Н). Как правило, коллектор расположен под печью, температура его наружной стенки близка к температуре продукта (около 800°С). В большинстве печей этот тип коллекторов используется только для субколлекторов, расположенных под печью. Как правило, горячий коллектор находится в футерованном тоннеле (рис. 4) со смотровыми окнами для контроля состояния коллектора. Реже применяется наружная теплоизоляция для защиты оборудования и персонала от воздействия высоких температур. На выходе из тоннеля субколлекторы входят в футерованный сборный и далее в трансферный коллекторы.
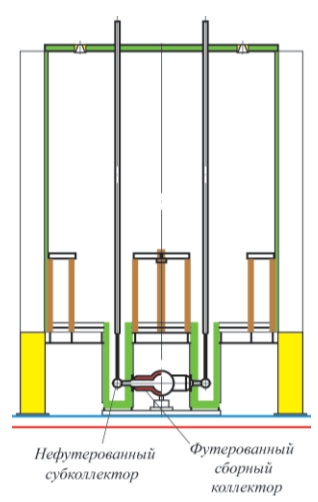
Сегодня такие технические решения используются не только в печах 1960–1970-х годов, но и в современных печах, например в ОАО «ТАИФ НК» (г. Нижнекамск, пуск в эксплуатацию – 2001 г.). В печах очень малой мощности такое решение применяется для всего коллектора.
Например, нами был выполнен и реализован проект печи в составе минизавода по производству метанола (12 500 т/год) на Юрхаровском месторождении, в котором весь коллектор был из высоконикелевой (инколой 800Н) трубы (рис. 5).
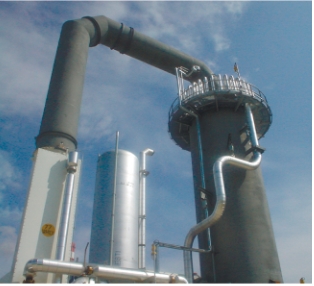
Коллектор на этой печи идет от ее верхней части, имеет многочисленные изгибы для температурной компенсации, находится в теплоизоляционном кожухе.
Преимущества такого решения: – простота обслуживания, легкость осмотра состояния трубы. Недостатки: высокая стоимость трубы для коллектора (7…10 млн. руб/т), большие тепловые потери, дополнительный риск пожаровзрывоопасности.
Коллекторы футерованные с внутренней оболочкой
Для снижения стоимости коллекторов с конца 1960-х годов стали применять футерованные коллекторы. Для направления потока синтезгаза и предотвращения прохождения синтез-газа через трещины в футеровке, предотвращения уноса футеровки внутри коллектора применяется труба из инколоя 800Н (либо из стали ХН32Т). Пространство между наружной и внутренней трубой (как правило, 120…130 мм) заполняют огнеупорным теплоизоляционным бетоном. Температура поверхности коллектора при нормальном режиме работы не превышает 190…210°С.
В качестве материала для наружной трубы в первых проектах применяли сталь 15Х5М, так как допускается эксплуатация этой стали в водородсодержащей среде при температуре до 550°С. Позднее, после накопления опыта, начали применять стали 09Г2С, 16ГС, максимальная температура эксплуатации в водородсодержащих средах которых ограничивается 280…300°С.
Данное техническое решение сегодня является наиболее распространенным, применяется для изготовления всех типов коллекторов по назначению (субколлекторы, сборные, трансферные коллекторы).
В азотной промышленности для повышения надежности и понижения температуры стенки наружной трубы в некоторых проектах на трансферных коллекторах используют наружную водяную рубашку для охлаждения.
На рис. 3 показан эскиз трансферного коллектора. Преимущества данного решения – значительно меньшая стоимость, чем стоимость нефутерованных коллекторов.
Недостатки: необходим постоянный контроль температуры поверхности коллектора, так как при превышении допустимых температур возможно резкое развитие аварийной ситуации, что не раз было на практике.
Коллекторы футерованные без внутренней металлической оболочки
Прогресс в области разработки огнеупорных бетонов, накопленный опыт эксплуатации выходных коллекторов печей водородного риформинга позволили в начале 2000-х годов перейти к изготовлению коллекторов с футеровкой без внутренней трубы (рис. 6). Футеровка в этом случае двухслойная, толщиной не менее 250 мм, рабочий слой – максимально газоплотный из низкоусадочного бетона без окислов, склонных к восстановлению (окиси железа и кремния), внутренний слой – из теплоизоляционного бетона плотностью 0,8…1,0 г/см3. По такой схеме реализованы проекты последних лет ЗАО «РНПК», ОАО «Татнефть», и ряд проектов сегодня находятся на стадии реализации.
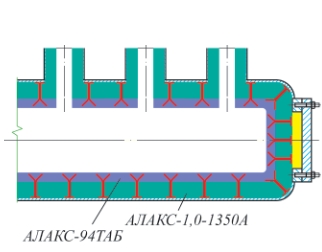
Преимущество данного решения: еще большая дешевизна и быстрота в реализации по сравнению с коллектором с внутренней трубой, а также возможность проводить ревизии и ремонты футеровки в период остановок для ремонта.
Недостатки: большая толщина футеровки приводит к значительному увеличению диаметра коллектора (больше 1 м), увеличению толщины металлической стенки коллектора.
Требования к выбору бетона, качеству его укладки значительно повышаются; при разрушении бетона – перегрев наружной стенки, развитие аварийной ситуации возможно в более короткий период времени. Для качественной реализации этого решения необходимо, чтобы внутренний диаметр коллектора (после футеровки) был не менее 400…450 мм для выполнения работ внутри. Если коллектор имеет меньший диаметр, то необходимо использовать решение с внутренней трубой.
Таким образом, несмотря на многолетний опыт эксплуатации выходных коллекторов печей водородного риформинга, в настоящий момент используются различные технические решения в отношении конструкции коллекторов, материального исполнения наружной трубы и футеровки.
Огнеупорные бетоны, применяемые для изготовления футеровки коллекторов
Вопросам химического состава, способа подготовки футеровки для коллекторов водородного риформинга посвящено много работ [1, 2]; многие компании предлагают свои услуги. Требования к бетонам достаточно понятны: минимальная усадка, минимальное образование трещин, низкая плотность, низкая теплопроводность, инертность к водороду, монооксиду углерода.
Однако уровень формализации нормативных требований к бетонам в мире достаточно низкий. В отличие от марок сталей (формализованных в международных стандартах и имеющих аналоги в России) огнеупорные бетоны выпускаются под торговыми марками компаний-производителей с указанием минимума свойств. Компании создают вокруг данных работ ореол таинственности.
Так, известная компания Plibrico International рекомендует для футеровки в атмосфере водорода и монооксида углерода материалы под своими торговыми марками, называя их новыми «инновационными» материалами [1]. При этом указываются только окисный состав (низкое содержание оксидов железа, 35–50% окиси кремния) и теплопроводность.
Сегодня многие зарубежные и немногие российские компании производят огнеупорные бетоны разнообразного химического состава с широкой гаммой свойств. Так,
ООО «Алитер-Акси» производит около 100 наименований огнеупорных бетонов [3], большая часть которых по окисному составу соответствует рекомендациям ведущих зарубежных компаний, однако лишь немногие бетоны удовлетворяют требованиям надежной работы в условиях, характерных для водородных коллекторов.
В составе бетона содержание оксида железа и других соединений железа должно быть минимальным (менее 1%, желательно менее 0,1%).
Оксид кремния, как указывалось, также нежелателен. Но проблема в том, что бетоны на основе легковесного корунда имеют минимальную плотность (1,5 кг/см3) и достаточно высокую теплопроводность.
Исходя из этого, для решения задачи защиты стенок водородного коллектора применяют бетоны на основе высокоглиноземистого шамота, который состоит в основном из алюмосиликатов и содержит минимальное количество свободного оксида кремния.
Второй подход – использование в качестве заполнителя гексаалюмината кальция. Этот синтетический материал появился на рынке в последние 10 лет. Производителями это сырье рекомендуется для применения в восстановительных средах, но большого практического опыта работы с ним пока не накоплено.
Выбрать сырье для необходимых бетонов, осуществлять входной контроль – задача для специалистов по огнеупорам.
Таблица 2
Бетоны серий АЛАКС, АЛКОР производства ООО «Алитер-Акси» и импортные аналоги, применяемые для футеровок выходных коллекторов установок водородного риформинга
Бетон | Химический состав, % | Плотность после обжига
при 800°С, г/см3 |
Теплопроводность при средней температуре 500°С, Вт/м×К | Предел прочности при сжатии после обжига при 800°С, Н/мм2 | |||
Al2O3 | SiO2 | Fe2O3 | CaO | ||||
АЛАКС-1,0-1350А | 38 | 45 | 1,5 | 11 | 1,0 | 0,3 | 5 |
АЛАКС-1,2-1350АС* | 48 | 36 | 1 | 14 | 1,15 | 0,4 | 10 |
АЛАКС-1,6-1800 | 90 | 0,1 | 0,1 | 9 | 1,5 | 1,1 | 30 |
АЛКОР-94ТАБ | 94 | 0,1 | 0,1 | 5 | 2,5 | 2,0 | 70 |
KAST-0-LITE 23 LI* | 33 | 54 | 0,6 | 10 | 0,9 | 0,3 | 2 |
FIRELITE 2300VLI** | 47 | 32 | 0,5 | 18 | 0,9 | 0,2 | 2 |
FERECRETE 95** | 94 | 0,1 | 0,1 | 5 | 2,5 | 1,7 | 60 |
В табл. 2 показаны бетоны, разработанные ООО «Алитер-Акси», и импортные аналоги, которые рекомендуются для решения этой задачи. Бетоны АЛАКС-1.0-1350А и АЛАКС1.2-1350АС содержат в составе алюмосиликаты, минимум оксидов железа, минимальное количество свободного оксида кремния. Эти бетоны имеют низкую теплопроводность, подходят для решения проблемы футеровки коллекторов. Бетон АЛАКС-1.6-1800 наиболее чист, практически не содержит оксидов кремния и железа, но имеет несколько большую теплопроводность. Мы активно используем этот бетон для футеровки конвертеров в азотной промышленности (температура в зоне реакции до 1600°С) и для трансферных коллекторов водородных печей. При этом на наружной стенке коллектора температура несколько повышенная (до 210°С), но работают коллекторы очень надежно более 10 лет. Бетон АЛКОР-94ТАБ применяется в субколлекторах и сборных коллекторах без внутренней обечайки с двухслойной футеровкой для внутреннего, рабочего слоя. Этот бетон обладает высокой газоплотностью, низким трещинообразованием. Этих качеств достаточно для обеспечения безопасной работы коллектора. Однако опыт работы таких коллекторов у нас пока ограничен двумя годами.
В табл. 2 приведены также наиболее популярные зарубежные аналоги, применяемые для футеровки коллекторов. Как видно из таблицы, эти материалы близки по свойствам к выпускаемым ООО «Алитер-Акси», но по параметрам прочности наши материалы превосходят импортные аналоги, что, по нашему мнению, важно.
Таким образом, несмотря на большой срок и накопленный опыт эксплуатации печей водородного риформинга установок производства водорода, для выходных коллекторов сегодня применяются различные конструктивные решения и материальные исполнения.
По материальному исполнению наружной обечайки наиболее широко применяются углеродистые стали, хотя слаболегированные и высоколегированные стали для некоторых конструкций еще не потеряли своей актуальности. По конструкции и материалу футеровки в настоящее время имеет место набольшее разнообразие решений.
Для эффективного решения вопросов проектирования и изготовления выходного коллектора печей установок производства водорода необходимо особое внимание уделить выбору квалифицированной компании, имеющей опыт подобных работ.
Список литературы
- Patrick Tassot, Erik Bachman, Richard C. Johnson. The influence of reducing atmospheres on monolithic refractory linings for petrochemical service//7th Biennial Worldwide Congress on Refractories. November 4-7, 2001, Cancun, Mexico.
- Richard C. Johnson, M.S. Crowley. State of the refractory lining for hydrogen reformer vessels//9th Biennial Worldwide Congress on Refractories. November 8-11, 2005, Orlando, USA.
- Денисов Д.Е., Жидков А.Б., Власов В.В. Огнеупорные (жаростойкие) бетоны для предприятий нефтепереработки и нефтехимии//Химия и технология топлив и масел. 2004. №4.